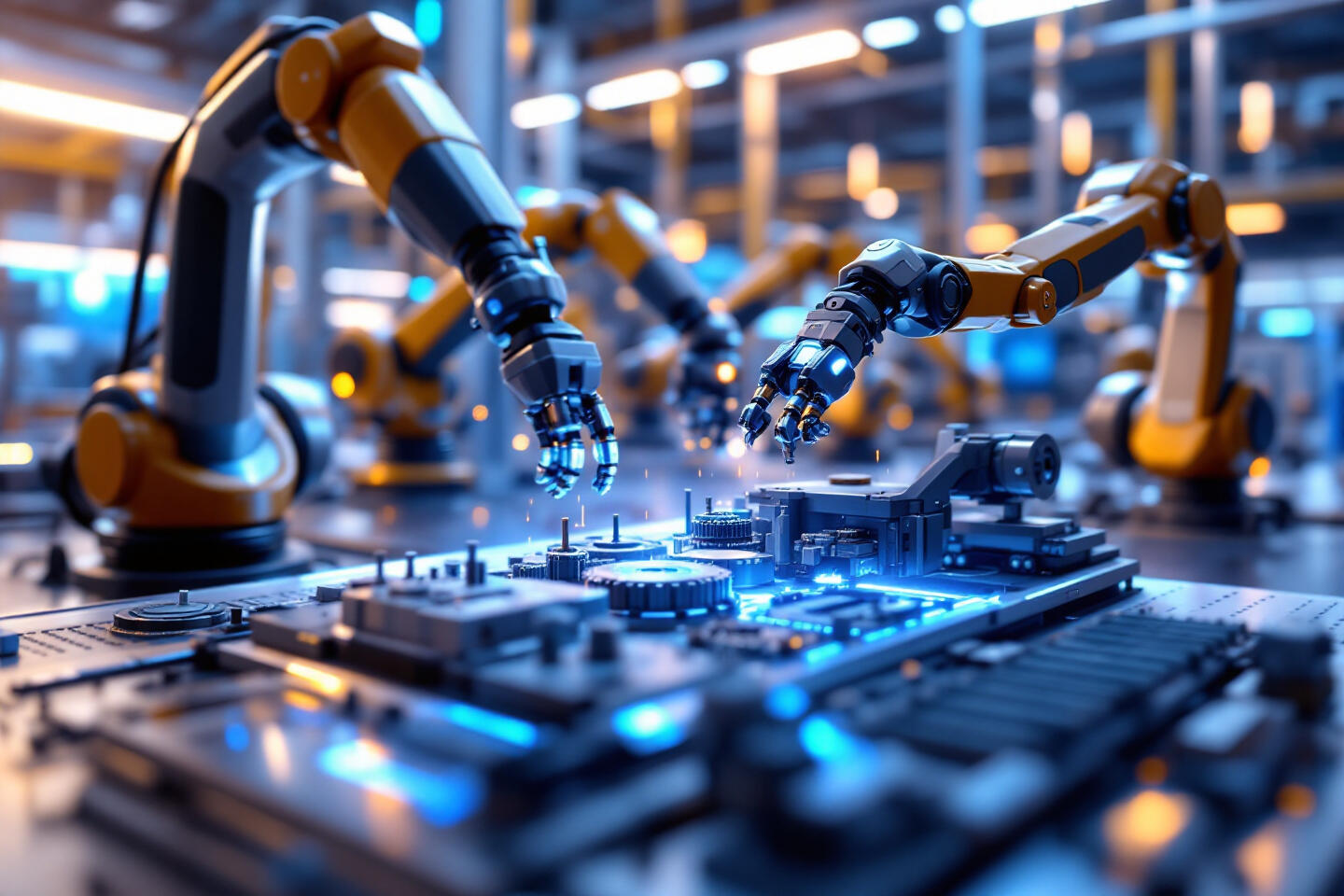
In production, every piece of scrap counts – not only as a cost factor but also as an indicator of inefficient processes. But why does scrap occur in the first place, and how can you specifically avoid it? This article shows you the causes behind high error rates, innovative approaches to reduction, and how to transform your scrap into a competitive advantage using data-based methods and smart technology. Your path to greater efficiency and less waste begins here.
Scrap in Production – Causes and Economic Impact
Simply put: Scrap is created when production processes are not precisely controlled. Defective products that fall outside given specifications cause not only material losses but also tie up important plant capacities. This reduces the Overall Equipment Effectiveness (OEE) and ultimately your efficiency.
The direct effects of scrap can be observed in several areas:
- Direct material costs: Raw materials and components processed in defective products.
- Wasted machine capacity: Production time during which no saleable parts are created.
- Energy consumption and personnel costs: Energy expended on faulty production, as well as working time for manufacturing and handling.
- Disposal costs: Expenses for the environmentally sound disposal of scrap parts.
Scrap is caused by various factors such as start-up losses, technical malfunctions, process fluctuations, material problems, setting errors, tool wear, and material loss in quality assurance samples. Each of these causes ties up resources that could be used productively elsewhere – and that's a clear competitive disadvantage in production.
Get the Best Out of Your Production with Clouver!
Connect your machines and gain valuable insights into your production processes. Reduce unused capacity, optimise resource utilisation, and increase your revenue. Contact us today for a no-obligation consultation!
Digital Real-Time Monitoring for Scrap Reduction
Are you wondering how to effectively reduce production scrap in your company? A decisive step is the introduction of digital real-time monitoring. Modern Industrial Internet of Things (IIoT) solutions like Clouver enable you to continuously monitor your machines and processes and identify problems before they lead to costly scrap.
The main advantages of digital monitoring are:
- Early warning system: Clouver continuously records machine data and identifies deviations from the target state, allowing for early correction.
- Automated quality control: Sensors measure critical parameters such as temperature, pressure, or speed and trigger automatic alarms when limits are exceeded.
- Real-time analysis and dashboards: Visualise scrap rates and process parameters in intuitive dashboards so you can see at a glance where action is needed.
- Push notifications: Direct notifications enable rapid intervention before minor problems escalate into scrap.
This digital method creates a transparent data basis for optimisation measures and reduces not only obvious scrap items but also hidden costs through material waste and inefficient machine runtimes.
Calculating the Hidden Costs of Production Scrap
If you want to understand the true costs of scrap in your production, you need to think beyond pure material loss. Scrap means that resources – from manufacturing wages to machine depreciation – remain unused or even cause additional costs.
The cost structure can be divided into direct and hidden costs:
- Direct costs include individual material costs, individual manufacturing costs, and proportionate overheads incurred during the production of defective parts.
- Hidden costs arise from manufacturing overheads such as depreciation, increased energy costs, and maintenance costs. Additionally, blocked machine capacity leads to an increase in fixed costs per unit produced.
- OEE losses: Any inconsistency in process quality reduces the overall equipment effectiveness, which affects the economic efficiency of your production in the long term.
The systematic recording and analysis of these costs ideally takes place via real-time data from the IIoT platform Clouver. By linking production data with cost structures, you gain complete transparency and can invest specifically in process improvements.
Data-Based Quality Optimisation in the Smart Factory
How can you reduce scrap in production through intelligent data analysis? The answer lies in data-based optimisation of your processes. The connection of sensors, control systems, and modern analysis allows you to capture and evaluate production data in real time.
Central components of this method are:
- Real-time monitoring of process parameters: Through continuous measurements of critical variables, you can identify trends that lead to a deterioration in quality.
- Data correlation and pattern analysis: The analysis of time series enables you to identify relationships between different process parameters and recognise causes of scrap.
- Process optimisation: Historical and current data provide a sound basis for adjusting machine parameters so that they permanently work within optimal tolerance values.
- Traceability: Comprehensive documentation of production data makes it possible to trace quality problems back to their origin and specifically address them.
The implementation of an IIoT production monitoring system like Clouver, which also integrates older systems via the Clouver SmartKit, provides a comprehensive overview of your production processes and supports you in sustainable scrap reduction.
Boost Your Productivity with Clouver!
With our powerful IIoT platform, you'll have complete control over your production processes at all times. Reduce downtime, optimise resource usage, and stay ahead of your competition. Schedule your personal consultation now and discover how Clouver can support you!
Sustainable Manufacturing Through Systematic Scrap Management
In Industry 5.0, systematic scrap management is the key to sustainable manufacturing processes. It combines ecological responsibility with economic efficiency and creates a comprehensive approach to reducing scrap batches.
A holistic approach to sustainable scrap management includes:
- Digital real-time recording: By using Clouver, all relevant process data is continuously recorded, allowing early detection of deviations.
- Root cause analysis with OEE loss breakdowns: A multi-level categorisation of the causes of disruption makes it possible to specifically address the main causes of scrap.
- Resource accounting: In addition to material costs, energy consumption, machine running times, and disposal costs are also included in the assessment.
- Circular economy: Approaches such as recycling or returning scrap material to the production cycle contribute to resource-efficient manufacturing.
- Human-centred processes: The involvement of employees in continuous improvement processes ensures that technical and organisational optimisations are implemented together.
The systematic recording of scrap data and the direct link with economic figures lead to more sustainable production with lower operating costs and improved overall equipment effectiveness.
Your Partner for Innovative Automation Solutions!
ProCom offers the perfect combination of intelligent software, premium hardware, and comprehensive support. Whether knife, laser, or waterjet cutting – we'll develop the ideal solution for your production needs. Arrange your consultation today and get started!
Conclusion
Scrap in production is not only an indicator of quality losses but also a clear sign of untapped potential in plant productivity. With targeted analysis and optimisation of OEE, you can not only reduce scrap but also sustainably improve the availability, performance, and quality of your plant. It is crucial to specifically identify and address all areas of loss.
If you want to tackle the challenges in your manufacturing and minimise scrap and other losses, Clouver offers you a tailored solution as an IIoT production monitoring platform. Make your IIoT environment secure and future-proof! Discover how Clouver helps you minimise risks and maximise efficiency. Arrange a non-binding consultation now – together we'll find the right solution for your company.