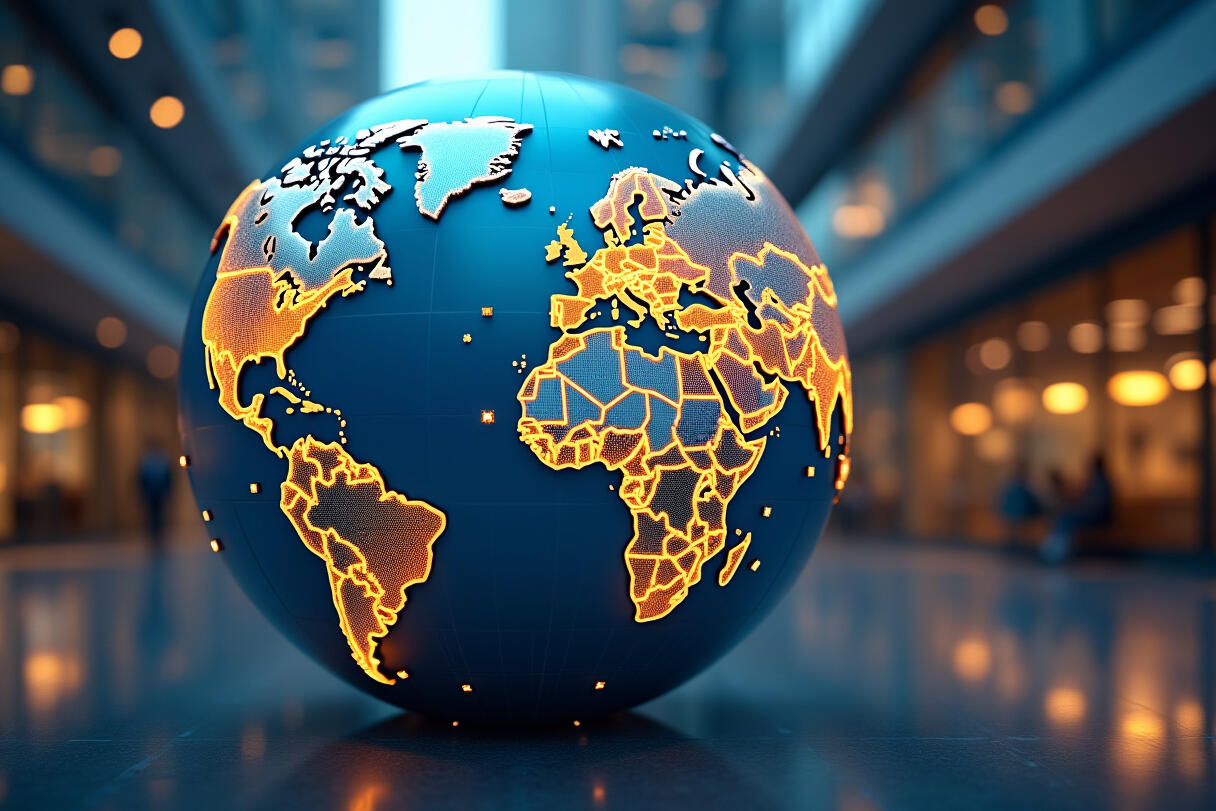
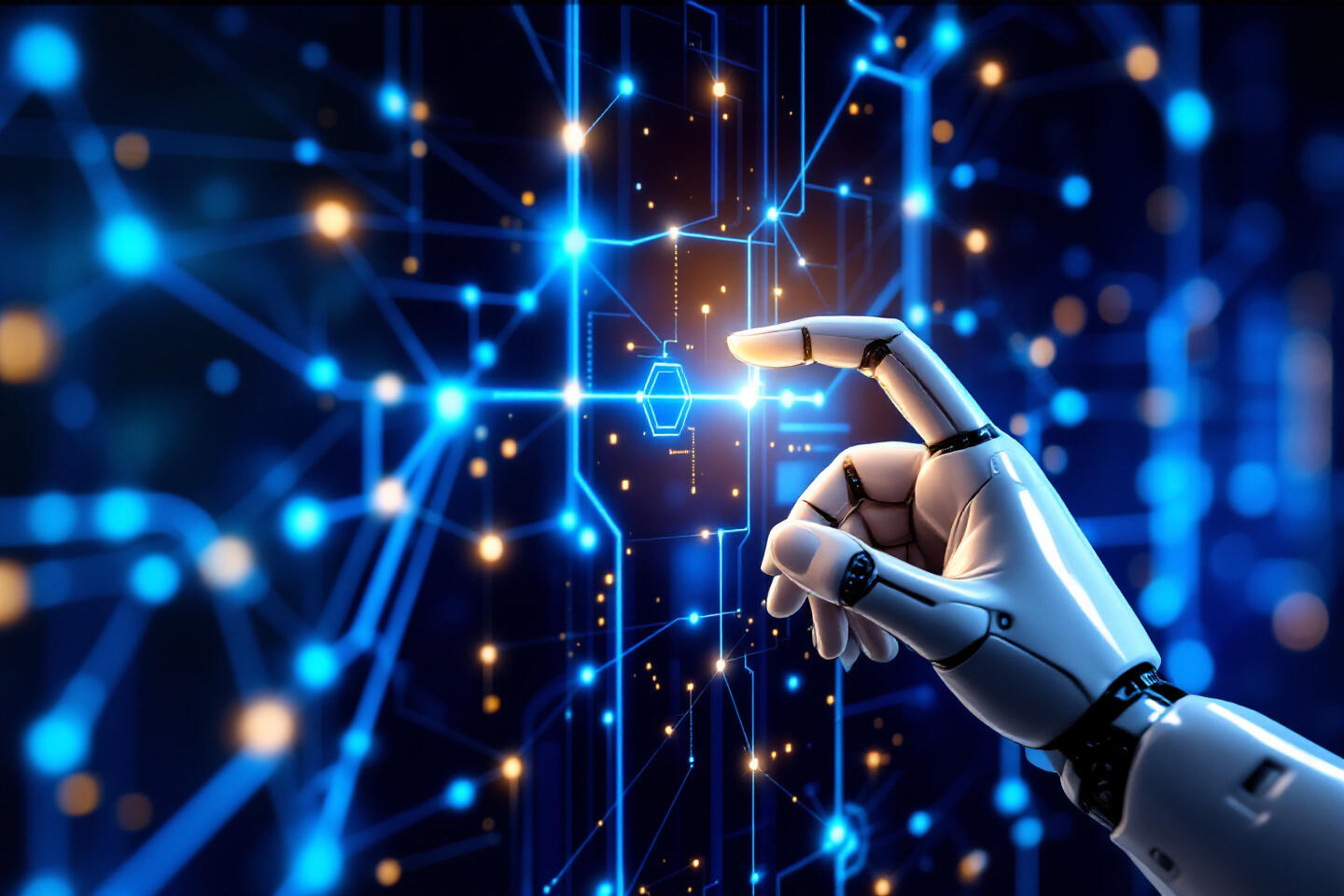
In der heutigen digitalen Ära ist die effiziente und zuverlässige Bewirtschaftung von Maschinen und Anlagen für Unternehmen unerlässlich. Hier kommt das Konzept der vorausschauenden Instandhaltung ins Spiel. Aber was genau verbirgt sich hinter dem Begriff Predictive Maintenance und warum ist es so relevant für moderne Industrieunternehmen?
Predictive Maintenance ermöglicht es, durch die Analyse von Echtzeit-Daten potenzielle Störungen frühzeitig zu erkennen und gezielt zu verhindern. Dadurch können Unternehmen teure Ausfallzeiten minimieren, die Lebensdauer ihrer Anlagen verlängern und die Wirtschaftlichkeit steigern. Doch wie funktioniert diese Technologie konkret und welche Voraussetzungen müssen erfüllt sein, um sie erfolgreich zu implementieren?
In diesem Beitrag beantworten wir alle Ihre Fragen rund um Predictive Maintenance, von den technologischen Grundlagen über Implementierungsstrategien bis hin zu branchenspezifischen Anwendungen und zukünftigen Entwicklungen. Wir zeigen Ihnen nicht nur die zahlreichen Vorteile auf, sondern geben auch praktische Tipps und Best Practices, um Ihnen den Einstieg zu erleichtern. Lassen Sie sich inspirieren und entdecken Sie, wie Predictive Maintenance Ihr Unternehmen revolutionieren kann!
Einführung und Grundlagen
Bedeutung und Definition von Predictive Maintenance
Predictive Maintenance, oder vorausschauende Instandhaltung, ist eine fortschrittliche Wartungsstrategie, die den Zustand von Maschinen und Anlagen kontinuierlich überwacht. Durch die Analyse von Echtzeit-Daten und den Einsatz moderner Technologien zielt sie darauf ab, Wartungsmaßnahmen bedarfsorientiert zu planen, bevor es zu einem Maschinenausfall kommt. Im Gegensatz zur reaktiven Wartung, bei der erst nach einem Ausfall reagiert wird, und zur präventiven Wartung, die nach festen Zeitintervallen erfolgt, basiert Predictive Maintenance auf dem tatsächlichen Zustand und der Nutzung der Geräte.
Diese Methode nutzt umfangreiche Daten, um präzise Vorhersagen über den Wartungsbedarf zu treffen, was zu einer effizienteren Ressourcennutzung und einer höheren Betriebssicherheit führt. Besonders in Branchen mit komplexen und kostenintensiven Maschinen bietet Predictive Maintenance erhebliche Vorteile, indem sie unvorhergesehene Stillstände vermeidet und die Lebensdauer der Anlagen verlängert.
Unterschiede zu anderen Wartungsstrategien
Im Vergleich zu traditionellen Wartungsstrategien bietet Predictive Maintenance deutliche Vorteile:
- Reaktive Wartung (Reactive Maintenance): Wartung erfolgt erst nach dem Auftreten eines Fehlers oder Ausfalls. Diese Methode kann zu hohen Stillstandskosten und unerwarteten Produktionsunterbrechungen führen.
- Präventive Wartung (Preventive Maintenance): Regelmäßige Wartungsarbeiten werden nach festen Zeitintervallen durchgeführt, unabhängig vom Zustand der Maschine. Dies kann zu unnötigen Wartungsarbeiten und erhöhten Kosten führen, wenn keine Probleme vorhanden sind.
- Predictive Maintenance: Wartungsmaßnahmen werden basierend auf Echtzeit-Daten und Zustandsanalysen geplant. Dies ermöglicht eine präzise und bedarfsgerechte Wartung, die Kosten reduziert und die Anlageneffizienz erhöht.
Durch den Einsatz von Predictive Maintenance werden Wartungsarbeiten effizienter geplant, was zu einer Minimierung von ungeplanten Ausfallzeiten und einer optimalen Nutzung der Ressourcen führt. Im Gegensatz zur präventiven Wartung ist sie flexibler und genauer, da sie auf tatsächliche Nutzung und Zustand der Maschinen basiert.
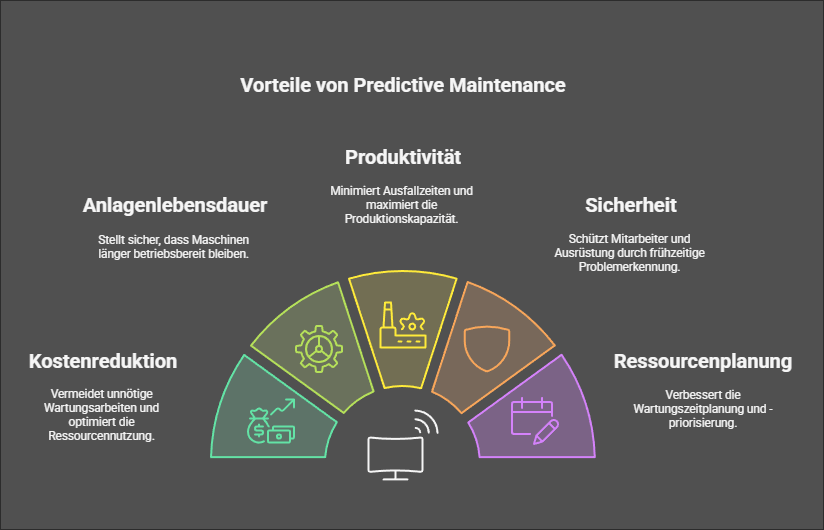
Ziel und Nutzen von Predictive Maintenance
Das Hauptziel von Predictive Maintenance ist die Maximierung der Effizienz und Zuverlässigkeit von Maschinen und Anlagen. Durch die frühzeitige Erkennung potenzieller Probleme können Wartungsmaßnahmen gezielt und rechtzeitig durchgeführt werden, bevor schwerwiegende Schäden entstehen. Der Nutzen umfasst:
- Reduktion der Wartungskosten: Durch bedarfsorientierte Wartung werden unnötige Arbeiten vermieden und Ressourcen effizient eingesetzt.
- Verlängerung der Lebensdauer der Anlagen: Regelmäßige und gezielte Wartung verhindert vorzeitigen Verschleiß und erhöht die Lebensdauer der Maschinen.
- Steigerung der Produktivität: Weniger Ausfallzeiten bedeuten eine durchgehend hohe Produktionskapazität.
- Erhöhung der Sicherheit: Früherkennung von Problemen trägt zur Sicherheit der Mitarbeiter und der Produktionsanlagen bei.
- Optimierung der Ressourcenplanung: Wartungsarbeiten können besser geplant und priorisiert werden, was die gesamte Betriebsführung verbessert.
Diese Vorteile machen Predictive Maintenance zu einer unverzichtbaren Strategie für moderne Industrieunternehmen, die ihre Wettbewerbsfähigkeit steigern und ihre Betriebskosten senken möchten.
Technologische Grundlagen
Sensortechnologien und deren Einsatz
Eine der wesentlichen Komponenten von Predictive Maintenance sind die Sensoren, die zur Erfassung verschiedener Betriebsparameter eingesetzt werden. Diese Sensoren messen kontinuierlich Daten wie Vibrationen, Temperaturen, Druck, Feuchtigkeit und elektrische Ströme. Die präzisen Messungen ermöglichen eine genaue Überwachung des Anlagenzustands.
Fortschrittliche Sensortechnologien, wie beispielsweise Schwingungssensoren, Temperatursensoren und akustische Sensoren, liefern die notwendigen Echtzeit-Daten. Moderne Sensoren sind oftmals mit drahtlosen Kommunikationsfähigkeiten ausgestattet, wodurch sie nahtlos in bestehende IT-Infrastrukturen integriert werden können. So stellt die Firma Procom mit ihren CNC-Maschinen sicher, dass durch hochwertige Sensoren zuverlässige Daten für die Predictive Maintenance gesammelt werden.
Datenanalyse-Tools und Software-Lösungen
Die gesammelten Daten müssen effizient verarbeitet und analysiert werden, um nützliche Erkenntnisse zu gewinnen. Hier kommen spezialisierte Datenanalyse-Tools und Software-Lösungen ins Spiel. Diese Programme ermöglichen die Verarbeitung großer Datenmengen und die Identifizierung von Mustern, die auf potenzielle Probleme hinweisen.
Clouver, eine führende Software im Bereich Produktionsmonitoring, bietet leistungsstarke Analysefunktionen, die speziell auf die Anforderungen der Predictive Maintenance zugeschnitten sind. Solche Tools nutzen statistische Analysen und maschinelles Lernen, um Abweichungen im Anlagenbetrieb zu erkennen und Vorhersagen über den Wartungsbedarf zu treffen.
Steigere deine Produktivität mit Clouver!
Mit unserer leistungsstarken IIoT-Plattform behältst du jederzeit den Überblick über deine Produktionsprozesse. Reduziere Ausfallzeiten, verbessere deine Ressourcennutzung und bleibe deinen Wettbewerbern einen Schritt voraus. Sichere dir jetzt eine persönliche Beratung und erfahre, wie Clouver dich unterstützen kann!
Machine Learning Algorithmen
Machine Learning (ML) Algorithmen sind ein zentraler Bestandteil von Predictive Maintenance. Sie verarbeiten historische und Echtzeit-Daten, um Muster und Zusammenhänge zu erkennen, die menschlichen Analysten möglicherweise entgehen. Diese Algorithmen können kontinuierlich aus neuen Daten lernen und ihre Vorhersagegenauigkeit verbessern.
Durch den Einsatz von ML-Algorithmen können Unternehmen präzisere Vorhersagen über den Zustand ihrer Maschinen treffen und dadurch gezieltere Wartungsmaßnahmen planen. Dies führt zu einer höheren Effizienz und Zuverlässigkeit der Produktionsprozesse.
IoT-Infrastruktur und Connectivity
Eine robuste IoT-Infrastruktur (Internet of Things) ist unerlässlich für die erfolgreiche Umsetzung von Predictive Maintenance. Sie gewährleistet, dass alle Sensoren und Geräte zuverlässig miteinander kommunizieren und die gesammelten Daten in Echtzeit übertragen werden. Eine stabile Konnektivität ermöglicht es, Daten nahtlos an zentrale Datenbanken oder Cloud-Dienste wie die Lösungen von Clouver zu senden, wo sie analysiert und ausgewertet werden können.
Edge Computing vs. Cloud Computing
Bei der Datenverarbeitung im Rahmen von Predictive Maintenance gibt es zwei Hauptansätze: Edge Computing und Cloud Computing.
- Edge Computing: Hier werden die Daten direkt an der Quelle, also nahe am Standort der Maschinen, verarbeitet. Dies reduziert die Latenzzeiten und ermöglicht schnellere Reaktionszeiten bei der Erkennung von Anomalien. Zudem entlastet es die zentrale IT-Infrastruktur, da nur relevante Daten weitergeleitet werden.
- Cloud Computing: Cloud-basierte Lösungen bieten eine zentrale Plattform für die Datenspeicherung und -verarbeitung. Sie erlauben eine skalierbare Analyse großer Datenmengen und den Einsatz fortschrittlicher Analysetools. Allerdings können höhere Sicherungs- und Datenschutzanforderungen bestehen.
Die Wahl zwischen Edge und Cloud Computing hängt von den spezifischen Anforderungen des Unternehmens ab. Oft werden beide Ansätze kombiniert, um die Vorteile beider Technologien zu nutzen.
Funktionsweise von Predictive Maintenance
Datenkollektion durch Sensoren und Monitoring
Die Grundlage von Predictive Maintenance ist die kontinuierliche Datenerfassung durch verschiedene Sensoren. Diese Sensoren überwachen wesentliche Betriebsparameter wie Temperatur, Vibration, Druck und Feuchtigkeit. Die gesammelten Daten werden in Echtzeit erfasst und an zentrale Datenbanken weitergeleitet. Mit hochwertigen CNC-Maschinen von Procom und dem Einsatz der Clouver-Software wird sichergestellt, dass die Daten präzise und zuverlässig sind.
Echtzeitanalyse und In-memory Datenbanken
Die Echtzeitanalyse der gesammelten Daten ist entscheidend für die frühzeitige Erkennung von Anomalien. In-memory Datenbanken ermöglichen die schnelle Verarbeitung und Auswertung großer Datenmengen direkt im Arbeitsspeicher. Dies ermöglicht eine sofortige Reaktion auf erkannte Probleme und verbessert die Entscheidungsfindung.
Clouver bietet leistungsstarke Tools für die Echtzeitanalyse, die es Unternehmen ermöglichen, schnell auf Veränderungen im Anlagenzustand zu reagieren und notwendige Maßnahmen zu ergreifen.
Zustandsbeurteilung
Die Zustandsbeurteilung kann in zwei Formen erfolgen: periodisch und kontinuierlich.
- Periodische Zustandsbeurteilung: Hierbei werden Daten in regelmäßigen Abständen ausgewertet, um den Zustand der Maschinen zu überprüfen. Dies ist hilfreich für Anlagen, die nur selten genutzt werden oder deren Zustandsänderungen langsam verlaufen.
- Kontinuierliche Zustandsbeurteilung: Diese Methode basiert auf einer fortlaufenden Überwachung und Analyse der Daten. Sie ermöglicht eine sofortige Erkennung von Problemen und eine proaktive Wartung, wodurch die Verfügbarkeit der Anlagen maximiert wird.
Verschiedene Testmethoden
Predictive Maintenance nutzt verschiedene Testmethoden, um den Zustand der Maschinen zu beurteilen. Dazu gehören:
- Infrarot-Thermografie: Misst die Temperaturverteilung von Maschinenkomponenten, um Überhitzung oder andere thermische Anomalien zu erkennen.
- Akustische Analysen: Identifiziert ungewöhnliche Geräusche, die auf mechanische Probleme hinweisen könnten.
- Schwingungsanalysen: Erfasst und analysiert Schwingungsmuster, um Verschleiß oder Unwuchten in rotierenden Teilen zu erkennen.
Jede dieser Methoden bietet spezifische Vorteile und kann je nach Anwendungsbereich und Maschinenart eingesetzt werden, um ein umfassendes Bild des Anlagenzustands zu erhalten.

Implementierung und Integration
Schritt-für-Schritt Einführungsleitfaden
Die Implementierung von Predictive Maintenance erfordert einen systematischen Ansatz, der mehrere Schritte umfasst:
- Bedarfsanalyse: Identifizieren Sie die Maschinen und Anlagen, die für Predictive Maintenance am meisten von den Vorteilen profitieren.
- Dateninfrastruktur aufbauen: Installieren Sie die notwendigen Sensoren und stellen Sie eine zuverlässige IoT-Infrastruktur sicher, um die Daten zu erfassen und zu übertragen.
- Softwareauswahl: Wählen Sie geeignete Datenanalyse-Tools und Software-Lösungen wie Clouver, die auf Ihre spezifischen Anforderungen abgestimmt sind.
- Datenintegration: Integrieren Sie die gesammelten Daten in Ihre bestehenden Systeme und stellen Sie sicher, dass sie für die Analyse verfügbar sind.
- Modellanpassung: Entwickeln und trainieren Sie Machine Learning-Modelle, die auf Ihre spezifischen Maschinen und Betriebsbedingungen abgestimmt sind.
- Pilotphase: Führen Sie eine Pilotphase durch, um die Implementierung zu testen und die Modelle zu verfeinern.
- Skalierung: Nach erfolgreichen Tests skalieren Sie die Lösungen auf alle relevanten Maschinen und Anlagen im Unternehmen.
Durch diesen strukturierten Ansatz wird sichergestellt, dass die Implementierung reibungslos verläuft und die gewünschten Ergebnisse erzielt werden.
Kostenanalyse und ROI-Berechnung
Eine gründliche Kostenanalyse ist essenziell, um die wirtschaftliche Machbarkeit von Predictive Maintenance zu bewerten. Dabei sollten sowohl die initialen Investitionskosten für Sensoren, Software und Infrastruktur als auch die laufenden Betriebskosten berücksichtigt werden. Gleichzeitig müssen die potenziellen Einsparungen durch reduzierte Ausfallzeiten, längere Lebensdauer der Anlagen und optimierte Wartungsprozesse berechnet werden.
Die Berechnung des Return on Investment (ROI) ist ein wichtiger Schritt, um den wirtschaftlichen Nutzen der Implementierung von Predictive Maintenance zu verdeutlichen. Beispielsweise können Unternehmen durch die Reduktion ungeplanter Ausfallzeiten und die Vermeidung teurer Reparaturen innerhalb weniger Jahre einen positiven ROI erzielen.
Change Management bei der Einführung
Die Einführung von Predictive Maintenance erfordert nicht nur technologische Anpassungen, sondern auch organisatorische Veränderungen. Ein effektives Change Management ist entscheidend, um sicherzustellen, dass alle Mitarbeiter die neuen Prozesse akzeptieren und unterstützen. Dies umfasst:
- Kommunikation: Transparente und regelmäßige Kommunikation über die Vorteile und Ziele der Predictive Maintenance.
- Einbindung der Mitarbeiter: Beteiligung der Mitarbeiter an der Implementierung und Schulung, um Akzeptanz und Engagement zu fördern.
- Anpassung der Arbeitsprozesse: Integration der neuen Wartungsstrategien in bestehende Arbeitsabläufe, um eine nahtlose Übergabe zu gewährleisten.
Ein gut geplantes Change Management minimiert Widerstände und erhöht die Erfolgschancen der Implementierung.
Mitarbeiterschulung und Qualifikationsanforderungen
Die Schulung der Mitarbeiter ist ein wesentlicher Bestandteil der erfolgreichen Einführung von Predictive Maintenance. Mitarbeiter müssen über die notwendigen Kenntnisse und Fähigkeiten verfügen, um die neuen Systeme zu bedienen und die gewonnenen Daten effektiv zu nutzen. Dies umfasst:
- Technische Schulungen: Vermittlung von Kenntnissen über den Betrieb und die Wartung der neuen Sensoren und Softwarelösungen.
- Datenanalyse: Training im Umgang mit Datenanalyse-Tools und Interpretation der Ergebnisse.
- Prozesse und Abläufe: Anpassung der Wartungsprozesse an die neuen Strategien und Technologien.
Durch gezielte Schulungsprogramme wird sichergestellt, dass das Personal optimal vorbereitet ist und die Vorteile von Predictive Maintenance voll ausschöpfen kann.
Integration in bestehende Maintenance-Systeme
Die nahtlose Integration von Predictive Maintenance in bestehende Wartungssysteme ist entscheidend für die Effizienz und Effektivität der gesamten Strategie. Dies umfasst:
- Kompatibilität: Sicherstellung, dass die neuen Systeme mit den vorhandenen IT-Infrastrukturen und Wartungssystemen kompatibel sind.
- Datenintegration: Einbindung der Predictive Maintenance-Daten in bestehende Datenbanken und Managementsysteme, um eine ganzheitliche Übersicht zu ermöglichen.
- Automatisierung: Automatisierung von Wartungsprozessen, um menschliche Eingriffe zu minimieren und die Effizienz zu steigern.
Durch die Integration in bestehende Systeme wird eine einheitliche und effiziente Wartungsstrategie gewährleistet, die die gesamten Betriebsabläufe optimiert.
Rechtliche und Sicherheitsaspekte
Datenschutz und DSGVO-Konformität
Bei der Implementierung von Predictive Maintenance müssen alle gesammelten Daten den Datenschutzbestimmungen und der DSGVO entsprechen. Dies stellt sicher, dass die Privatsphäre der Nutzer geschützt wird und keine unbefugten Zugriffe auf sensible Daten erfolgen. Unternehmen müssen klare Richtlinien für die Datenerfassung, -speicherung und -verarbeitung festlegen und sicherstellen, dass alle Datenschutzanforderungen eingehalten werden.
IT-Sicherheit bei vernetzten Systemen
Die Sicherheit der vernetzten Systeme ist ein entscheidender Aspekt bei Predictive Maintenance. Es müssen umfassende Maßnahmen ergriffen werden, um die Systeme vor Cyberangriffen zu schützen und die Integrität der Daten zu gewährleisten. Dazu gehören Firewalls, Verschlüsselungstechnologien und regelmäßige Sicherheitsüberprüfungen. Eine robuste IT-Sicherheitsstrategie verhindert Datenverlust und unbefugten Zugriff auf kritische Informationen.
Haftungsfragen bei automatisierten Entscheidungen
Automatisierte Entscheidungen im Kontext von Predictive Maintenance können rechtliche Haftungsfragen aufwerfen. Es ist wichtig, klare Verantwortlichkeiten und Prozesse zu definieren, um rechtliche Risiken zu minimieren. Unternehmen müssen sicherstellen, dass die automatisierten Systeme transparent und nachvollziehbar sind und dass im Falle von Fehlentscheidungen klare Regelungen zur Haftung bestehen.
Standardisierung und Normen
Die Einhaltung von Standards und Normen stellt sicher, dass die Predictive Maintenance-Lösungen sicher und zuverlässig sind und den gesetzlichen Anforderungen entsprechen. Normen wie ISO 55000 (Asset Management) und ISO/IEC 27001 (Informationssicherheit) bieten Rahmenwerke, die Unternehmen bei der Implementierung und dem Betrieb von Predictive Maintenance unterstützen.
Zukunftstrends und Entwicklungen
Künstliche Intelligenz und Deep Learning in der Wartung
Die Integration von Künstlicher Intelligenz (KI) und Deep Learning in Predictive Maintenance wird die Genauigkeit der Vorhersagen weiter verbessern. Diese Technologien ermöglichen eine tiefere Analyse komplexer Datenmuster und bieten neue Möglichkeiten zur Optimierung der Wartungsprozesse. Durch den Einsatz von KI können Unternehmen noch präzisere Vorhersagen treffen und die Effizienz ihrer Produktionsanlagen weiter steigern.
Digital Twin Technologie
Die Digital Twin Technologie ermöglicht die Erstellung digitaler Zwillinge von physischen Assets, die in Echtzeit überwacht und analysiert werden können. Dies ermöglicht eine detaillierte Simulation und Vorhersage des Anlagenzustands, was die Planung und Durchführung von Wartungsmaßnahmen weiter optimiert. Digital Twins bieten eine exakte Nachbildung der physischen Anlagen und ermöglichen so eine präzisere Zustandsbewertung und Wartungsplanung.
Augmented Reality in der Wartung
Augmented Reality (AR) kann Wartungstechniker dabei unterstützen, komplexe Aufgaben effizienter und genauer auszuführen. Durch visuelle Anleitungen und Echtzeit-Datenüberlagerungen erhalten Techniker wertvolle Informationen direkt vor Ort, was die Fehlerquote reduziert und die Wartungszeiten verkürzt.
Autonome Wartungssysteme
Autonome Wartungssysteme, die auf Künstlicher Intelligenz basieren, könnten in Zukunft viele Wartungsaufgaben selbstständig durchführen. Diese Systeme könnten automatisch Probleme erkennen, Diagnosen stellen und sogar die notwendigen Reparaturmaßnahmen durchführen, wodurch die Effizienz weiter gesteigert wird.
Predictive Quality als Erweiterung
Predictive Quality erweitert das Konzept der vorausschauenden Wartung auf die Qualitätssicherung. Durch die frühzeitige Erkennung von potenziellen Qualitätsproblemen können Unternehmen proaktive Maßnahmen ergreifen, um die Produktqualität sicherzustellen und Ausschuss zu reduzieren. Dies führt zu einer verbesserten Kundenzufriedenheit und senkt die Kosten für Nacharbeiten und Qualitätskontrollen.
Häufige Herausforderungen
Die Qualität und Verfügbarkeit der Daten sind entscheidend für den Erfolg von Predictive Maintenance. Eine unzureichende Datenqualität kann zu fehlerhaften Vorhersagen und ineffizienten Wartungsmaßnahmen führen. Unternehmen sollten sicherstellen, dass sie über eine robuste Datenerfassung und -verarbeitung verfügen, um genaue und verlässliche Einsichten zu erhalten.
Die Integration von Predictive Maintenance-Lösungen in bestehende Systeme kann eine Herausforderung darstellen. Eine nahtlose Integration ist jedoch essenziell, um die Effizienz der Wartungsstrategien zu maximieren. Unternehmen sollten sicherstellen, dass ihre Predictive Maintenance-Systeme kompatibel mit ihren bestehenden IT-Infrastrukturen und Wartungssystemen sind.
Die Akzeptanz der Mitarbeiter ist ein wichtiger Erfolgsfaktor für die Einführung von Predictive Maintenance. Widerstände können durch mangelndes Verständnis und fehlende Schulungen entstehen. Durch effektives Change Management und umfassende Schulungsprogramme können Unternehmen sicherstellen, dass ihre Mitarbeiter die neuen Technologien und Prozesse unterstützen und effektiv nutzen.
Technical Debt, also die technologischen Schulden, die durch veraltete Systeme und unzureichende Wartung entstehen, kann eine Herausforderung bei der Implementierung von Predictive Maintenance sein. Unternehmen sollten sicherstellen, dass ihre bestehenden Systeme auf dem neuesten Stand gehalten werden und dass sie in neue Technologien investieren, um ihre Betriebsprozesse kontinuierlich zu verbessern.
Die Skalierbarkeit von Predictive Maintenance-Lösungen ist entscheidend, um den wachsenden Anforderungen und der zunehmenden Komplexität der Industrieanlagen gerecht zu werden. Unternehmen sollten sicherstellen, dass ihre Lösungen flexibel und anpassungsfähig sind, um zukünftiges Wachstum und neue Anforderungen zu bewältigen.
Mit Clouver immer einen Schritt voraus
Predictive Maintenance verändert die Industrie, indem es Ausfälle verhindert, Kosten senkt und die Effizienz steigert. Mit Clouver hast du ein leistungsstarkes Tool an der Hand, das dir datenbasierte Entscheidungen für eine smartere Produktion ermöglicht.
Möchtest du Clouver in Aktion sehen? Buche jetzt eine kostenlose Demo!
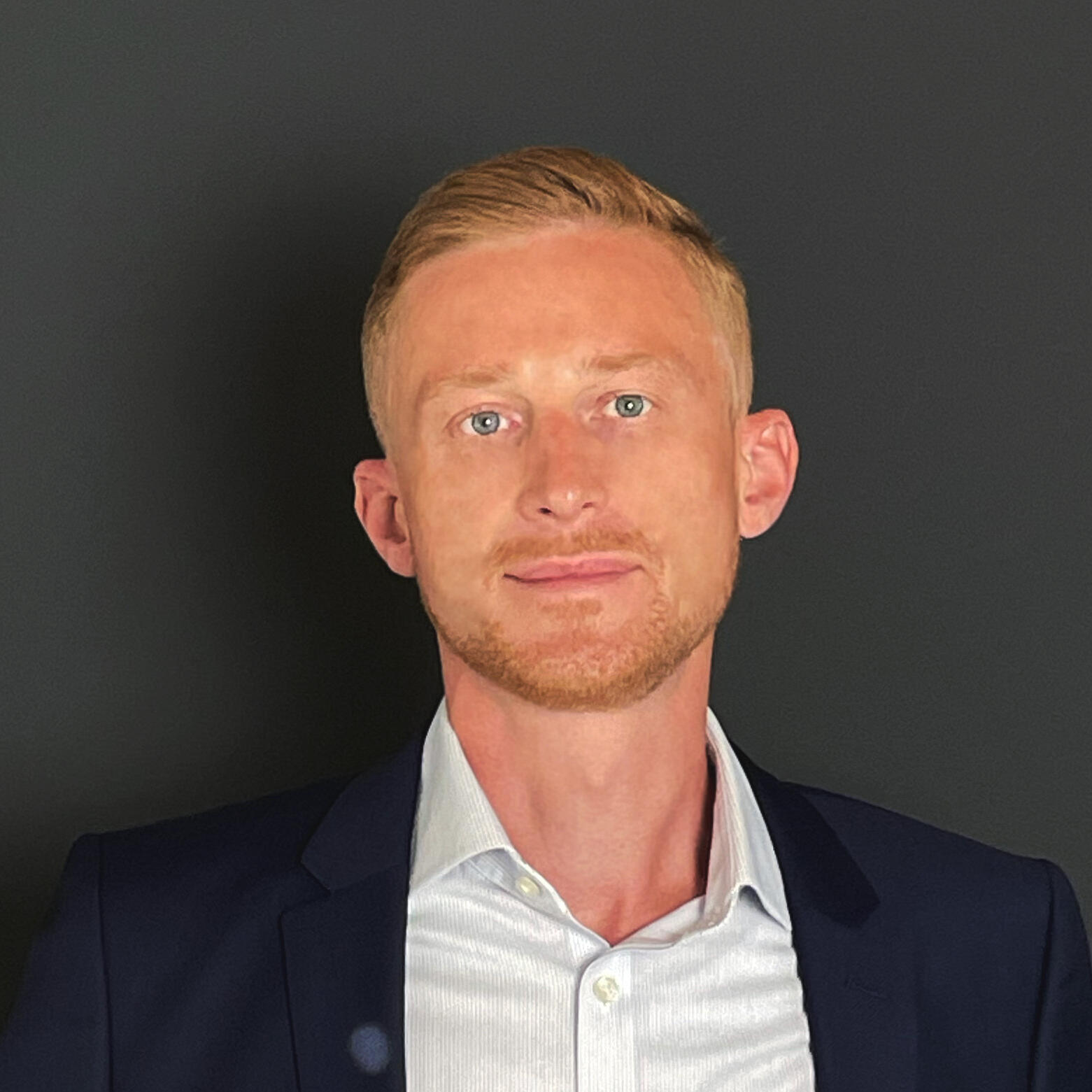
Dimitri Koneger
Sales Manager
Du hast Fragen zum Thema oder möchtest mehr über unsere Lösungen erfahren?
Kontaktiere uns und entdecke, wie unsere Produkte Deine Maschinen zukunftssicher machen. Lass uns gemeinsam herausfinden, wie wir Dir helfen können, Deine Produktion auf das nächste Level zu bringen!
- +49 241 93681-500
- contact@procom-automation.de
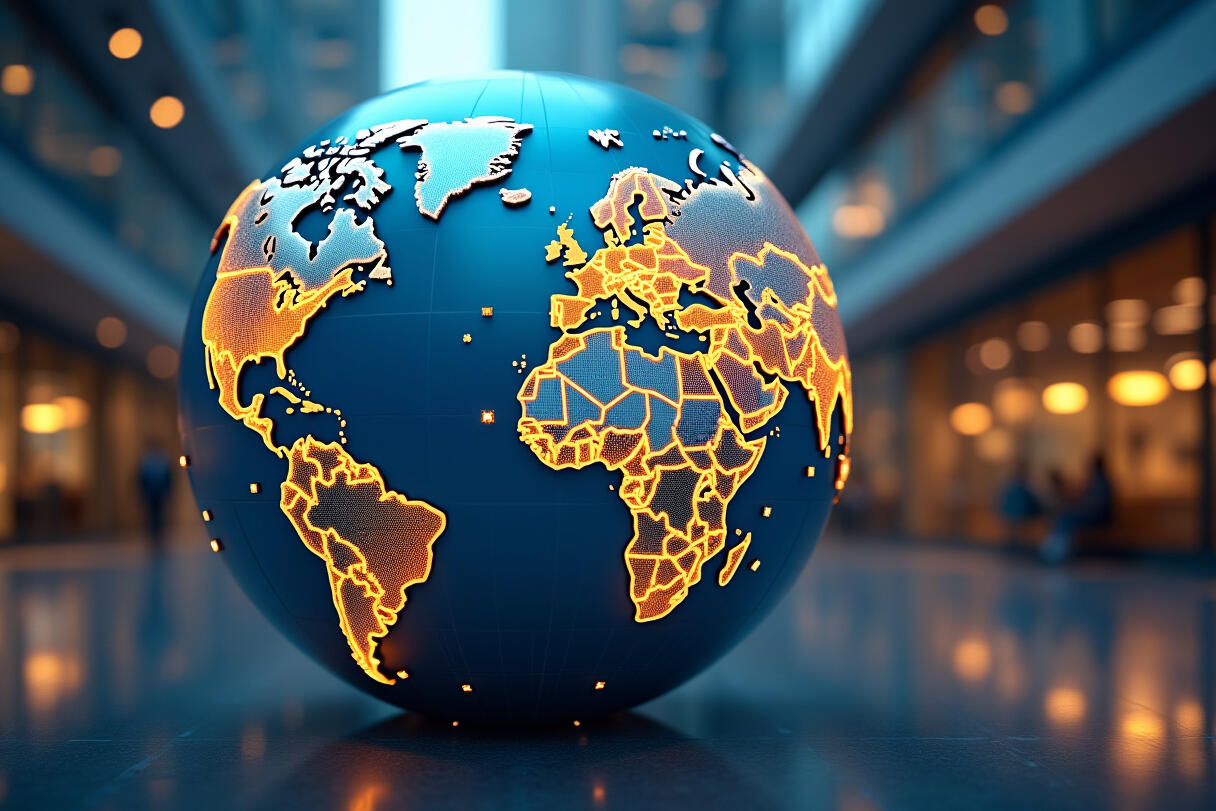
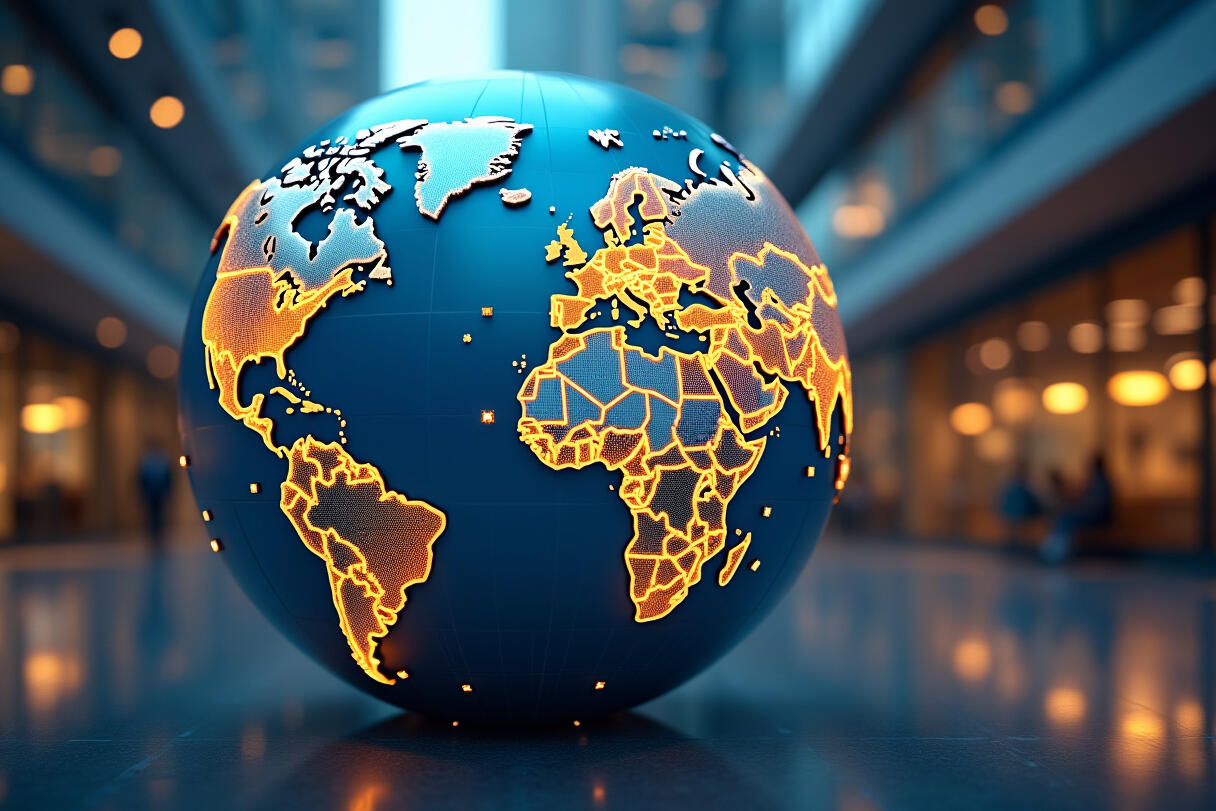