General Questions
What is Clouver?
Clouver is an IoT-based platform for real-time monitoring and optimisation of production processes. The software helps increase efficiency, reduce downtime, and support data-driven decision-making based on production data.
Which companies is Clouver suitable for?
Clouver is ideal for manufacturing companies across all industries – from metal and plastics processing to the textile sector. The platform is manufacturer-independent and compatible with all types of machines – including heterogeneous machine fleets and older legacy equipment.
What are the benefits of Clouver?
- Live insights into all production processes
- Improve performance through data-driven insights
- Prevent failures early on
- Identify consumption and reduce costs
- Identify root causes and improve availability
- Paperless, error-free and time-saving
- Flexible use – in the cloud or on-premises
- Compatible with all machines – old and new
- Seamless connection with IT systems
- Less effort and more transparency
- Relevant data, clearly visualised
- GDPR-compliant and protected in certified German data centres
How secure is my data with Clouver?
Data security is a top priority. Clouver uses state-of-the-art encryption technologies and processes data in certified data centres located in Germany – all in compliance with current data protection regulations.
How can I test Clouver?
We offer a free demo that allows you to explore Clouver with no obligations and speak directly with one of our experts about any technical questions. Simply book an appointment with our team.
How much does it cost to use Clouver?
With Clouver, you can tailor a solution to fit your specific needs. Pricing depends on the type and number of machines. Clouver is designed to be flexible and scalable, so it can grow along with your business.
Contact: Book an appointment
Can I connect Clouver with my ERP system?
Yes, that is possible! If your ERP system supports data export via the MQTT network protocol, the integration can be carried out without any further steps. Otherwise, the SmartKit can be used to create an interface between the ERP system and Clouver.
Either way, we’ll ensure a solution that allows you to bring data from your production planning and job management systems to your machines, and transfer machine data collected via Clouver back into your ERP system.
Which consumption meters can be connected to Clouver?
Clouver supports the integration of the following types of consumption meters:
- Electricity meters
- Water meters
- Gas meters
What analysis options does Clouver offer for consumption data?
Consumption data can be analysed flexibly on an hourly, weekly, monthly, or yearly basis. This gives you detailed insights into the resource usage within your production environment.
Features & Technical Details
What features does Clouver offer?
- Real-time monitoring
- OEE analysis (Overall Equipment Effectiveness)
- Predictive maintenance
- Energy monitoring
- Downtime tracking
- Paperless production
- Cloud and edge computing
- Machine connectivity
- ERP integration
- Automated reporting
- Custom dashboards
- Data security and compliance
How does integration with existing systems work?
Clouver can be connected to existing IT and ERP systems via open interfaces (APIs). The integration is flexible and can be linked to machine controls, sensors, or existing data sources.
Do I need new hardware for Clouver?
Apart from the SmartKit units, no new hardware is usually required. Clouver can use existing machine interfaces and sensor signals to monitor machine status. If needed, we can support you in selecting suitable IoT hardware to connect older machines.
What hardware components, devices, and sensors are needed to collect relevant data?
The required hardware can range from easy-to-use, non-invasive current clamps and gateways with data interfaces to tailored sensor packages for your machines. In most cases, we use our SmartKit gateways.
To factor in the "human element" in production, we also rely on the touch panels used in our DowntimeAnalytics and Paperless solutions. We provide a complete package for you.
Contact: Book an appointment
Is Clouver suitable for companies of all sizes?
Yes, Clouver is scalable and can be adapted to small, medium, and large companies. Its modular architecture allows for gradual implementation based on your individual needs.
What types of data can be collected with Clouver?
Clouver consolidates data from various areas:
From your machines, depending on the interface, Clouver collects production-related information such as:
- Status information
- Production events
(downtimes, shift changes, number of parts produced, etc.) - Machine availability and failures
- Performance data
- Quality data
(e.g. through scrap detection)
From your staff, Clouver gathers detailed information on:
- Downtimes
- Service activities
- Manual operations
From your overarching MES or ERP systems, Clouver completes the picture with:
- Data on manufactured products
- Materials used
- Work orders
- Planning information
With Clouver, you centralise all of this information, enabling you to use it effectively in production, as well as for managing and optimising your entire manufacturing process.
How long does it take to implement Clouver?
Implementing Clouver is straightforward, as we meet you where you currently are. We support you every step of the way – from your first steps in digitising a bottleneck machine, to digitising and monitoring your production line, all the way to developing a full digitalisation strategy for your entire business.
This might also be of interest to you
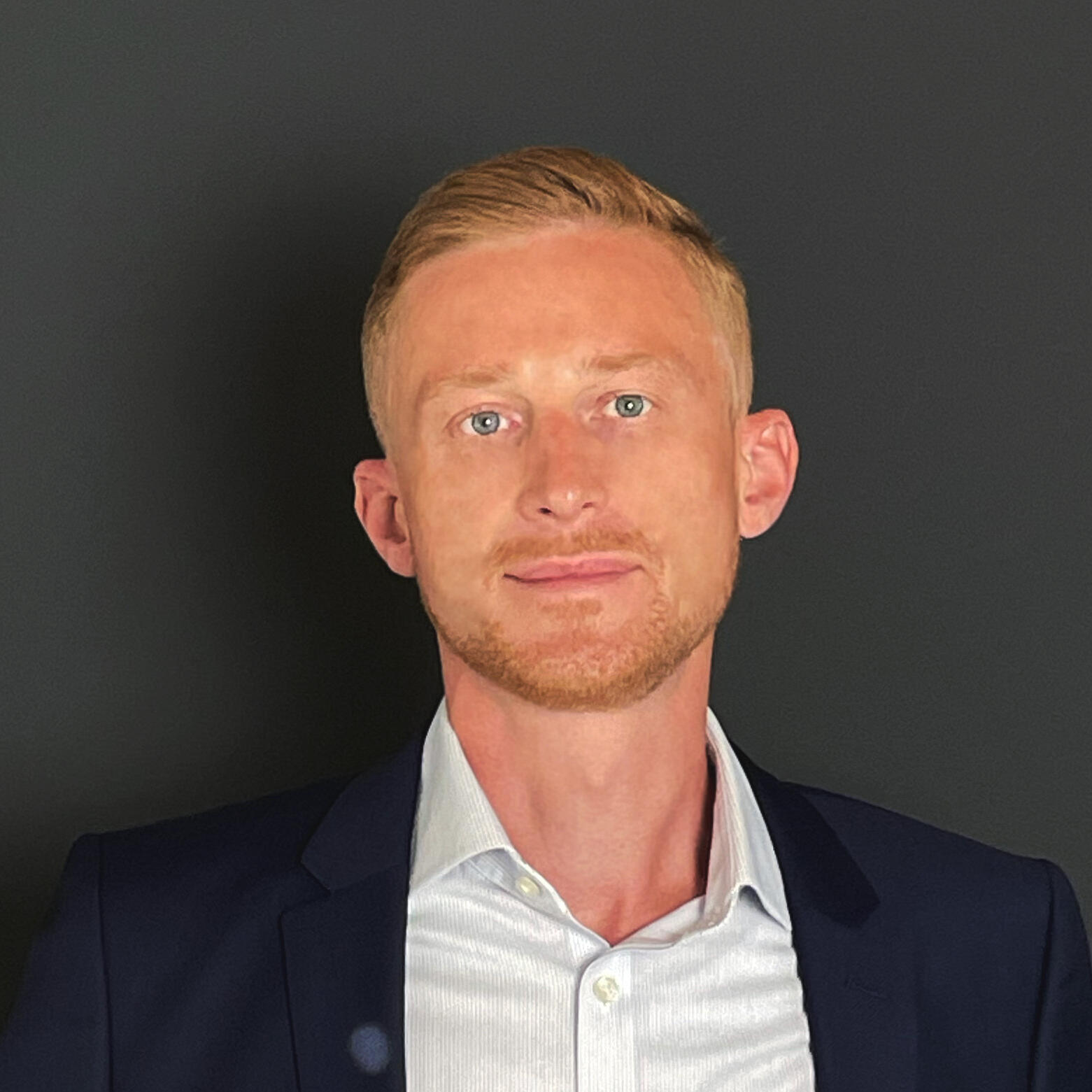
Dimitri Koneger
Sales Manager
More Information? Reach Out to Us!
Learn more about our products, services, and potential collaboration. Simply get in touch with us by phone or email. I look forward to a personal exchange!
- Phone: +49 241 93681-500
- Email: contact@procom-automation.de