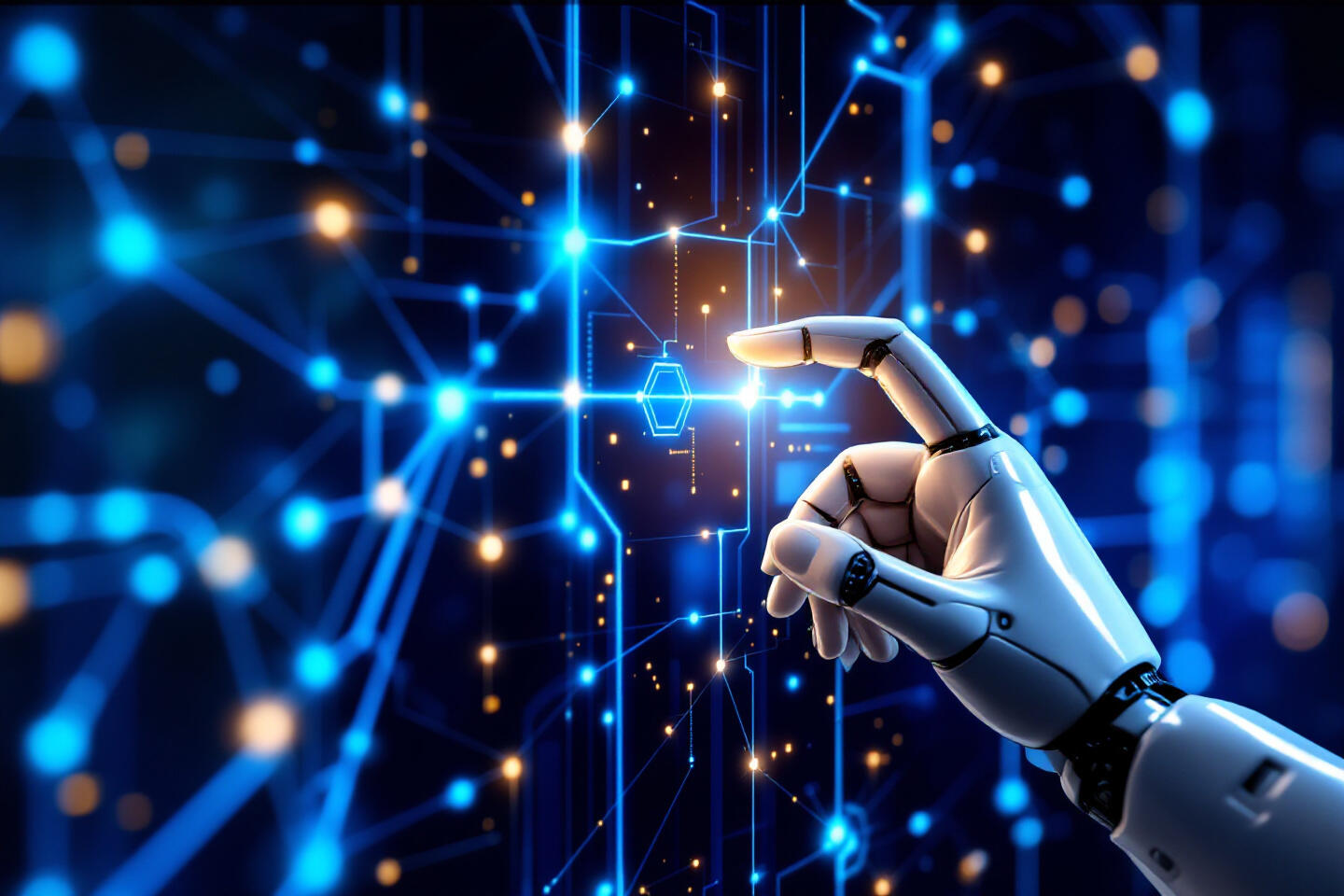
In today's fast-paced and technology-driven business world, you're probably looking for innovative ways to boost your efficiency and gain a competitive edge. One concept that's becoming increasingly important in this context is the digital twin. But what exactly does this term mean, and how can it revolutionise your business models?
A digital twin is a precise virtual representation of a physical object or system. This digital copy captures, analyses, and utilises real-time data to optimise processes, predict maintenance tasks, and develop entirely new business models. But how exactly does this work, and what technical prerequisites do you need to successfully implement a digital twin in your company?
What is a Digital Twin?
A digital twin is an exact digital copy of a physical object or system that is continuously updated with real-time data from the real world. In a business context, this can be applied to machines, production lines, entire factories, or even services. Imagine you have a virtual version of your CNC machines from ProCom Automation that captures and analyses all operational data in real-time. This digital representation allows you to run simulations, identify potential problems early, and optimise processes without having to physically alter the machine.
How Do Physical and Digital Business Models Differ?
Physical business models are based on traditional, tangible products and services. For example, the sale of machines or the provision of maintenance services. In contrast, digital business models use digital technologies and data to create added value and unlock new revenue streams. The digital twin is a key element of this digital transformation, as it enables the development of new business models through data-driven decisions and innovative service offerings. For example, you can offer new services based on the data of your digital twins through the production monitoring software Clouver from ProCom Automation.
How Has the Digital Twin Evolved?
The idea of the digital twin originated in the early 2000s and has continuously evolved since then. With the increasing prevalence of Industrial Internet of Things (IIoT) technologies and improvements in data analysis tools, the digital twin has gained significance. Today, it is a central component of Industry 4.0, which aims for a connected and intelligent factory. Companies like ProCom Automation use digital twins to optimise their production processes and develop innovative business models that were previously unthinkable.
What Technical Prerequisites Do You Need?
To successfully implement a digital twin, you need certain technical prerequisites. Sensors and Industrial Internet of Things devices continuously capture data from the real world. A real-time Ethernet protocol such as EtherCAT ensures fast and deterministic communication in automation systems. The OPC UA interface enables secure and reliable data exchange. A cloud connection, for example, via the Clouver Gateway from ProCom Automation, processes and stores the captured data. Data processing and analysis tools are necessary to evaluate and utilise the collected data.
How is Data Captured and Processed?
Data capture is achieved by integrating sensors and Industrial Internet of Things devices into your physical systems. These devices continuously collect data such as temperature, pressure, vibration, and other relevant parameters. Via a cloud connection, such as the Clouver Gateway from ProCom Automation, this data is processed and stored in real-time. Data processing involves cleaning, aggregating, and analysing the data to gain valuable insights that can be used to optimise your business processes.
What Interfaces and Protocols Are Necessary?
To ensure seamless communication between the various systems, standardised interfaces and protocols are essential. The OPC UA interface enables secure and reliable data exchange, while the EoE-Gateway (Ethernet over EtherCAT) optimises data transfer between devices. These interfaces ensure that data is transmitted efficiently and without delays, which is crucial for real-time analysis and simulation of a digital twin.
How Do You Integrate Sensors and Industrial Internet of Things Devices?
The first step to implementing a digital twin is selecting and integrating suitable sensors and Industrial Internet of Things devices. These devices capture the necessary data from the physical world, such as the operating hours of CNC machines from ProCom Automation. A careful selection of sensors is critical to accurately capture the relevant data and provide a reliable foundation for the digital representation.
How Does Cloud Connectivity and Data Management Work?
The captured data is processed and stored via a cloud platform like the Clouver Gateway from ProCom Automation. This allows for centralised management and analysis of the data, regardless of the location of the physical systems. By using cloud technologies, you can flexibly and scalably access and analyse your data, supporting efficient decision-making and process optimisation.
How Do You Ensure Data Security and Privacy?
Data security is a critical aspect of implementing digital twins. You must implement appropriate security measures such as encryption, access controls, and regular security audits to protect your data from unauthorised access and cyber-attacks. ProCom Automation offers comprehensive security solutions to ensure that your data is protected and the integrity of your digital twin is maintained.
What Business Model Innovations Are Possible?
Predictive maintenance uses the data from the digital twin to predict maintenance needs and minimise downtime. By analysing operational data from your CNC machines from ProCom Automation, you can precisely determine when maintenance is needed before a failure occurs. This leads to more efficient use of resources, extended machine life, and significant cost savings. Read more about predictive maintenance in our article on the subject.
What New Service Offerings Can You Develop?
By analysing the data from the digital twin, you can develop new service offerings, such as remote monitoring services or customised maintenance plans. With the production monitoring software Clouver from ProCom Automation, you can offer your customers continuous monitoring and optimisation of machine performance, significantly increasing the value of your services and opening up new revenue streams.
Pioneering Technologies for Your Manufacturing!
With ProCom's high-tech solutions, you can digitise workflows, reduce downtimes, and make your production smarter. Contact us now for a no-obligation consultation!
How Does the Digital Twin Support Product Development?
Digital twins enable more precise and faster product development by performing simulations and tests in a virtual environment. You can virtually test different design variants of your machines from ProCom Automation before creating physical prototypes. This shortens development time, reduces costs, and improves product quality. Learn more about Computer-Aided Design in our blog.
How Can You Offer Remote Monitoring Services?
With a digital twin, you can offer your customers remote monitoring services that allow continuous monitoring and optimisation of machine performance. By using Clouver from ProCom Automation, customers can access real-time data at any time, monitor machine performance, and respond to potential problems immediately without being on-site.
What Practical Use Cases Are There?
Digital twins enable precise control and monitoring of machines in real-time. With CNC machines from ProCom Automation, you can continuously monitor and optimise operating conditions. This leads to improved performance, higher efficiency, and reduced downtime as you can react immediately to deviations.
How Do You Improve Quality Control?
By continuously monitoring and analysing production data, you can significantly improve the quality of your products. With a digital twin, for example, you can monitor the cutting quality of your machines from ProCom Automation in real-time and make adjustments to ensure consistently high-quality standards. Learn more about quality control in our blog.
How Do You Optimise Processes?
Digital twins help identify inefficient processes and make real-time adjustments to improve overall performance. You can identify bottlenecks in your production, optimise material flow, and maximise resource utilisation, leading to a significant increase in productivity. Read more about process optimisation in our guide.
How Do You Plan Maintenance More Efficiently?
By using data such as the Operating Hours Counter, you can carry out a more precise and efficient maintenance plan. This avoids unplanned downtime and prolongs the lifespan of your machines from ProCom Automation. Well-planned maintenance ensures that your production lines are always functioning optimally. Read more about predictive maintenance in our article on the topic.
What Cost Savings Are Possible?
By optimising processes and predictive maintenance, you can achieve significant cost savings. You avoid costly downtime, reduce maintenance effort, and can use your resources more efficiently. The implementation of a digital twin from ProCom Automation quickly pays off through these savings.
How Do You Increase Efficiency?
Continuous monitoring and analysis of data lead to improved efficiency and productivity. You can identify bottlenecks early, optimise processes, and maximise the utilisation of your machines. With the production monitoring software Clouver from ProCom Automation, you achieve optimal performance from your equipment. Learn more about efficiency improvement in our blog.
What New Revenue Streams Can You Tap?
Digital twins open up new business opportunities and revenue streams. By selling remote monitoring services or developing customised maintenance plans, you can generate additional revenues. These new services offer significant added value to your customers and strengthen your business at the same time.
What Competitive Advantages Do Digital Twins Offer?
Companies that use digital twins are better equipped to respond to market changes and secure their competitiveness. You can respond to customer requirements more quickly, offer innovative products and services, and stand out from the competition through higher efficiency and quality. Learn more about competitive advantages through digitalisation in our blog.
How Does Data-Driven Decision Making Support Your Business?
The use of predictive analytics and real-time monitoring enables data-driven decision-making and continuous optimisation of business processes. With the detailed data from the digital twin, you can make informed decisions based on concrete insights, thereby enhancing the overall performance of your company.
How Do You Integrate the Digital Twin into Existing Systems?
The seamless integration of the digital twin into existing ERP and MES systems is crucial for successful implementation. ProCom Automation offers comprehensive solutions to ensure that your digital twins communicate smoothly with your existing systems and seamlessly support your business processes. Learn more about integration into existing systems in our blog.
How Do You Manage Change in the Company?
The introduction of a digital twin requires adjustments to organisational processes and the qualification of employees. Effective change management ensures that your employees understand and can use the new technologies, and that changes in the company run smoothly. ProCom Automation supports you in successfully implementing these changes.
What Are the Current Trends and Developments?
The integration of artificial intelligence (AI) into digital twins enables even more precise analysis and optimisation of processes. AI algorithms can recognise patterns in the data, make predictions, and support automated decisions, significantly increasing the efficiency and accuracy of your business processes. Learn more about current trends in our blog.
How Do Digital Twins Contribute to Sustainability?
Digital twins help optimise resource use and reduce carbon footprints. By precisely monitoring and controlling your production processes, you can minimise energy consumption and waste, which not only saves costs but also protects the environment. Learn more about sustainability in industry in our blog.
How Do You Integrate Digital Twins into Industry 4.0?
Digital twins are a central component of Industry 4.0 and enable the implementation of smart factory concepts and full automation of production. With a digital twin, you can design flexible and intelligent production processes that quickly adapt to changing market conditions.
What Practical Implementation Aspects Are Important?
Implementing a digital twin requires a suitable sensor infrastructure, stable network connectivity, and powerful data processing systems. ProCom Automation ensures that you have the necessary technical resources to efficiently and reliably operate your digital twin. Learn more about implementation aspects in our blog.
What Organisational Aspects Should Be Considered?
Successful project management, careful resource planning, and effective stakeholder management are crucial for the successful implementation of a digital twin. It is important to involve all relevant departments and establish clear communication channels to ensure collaboration and project success.
Why Should You Invest in Digital Twins?
Digital twins offer immense benefits for modern business models by enabling precise simulations and real-time monitoring. By integrating technologies such as the Clouver platform from ProCom Automation, you can increase efficiency, optimise maintenance, and reduce production costs. The versatile applications and high ROI make the digital twin an indispensable technology for forward-thinking companies.
Discover how ProCom Automation can help you transform your business models with digital twins. Visit our blog for more information or book a demo version of Clouver to experience the benefits for yourself.