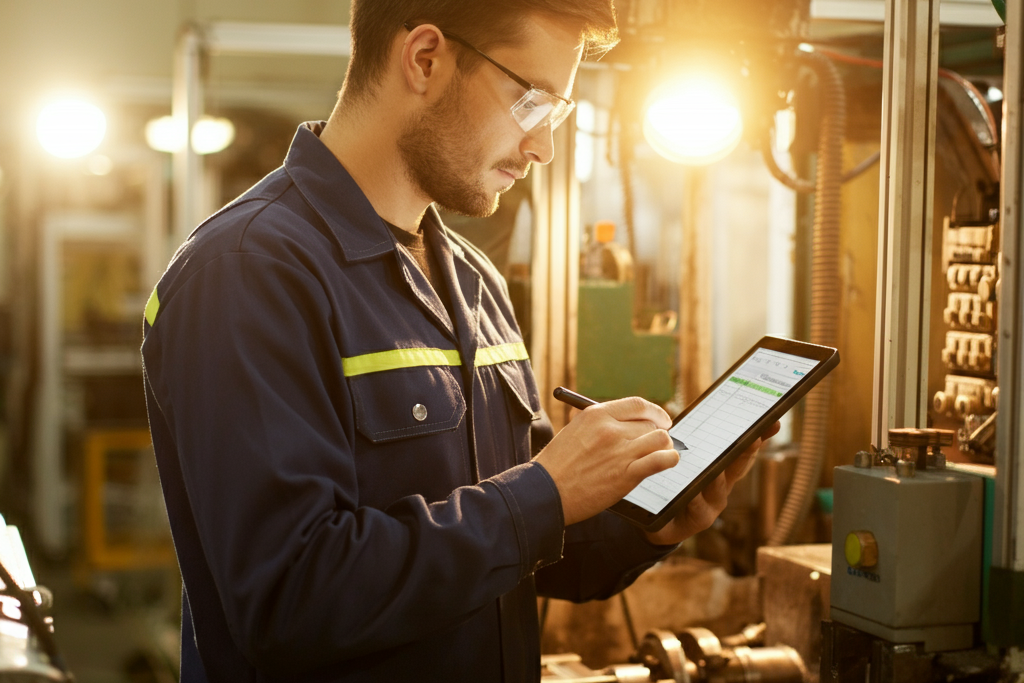
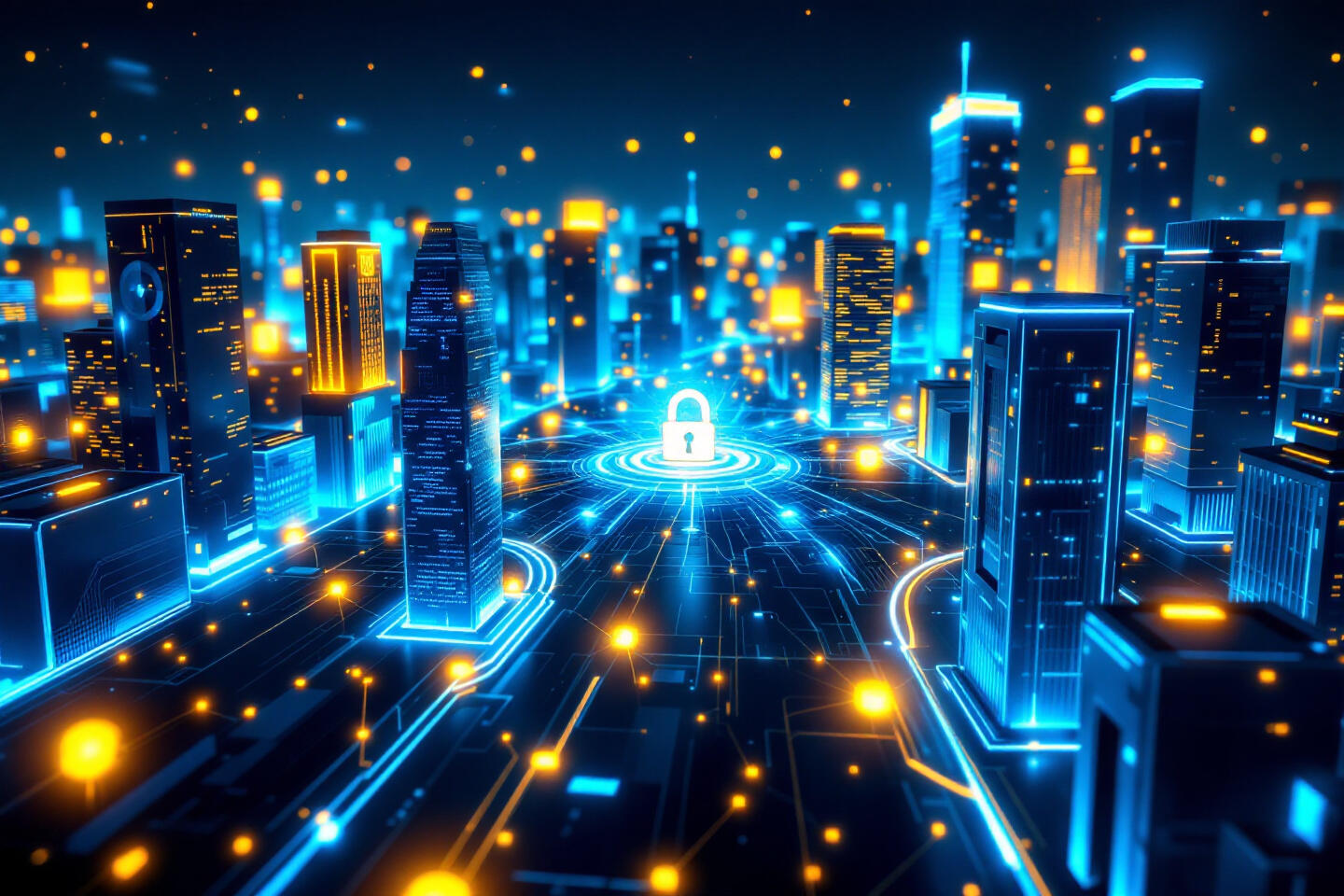
Whilst many of us are still working to understand and implement the concepts and technologies of Industry 4.0, the next major wave of innovation is already on our doorstep. But what exactly lies behind the term "Industry 5.0"? Why is it so important for companies and professionals to engage with it now?
Industry 5.0 promises even closer collaboration between humans and machines, supported by advanced technologies such as Artificial Intelligence (AI), Big Data Analytics and Edge Computing. This new era of industrial development focuses not only on efficiency and automation but also on the adaptability and sustainability of production processes.
In this article, we will illuminate the essential differences between Industry 4.0 and 5.0, introduce the key technologies and demonstrate practical implementation strategies. We will also address the challenges that companies might face when transitioning to Industry 5.0 and how these can be overcome.
Definition and Significance
Industry 5.0 is the next stage of the industrial revolution, focusing on seamless collaboration between humans and machines. Whilst Industry 4.0 heavily emphasises automation and networking, Industry 5.0 focuses on integrating human creativity and intelligence into the production process. This new era emphasises human-machine collaboration to develop more efficient, creative and flexible solutions. The significance of Industry 5.0 lies in its ability to combine the strengths of humans and machines to not only increase productivity but also create more innovative and sustainable production methods.
Evolution from Industry 1.0 to 5.0
An overview of the development of industrial revolutions shows how profoundly technological progress has changed production:
- Industry 1.0: Introduction of mechanisation through water and steam power, which laid the foundation for industrial production.
- Industry 2.0: Enabled mass production through the use of electrical energy and assembly line work, leading to significant efficiency gains.
- Industry 3.0: Introduction of automation through electronics and information technology, making production processes more intelligent and flexible.
- Industry 4.0: Networking and digitalisation through the Internet of Things (IoT) and cyber-physical systems, enabling real-time monitoring and control.
The transition to Industry 5.0 marks another evolutionary step, where the synergy between human creativity and machine precision is used to make production not only more efficient but also more adaptable and sustainable.
Differences between Industry 4.0 and 5.0
Technological Differences
Industry 4.0 focuses on automation, networking and comprehensive data analysis to increase production efficiency and precision. In contrast, Industry 5.0 goes a step further by placing human-machine collaboration at its centre. The key technologies of Industry 5.0 include advanced AI, robotics, Big Data Analytics, Edge Computing and cybersecurity. These technologies enable deeper integration and interaction between human workers and machines, leading to a symbiotic production environment.
Human-Machine Collaboration
In Industry 5.0, humans play a central role in the production process. The collaboration between humans and machines leverages the strengths of both parties: humans bring creativity, problem-solving skills and flexibility, whilst machines offer precision, speed and efficiency. This interaction leads to improved product quality, higher flexibility in production and better adaptability to changing market requirements. Companies like Procom Automation rely on these collaborative approaches by using CNC machines and cutting machines that optimally interact with human workers to ensure seamless production.
Key Technologies of Industry 5.0
Artificial Intelligence and Machine Learning
AI and machine learning are central technologies in Industry 5.0 that enable the analysis of large amounts of data and the optimisation of production processes. Applications range from quality control to predictive maintenance and intelligent production planning. Through the use of AI, companies like Procom Automation can control and adjust their CNC machines and cutting machines more efficiently, leading to higher productivity and reduced downtime.
Robotics and Automation
Advances in robotics enable the automation of complex tasks and improved collaboration between humans and robots. Modern robots can flexibly respond to changes in production and support humans in physically demanding or dangerous tasks. Procom Automation integrates advanced robotics solutions to increase efficiency and safety in production whilst promoting the creativity and adaptability of human workers.
Internet of Things (IoT)
Connected devices and systems play a central role in Industry 5.0. IoT enables real-time monitoring and control of production processes, leading to higher efficiency and transparency. By using IoT technologies, companies like Procom Automation can collect and analyse precise data from their CNC machines and cutting machines to continuously optimise processes and identify bottlenecks early.
Big Data and Analytics
Processing and analysing large amounts of data are crucial for decision-making in Industry 5.0. Big Data Analytics helps identify patterns, optimise processes and make informed decisions. Companies use this data to improve production processes, reduce costs and increase product quality. With software solutions like Clouver, the leading production monitoring tool, companies can analyse real-time data and make immediate optimisations.
Edge Computing and Cloud Computing
Edge Computing and Cloud Computing complement each other perfectly in Industry 5.0. Whilst Cloud Computing enables central data processing and stores large amounts of data, Edge Computing ensures data processing close to the point of origin. This reduces latency times and increases system responsiveness. Procom Automation uses both technologies to ensure their production processes are both efficient and flexible, allowing data to be processed quickly and used in real-time.
Cybersecurity
With increasing networking and digitalisation, the importance of cybersecurity in Industry 5.0 is also growing. Protection measures and security protocols are essential to protect data and systems from threats. Companies must continuously invest in cybersecurity to secure their production processes and sensitive data. The implementation of robust security solutions ensures that industrial systems can be operated reliably and securely.
Optimise Your Production with Clouver!
With Clouver, you get precise insights into performance, downtimes, and production volumes – in real time. Make your processes more efficient and save time and costs. Get started now and discover how Clouver can revolutionise your production!
Automation and Control
Modern Control Systems
Modern control systems offer a variety of functions and benefits, including higher flexibility and efficiency. They enable the integration of AI systems and the implementation of predictive maintenance. Procom Automation relies on advanced control systems that enable precise monitoring and control of CNC machines and cutting machines, optimising production processes and minimising downtime.
Integration of AI Systems
The integration of AI systems into production control offers numerous benefits. AI can optimise production processes, predict downtimes and improve product quality. Through the use of AI, companies like Procom Automation can make their machines more intelligent, allowing them to independently adapt to changing conditions and work continuously more efficiently.
Predictive Maintenance
Predictive maintenance uses sensors and data analysis tools to predict maintenance needs. This significantly reduces unforeseen downtimes and maintenance costs. Procom Automation implements predictive maintenance in its CNC machines and cutting machines to proactively conduct maintenance work and extend machine lifespans.
Adaptive Production Control
Adaptive production processes flexibly adjust to changes, enabling higher efficiency and responsiveness to market requirements. This flexibility is particularly important in dynamic markets where demand can fluctuate quickly. Procom Automation uses adaptive control systems to quickly retool their production lines and thus meet their customers' requirements.
Enhanced Process Optimisation
Optimisation techniques and strategies help to continuously improve production processes and use resources more efficiently. Through ongoing process analysis and adjustment, companies can identify and eliminate bottlenecks.
Data Technical Aspects
Big Data Analytics plays a central role in decision-making within Industry 5.0. Companies collect vast amounts of data from various sources, including machines, sensors and production systems. This data is then analysed to gain valuable insights that contribute to optimising production processes. Big Data Analytics enables the identification of patterns and trends that indicate potential problems before they occur. This allows companies to take proactive measures to increase efficiency and improve product quality. Additionally, Big Data supports personalised production, where products can be individually tailored to customer wishes, increasing customer satisfaction and strengthening competitiveness.
Real-time Data Processing
Real-time data processing is crucial for rapid adaptation and control of production processes. By processing data in real-time, companies can immediately react to changes in production flow, e.g., during unexpected machine downtimes or quality deviations. This enables more precise and flexible control of production lines, increasing efficiency and minimising failures. With real-time data processing, companies like Procom Automation can continuously monitor their CNC machines and cutting machines and make immediate adjustments to ensure consistently high product quality.
Cloud Computing Solutions
Cloud Computing offers numerous benefits for Industry 5.0, including scalability, flexibility and cost efficiency. Through central storage and processing of data in the cloud, companies can access and analyse their production data from anywhere. This facilitates collaboration between different locations and enables faster decision-making. However, companies must also consider challenges such as data protection and data security. With solutions like Clouver, the leading production monitoring software, companies can ensure their data is securely stored and processed in the cloud whilst benefiting from cloud technology.
Future Perspectives
Sustainability Aspects
Industry 5.0 promotes environmentally friendly technologies and processes that contribute to reducing the ecological footprint. This includes the use of renewable energies, optimisation of energy consumption and minimisation of waste through more precise production methods. Sustainable practices are not only good for the environment but also make economic sense as they enable long-term cost savings and strengthen corporate image. Procom Automation supports companies in implementing sustainable production solutions that are both environmentally and economically beneficial.
Social Impact
The changes in the working world through Industry 5.0 are diverse. New job profiles and qualifications are emerging that require close collaboration between humans and machines. The integration of humans and machines leads to increased collaboration and a better working environment where creative and intellectual tasks take centre stage. Companies must ensure their employees have the necessary skills and knowledge to work successfully in an Industry 5.0 environment. Procom Automation offers training programmes and support to prepare employees for the new requirements.
Workplace Development
Industry 5.0 creates new job profiles and requires new qualifications. Employees must continuously undergo further training to meet the requirements of modern production environments. This includes skills in data analysis, operation and maintenance of advanced machines, and collaboration with intelligent systems. The development of the workplace towards a more networked and collaborative environment increases workplace attractiveness and promotes an innovative corporate culture.
Economic Potential
Industry 5.0 offers numerous market opportunities and growth possibilities. By implementing new technologies, companies can increase their competitiveness, develop new markets and create innovative products. The increased efficiency and flexibility of production processes enable companies to react more quickly to market changes and strengthen their position in global competition. With solutions from Procom Automation and Clouver, companies can optimise their production processes and fully exploit their economic potential.
FAQ
What is Industry 5.0?
Industry 5.0 is the next stage of industrial revolution focusing on collaboration between humans and machines. Unlike Industry 4.0, which focuses heavily on automation and networking, Industry 5.0 integrates human creativity and intelligence into the production process.
How does Industry 5.0 differ from Industry 4.0?
Industry 4.0 focuses on automation, networking and data analysis, whilst Industry 5.0 emphasises human-machine collaboration. It's about combining the strengths of humans and machines to develop more efficient and creative solutions.
What key technologies drive Industry 5.0?
Key technologies include Artificial Intelligence (AI), robotics, Big Data Analytics, Edge Computing, Cloud Computing and advanced sensors. These technologies enable seamless integration and collaboration between humans and machines.
What are the benefits of Industry 5.0?
Industry 5.0 offers numerous benefits, including increased efficiency, improved product quality, greater flexibility in production and stronger employee involvement in the production process. It also promotes innovation and creativity through the combination of human and machine capabilities.
What challenges exist in implementing Industry 5.0?
Challenges include the need to modernise existing systems, improve employee qualifications, ensure data protection and cybersecurity, and manage high investment costs. Effective change management is also crucial to successfully managing the transition to Industry 5.0.
Conclusion
Industry 5.0 represents a new era of industrial development characterised by closer collaboration between humans and machines. The central pillars of this development include not only the optimisation of production processes and the integration of cutting-edge technologies but also the sustainable and human-centric design of work environments. Companies like Procom Automation and Clouver play a decisive role by offering innovative solutions and software that facilitate the transition to Industry 5.0 and increase their customers' competitiveness.
Would you like to learn more about the latest technologies and developments in Industry 5.0? Visit our blog for further content or book a demo version of Clouver to experience the benefits of data-driven production control for yourself. Click here to learn more!
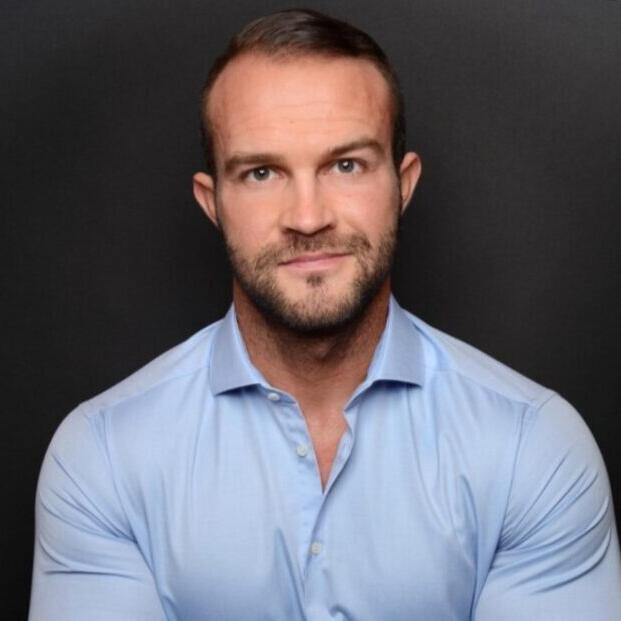
Sergej Gigel
Senior Sales Manager
Have questions about the topic or want to learn more about our solutions?
Contact us and discover how our products can future-proof your machines. Let’s work together to find out how we can help take your production to the next level!
- +49 241 93681-500
- contact@procom-automation.de
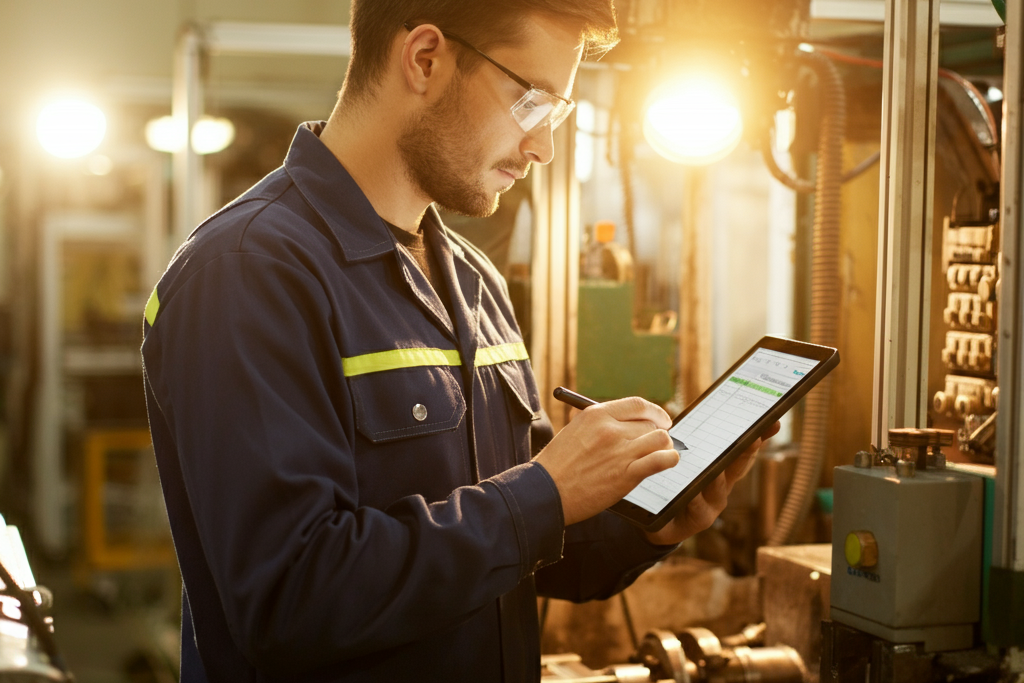
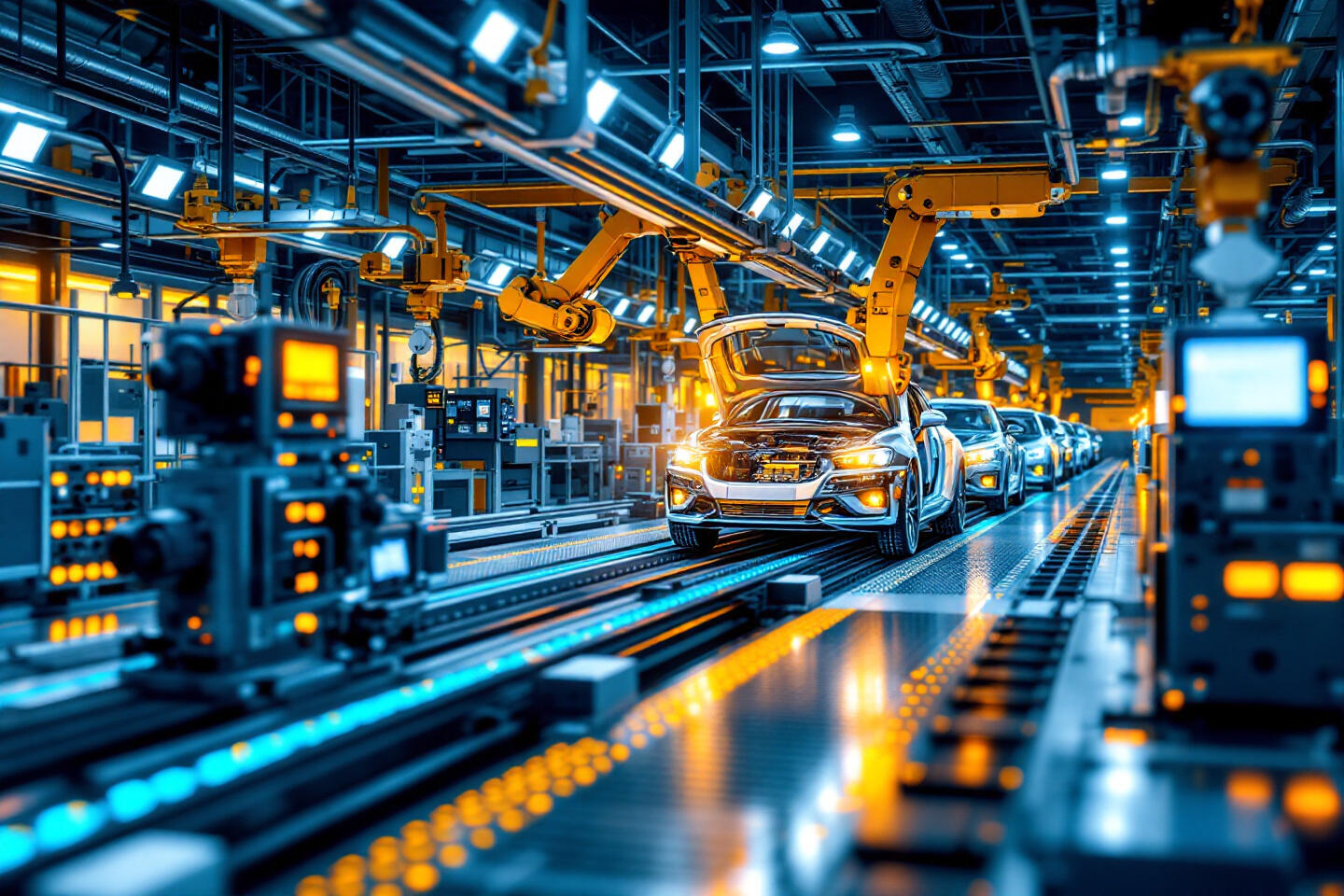