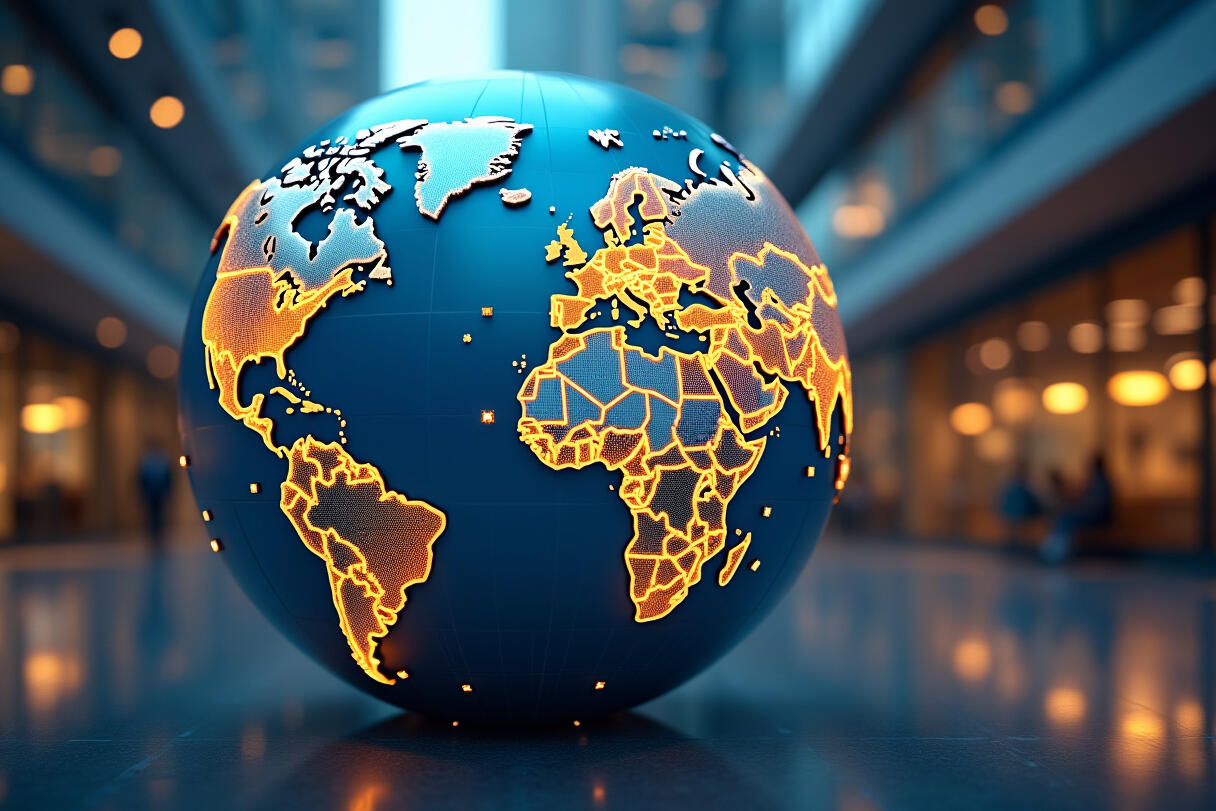
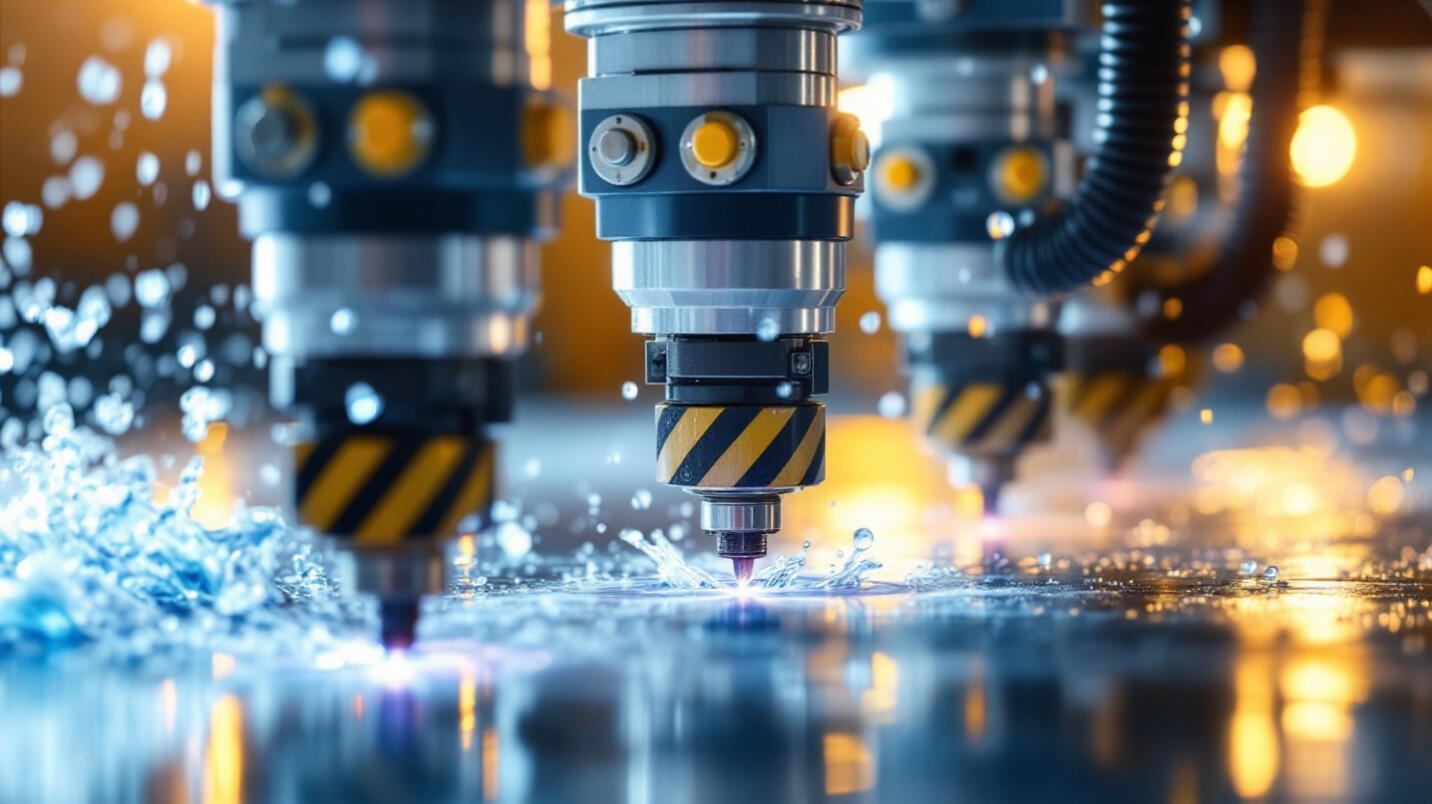
Are you facing the challenge of cutting complex shapes precisely whilst preserving material properties? Are you looking for a flexible solution for various materials? Then 5-axis water jet cutting might be exactly what you need. In this guide, you'll learn everything you need to know for the successful implementation of this technology.
What Makes 5-Axis Water Jet Cutting So Special?
Imagine being able to cut any material – from steel to glass – with the highest precision, without affecting it through heat. That's exactly what 5-axis water jet cutting enables. With a high-pressure water jet, reinforced by abrasives like garnet sand, you can cut even the most complex shapes.
The uniqueness lies in the system's exceptional mobility. Thanks to the five movement axes, you can reach any angle and even difficult-to-access areas. This gives you not only maximum flexibility in shaping but also highest precision without any material alterations. This versatility makes the technology a true all-rounder in modern manufacturing.
What Concrete Benefits Do You Bring to Your Manufacturing?
Compared to conventional cutting methods, 5-axis water jet cutting offers you decisive advantages. Unlike laser or plasma cutting, the material properties remain completely intact as no heat is applied. You can cut complex 3D shapes with minimal tolerances whilst utilising an impressive variety of materials – from metal to stone to sensitive materials like rubber.
Particularly interesting for your cost calculation: You save time and money through minimal waste and significantly less post-processing. The process also scores points in terms of sustainability. With modern water recovery systems and recyclable abrasives, you make your manufacturing process environmentally friendly and resource-efficient.
Your Practical Guide: How to Master 5-Axis Water Jet Cutting
Successful implementation begins with the right system configuration. You need a powerful high-pressure pump that you can flexibly adjust – ideally up to 4,000 bar. Precise CNC control ensures exact movements, whilst a suitable CAD/CAM system provides the programming foundation. The setup is completed by an efficient water treatment and recycling system.
Optimising your cutting parameters plays a central role in achieving perfect results:
- Water pressure should be higher for hard materials than for soft ones
- Adjust the feed rate according to material thickness and hardness
- Amount of abrasive varies depending on the material – more for hard materials, less or none for soft materials
- Optimise the cutting angle for best cut quality
Practical Application for Optimal Results
As a beginner in the technology, it's best to start with simpler 2D cuts. This way, you'll get to know and understand the system's basics. Initially, use the predefined parameters for standard materials – they provide you with a solid foundation. It's important that you perform regular calibrations from the start and carefully document your settings and results. This documentation will be very useful later when optimising your processes.
With growing experience, you can venture into more complex 3D contours. Experiment with cutting parameters for special materials and develop your own process strategies. The integration of quality monitoring systems will help you achieve consistently high-quality results.
Would you like to learn more about how you can optimally implement this innovative technology in your organisation?
We're happy to support you in analysing your specific requirements and finding the best solution for your manufacturing together. Contact us for individual consultation – we look forward to discussing your project with you!
Industry-Specific Applications and Solutions
Automotive Industry
In the automotive industry, 5-axis water jet cutting has proven particularly valuable in manufacturing precise body parts and complex engine components. The technology enables you to produce high-quality components with tight tolerances. The strength of the cold cutting process is especially evident in the production of special sealing systems.
Aerospace Industry
The aerospace industry benefits primarily in the processing of titanium components and composite materials. Here, absolute precision is crucial – every cut must be perfect and documented. Quality assurance plays a particularly important role in this sector.
Medical Technology
In medical technology, the process enables you to manufacture implants, surgical instruments, and prosthetic components. The special strength here lies in absolute material preservation and the ability to ensure sterile processes.
Future-Proof Production Design
The integration of modern digitalisation technologies opens up new possibilities for process optimisation. Through real-time monitoring of cutting parameters, you can immediately recognise deviations and react accordingly. Predictive maintenance helps you minimise downtime, whilst digital twins support process optimisation. AI-supported quality control optimally complements your quality management.
Sustainability plays an increasingly important role in modern manufacturing. With a well-designed water recycling system, you significantly reduce your water consumption. Energy-efficient components lower your power consumption, whilst recycling abrasives saves costs and conserves resources. Through clever nesting of cutting patterns, you also minimise material waste.
Your Path to Successful Implementation
The first step toward successful implementation is a thorough analysis of your specific requirements. Consider carefully which materials you will primarily process and what accuracies you need. Your planned production volume also plays an important role in system selection.
When planning your investment, you should carefully compare different systems. Calculate the return on investment considering all factors – from acquisition costs through maintenance to ongoing operating costs. An often underestimated aspect is employee training. Invest in comprehensive training for your machine operators and programmers. Regular safety training is also essential.
Conclusion: Your Competitive Advantage Through Innovative Technology
As a modern manufacturing technology, 5-axis water jet cutting offers you enormous possibilities. You benefit from highest precision with maximum flexibility whilst being able to produce sustainably. With proper implementation and continuous process optimisation, you create a significant competitive advantage.
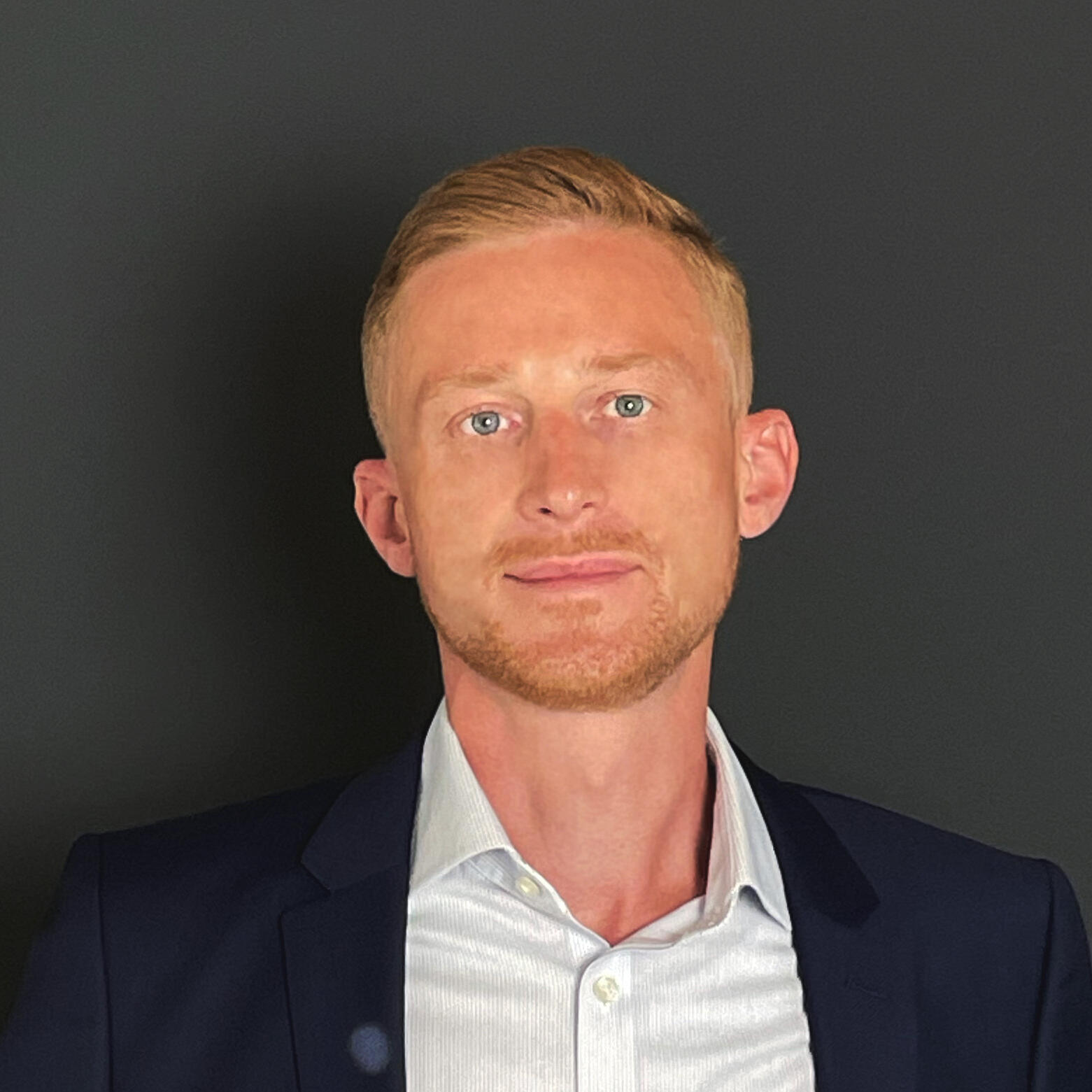
Dimitri Koneger
Sales Manager
Have questions about the topic or want to learn more about our solutions?
Contact us and discover how our products can future-proof your machines. Let’s work together to find out how we can help take your production to the next level!
- +49 241 93681-500
- contact@procom-automation.de
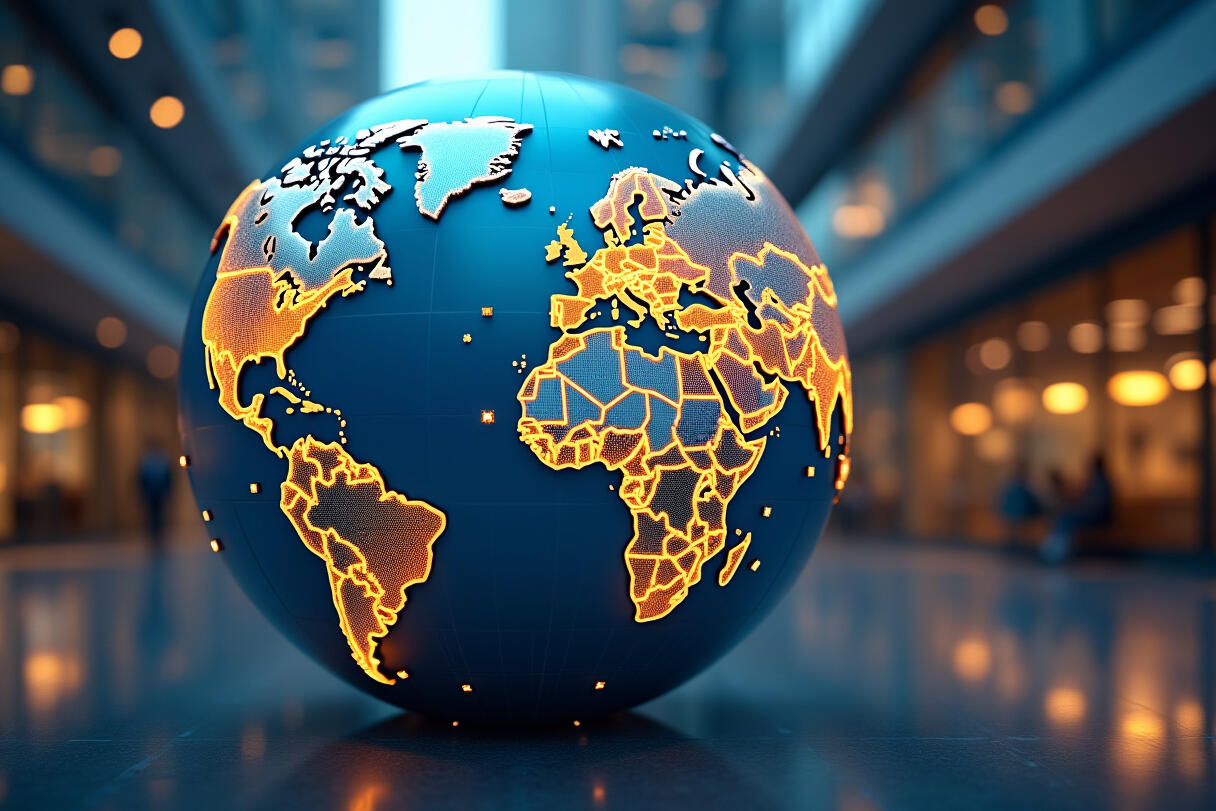
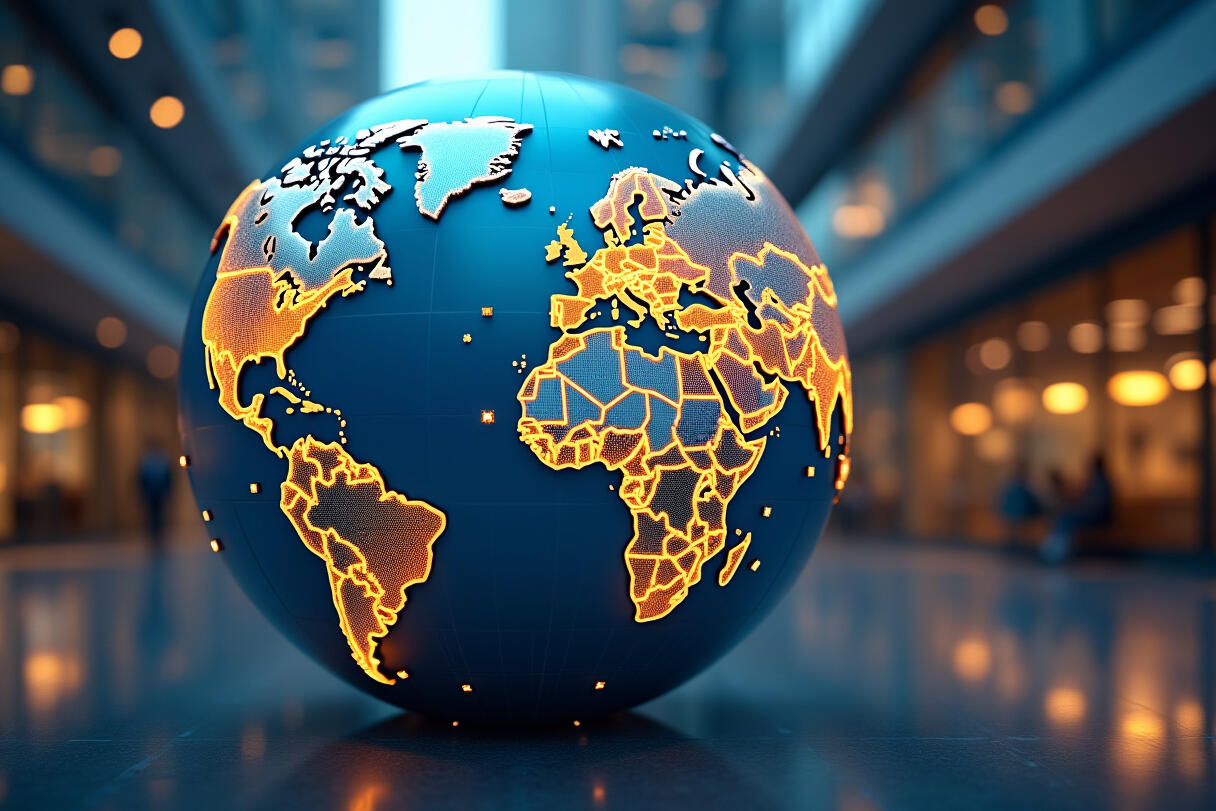