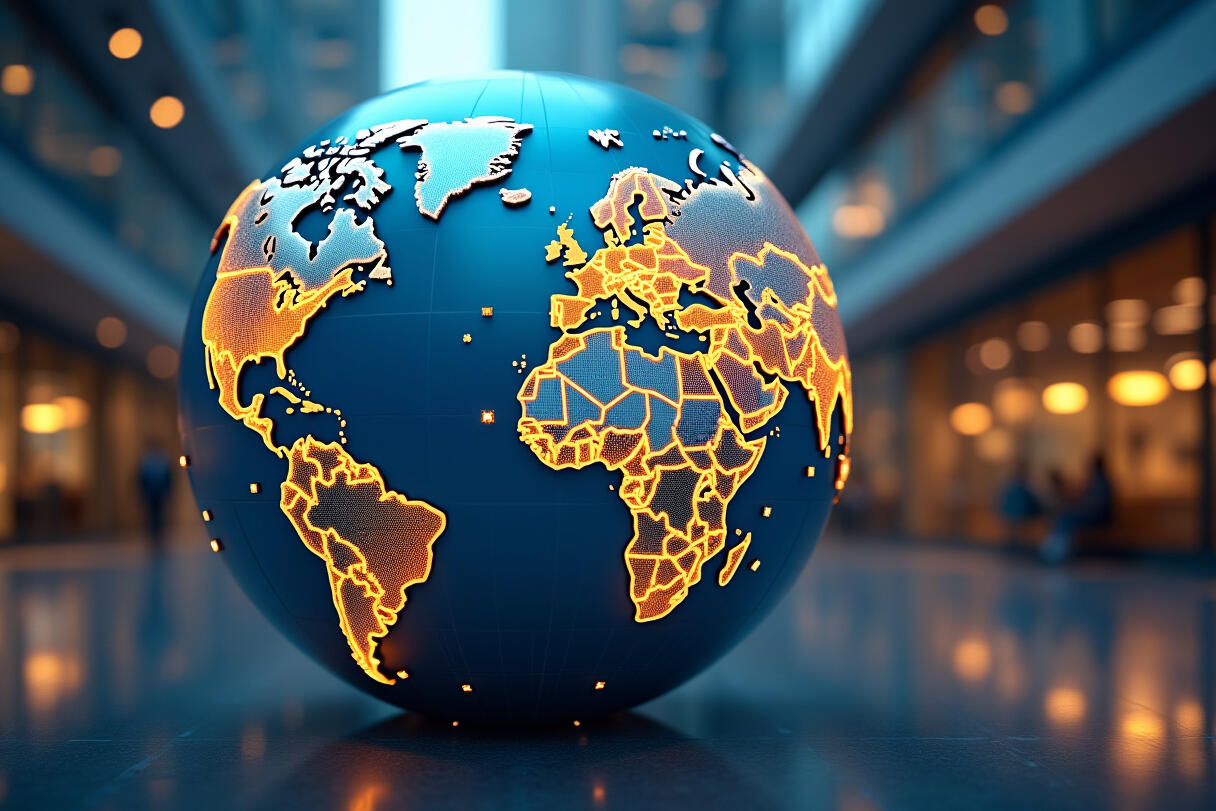
How Do You Increase Precision and Efficiency in Your Cutting Processes?
Precise and efficient cutting processes are crucial for success in today's manufacturing industry. Yet many production managers face the challenge of improving their cutting quality whilst optimising operating costs. Modern band knife technology offers the solution here - but only with the right know-how can its potential be fully exploited. In this guide, you'll learn how to elevate your cutting processes to the next level through intelligent band knife technology.
Why Are Modern Band Knives the Key to Better Cutting Results?
The evolution of band knife technology reflects the continuous progress in industrial manufacturing. What began as a simple mechanical tool in the 19th century has developed through intensive research and technological innovation into a high-precision cutting solution. This evolution was driven by industry's increasing demands for precision, efficiency and process reliability.
Modern band knives today combine various key technologies that enable their superior performance. Material development stands at the forefront. Through decades of metallurgical research, steel alloys have been developed that offer an optimal balance between hardness and flexibility. These special alloys are further refined through innovative coating technologies. Multi-layer coatings based on titanium nitride or chromium carbide not only increase wear resistance but also optimise cutting behaviour through reduced friction and improved heat dissipation.
Another crucial advancement lies in the precision processing of cutting edges. Modern manufacturing processes enable cutting geometries that are precisely matched to the respective cutting material. Through the use of computer-controlled grinding processes, cutting edges are created that are not only extremely sharp but also absolutely uniform along the entire length of the band knife. This precision is crucial for cut quality and tool service life.
The integration of sensors directly on the band knife also enables continuous monitoring of all relevant parameters during the cutting process. Modern sensors detect not only band tension and guidance but also temperatures, vibrations and wear conditions. This data forms the basis for intelligent process control that optimises cutting parameters in real-time and identifies potential problems early.
How Do You Maximise the Performance of Your Band Knife Systems?
The key to maximum performance of your band knife systems lies in the perfect interaction of all components. Modern control technology plays a central role here. Unlike conventional band knives, digital control systems enable precise control of all process parameters in real-time. This continuous monitoring and adjustment ensures consistently high cutting quality whilst minimising wear.
Optimisation begins with selecting the right cutting parameters. Modern control systems have extensive databases that provide optimal settings for various materials and cutting tasks. These parameters are continuously refined through machine learning, based on actual cutting results and process data. The system learns from each cutting operation and optimises parameters independently.
Another important aspect is predictive maintenance. Through permanent monitoring of all operating parameters, potential problems can be detected early before they lead to quality losses or machine downtime. The analysis of wear patterns and operating data enables precise planning of maintenance intervals, minimising unplanned downtimes.
Our customised CNC control solutions combine state-of-the-art technologies with years of experience. Experience highest precision, reduced production costs and more efficiency with every cut. Contact us now for individual consultation and find out how ProCom can optimise your process!
What Role Does Digital Integration Play in Your Cutting Quality?
The integration of your band knife systems into a digital production environment opens up completely new possibilities for process optimisation. Through connection to modern IIoT platforms like Clouver, all process data is captured and analysed in real-time. This comprehensive data basis enables not only detailed analysis of cutting processes but also forms the foundation for continuous improvements.
Particularly valuable is the ability to analyse process data over longer periods. This allows trends and patterns to be recognised that remain hidden when viewing individual cutting operations in isolation. These insights help optimise cutting parameters, improve maintenance cycles and increase overall equipment effectiveness.
Digital integration also enables seamless networking with upstream and downstream production processes. Changes in material composition or quality requirements can automatically be translated into adjusted cutting parameters. This continuous process integration not only reduces manual effort but also minimises the risk of errors through manual intervention.
Optimise your cutting processes!
With ProCom's IIoT-capable control solutions, we intelligently network your band knife systems and increase their efficiency. Arrange a free consultation now.
How Do You Find the Optimal Band Knife Solution for Your Application?
Modern band knives are characterised by their versatility and are used in numerous industries - from the food industry to the processing of technical materials. To find the optimal solution for your application, a detailed analysis of the specific requirements is essential.
A decisive factor is the cutting material. For soft materials like food, a particularly sharp and hygienically clean cut is crucial. Stainless steel alloys and special coatings like PTFE are often used here. In textile or plastic processing, however, precision and durability play a greater role, which is why hardened band knives with abrasion-resistant coatings are preferred.
Another point is the cutting geometry. Different knife shapes are suitable depending on the application and material thickness. Straight knives are suitable for exact longitudinal cuts, while serrated knives are better suited for slippery or elastic materials.
Besides physical properties, digital integration plays an increasingly important role. Band knife systems that are compatible with IIoT technologies offer enormous advantages in process monitoring and optimisation. Real-time monitoring of relevant parameters such as cutting speed or temperature makes it possible to detect cutting errors early and increase efficiency.
Expert consultation helps you find the right combination of material, geometry and digital control. This ensures that your band knife solution meets requirements not only today but also in the long term.
How Do You Optimise Your Processes Through Intelligent Control?
The intelligent control of modern band knife systems is revolutionising industrial manufacturing processes. The integration of advanced technologies like artificial intelligence (AI) and machine learning opens up completely new possibilities for automating and optimising processes.
A central element is continuous data collection. Sensors monitor the band tension, cutting temperature and material thickness in real-time. This data is analysed to automatically adjust cutting parameters to changing conditions. This guarantees consistently high cutting quality - regardless of material variations or external influences.
Another advantage of intelligent controls is predictive maintenance. Through the analysis of wear patterns, maintenance work can be planned exactly before disruptions occur. This minimises downtime and reduces maintenance costs.
Integration into IIoT platforms like Clouver raises process optimisation to a new level. Production data can be centrally stored, analysed and used for various applications. This enables not only the optimisation of individual machines but also the improvement of entire production lines.
Through intelligent control, manual effort is significantly reduced while efficiency and precision increase. In the long term, this helps reduce production costs and secure competitive advantages.
What Must You Consider in Daily Production?
The successful use of band knives requires a well-thought-out operating and maintenance concept. Regular monitoring of machine parameters such as band tension and knife guidance is essential to ensure optimal cutting results.
Special attention should be devoted to cleaning, as contamination can impair cutting performance and shorten knife life. Use suitable cleaning agents and ensure that the machines are thoroughly cleaned after each shift.
Another important aspect is setting cutting parameters. These should be precisely adjusted to the material being used. Modern control systems facilitate this through pre-programmed parameters that can be called up at the touch of a button.
Additionally, maintenance work should be digitally documented. Accurate recording of all work performed helps optimise maintenance intervals and identify potential weak points early. The combination of regular maintenance and digital monitoring ensures smooth operation and extends equipment life.
Conclusion: How Do You Achieve Maximum Cutting Precision in Your Manufacturing?
Modern band knives are the key to precise and efficient cutting processes. Their performance is based on innovative material technology, intelligent control and digital integration. With the right CNC control solution, you can not only optimise your manufacturing but also make it future-proof.
The combination of high-quality materials, intelligent technologies and well-thought-out maintenance concepts guarantees maximum efficiency and quality. With an experienced partner like ProCom and our IIoT-capable CNC control solutions, you'll elevate your cutting processes to the next level. Start into the future of precise manufacturing now - we'll support you!
Benefit from over 40 years of expertise in CNC control solutions for band knives! Get advice from our experts now and find the optimal solution for your production.
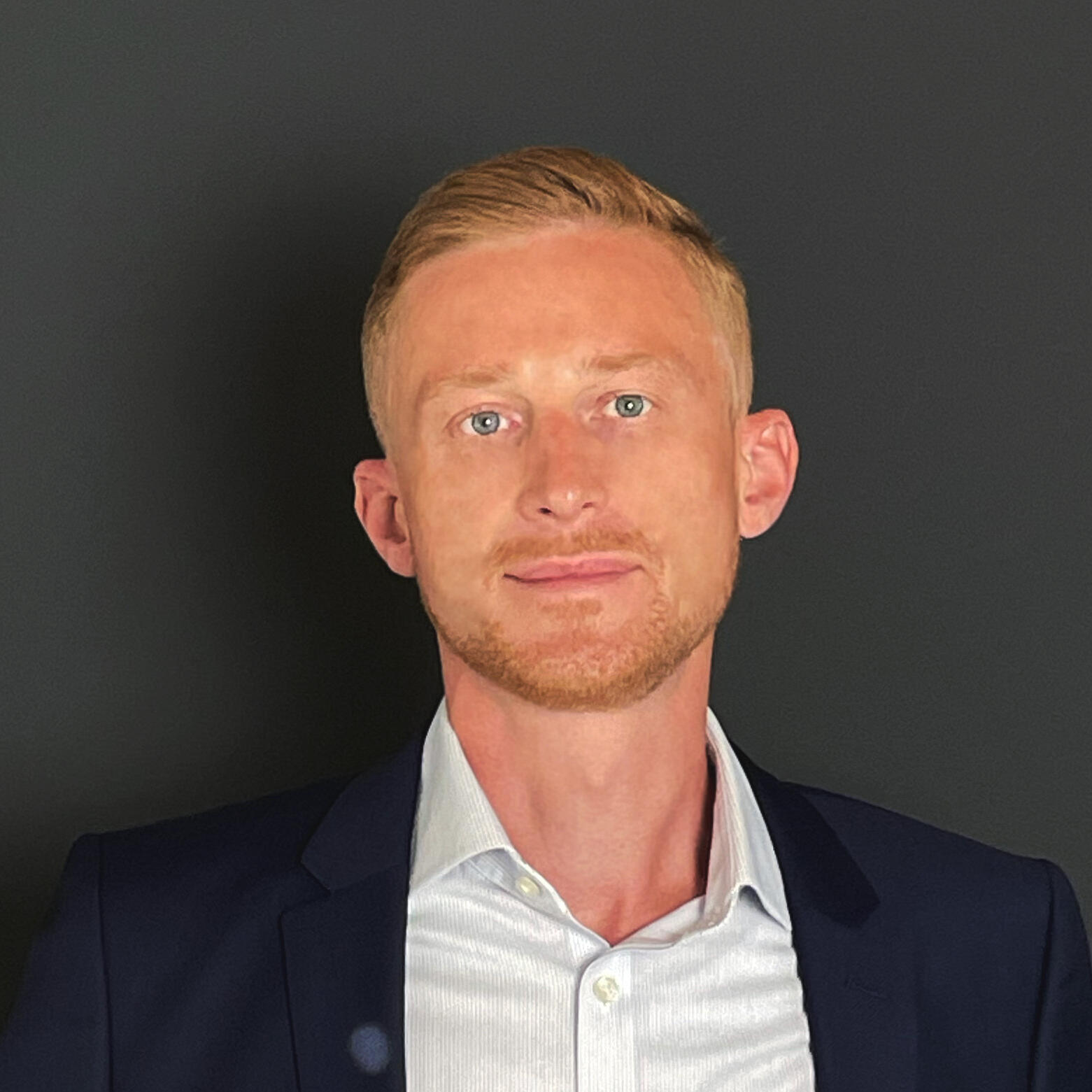
Dimitri Koneger
Sales Manager
Have questions about the topic or want to learn more about our solutions?
Contact us and discover how our products can future-proof your machines. Let’s work together to find out how we can help take your production to the next level!
- +49 241 93681-500
- contact@procom-automation.de
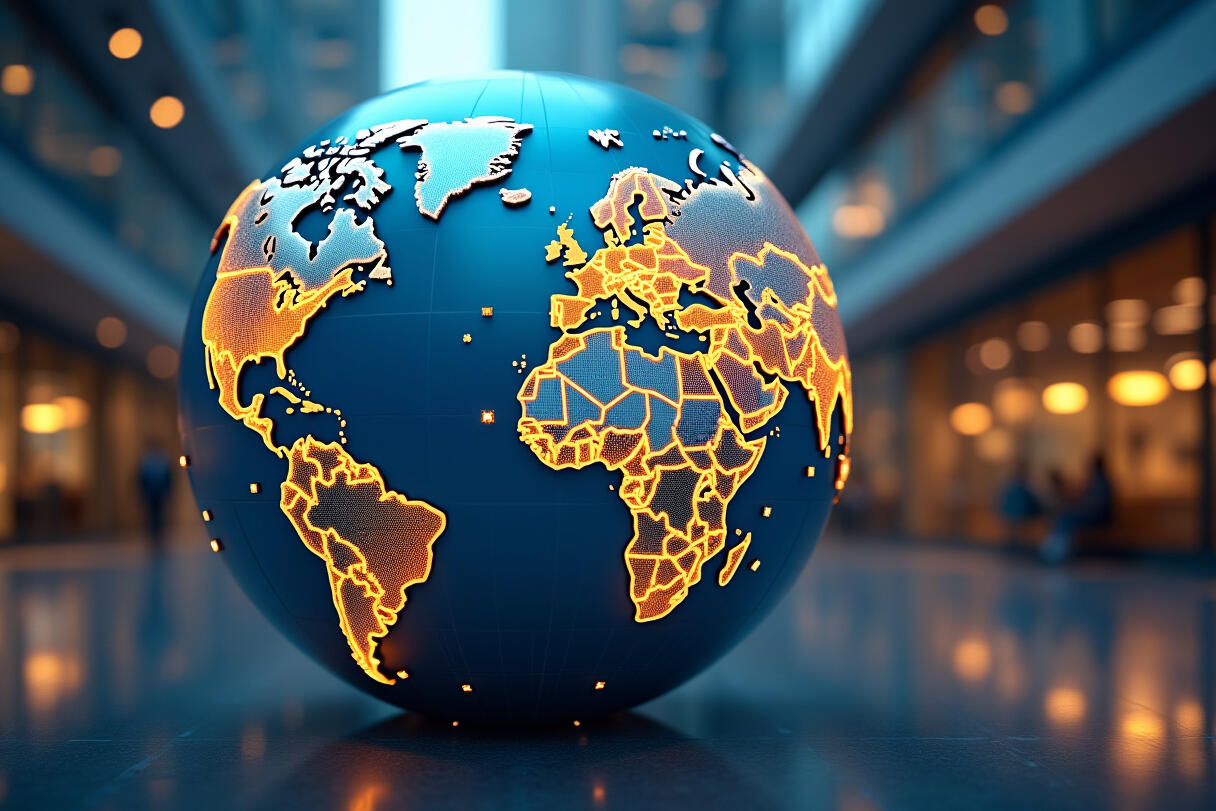
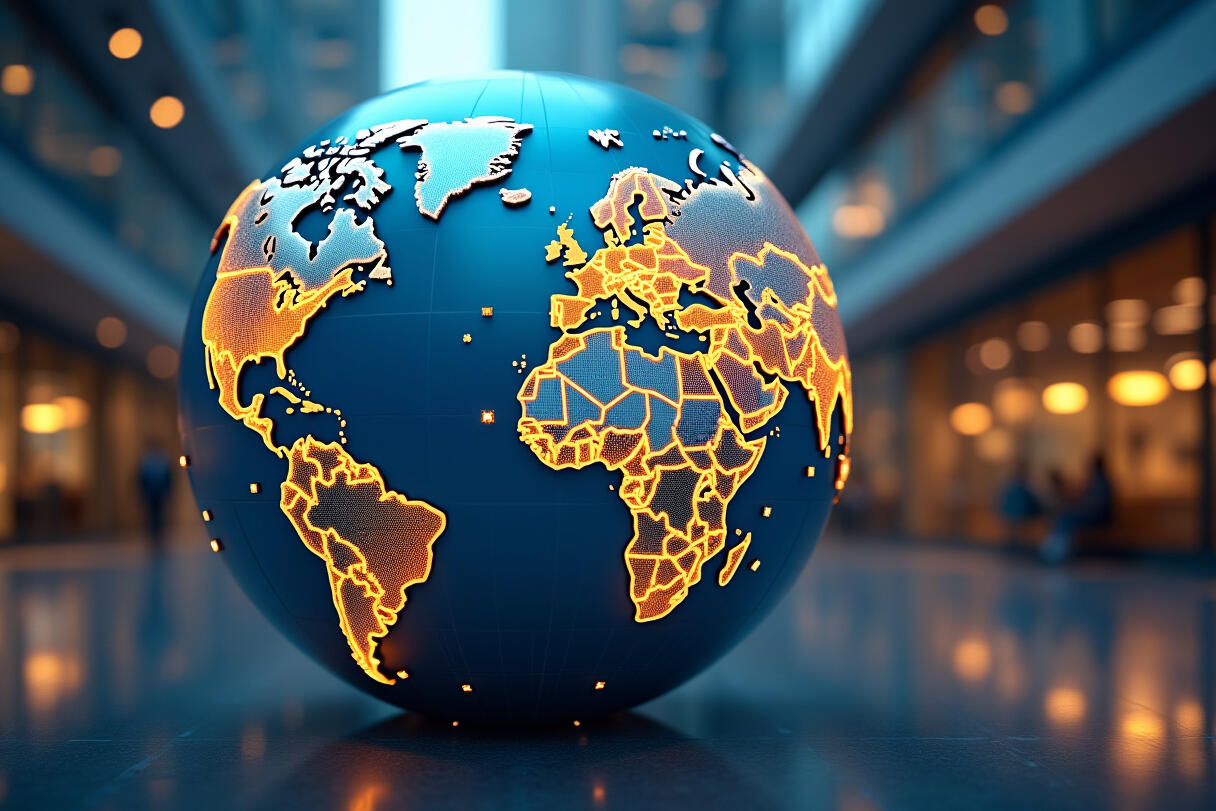