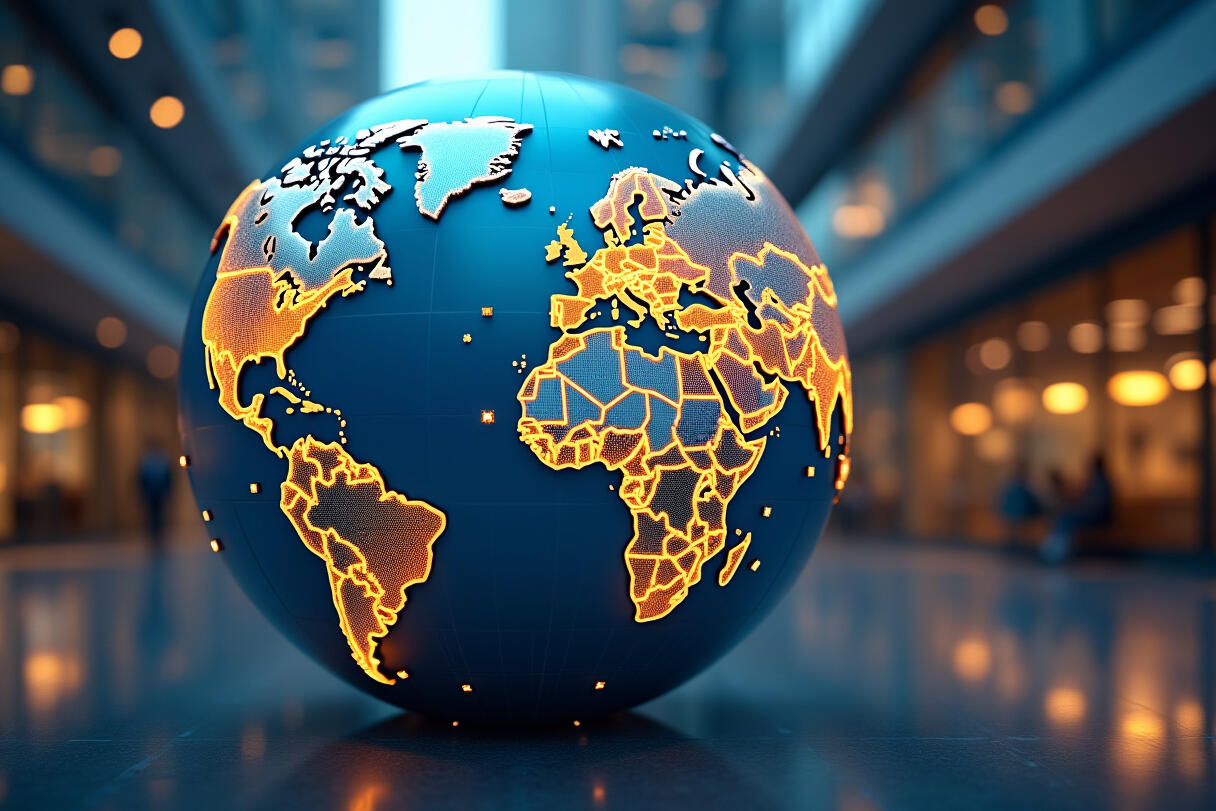
This article not only explains the technical foundations and developmental history of CNC technology but also illuminates the diverse applications and latest trends in the industry. Whether you're a beginner wanting to understand how CNC machines work, or an experienced professional looking for tips to optimise your processes – this article offers valuable insights and practical information.
Learn more about the advantages of CNC technology, how it revolutionises production processes, and which economic and forward-looking aspects you should consider.
What is a CNC Machine?
CNC stands for Computerized Numerical Control and refers to a technology where computer-controlled machines are used for precise workpiece processing. Unlike traditional machines that are operated manually, CNC machines use digital control data to automate movements and processing operations and execute them with high precision.
Basic Functionality of CNC Machines
CNC machines work based on numerical control commands in the form of G-codes. These G-codes control the movement of machine axes (X, Y, Z) and other functions such as tool changes and coolant supply. The control process begins with creating a CAD model (Computer-Aided Design), which is then imported into a CAM program (Computer-Aided Manufacturing). Here, the G-code that controls the machine is generated.
Examples of specific G-codes: G00: Rapid positioning – Moves the machine quickly to a new position without processing. G01: Linear interpolation – Executes a straight line between two points. G02: Clockwise circular interpolation – Creates a circular movement clockwise. G03: Counter-clockwise circular interpolation – Creates a circular movement counter-clockwise.
A typical programme might look like this:
G00 X0 Y0 Z0
G01 X10 Y10 Z-5 F100
G02 X20 Y20 I10 J10
G03 X30 Y30 I-10 J-10
M30
The Difference Between CNC and Traditional Machines
The main difference between CNC and traditional machines lies in automation and precision. Traditional machines require manual intervention, which can lead to higher error rates and variable quality. CNC machines, however, run fully automatically and with high repeatability. This leads to higher productivity, consistent quality, and lower error rates. The programmability of CNC machines also enables quick changeover to different manufacturing orders, significantly increasing flexibility and efficiency in production.
Technical Foundations of CNC Machines
Axis Systems: From 3-Axis to 5-Axis Machines
3-Axis CNC: Processing in X, Y and Z coordinates. These machines are suitable for simple milling and drilling work. 4-Axis CNC: In addition to the X, Y, Z axis, a rotational axis (A-axis) that enables the workpiece to be rotated and more complex geometries to be processed. 5-Axis CNC: Processing in X, Y, Z and two rotational axes (A and B). These machines offer the highest flexibility and precision and are ideal for complex processing in aerospace and medical technology.
Set New Standards in Production with ProCom! Our high-tech control solutions are specifically designed to maximise efficiency and precision in your production. With our support, you remain competitive and future-proof. Contact us now to learn more about our technologies and achieve your goals!
Modern Developments and Trends
AI and Machine Learning Integration
AI and Machine Learning are revolutionising CNC technology by optimising processes and reducing errors. These technologies enable self-learning systems that continuously improve their performance. For example, machine learning algorithms can be used to adjust cutting parameters in real-time, maximising processing efficiency and quality.
Industry 4.0 and Smart Factory
Networking and automation in Industry 4.0 lead to intelligent factories where CNC machines are seamlessly integrated into production systems and exchange data in real-time. This enables better monitoring and control of production processes, leading to higher efficiency and product quality. The use of IIoT (Industrial Internet of Things) and Big Data also enables predictive maintenance and optimisation of production processes.
Digital Twins: Simulation and Optimisation in CNC Manufacturing
Digital twins enable the simulation and optimisation of manufacturing processes in a virtual environment before they are implemented in real production. This reduces waste and increases efficiency by identifying and resolving potential problems early. Through the use of digital twins, companies can also improve the quality and consistency of their products.
Predictive Maintenance: Predictive Maintenance Systems
Predictive maintenance systems analyse machine data to predict maintenance needs and avoid unplanned downtime. This increases the uptime and reliability of CNC machines. By using sensor data and advanced analysis algorithms, companies can proactively plan maintenance measures and thus extend the life of their machines.
Secure Your Production Processes with Clouver!
Discover how our IIoT platform uncovers untapped potential and sustainably boosts your efficiency. With real-time data analysis, you can reduce errors, cut costs, and maximise productivity.
Start with a no-obligation consultation today – explore Clouver and our CNC solutions in perfect harmony!
Economic Aspects of CNC Machines
Cost-Benefit Analysis
A thorough evaluation of various CNC systems is essential. The acquisition costs should be compared with ongoing operating costs. Also consider potential savings through increased efficiency and reduced error rates.
ROI Calculation for Small and Medium-sized Enterprises
Initial costs: Calculation of acquisition costs. Consider not only the purchase price but also costs for installation, training and maintenance. Savings: Determination of savings through reduction of waste and setup times. Calculate possible savings through higher precision and efficiency of CNC machines. Amortisation: Sample calculation of amortisation period. Calculate how long it takes for the investment in a CNC machine to amortise.
Comparison: Conventional Processing vs. CNC Processing
CNC processing offers higher precision and efficiency compared to conventional processing, leading to cost savings and productivity increases. The ability to produce complex parts with high accuracy and repeatability makes CNC machines an attractive choice for many manufacturing applications.
Personnel Costs
The introduction of CNC machines requires qualified personnel, leading to training needs and corresponding personnel costs. Investments in employee education and training are necessary to fully exploit the advantages of CNC technology.
Special Applications
Additive Manufacturing: Combination of 3D Printing and CNC
The combination of 3D printing and CNC enables the production of complex components with high precision and reduced material usage. Through the use of CNC machines, printed parts can be post-processed and refined to achieve the final shape and surface quality.
Woodworking: CNC in Wood Crafts
CNC machines are used in woodworking to produce precise and complex wood products. They enable wood processing with high accuracy and repeatability, which is particularly advantageous in the production of furniture and decorative elements.
Plastic Processing: Applications and Advantages
In plastic processing, CNC machines offer high flexibility and precision when processing various plastics. They enable the production of complex shapes and structures that would be difficult to achieve in traditional processing.
Special Applications: Medical Technology, Aerospace
CNC machines are used in medical technology and aerospace where highest precision and reliability are required. They are used to manufacture medical implants, surgical instruments and components for aircraft and spacecraft.
Future Perspectives of CNC Technology
Technological Developments: New Materials and Processing Methods
The development of new materials and processing methods expands the application possibilities of CNC machines. For example, high-strength alloys and composite materials enable the production of lightweight yet robust components.
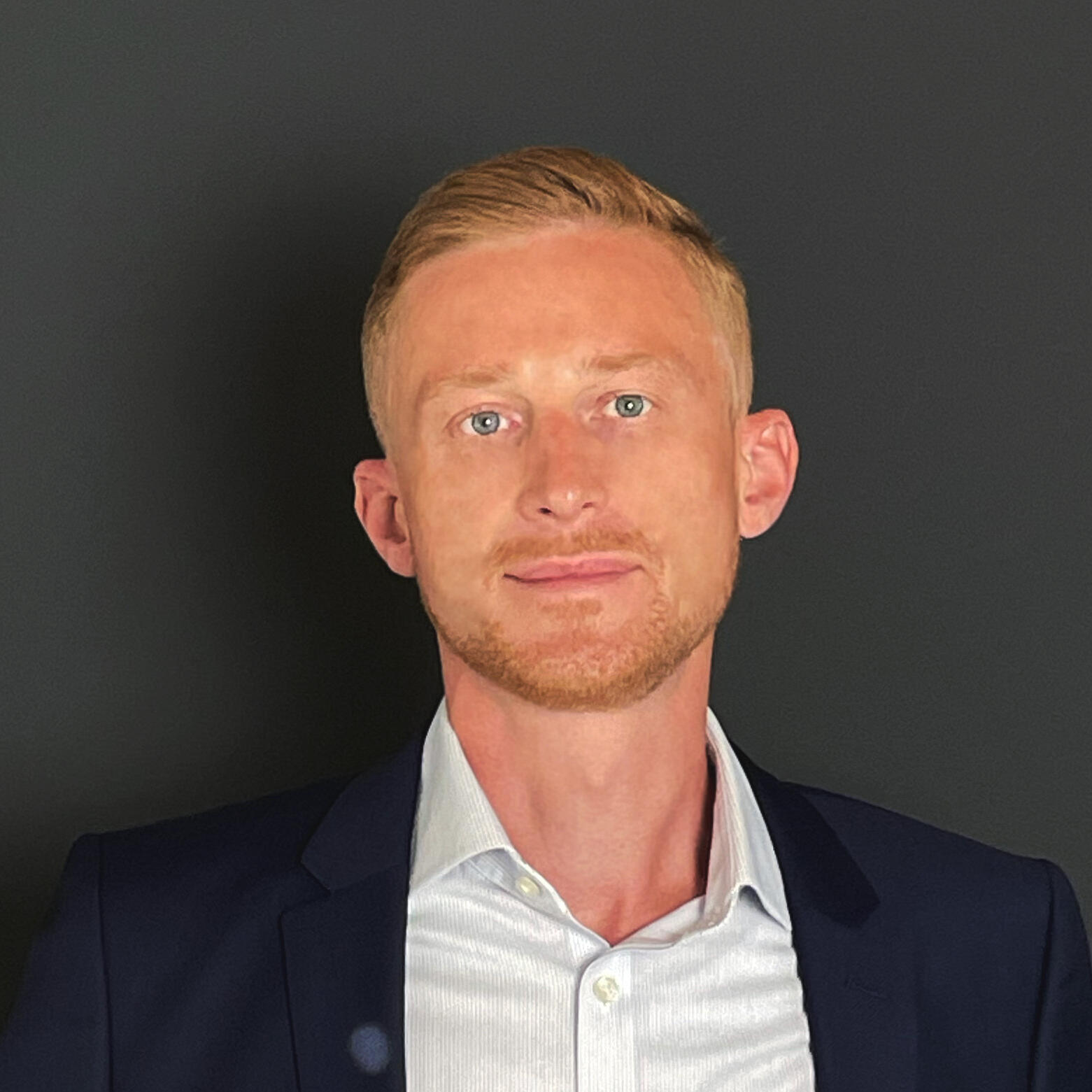
Dimitri Koneger
Sales Manager
Have questions about the topic or want to learn more about our solutions?
Contact us and discover how our products can future-proof your machines. Let’s work together to find out how we can help take your production to the next level!
- +49 241 93681-500
- contact@procom-automation.de
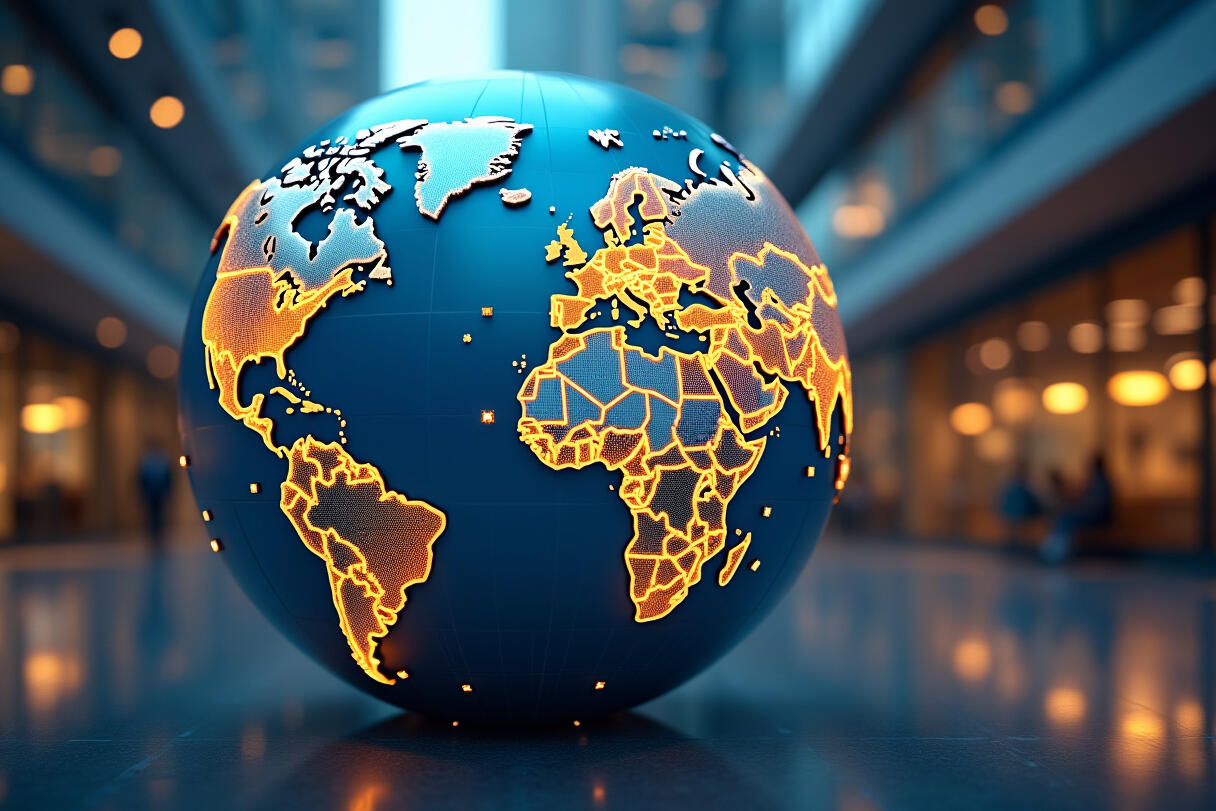
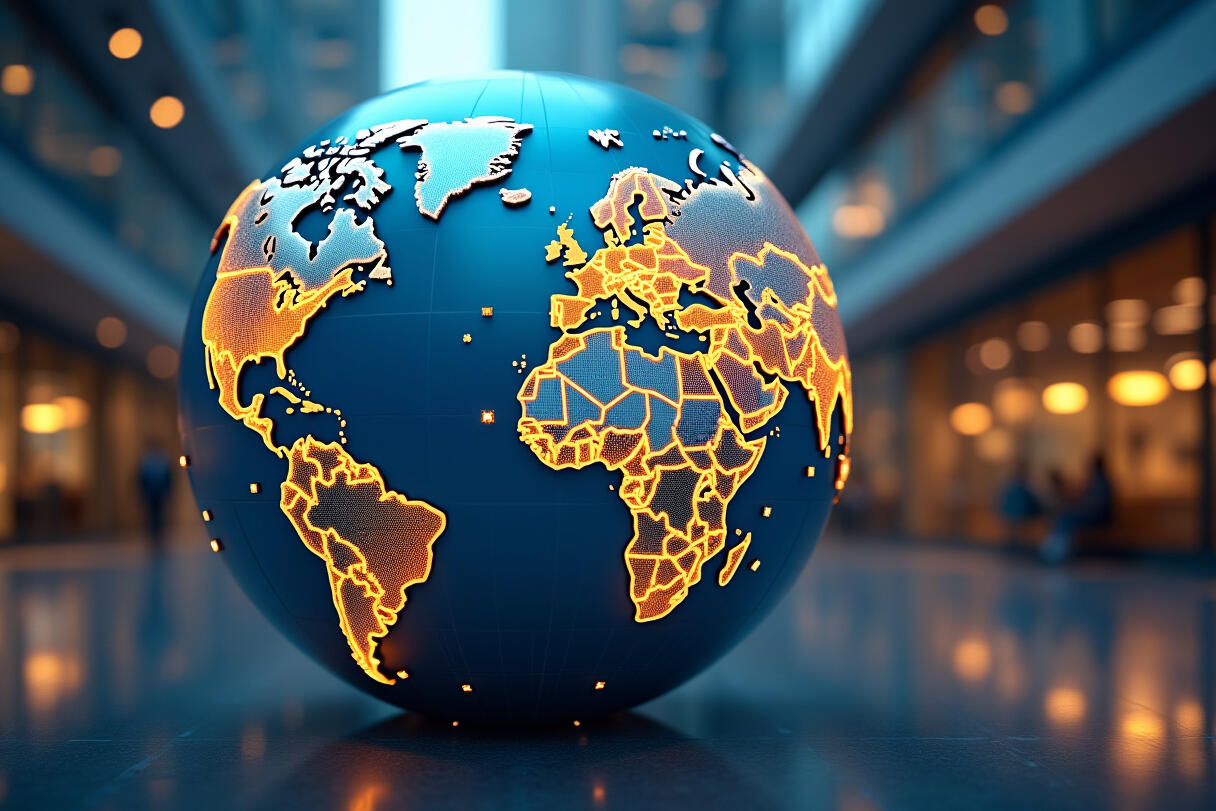