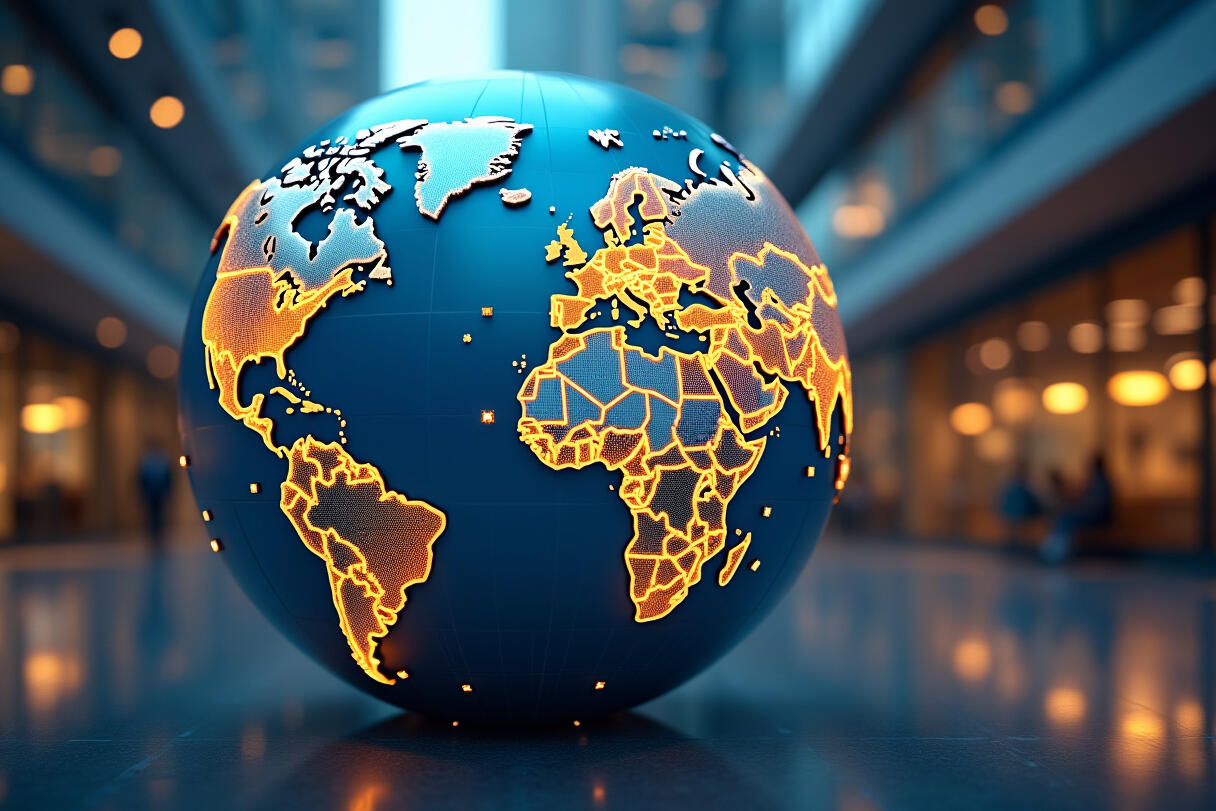

The cutting of fabrics is a crucial step in textile production, encompassing the precise separation of material according to predetermined patterns and shapes. We distinguish between manual methods, such as scissors and rotary cutters, and mechanical methods like laser cutters. Manual methods are easily accessible and cost-effective but require skill and care to ensure consistent quality. Mechanical methods, particularly laser cutting, offer significant advantages in terms of precision and efficiency. Laser cutting machines work without contact, thereby avoiding fraying and rough edges, which is particularly advantageous for delicate fabrics such as silk or lace. The use of software enables consistent and repeatable results, ideal for complicated designs.
Advantages of Laser Cutting
Key Advantages of Laser Cutting Machines
Laser cutting machines offer numerous advantages that make them a preferred choice for many applications. They enable precise and clean cuts through contactless operation, avoiding fraying and rough edges - particularly important for delicate fabrics. The software-controlled consistency through CAD integration ensures high accuracy and repeatability for complicated designs. Another significant advantage is the acceleration of production, as laser cutters can work quickly and efficiently, particularly when cutting multiple layers of fabric simultaneously. Their versatility is demonstrated in their ability to cut and engrave various materials.
Materials
Materials That Can Be Cut with Laser Cutters
In the field of laser cutting technology, various materials can be processed. These include denim, a robust fabric in the fashion industry, linen with its natural breathability and durability, and felt for craft and home textiles. Also suitable are satin for elegant garments, fine silk for luxury fashion, versatile polyester, and widely-used cotton. Fleece, known for its insulating properties, rounds out the spectrum of cuttable materials.
Materials Well-Suited for Laser Engraving
For laser engraving, materials with special structural properties are particularly suitable. Denim provides an excellent surface for detailed engravings, whilst canvas stands out for its durability. Suede and velvet enable particularly impressive engravings due to their soft and luxurious characteristics, respectively. Pure cotton and felt also provide ideal conditions for high-quality engraving results.
Technical Details and Laser Types
Best Laser Types for Fabric Cutting
CO2 lasers have established themselves as the optimal choice for cutting and engraving fabrics. They impress with high performance and precision when processing both natural and synthetic fabrics. Diode lasers represent a more cost-effective alternative, particularly suitable for DIY projects and smaller applications.
Advanced Technical Details
The technical aspects include various cutting speeds depending on the type of fabric, with cotton being cut at approximately 50 mm/sec and leather at about 30 mm/sec. The maximum material thicknesses are up to 20 mm for laser cutters and up to 10 mm for knives. Regular maintenance, including inspections and calibrations, is essential for optimal performance.
Benefit from over 40 years of expertise in control solutions for textile cutting!
Get in touch with our experts today and discover the perfect solution for your production needs.
Practical Tips and Safety Considerations
Important Tips for Laser Cutting
Before beginning cutting, it is essential to determine the optimal settings through tests on fabric remnants. Correct setup of the cutting table and proper height adjustment of the laser beam are fundamental. Safety aspects such as wearing protective goggles and gloves, and avoiding easily flammable materials in the work area, are essential.
Troubleshooting Guide
For unclean cuts, checking the blades or laser focus and adjusting cutting parameters is recommended. Material distortion can be minimised through secure fixation and optimised cutting parameters.
Economic Aspects
For the economic analysis of different cutting methods, a comprehensive cost comparison between laser, knife, and water jet cutting is necessary. This must consider acquisition costs, operating costs, and maintenance. For commercial users, a detailed ROI analysis is essential, incorporating initial investment costs, ongoing operating costs, and productivity improvements.
Industry-Specific Applications
The applications of laser cutting are diverse. In the fashion industry, it enables precise cutting of delicate fabrics such as silk or lace. The automotive industry uses the technology for robust materials like leather in seat covers. In home textiles, it is used for manufacturing curtains, bedding, and cushion covers. Technical textiles for medicine through to aerospace, as well as arts and crafts, also benefit from this technology.
Special Applications
In multilayer cutting, multiple layers of fabric are processed simultaneously, increasing efficiency and reducing production times. Pattern matching enables precise designs with seamless transitions.
Quality and Sustainability
Quality Standards
Compliance with ISO standards such as ISO 9001 for quality management systems guarantees the highest production standards. Systematic error analysis for identifying and resolving common cutting errors is essential for high-quality end products.
Environmental Aspects
A comparison of the environmental friendliness of different cutting methods shows that laser cutting has a higher energy consumption than mechanical methods. Sustainability is promoted through efficient recycling of fabric remnants.
Innovation and Digitalisation
Software and Automation
The integration of CAD/CAM software optimises the cutting process in terms of efficiency and precision. Automation possibilities increase productivity and reduce errors.
Future Trends
Development includes AI-supported cutting systems, IoT integration for improved monitoring, robot-supported systems for process automation, and hybrid technologies for greater flexibility. The networking of systems, predictive maintenance through data analysis, and cloud-based solutions characterise the modern production landscape.
Practice-Relevant Decision Aids
Selection Criteria
Decision aids for various systems are based on application requirements, budget, and production volume. Checklists for procurement, ROI calculators, and comparison tables support the selection process.
Best Practices and Safety
Material preparation, process optimisation, and regular maintenance are crucial for optimal results. Advanced safety guidelines, personal protective equipment, and thoughtful workplace design ensure safe operation.
Conclusion
Laser cutting has established itself as a forward-looking technology in fabric processing. The combination of precision, efficiency, and versatility makes it a valuable investment for various applications. With advancing digitalisation and focus on sustainability, its importance will continue to increase. Crucial for successful implementation are both technical understanding and consideration of economic and practical aspects. Through proper implementation and consistent quality assurance, companies can benefit from the diverse advantages of this innovative cutting technology. Please feel free to contact us with any questions!
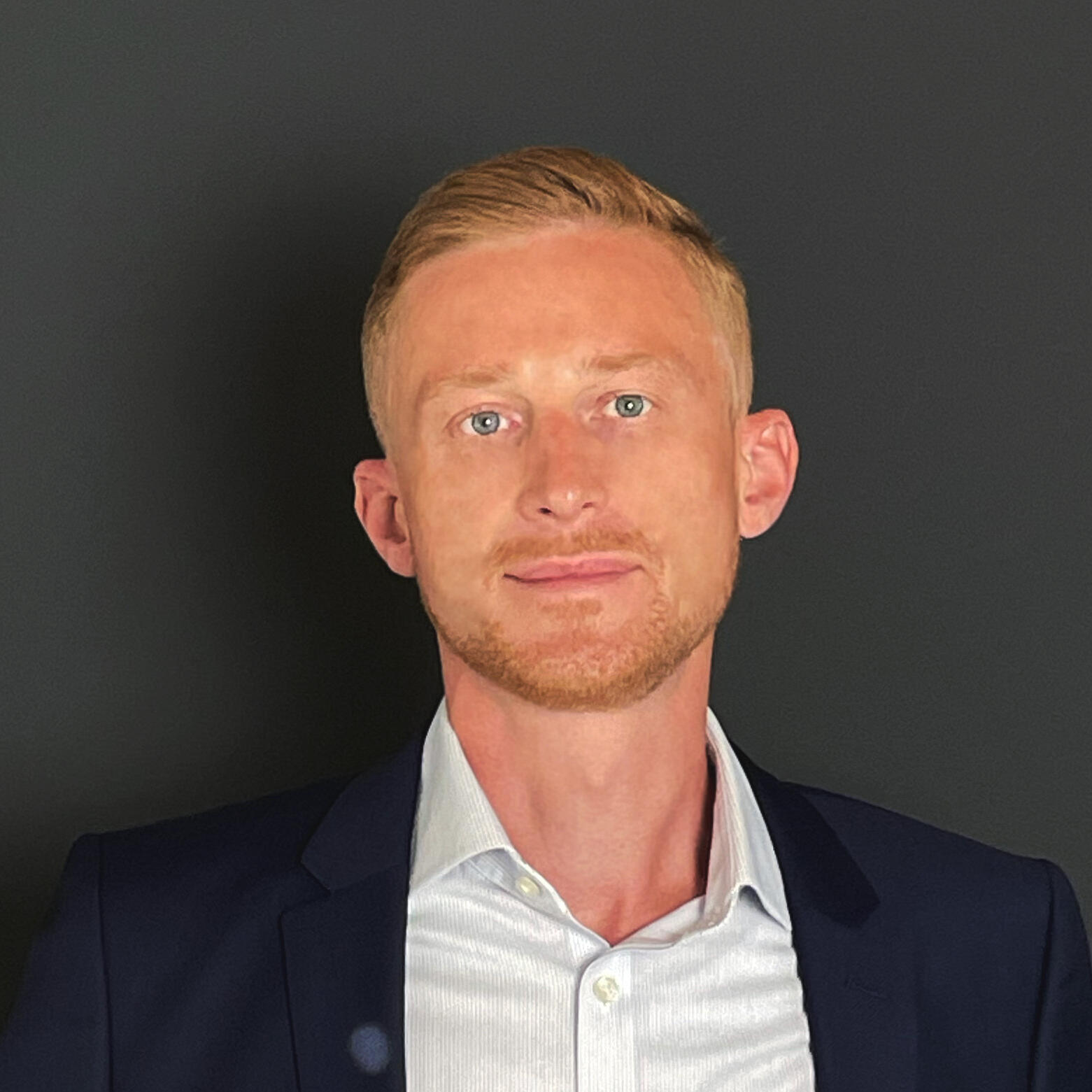
Dimitri Koneger
Sales Manager
Have questions about the topic or want to learn more about our solutions?
Contact us and discover how our products can future-proof your machines. Let’s work together to find out how we can help take your production to the next level!
- +49 241 93681-500
- contact@procom-automation.de
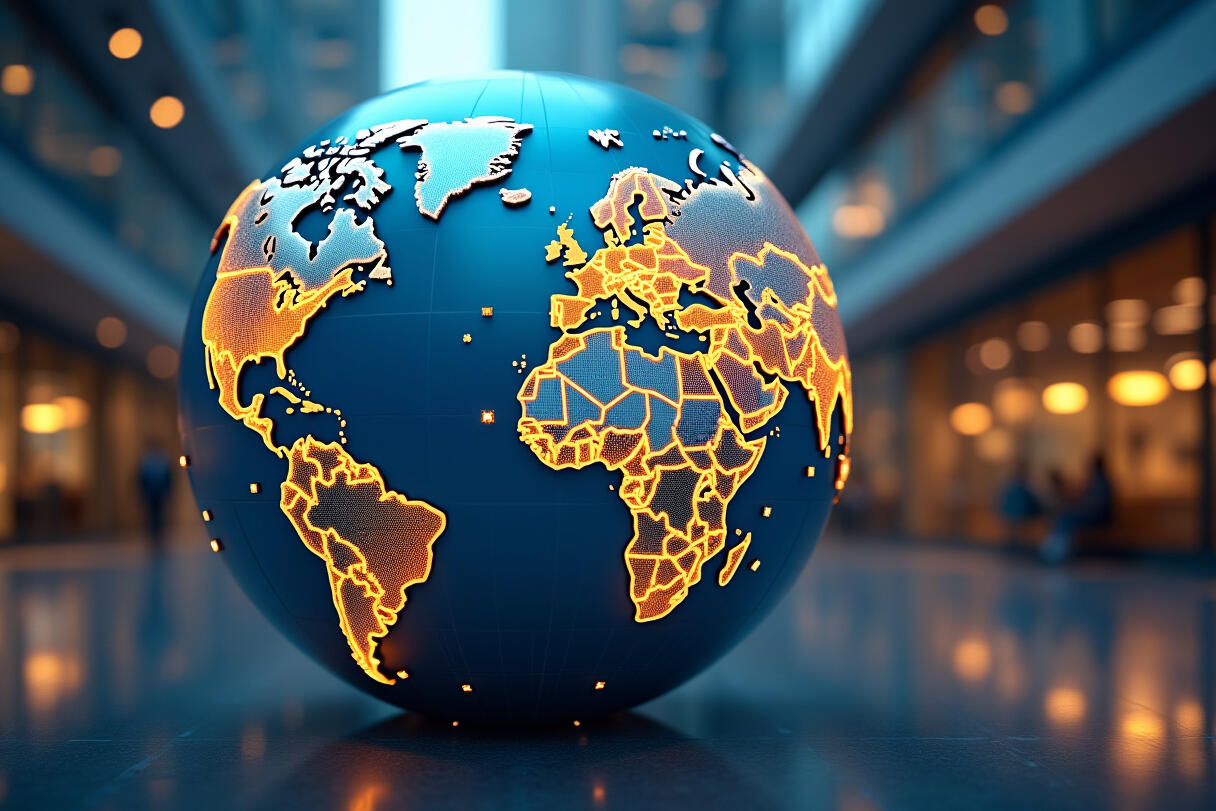
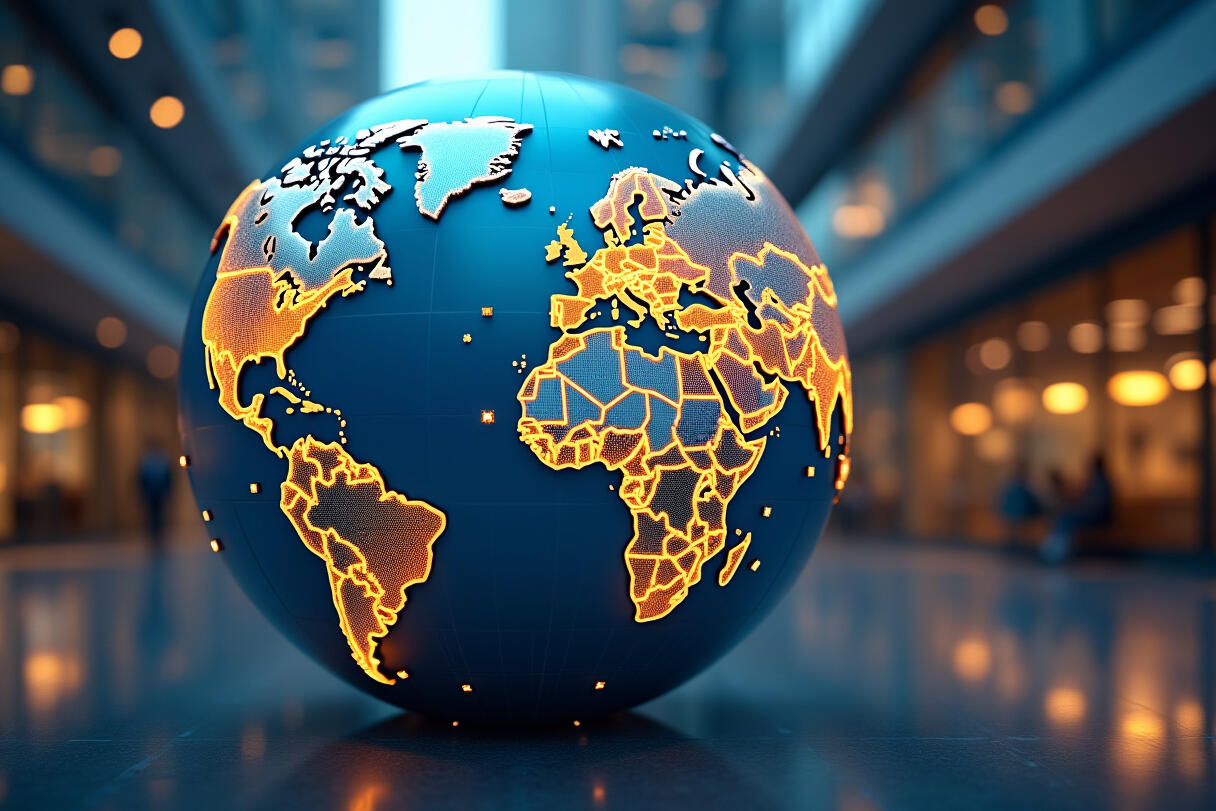