Industrial production is at a significant turning point. With the advancement of digitalisation and the introduction of Industry 5.0, new technologies and concepts are emerging that aim to optimise the efficiency, flexibility, and sustainability of production processes. In this context, IIoT Monitoring (Industrial Internet of Things) plays a central role. It connects machines, people, and data in an intelligent network, enabling companies to make informed decisions in real-time. This article explores the relationship between IIoT monitoring and Industry 5.0, discusses key KPIs, and explains how companies can successfully implement an IIoT monitoring platform.
Industry 5.0 and IIoT Monitoring: A Strong Duo
Industry 5.0 brings humans back into the spotlight of production and promotes collaboration between humans and machines. While Industry 4.0 was primarily shaped by automation and connectivity, Industry 5.0 expands these concepts by adding the human factor. IIoT monitoring plays a crucial role here. It enables the continuous monitoring and analysis of production processes, not only improving efficiency but also enhancing collaboration between humans and machines.
Industry 5.0 emphasises the role of humans in production, integrating individual skills and expertise into processes. This new era is about combining the strengths of automation and artificial intelligence with the creativity, flexibility, and problem-solving abilities of humans.
While Industry 4.0 focused on automation, often reducing manual interventions, Industry 5.0 recognises the added value humans bring in complex and unpredictable situations. Machines can analyse large amounts of data and efficiently perform repetitive tasks, but it is humans who, with their experience and judgment, find innovative solutions and continuously improve processes.
IIoT monitoring plays a key role in this context, providing humans with relevant information and tools to make informed decisions. It enables a symbiosis between humans and machines, where humans are not just supervisors but are actively involved in the production process, using data-driven insights to control and optimise their work. By integrating IIoT monitoring into Industry 5.0, companies can monitor the condition of their machines in real-time and respond early to deviations or potential problems. This is critical to increasing production flexibility and adaptability while maintaining high quality and efficiency.
The Importance of KPIs in Industry
Monitoring and analysing Key Performance Indicators (KPIs) is an essential part of IIoT monitoring and a central aspect of Industry 5.0. Key KPIs in modern industrial production include Overall Equipment Effectiveness (OEE), which measures machine efficiency and product quality on a broad scale. OEE consists of the components availability, performance, and quality, and serves as an indicator of machine or production line productivity. Continuous monitoring of OEE through IIoT monitoring can identify weaknesses and reveal optimisation potential.
Another important KPI is machine availability, which measures the proportion of time a machine is productively in use. High availability signals well-maintained and reliable equipment, which in turn increases productivity. Throughput, which measures the amount of units produced within a given period, is also a critical indicator of production efficiency.
Additionally, monitoring First Pass Yield (FPY) plays an important role. FPY shows the proportion of products that meet quality standards in the first production run without rework. A high FPY value indicates stable and efficient production processes. Given the growing pressure to produce more sustainably, energy consumption monitoring is becoming an increasingly important KPI. Companies that continuously monitor their energy consumption can not only improve their environmental footprint but also reduce energy costs.
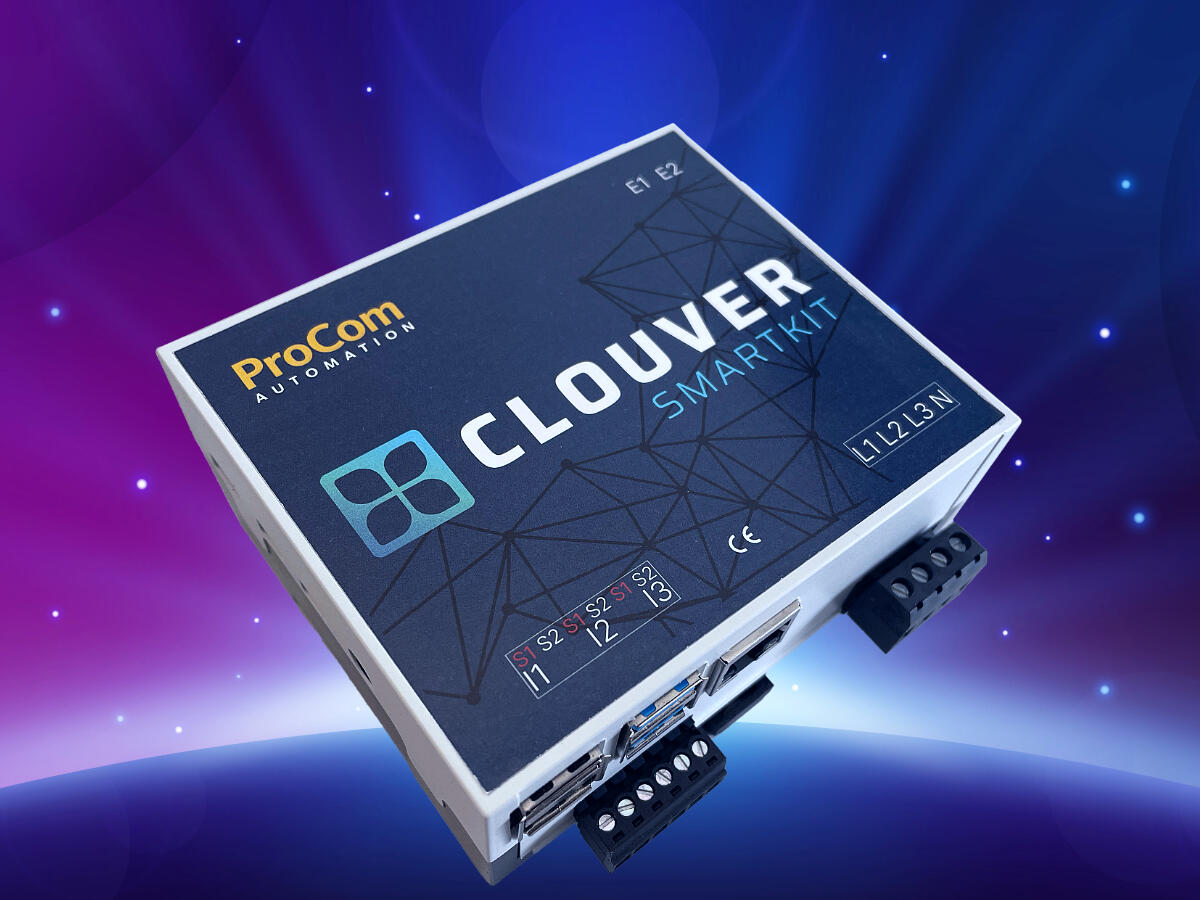
Implementing IIoT Monitoring Platforms
Introducing an IIoT monitoring platform requires careful planning and execution. Companies must first consider how best to connect their machines to the IIoT platform. For older machines that are not IIoT-ready, retrofit solutions offer a cost-effective way to network them. Sensors and communication modules are installed on the machines to collect relevant data and transmit it to the IIoT platform. For new machines already designed for integration into IIoT platforms, plug-and-play systems are available. These allow for quick and easy connectivity without the need for extensive configuration. Additionally, smart kits offer a flexible way to integrate various types of machines into an IIoT platform. These kits contain pre-configured hardware and software solutions that enable rapid implementation.
When selecting the right IIoT monitoring tool, companies should consider several key criteria. A crucial requirement is the platform’s scalability. It must be able to keep pace with the company’s growing demands, especially when production is expanded or diversified. The user-friendliness of the platform is also essential. An intuitive interface and ease of use are critical to ensuring that employees can efficiently utilise the system. This reduces training times and increases adoption. The platform must also ensure interoperability. It should seamlessly integrate into existing systems such as ERP, MES, or SCADA, allowing all relevant data to be consolidated and comprehensively analysed. Finally, data security must not be overlooked. The platform should support modern security standards such as data encryption and access controls to protect sensitive production data.
Another important criterion is real-time data processing. To respond quickly to changes in production, the platform should collect and process data in real-time. This enables companies to respond immediately to disruptions or deviations, thereby ensuring the efficiency and quality of their production.
Successful Implementation and Continuous Optimisation
Introducing an IIoT monitoring platform is just the first step towards Industry 5.0. Companies must ensure that the data they collect is continuously used to improve production processes. This requires close collaboration between IT and production teams, as well as regular training and further education for employees.
Conclusion
Industry 5.0 represents the next evolutionary stage of industrial production, requiring close collaboration between humans and machines. IIoT monitoring plays a crucial role by enabling continuous monitoring and optimisation of production processes. Selecting the right KPIs and implementing a suitable IIoT monitoring platform are key factors for success. Companies that pursue this path can not only enhance their efficiency and flexibility but also position themselves as leaders in modern industrial production.
Sparked Your Interest?
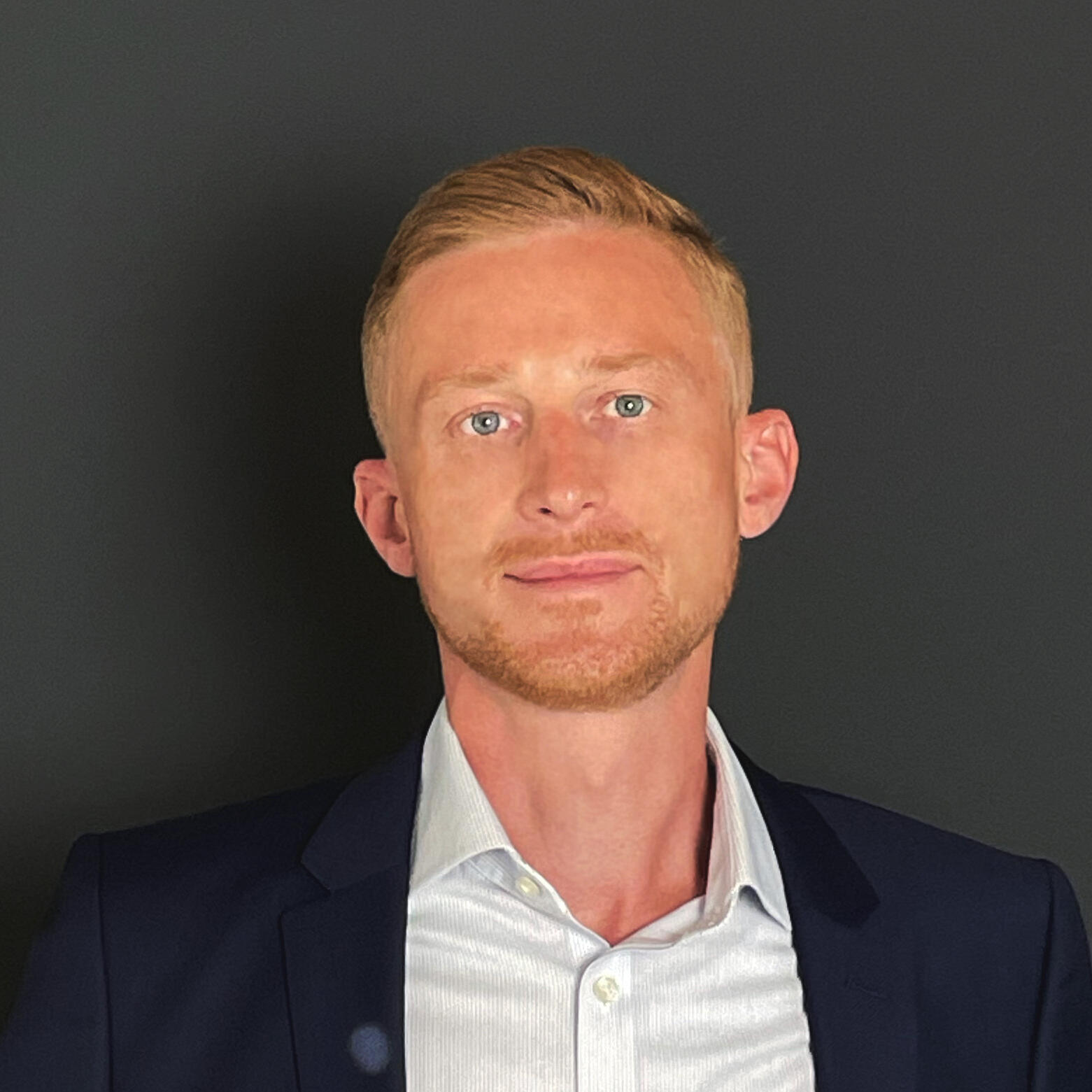
Dimitri Koneger
Sales Manager
Have questions about the topic or want to learn more about our solutions?
Contact us and discover how our products can future-proof your machines. Let’s work together to find out how we can help take your production to the next level!
- Phone: +49 241 93681-500
- Email: contact@procom-automation.de