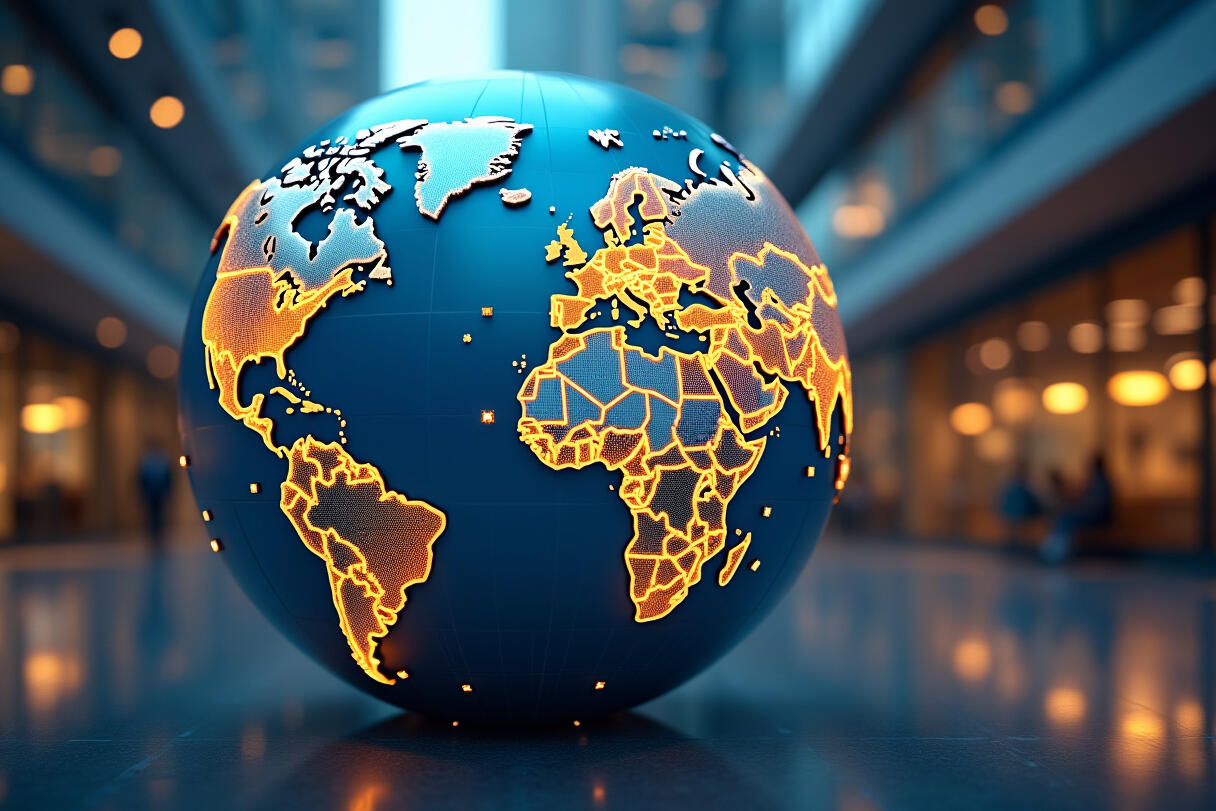
Whether in industrial automation, mechanical engineering, or medical technology – linear spindle drives play a crucial role in numerous applications. But what makes this technology so indispensable, and what advantages does it offer? In our detailed blog post, we take you on a journey through the world of linear spindle drives. We examine the technical fundamentals, the various types of spindles and their applications, as well as the latest developments and trends. You will learn how to select the right drive for your specific requirements, which maintenance strategies have proven effective, and how you can maximise the lifespan of your systems through preventive measures. Benefit from practical tips and expert knowledge to make your projects more efficient and sustainable. Stay tuned and discover how you can master your technical challenges with the right linear spindle drive!
Introduction to Linear Spindle Drives
Definition and Operation
A linear spindle drive is a mechanical system that converts rotational motion into linear motion. The main components of such a drive are the electric motor, gearbox, guide, and ball screw. These drives are used in numerous applications to enable precise movements and positioning. The electric motor generates a rotational movement that is transferred to the spindle via the gearbox. This rotational movement is converted into linear motion by the ball screw, allowing loads to be precisely positioned or moved.
Main Components
Electric Motor: The electric motor is the heart of the linear drive and provides the necessary rotational movement. Depending on the application, various types of electric motors can be used, such as DC motors, AC motors, or stepper motors.
Gearbox: The gearbox transfers the motor's rotational movement to the spindle and amplifies the torque. It can have various gear ratios to achieve the desired speed and force.
Guide: The guide ensures stability and precision of movement. It ensures that the spindle moves in a straight line while minimising lateral deviations or vibrations.
Ball Screw: The ball screw is a central element that converts rotational movement into linear motion. It consists of a threaded spindle and balls that are guided in a circulation path. This design reduces friction and increases the efficiency and lifespan of the system.
Fields of Application
Linear spindle drives are used in many areas, including industrial automation, mechanical engineering, medical technology, and many more. In industrial automation, for example, they are used in CNC machines to precisely position and move tools. In mechanical engineering, they enable exact control of machine components. In medical technology, they are used to position patient beds and medical devices. Other applications include robot arms, packaging machines, optical devices, and numerous other areas where precise and reliable linear movements are required.
Technical Fundamentals
Different Types of Spindles
There are various types of spindles that can be selected depending on requirements and operating conditions:
Ball Screw: This type of spindle offers high precision and efficiency. The balls reduce friction and enable smooth movement. They are ideal for applications requiring high accuracy and repeatability.
Trapezoidal Thread Spindle: These spindles are cost-effective and simple to manufacture. However, they are less efficient than ball screws as they generate more friction. They are well-suited for applications with lower precision and efficiency requirements.
Roller Thread Spindle: These spindles offer high load capacity and longevity. They consist of rollers guided in a threaded path, which reduces friction and increases load capacity. They are suitable for applications requiring high forces and long service life.
Mathematical Foundations
The mathematical foundations of a linear spindle drive include gear ratios and efficiencies that affect the drive's efficiency and performance. The gear ratio determines how many motor revolutions are required to achieve a specific linear movement. The efficiency indicates how much of the applied energy is actually converted into motion. High efficiency is crucial to minimise energy losses and maximise performance.
Types of Pitch and Their Influence
The type of pitch of the spindle has a direct influence on the speed and force of the drive. A higher pitch means the spindle covers a greater distance with each revolution, enabling higher speeds. However, the force decreases as the rotational movement is distributed over a greater distance. A lower pitch leads to higher forces but lower speeds. The selection of the right pitch therefore depends on the specific requirements of the application.
Bearing Concepts
The bearing of the spindle is crucial for the performance and lifespan of the drive. Correct bearing reduces friction and minimises wear. Common bearing concepts include fixed bearings and floating bearings that provide axial and radial stability for the spindle. Precision bearings can be used to increase accuracy and extend service life. Regular maintenance and lubrication of the bearings is also important to ensure optimal drive function.
Main Types of Linear Spindle Drives
There are various main types of linear spindle drives that differ in design and application:
Spindle Lifting Gear: These drives are available in various versions, including cubic, classic, high-performance, and quick-lift gears. They are versatile and offer high precision and load capacity.
Push Chain: These drives offer flexibility and high load capacity. They are space-saving and can be used in applications with limited space.
MINI Drive: These compact drives are ideal for applications with confined spaces. They are water and dust protected and require no lubrication.
Electric Cylinder: These drives are energy efficient and offer high precision. They are suitable for applications requiring precise positioning and repeatability.
IP66 Actuator: These drives are protected against dust and water and are suitable for harsh environments. They offer long service life and require no lubrication.
Thread Drives: These drives are cost-effective and offer self-locking properties that enable secure positioning without additional brakes.
Selection Criteria for Linear Spindle Drives
Calculation Basics
When selecting a linear spindle drive, various calculation basics must be considered to ensure that the drive meets the requirements of the application:
Required Load: The load that the drive must move is a crucial factor in selection. The load capacity of the drive must be sufficient to safely move the load.
Speed: The desired movement speed influences the choice of spindle pitch and motor. Higher speed requires a higher pitch or a more powerful motor.
Positioning Accuracy: The required positioning accuracy determines the choice of spindle type and bearing system. Precision spindles and high-precision bearings are required to achieve high positioning accuracy.
Service Life Calculation and Critical Speeds
The calculation of the service life of a linear spindle drive is crucial to ensure the reliability and longevity of the system. Operating conditions such as load, speed, and operating time must be considered. The critical speeds of the spindle must also be considered to avoid vibrations and instabilities. Careful dimensioning and selection of components contributes to extending service life.
Buckling Load and Safety Factors
The consideration of buckling loads and safety factors is crucial for the reliability and longevity of the drive. The spindle must be sufficiently dimensionally stable to absorb the forces acting on it without buckling. Safety factors are applied to create a buffer against unexpected loads and increase the reliability of the drive.
Pioneering Technologies for Your Manufacturing!
With ProCom's high-tech solutions, you can digitise workflows, reduce downtimes, and make your production smarter. Contact us now for a no-obligation consultation!
Total Cost of Ownership (TCO)
Total Cost of Ownership (TCO) plays an important role in drive selection. In addition to acquisition costs, operating costs, maintenance costs, and the service life of the drive must be considered. A drive with higher acquisition costs can prove more cost-efficient in the long term if it offers lower operating costs and a longer service life.
Maintenance and Service
Lubrication Concepts
Regular lubrication of the spindle is crucial to extend service life and maintain drive efficiency. Various lubrication concepts can be applied, including manual lubrication, automatic lubrication systems, and lifetime-lubricated spindles. The choice of the right lubricant and adherence to recommended lubrication intervals are important to minimise wear and maximise performance.
Wear Indicators and Preventive Maintenance Strategies
Through preventive maintenance measures and recognition of wear indicators, failures and expensive repairs can be avoided. Regular inspections and monitoring systems help to detect signs of wear such as noise, vibrations, or play in the spindle early on. Preventive maintenance strategies include timely replacement of wear parts and adjustment of operating conditions to extend the drive's service life.
Troubleshooting Guide
A troubleshooting guide helps to quickly identify and solve common problems. Typical problems include unusual noises, vibrations, irregular movements, or insufficient drive performance. The causes of these problems can lie in lubrication, bearing, alignment, or overload of the drive. A systematic approach to troubleshooting and resolution helps to quickly restore the drive's operability.
Replacement Intervals and Recommendations
Regular inspections and adherence to replacement intervals ensure reliable drive function. Wear parts such as bearings, seals, or spindles should be replaced according to manufacturer recommendations to avoid failures. A maintenance schedule based on operating conditions helps determine replacement intervals and ensure long-term reliability of the drive.
Modern Developments
Integration in Industry 4.0
The integration of linear drives in Industry 4.0 enables intelligent monitoring and control. By networking drives with IoT platforms, operating data can be captured and analysed in real-time. This enables predictive maintenance, optimisation of operating parameters, and increased flexibility in production. Integration in Industry 4.0 contributes to increasing efficiency and reducing costs.
Predictive Maintenance
Predictive maintenance systems detect problems early and prevent failures. Through continuous monitoring of operating data such as vibrations, temperatures, or loads, anomalies can be detected and measures taken before a failure occurs. Predictive maintenance reduces downtime and maintenance costs and increases the reliability and service life of drives.
Energy Efficiency Optimisation and New Material Technologies
New materials and technologies improve the energy efficiency and performance of drives. Lighter and stronger materials reduce the weight and energy consumption of the drive. Advances in manufacturing technology enable more precise and efficient components. Energy efficiency optimisation also includes improving motors, gearboxes, and lubrication systems to minimise energy consumption and maximise performance.
Comparative Analyses
Comparison of Different Drive Concepts
A comparison of electromechanical, hydraulic, and pneumatic drives shows the advantages and disadvantages of the different systems. Electromechanical drives offer high precision, efficiency, and flexibility but are more expensive to acquire. Hydraulic drives offer high forces and are robust but less precise and energy efficient. Pneumatic drives are cost-effective and fast but less precise and suitable for applications with lower forces.
Cost Comparison and Environmental Aspects
The costs and environmental aspects of the different drive types are analysed. Electromechanical drives have higher acquisition costs but offer lower operating costs and better environmental performance through lower energy consumption. Hydraulic and pneumatic drives have lower acquisition costs but cause higher operating costs and environmental impacts through energy consumption and the need for oil or air compression.
Advantages and Disadvantages of Different Spindle Types
The different spindle types are compared regarding their properties and applications. Ball screws offer high precision and efficiency but are more expensive and sensitive to contamination. Trapezoidal thread spindles are cost-effective and robust but less efficient and precise. Roller thread spindles offer high load capacity and service life but are more complex and expensive to manufacture.
Special Application Areas
Clean Room Applications
Drives for clean rooms must meet special requirements. They must be dust and particle-free and must not release contaminants into the environment. Materials and lubricants used in clean rooms must meet clean room requirements. Linear drives with special seals and coatings are used to ensure environment purity.
Explosion-Protected Versions
Special drives are required for use in potentially explosive areas. These drives must comply with ATEX directive requirements and be designed so they do not constitute ignition sources. Explosion-protected drives are used in the chemical industry, oil and gas industry, and other areas where explosive atmospheres can occur.
High Temperature Applications
Drives for high temperatures must be particularly robust and heat resistant. They must be able to work under extreme temperatures without losing performance or reliability. High-temperature resistant materials and special lubricants are used to meet the requirements of these applications. Such drives are used in the steel industry, glass manufacturing, and other high-temperature processes.
Underwater Use and Food Industry
Special requirements for hygiene and corrosion resistance apply for use underwater and in the food industry. Underwater drives must be waterproof and corrosion resistant to withstand harsh conditions. In the food industry, drives must be made from food-grade materials and be easy to clean. Stainless steel and special coatings are often used to meet the requirements of these industries.
Practical Implementation
Assembly Instructions and Alignment
Careful assembly and alignment of the drive are crucial for function. Improper assembly can lead to malfunctions, increased wear, and failures. The manufacturer's assembly instructions should be followed exactly and appropriate tools used. The alignment of the spindle must be precise to ensure smooth movement.
Adjustment and Installation Positions
Adjustment and correct installation position ensure optimal performance. The spindle must be mounted in a straight line and without tension. The brackets and bearings must be correctly positioned and adjusted to distribute loads evenly. Careful adjustment minimises friction and increases the drive's service life.
Wiring and Control Integration
Correct wiring and integration into the control system are essential for operation. The cables must be laid securely and neatly to avoid damage and interference. The control unit must be correctly configured and programmed to achieve the desired movements and positioning. Good integration enables precise and reliable control of the drive.
Safety Aspects in Implementation
Safety aspects must always be considered during implementation. The drive must be installed so that there is no danger to persons or machines. Protective devices, emergency stop switches, and safety mechanisms should be installed and regularly checked. Careful planning and implementation of safety measures helps prevent accidents and damage.
Economic Aspects
Market Overview of Leading Manufacturers
An overview of leading manufacturers helps in selecting the right drive. Well-known manufacturers of linear spindle drives include Bosch Rexroth, Thomson Industries, SKF, HIWIN, and IAI. These manufacturers offer a wide range of products and solutions for various applications and requirements.
Price Developments and Availability of Spare Parts
Price developments and availability of spare parts are important factors in planning and operating linear drives. The costs for components and spare parts can vary depending on market conditions and availability. Good planning of spare parts procurement and choosing a reliable supplier are important for smooth operation.
Conclusion
Linear spindle drives are indispensable components in modern automation technology. Their versatility, precision, and reliability make them an ideal solution for numerous applications. The right selection, installation, and maintenance are crucial for the successful implementation of this technology. With the advancement of Industry 4.0 and new materials, linear spindle drives will continue to play an important role in industrial development. Through careful planning, regular maintenance, and consideration of specific requirements, companies can optimally benefit from the advantages of this technology and make their processes more efficient. Contact us to learn more!
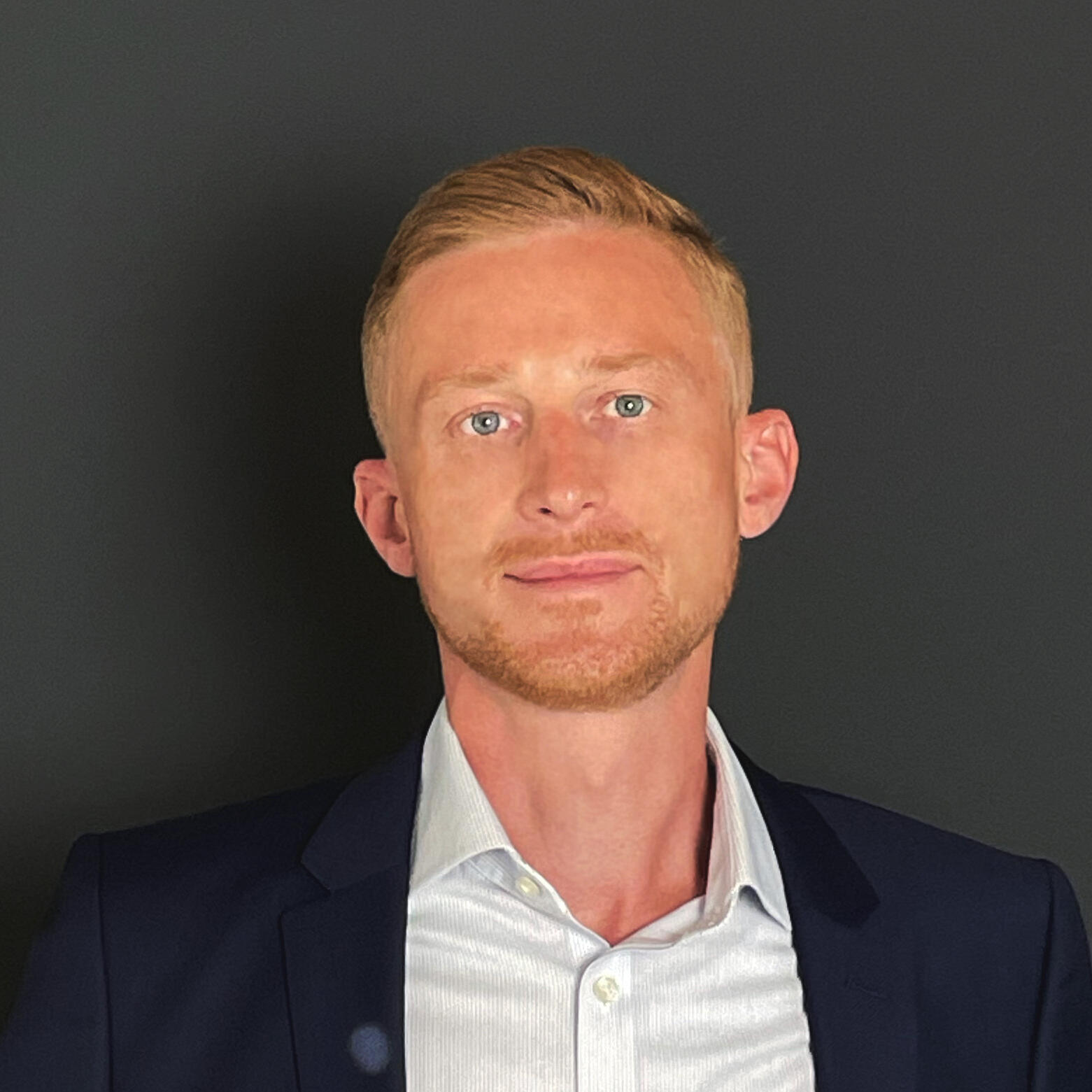
Dimitri Koneger
Sales Manager
Have questions about the topic or want to learn more about our solutions?
Contact us and discover how our products can future-proof your machines. Let’s work together to find out how we can help take your production to the next level!
- +49 241 93681-500
- contact@procom-automation.de
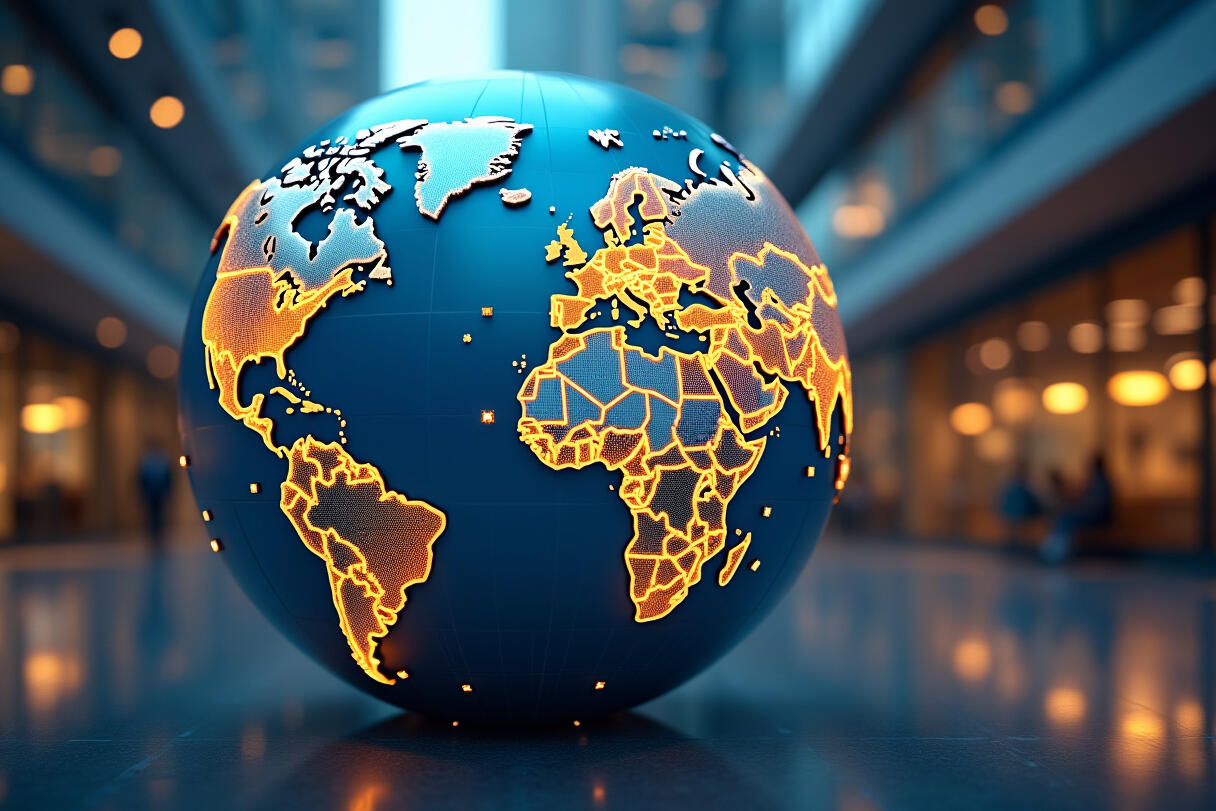
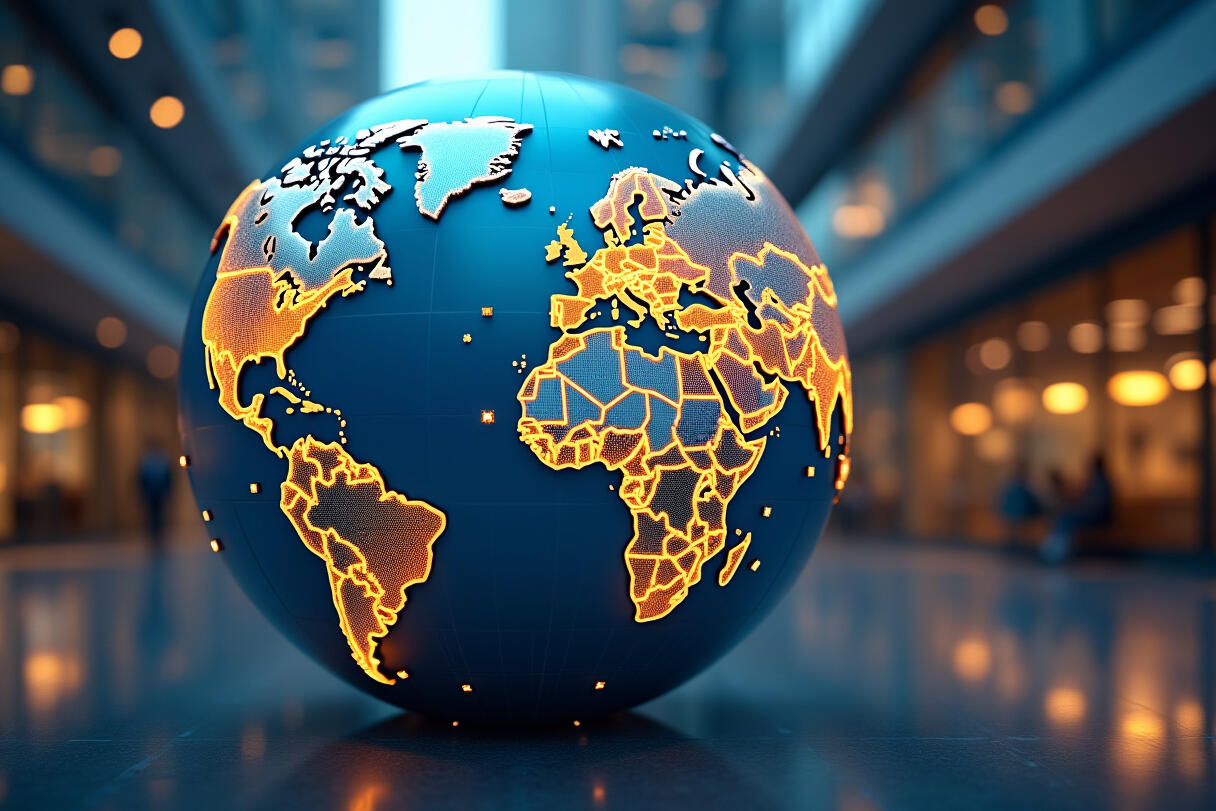