Maximum Performance
Tailored to the requirements of plasma cutting and equipped with numerous specific functions, ProCom Automation's control solution achieves the highest cutting precision and maximum speeds. With the comprehensive package of software, hardware, and drive technology, you control your plasma cutting machines with utmost precision, ensuring optimal efficiency.
The high cutting speed and the ability to penetrate thick materials make plasma cutting ideal for industrial applications. With ProCom Automation's CNC control solution, you maximise the efficiency of this technology through precise control and customisable options.
Leverage Our Expertise
With ProCom Automation's CNC control you get a solution precisely tailored to your plasma cutting machine. Through collaborative efforts, we address your specific needs and develop a control solution that ensures your machines deliver highest precision and best productivity.
Benefit from our extensive experience and technical know-how in the field of plasma cutting.
The Control Solution's Highlights
- High-definition and conventional plasma cutting
- Kerf and bevel compensation
- Parametrisable ignition interval
- Integrated height control
- Determination of nozzle change by monitoring the number of ignitions
and effective cutting time - Fully automated resuming with automated lead-in after beam breakage
- Graphic-interactive start point determination
- Slope correction of the material via joystick and laser pointer
- Activation of different tools
- Equipping the machine with different cutting heads
- OPC UA interface for capturing operational data and integrating your machine into production processes
Your Advantages as a Machine Builder
Choose ProCom Automation's control solution and benefit from numerous valuable advantages:
Intelligent, Technology-Specific Motion Algorithms
For maximum performance of your cutting machines and precise cutting results at the highest level.
All-In-One Control Solution
CNC and CAM software, control hardware, and drive technology – get them all in one package or choose the component(s) you need.
Custom Functionality Adaptation
Custom development according to your wishes and requirements.
Fast Commissioning
Your machine with the ProCom Automation control solution is ready for operation in no time.
Professional Support
Reliable and personal support from our staff: on-site during commissioning as well as for all technical questions.
Personal Service
A personal contact for all concerns at any time – trust in the advice and support from our experts, along with guaranteed assistance for all technical inquiries.
Future-Oriented Development
Continuous optimisation of functions and motion algorithms based on current and future market requirements and customer needs.
Frequently Asked Questions
What does the complete solution package from ProCom Automation include?
As a ProCom Automation customer, you receive a complete solution package comprising the following components:
- CNC300PRO in the preferred configuration (i3, i5, or i7)
- CNC300 software solution package, consisting of ergoCNC® and ergoCAM® with the latest release version for textile cutting
- Drive technology from leading manufacturers
- Interface to the IIoT production monitoring platform Clouver for analysing your machine data
The software solution for textile cutting (cutter software) is available in three variants: Essential package, Professional package, and Premium package, which you can choose based on your requirements. Feel free to contact our experts for further, comprehensive advice.
Can we retrieve the machine operating data?
Yes, the control solution captures a set of operational data, which, for example, can be made available through the IIoT production monitoring platform Clouver.
Is it possible to have individual functions programmed?
If a function you need is not already included in the standard features of our solution, we are happy to explore the possibility of individual function extensions. Feel free to contact our experts for comprehensive advice.
Is there a suitable CAM solution?
Naturally! The CAM solution from ProCom Automation is part of your complete solution package. The ergoCAM® software forms a unified system with the ergoCNC® software, ensuring a seamless transition between your work preparation and the cutting process. For more detailed information, consult our experts who will happily provide comprehensive advice.
Can I get suitable drive technology with ProCom Automation?
Certainly! Suitable drive technology for the control solution is also part of your complete solution package. We have been working with leading manufacturers for many years, providing you with reliable and robust drive technology for smooth and precise movements.
How long does commissioning take?
Based on our experience, we estimate that initial commissioning of your machine in collaboration with your machine experts and our control experts, being pre-coordinated and well-prepared on both sides, can be successfully completed within 2-3 weeks at your facility.
What support do I receive during commissioning?
You will receive personal support from ProCom Automation experts on-site for the commissioning of the first pilot machine. This includes step-by-step checks of all motors, aggregates, sensors, and actuators, as well as the configuration and commissioning of their associated functions. Our experts on-site will perform the configuration and commissioning of all participants in the EtherCAT communication bus, the creation of the necessary complete EtherCAT configuration files, the required detailed parametrisation of all associated CNC parameters for the coordinated contour machining movements of all machine axes, as well as the control of all other tools and aggregates (vacuum control, extraction, material transport, etc.) for the pilot machine.
Our experts will accompany the fine-tuning and optimisation of the drive components and axis control loops, as well as the securing of the determined parameter files.
Additional serial machines will be set up and commissioned based on the parameter and configuration files created during the pilot machine project.
What are the prerequisites for serial production?
The CNC300PRO control solution is a mature and much-used solution in many facilities globally.
Once the necessary mechanical and electrical components, as well as the parametrisation and configuration of the CNC control, all I/O modules, and the drive components tailored to the respective machine, are set up and fine-tuned for a pilot machine, subsequent new machine installations will require only a minimal amount of time.
Additional serial machines will be set up and commissioned based on the parameter and configuration files created during the pilot machine project.
FUTHER DISCOVER THE VARIETY OF PROCOM AUTOMATION CONTROL SOLUTIONS
This might also be of interest to you
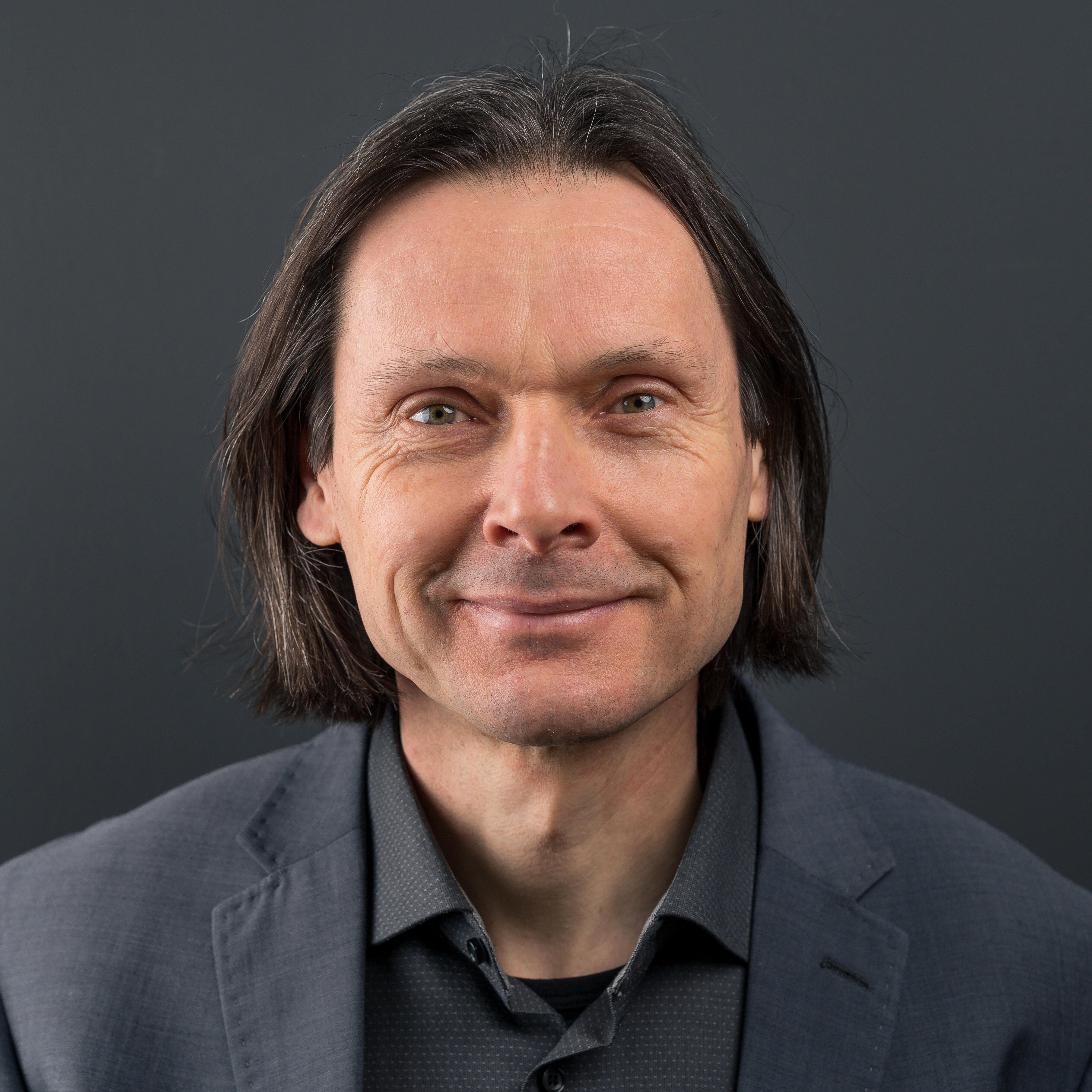
Harald Müller
Team Lead Delivery
More Information? Reach Out to Us!
Learn more about our products, services, and potential collaboration. Simply get in touch with us by phone or email. I look forward to a personal exchange!
- Phone: +49 241 93681-500
- Email: contact@procom-automation.de