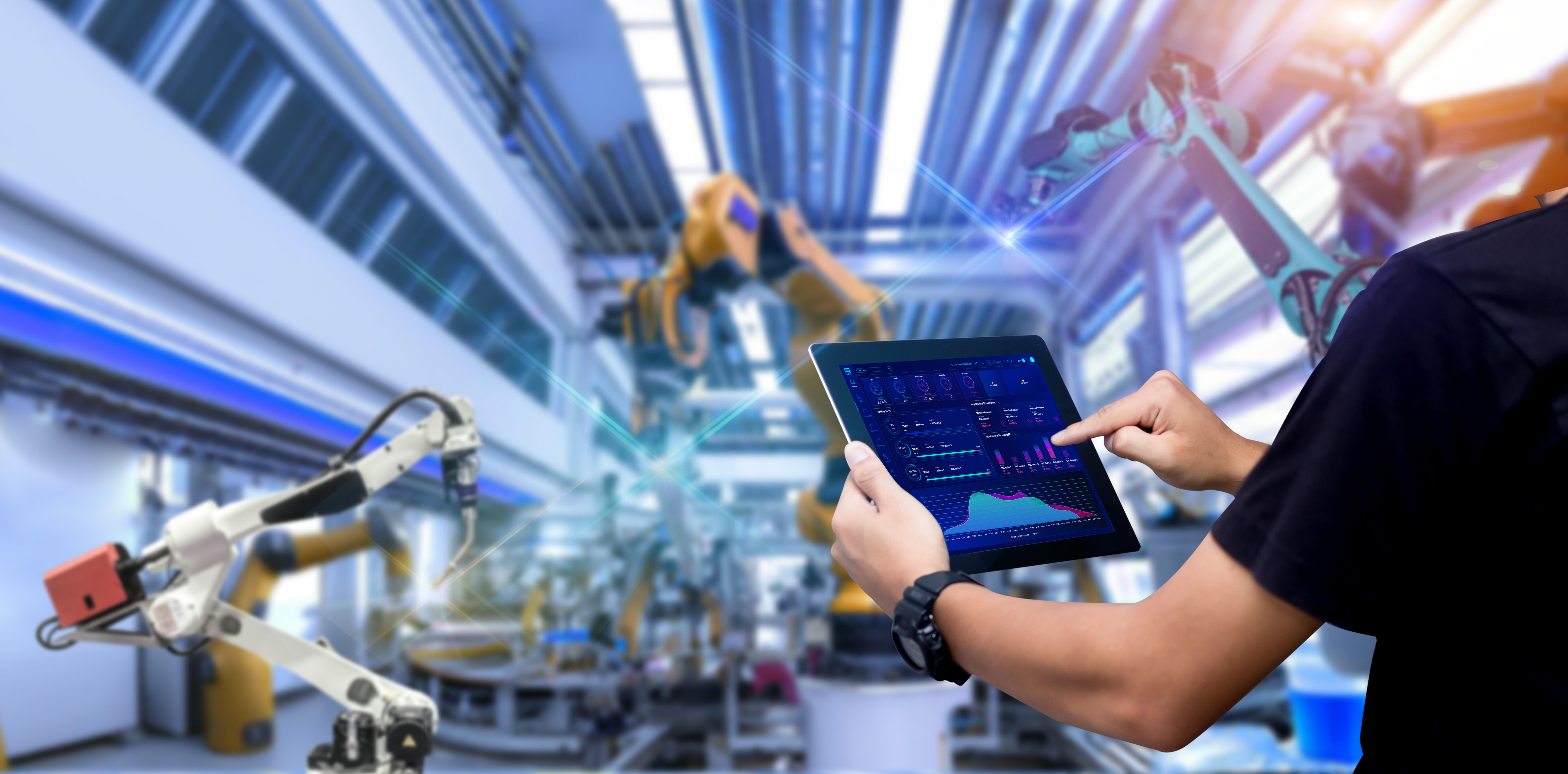
Imagine being able to network your production so that machines not only communicate with each other but also make independent decisions – that's the core of Industry 4.0. Many companies wonder: What really lies behind this term and how can you implement this digital transformation in your own business? In this article, you'll receive a clear, practical definition of Industry 4.0. You'll learn why it's relevant for your company and what concrete steps are necessary to make your production future-proof. Be inspired by how you can increase the efficiency of your manufacturing using modern IIoT solutions like Clouver.
1. Definition of Industry 4.0: Origin and Core Principles
Industry 4.0 refers to the fourth industrial revolution, which was launched in 2011 as a strategic initiative to strengthen the German economy. Unlike previous revolutions – characterised by mechanical production with water and steam power (1.0), mass production with electrical energy (2.0), and electronic automation (3.0) – Industry 4.0 is distinguished by the intelligent networking of the entire industrial value chain.
At its core, we understand it to encompass technologies and concepts where Cyber-Physical Systems (CPS) monitor physical processes, create a digital copy of the real world, and make autonomous, decentralised decisions. These systems communicate with each other and with humans in real time via the Industrial Internet of Things (IIoT).
The central principles that form the foundation of Industry 4.0 are:
- Service-oriented architecture: Modular systems for flexible adaptations of your production environment
- Self-organising systems: The connection of the physical and digital world with autonomous decisions
- Interoperability: Seamless communication between systems and human-machine interaction
- Flexibility: Production systems that quickly respond to changing market requirements
- Optimisation of overall effectiveness: Continuous improvement of all processes
- End-to-end data integration: Collection and use of data throughout the entire lifecycle
- Cybersecurity: Protection against unauthorised access in networked systems
Get the Best Out of Your Production with Clouver!
Connect your machines and gain valuable insights into your production processes. Reduce unused capacity, optimise resource utilisation, and increase your revenue. Contact us today for a no-obligation consultation!
2. Technological Foundations: CPS and IIoT
The technological basis of Industry 4.0 rests on two central concepts: Cyber-Physical Systems (CPS) and the Industrial Internet of Things (IIoT).
CPS are the bridge between the physical and digital worlds. They integrate information and communication technologies directly into physical processes. Sensors collect data from your production environment and process it in real time – often coupled with actuators that respond immediately to physical events.
The IIoT forms the connecting layer and enables the networking of sensors, actuators, and machines via standardised communication interfaces. Through this end-to-end data integration, not only can processes be monitored in real time, but hidden potentials for efficiency improvements can also be uncovered.
Clouver from ProCom Automation impressively demonstrates how CPS and IIoT work together. The platform offers you:
- Real-time data access via clear dashboards
- Modular structure for flexible adaptation to specific requirements
- Integration of existing machines with the Clouver SmartKit
This way, your production grows gradually and cost-efficiently towards fully networked manufacturing.
3. The Role of Real-Time Data in Networked Production
In modern Industry 4.0, real-time data dominates the competition. Potential losses often occur within very short timeframes if relevant information is processed with delay. IIoT platforms like Clouver transform the continuous data stream from your machines into immediately usable insights.
Why are real-time data so crucial?
- Immediate responsiveness: You can act instantly when performance losses occur
- Context-based analysis: The causes of efficiency losses become clearly visible
- OEE optimisation: Overall equipment effectiveness can only be increased through permanent monitoring
Collecting data via sensors or directly through your machines' PLC enables seamless monitoring. Modern dashboards visualise this data clearly, so you maintain an overview at all times.
Clouver relies on a modular structure with real-time data visualisation and analysis tools. Push notifications and customised dashboards help you intervene quickly when deviations occur and avoid production losses.
4. Efficiency Increases Through Smart Production Monitoring
Smart production monitoring is a central component of Industry 4.0. The focus is on the Overall Equipment Effectiveness (OEE) metric, which summarises the availability, performance, and quality of your equipment in a single value.
The advantages of these monitoring systems:
- Continuous transparency: Real-time dashboards give you insight into performance at any time
- Data-based decisions: Everyone works on the basis of the same precise data
- Targeted loss reduction: Specific measures make your production more efficient
- Integration of heterogeneous machines: Incorporation of new and older equipment into a unified system
Another plus point is paperless order processing, which conserves resources and shortens reaction time in case of disruptions. With Clouver, you receive a system with modular hardware and software components that can be quickly tailored to your individual needs.
Get the Best Out of Your Production with Clouver!
Connect your machines and gain valuable insights into your production processes. Reduce unused capacity, optimise resource utilisation, and increase your revenue. Contact us today for a no-obligation consultation!
5. Integration of Existing Machines into the Industry 4.0 Ecosystem
One of the biggest challenges is integrating existing machines into your Industry 4.0 ecosystem. With so-called brownfield integration, existing machines are equipped with retrofit sensors and communication modules – for example, with the Clouver SmartKit.
The process is divided into four steps:
- Analysis of the machine park: Identification of relevant equipment and parameters
- Selection of the retrofit solution: Appropriate sensors and communication modules
- Installation and configuration: Integration into your IIoT network
- Data utilisation: Using the information for optimisation
This integration offers you numerous advantages: comprehensive real-time insight into production processes, reduced downtime, and increased efficiency. Moreover, this solution enables a gradual, cost-efficient transformation of your manufacturing – also with regard to future developments such as Industry 5.0.
Your Partner for Innovative Automation Solutions!
ProCom offers the perfect combination of intelligent software, premium hardware, and comprehensive support. Whether knife, laser, or waterjet cutting – we'll develop the ideal solution for your production needs. Arrange your consultation today and get started!
6. Conclusion
The definition of Industry 4.0 shows how closely digital technologies are linked with modern production. From intelligent networking to the integration of real-time data – the possibilities for increasing efficiency are enormous. With approaches such as brownfield integration and continuous production monitoring, you create future-proof manufacturing.
Our expertise at ProCom Automation supports you in approaching the challenges of digitalisation pragmatically. With Clouver, you can effectively integrate both new and existing systems into your digital ecosystem and benefit from increased machine efficiency.
Make your IIoT environment secure and future-proof! Discover how Clouver helps you minimise risks and maximise efficiency. Arrange a no-obligation consultation now – together we'll find the right solution for your company.