Imagine being able to see how efficiently your production is actually running at any time and from anywhere. Recognising potential problems before they lead to costly downtime. Making decisions based not on gut feeling, but on precise real-time data.
The Industrial Internet of Things (IIoT) makes exactly this possible – it is a key element of Industry 4.0 and revolutionises how modern manufacturing companies operate. But how do you sensibly integrate this transformative technology, especially into an existing, often heterogeneous machine park?
In this comprehensive article, you will learn how IIoT production monitoring works, what potential it holds for your digital factory, how you can seamlessly integrate older equipment, and how you can not only optimise your processes with an intelligent solution like the Clouver platform from ProCom Automation, but also sustainably save costs and secure your competitiveness.
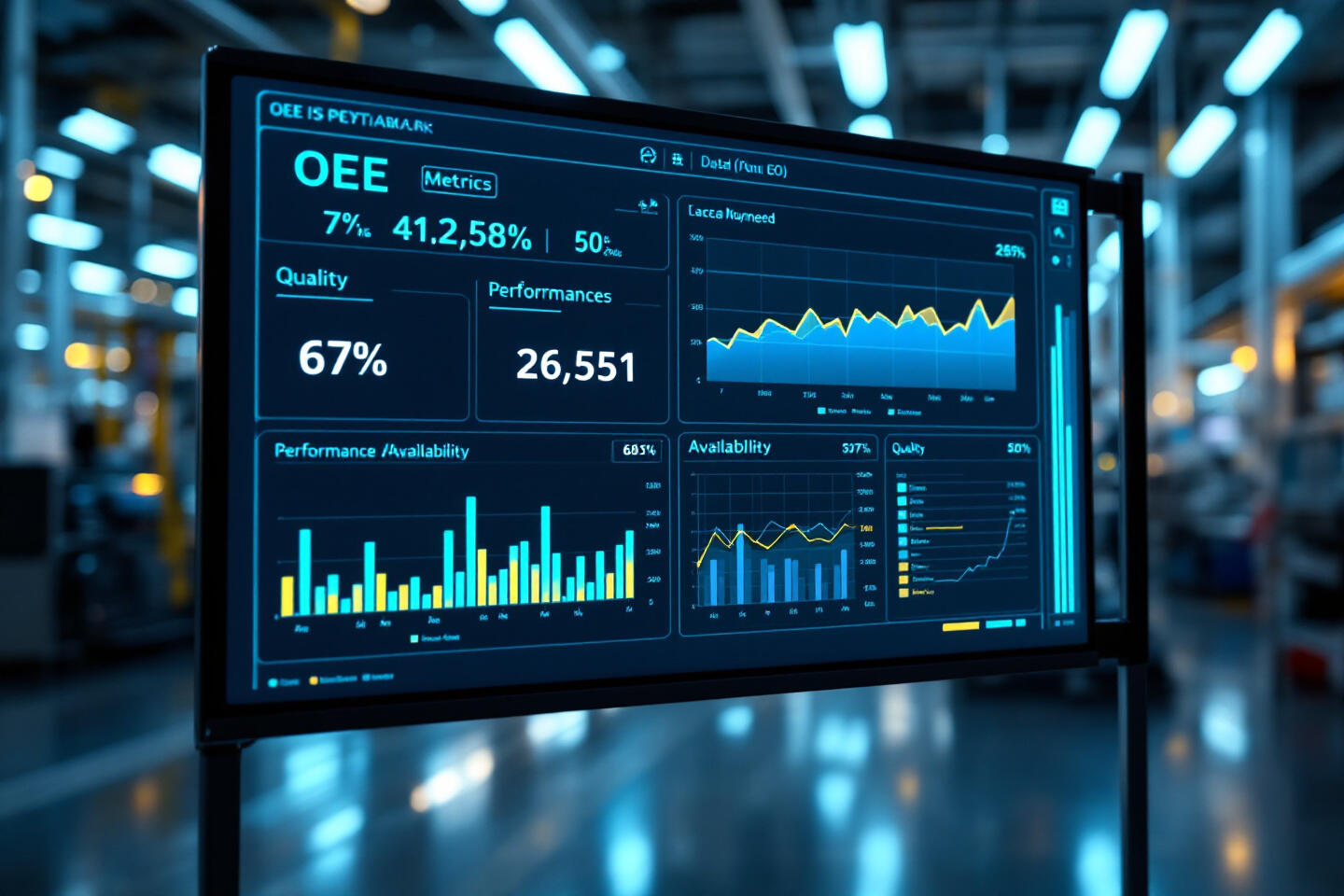
IIoT Production Monitoring: Fundamentals and Potential for Modern Manufacturing
The success of your production depends significantly on the transparency and efficiency of your processes. The Industrial Internet of Things (IIoT) provides the technological basis to elevate this transparency to a new level. IIoT production monitoring describes the systematic collection, transmission, processing and visualisation of production data – ideally in real time across the entire machine park, regardless of manufacturer or age of the equipment.
A modern IIoT production monitoring system, like Clouver from ProCom Automation, consists of several central components that work together seamlessly:
- Sensor network: A variety of sensors continuously records operational data (runtime, downtime, cycle time), process parameters (temperature, pressure, speed) and environmental conditions.
- Connectivity: Secure and stable connections (wired or wireless) between machines, sensors and the central IIoT platform.
- Data processing (Edge & Cloud): Raw data is often pre-processed at the machine (Edge Computing) and then centrally analysed and stored in the cloud or on-premises.
- Visualisation: User-friendly dashboards present the current production status, KPIs and trends clearly and comprehensibly.
Analysis tools: Intelligent algorithms identify patterns, deviations and trends, thus revealing optimisation potential.
These building blocks create a seamless digital twin of your manufacturing processes. They form the basis for data-driven decisions – without lengthy manual evaluations. The potential that results from this goes far beyond mere monitoring:
- Predictive Maintenance: Analyse sensor data (e.g. vibration, temperature increase) to predict machine failures and plan maintenance proactively rather than reactively.
- Process optimisation: Use real-time data to not only identify bottlenecks, but also specifically optimise process parameters such as cutting speeds, cycle times or energy use.
- Resource efficiency: Monitor the consumption of energy, compressed air or materials and identify savings potential. Optimise tool life through precise usage data.
Automated quality assurance: Capture quality data inline during the process to detect rejects early, find causes more quickly and initiate countermeasures.
Real-Time Data Collection: How IIoT Sensors Revolutionise Your Production Transparency
Are you wondering how you can precisely and immediately capture the actual state of your diverse production facilities? The answer lies in intelligent networking through the Industrial Internet of Things. Modern IIoT sensors provide precise measurements instead of rough estimates and allow you to react immediately to deviations or critical conditions.
Continuous, automated data collection is the foundation of any improvement. Important parameters such as machine availability (Running/Stopped/Fault), production performance (quantities, cycle times), product quality, energy consumption or material flow are monitored continuously. This includes sensors for vibration, temperature, pressure, current consumption, but also simple signal taps from controls or light barriers for counting pieces.
Clouver's dashboards not only visualise this flood of information as an overall view. They also allow drill-downs to quickly identify the causes of sudden machine stoppages, creeping performance drops or deviations in production cycles.
Through this real-time data, you always have the necessary transparency to react early to disruptions and address optimisation needs proactively. The result? More stable processes, higher Overall Equipment Effectiveness (OEE) and ultimately significantly lower operating costs.
Integrating Existing Machines into IIoT Monitoring Systems: The Bridge to the Smart Factory
One of the biggest hurdles on the way to the Smart Factory is often the heterogeneous machine park: modern equipment with open interfaces alongside proven but older machines without native network connectivity (brownfield). How do you integrate all these assets into a unified IIoT monitoring system? This is exactly where flexible solutions like Clouver show their strength.
With specialised hardware modules like the Clouver SmartKit, it is possible to cost-effectively integrate older or "dumb" machines into your IIoT ecosystem. The common integration approaches are:
- Direct connection: Modern machines (e.g. with Siemens S7, Beckhoff, OPC UA) are connected directly via their interfaces.
- Retrofit solutions (Clouver SmartKit): Older equipment is retrofitted with the SmartKit. This taps signals (e.g. from indicator lights, control cabinets) or uses simple additional sensors and acts as an edge device.
- Sensor-based recording: Additional sensors (vibration, current, etc.) are installed on critical components to capture their condition independently of the machine control.
- Edge Computing: The Clouver SmartKit as an edge device processes data directly at the machine. Benefits include reducing network load, faster local reactions and buffering data during network interruptions.
This variety of integration options allows you to include almost any asset in your IIoT production monitoring – regardless of age or manufacturer. This gives you a holistic view of your value chain without costly complete replacement actions.
Forward-thinking Technologies for Your Manufacturing!
With ProCom's high-tech solutions, you can digitalise work processes, minimise downtime and make your production smarter. Contact us now for a no-obligation consultation!
KPI-Based Decision Making Through Intelligent IIoT Production Monitoring
The true strength of IIoT production monitoring unfolds when data becomes knowledge and knowledge becomes well-founded decisions. By defining, continuously monitoring and analysing relevant Key Performance Indicators (KPIs), you can objectively identify production bottlenecks, uncover the true causes of quality problems, optimise maintenance intervals and specifically improve processes.
In an intelligent system like Clouver, you have the flexibility to customise your dashboards. Track exactly the KPIs that are most relevant to your specific production process and business goals. Typical examples are:
- Overall Equipment Effectiveness (OEE): The gold standard for measuring true equipment productivity.
- Machine availability & downtime analysis: Detailed recording and categorisation of downtime and reasons for downtime.
- Performance rate: Cycle times, output quantities, deviations from target speed.
- Quality rate: Good part count, scrap rate, rework rate, First Pass Yield (FPY).
- Energy consumption per piece or per hour: Identification of energy wasters.
- Tool life & changes: Optimisation of tool usage and setup times.
By analysing these KPIs over time, comparing between machines or shifts, targeted measures can be initiated – from adjusting maintenance plans to technical process optimisations and removing bottlenecks to targeted training for employees. Clouver provides the facts so you can find the right levers.
ROI Maximisation: Cost Reduction and Efficiency Increase Through IIoT Monitoring Solutions
The introduction of an IIoT production monitoring system is an investment – but one that quickly pays off. With a well-thought-out solution like Clouver from ProCom Automation, you achieve measurable results that translate into a significantly improved Return on Investment (ROI).
The most important levers for cost reduction and efficiency increases are:
- Reduction of unplanned downtime: Early warning systems and precise diagnoses minimise expensive stoppages. A reduction of just 20% can often mean annual savings in the five to six-figure range.
- Optimised maintenance (Predictive Maintenance): Switch from rigid, often unnecessary preventive maintenance to condition-based maintenance. Save massively on spare parts, personnel costs and avoid unplanned failures.
- Energy savings: Identify unnecessary energy consumption during standby times or through inefficient processes. Savings of 10-15% of energy costs are realistic.
- Reduction of scrap & rework: Faster reaction to quality problems and process optimisations often reduce material waste and expensive rework by 15-30%.
- Increased output: Through less downtime, optimised cycle times and more stable processes, you produce more in the same time.
A practical example: A medium-sized manufacturing company in the metal processing sector implemented Clouver to monitor its heterogeneous machine park (CNC machines, presses, welding robots). Within 12 months, the company was able to reduce unplanned downtime by 27% and increase Overall Equipment Effectiveness (OEE) from an average of 61% to 78%. The savings achieved (less downtime, lower maintenance costs, less scrap) exceeded the investment costs for Clouver after just nine months.
This underlines: IIoT production monitoring is not just a technology gimmick, but a strategic decision with clear economic benefits. Thanks to Clouver's modular structure, you can also start step by step and specifically invest in the areas that promise the greatest and fastest ROI for your company.
Would you like to estimate your individual ROI through the use of Clouver?
Speak with our IIoT experts and receive a tailored potential analysis for your production! Request your free consultation now!
Conclusion: Towards Efficient and Future-Proof Production with IIoT Monitoring
The Industrial Internet of Things is transforming the manufacturing industry. IIoT production monitoring is a central component that opens up entirely new possibilities for increasing efficiency, reducing costs and optimising processes.
The intelligent use of real-time sensor data, flexibly visualised via customised dashboards, enables you to make decisions on a solid, objective data basis. From seamless monitoring of your entire machine park – including the seamless integration of older equipment – to the derivation of concrete improvement measures, this technology offers the decisive competitive advantage in an increasingly digitalised world.
ProCom Automation is your experienced partner on the way to the Smart Factory. With our customised IIoT platform Clouver and our expertise in industrial automation, we ensure that your individual requirements are at the centre and that you fully exploit the potential of IIoT.
Make your production more transparent, efficient and profitable!
Ready for the next step?
Discover in detail how Clouver solves your specific challenges. Request a no-obligation live demo now. Together we'll shape your production of the future!