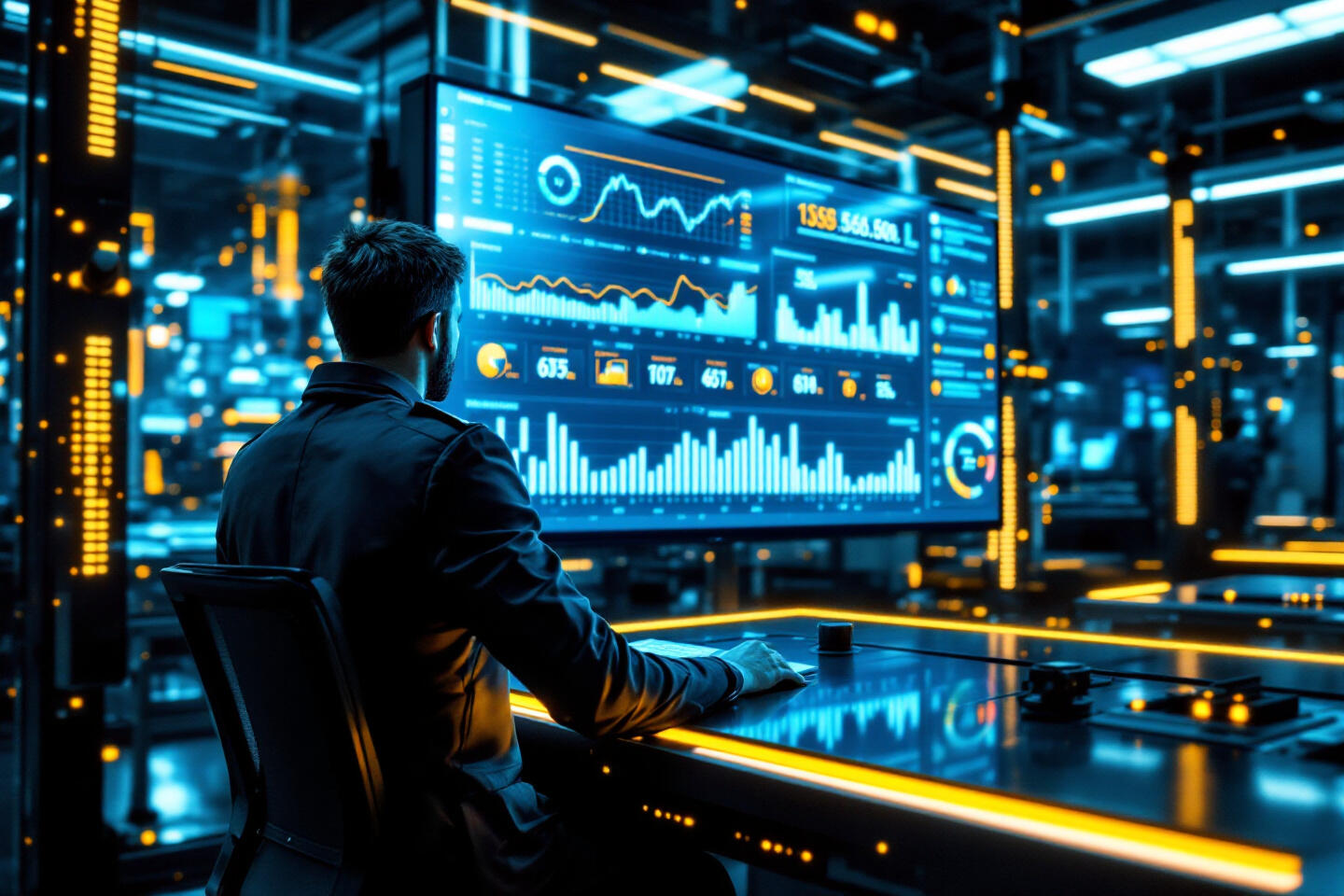
Machine data collection is much more than a technical buzzword – it's the key to more efficient processes, reduced downtime and data-driven decisions. Many companies face challenges: Which sensors are suitable? How can secure data transmission be achieved? And how can older machines be integrated into a modern Industrial Internet of Things (IIoT) network? In this article, we'll show you step by step how to not only collect machine data, but transform it into real added value for your production.
Fundamentals of Machine Data Collection: From Data Sources to Business Value
The starting point of any digital transformation in manufacturing is the systematic collection of operational data. Machine signals such as operating state, production speed and quality parameters are collected. Depending on the age and equipment of your systems, there are various collection methods:
- Direct control connection: For modern systems, data is read directly from the programmable logic controller (PLC) or CNC.
- Sensor-based collection: Older machines can be brought into the digital age using retrofittable sensors – for example, to detect vibrations or temperatures.
- Communication protocols: Industrial standards such as OPC UA and MQTT ensure reliable and secure data exchange.
The transition from raw data to usable business value occurs in several steps: First, data acquisition is carried out, then the input undergoes transformation and normalisation, before patterns and anomalies are detected through analysis and visualised in intuitive dashboards.
Get the Best Out of Your Production with Clouver!
Connect your machines and gain valuable insights into your production processes. Reduce unused capacity, optimise resource utilisation, and increase your revenue. Contact us today for a no-obligation consultation!
Systematic Data Selection for Successful MDE Projects
Are you wondering how to filter out the relevant data from a sea of information? Targeted data selection is crucial to gain insights that directly contribute to optimising your production processes.
The proven CRISP-DM approach structures this process into six iterative steps:
- Business Understanding: Define your production goals and derive concrete data requirements from them.
- Data Understanding: Identify the available data sources, from integrated sensors to control data from CNC systems.
- Data Preparation: Prepare the raw data purposefully – filter and normalise it for a uniform format.
- Modelling: Use suitable analysis methods to identify patterns and optimisation potentials.
- Evaluation: Check the results before rolling them out into your production processes.
- Deployment: Integrate the insights gained into your ongoing operations.
The modularly designed IIoT service – in the form of the Clouver platform – allows you to expand this process step by step and in a targeted manner.
Integration of Existing Machines into Modern Machine Data Collection
Particularly in heterogeneous machine parks with systems from different eras, technical hurdles must be overcome. Many older machines do not have Ethernet-based communication protocols or offer only limited access to internal data. But there are solutions:
- Retrofitting with IIoT gateways: You can indirectly capture operating states with external sensors.
- Direct connection to the control system: Open systems allow direct integration into the digital network.
- Specialised retrofit solutions: Adapters and protocol converters help to merge different data formats.
A structured approach first recommends an inventory: Check the machine park, determine the actual data requirements and assess the technical feasibility. With Clouver SmartKit, you can gradually integrate older systems into your IIoT network – modular and future-oriented.
Boost Your Productivity with Clouver!
With our powerful IIoT platform, you'll have complete control over your production processes at all times. Reduce downtime, optimise resource usage, and stay ahead of your competition. Schedule your personal consultation now and discover how Clouver can support you!
From Data Chaos to Process Optimisation: Real-time Analysis of Machine Data
How can you extract immediately usable insights from the confusing sea of data? Through real-time analysis of machine data. This analysis enables you to act not only reactively, but proactively: Through continuous monitoring, you identify deviations early and put immediate measures in place.
The multi-layered architecture of real-time analysis includes:
- Collection directly at the machine – sensors monitor critical components such as spindles or tools.
- Processing of data through cyber-physical systems, which perform initial evaluations close to the machine.
- Feeding the data into a central platform like Clouver, which enables advanced analyses and visualisations.
- Presentation of results in intuitive dashboards for all decision-makers in the operation.
In this way, data is transformed into actionable information: Faulty parts are identified in a timely manner, bottlenecks made visible, and energy consumption patterns analysed.
Cost-effectiveness of Machine Data Collection: ROI Calculation and Cost Savings
Investments in machine data collection systems must be economically worthwhile. A well-founded ROI calculation is therefore essential – whether through the reduction of unplanned downtimes, higher overall equipment effectiveness, or the optimisation of energy costs and setup times.
When calculating, you should consider the following factors:
- Investment costs: Hardware such as sensors, gateways and SmartKits, software licences, implementation effort and training costs.
- Quantifiable savings: Decreasing operational failures, improved efficiency (OEE increase) and reduced maintenance expenditures.
Practical examples show that even a few percentage points increase in machine utilisation can compensate for the investment costs – often within 6 to 18 months. With a modular IIoT system like Clouver, you can implement your MDE solution gradually, minimising investment risk whilst benefiting from initial efficiency gains.
Your Partner for Innovative Automation Solutions!
ProCom offers the perfect combination of intelligent software, premium hardware, and comprehensive support. Whether knife, laser, or waterjet cutting – we'll develop the ideal solution for your production needs. Arrange your consultation today and get started!
Conclusion
The collection of machine data is an indispensable component of modern production processes. It forms the basis for data-driven optimisations, increases efficiency and helps you remain competitive in the long term. IIoT platforms like Clouver score points with the highest data quality and real-time analyses – enabling you to react quickly and precisely to disruptions.