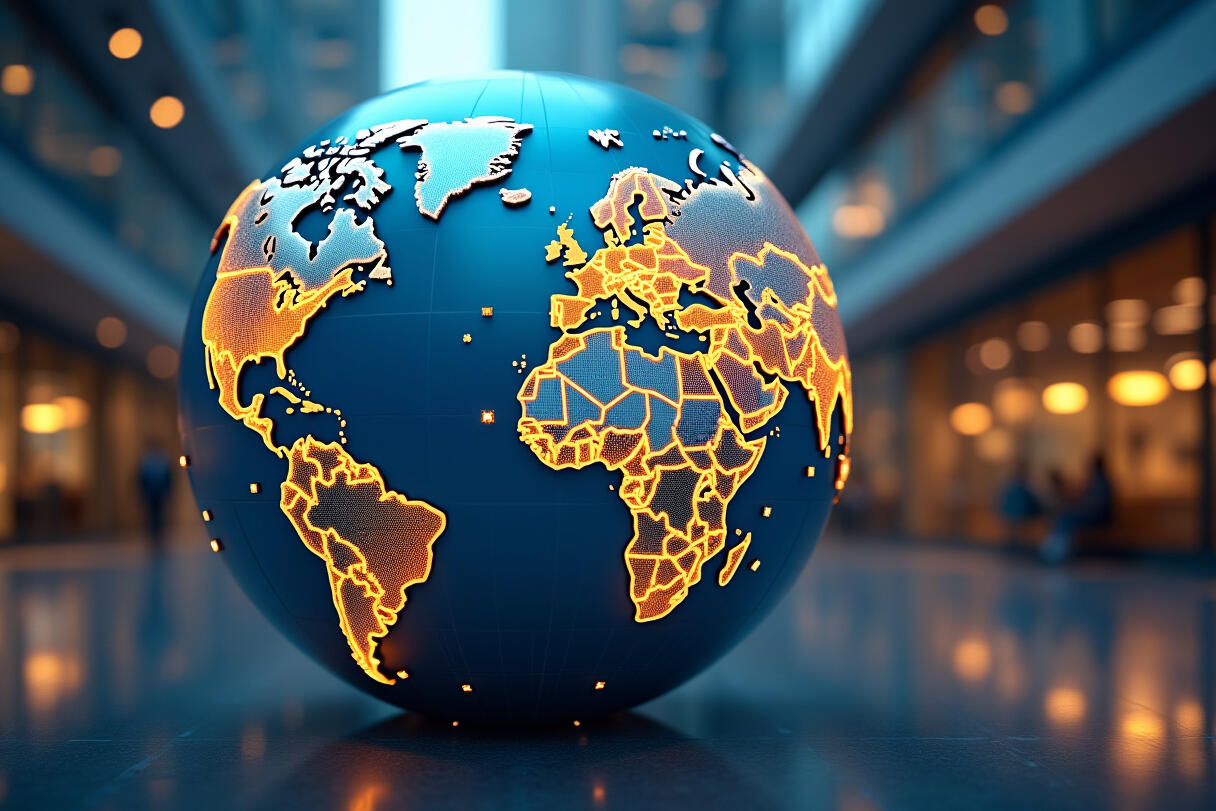

In a world where efficiency and productivity can make the difference between success and failure, understanding and applying OEE is essential. But what exactly lies behind this term, and why is it so important?
This post offers you a comprehensive introduction to the concept of OEE, explains the three main factors (availability, performance and quality) and shows you how they interact to form the overall picture of your production performance. Have you ever wondered how to minimise your machine downtime, optimise production speed or improve the quality of your products? We not only provide you with the answers but also practical tips and proven methods for implementation.
By reading this post, you will gain valuable insights that will help you increase the efficiency of your production facilities, reduce costs and ultimately enhance your competitiveness. Whether you're a beginner wanting to learn the basics or an experienced professional looking for advanced strategies – our post has something for everyone. Discover how OEE can revolutionise your production processes and why it is more relevant today than ever before.
What is OEE?
OEE stands for Overall Equipment Effectiveness and is a comprehensive metric for measuring the productivity of a machine or facility. The OEE metric serves to evaluate the actual performance of a production facility compared to its maximum possible performance. It comprises three main components: availability, performance and quality. The concept of OEE was originally developed as part of Total Productive Maintenance (TPM) and has since established itself as a standard in the manufacturing industry.
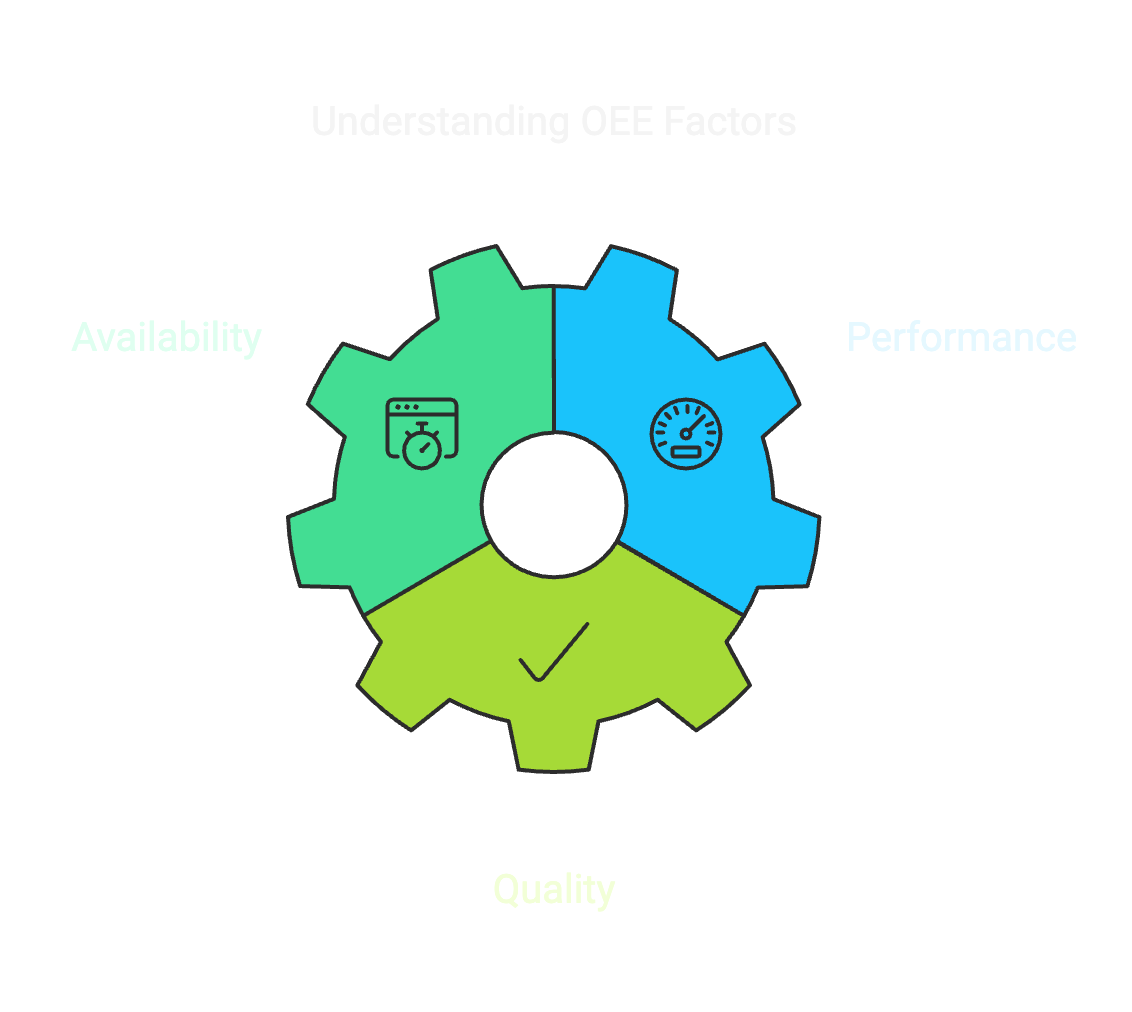
The Three OEE Factors
Availability
Availability measures the operating time of the facility in relation to the planned production time. To reduce downtime, it is recommended to focus on the Six Big Losses: breakdowns, setup times, idle time and minor stoppages, reduced speed, startup losses and scrap. By identifying and addressing the causes of these losses, you can significantly improve the availability of your facilities.
Performance
Performance assesses how quickly the facility produces compared to its ideal speed. To optimise production speed, you should implement strategies to reduce idle times and optimise process flows. A deep understanding of ideal cycle times and the factors that lead to delays is crucial.
Quality
Quality measures the proportion of good parts in total production. Measures to minimise defects are crucial to improve quality. This includes implementing strict quality controls, training staff and introducing process improvements to continuously enhance production quality.
Optimise Your Production with Clouver!
With Clouver, you get precise insights into performance, downtimes, and production volumes – in real time. Make your processes more efficient and save time and costs. Get started now and discover how Clouver can revolutionise your production!
Step-by-Step Implementation Guide
- Preparation: Communicate the goal and benefits of OEE to all stakeholders. Ensure all employees understand the concept and advantages.
- Data collection: Capture current operational data and document all downtimes and losses. Use automated systems for data collection to ensure accuracy and consistency.
- Analysis: Use the collected data to calculate OEE and identify causes of loss. Analyse the data to recognise patterns and trends.
- Plan measures: Develop strategies to reduce identified losses. Create a detailed action plan that includes specific measures and responsibilities.
- Implementation: Implement the measures and continuously monitor the results. Use regular reviews and adjustments to ensure improvements are sustainable.
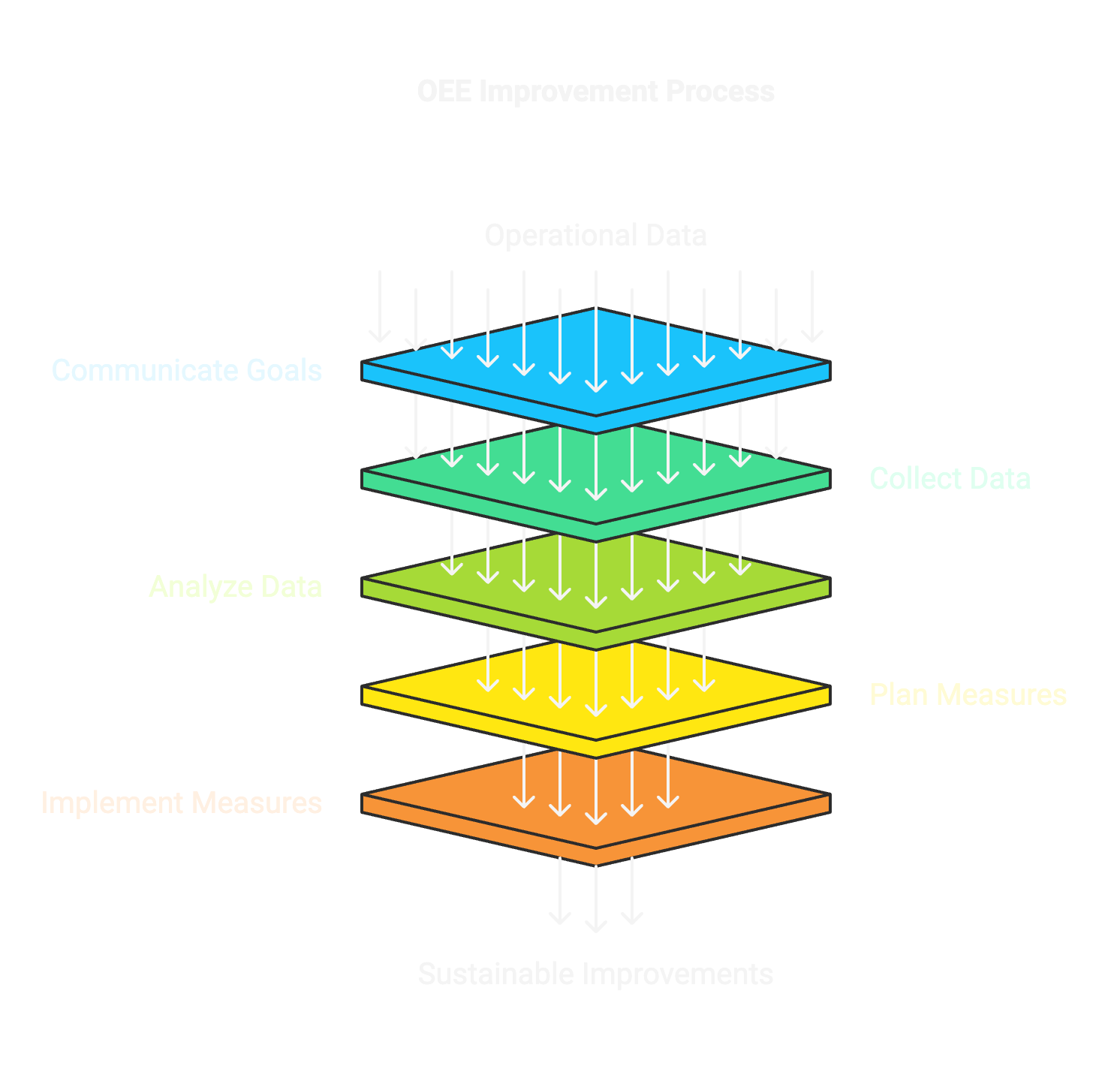
Modern Technologies and Trends
Technological Integration
- Use of AI for OEE optimisation: Artificial intelligence can be used to recognise patterns in production data and make predictions about future performance and potential failures.
- Integration of Predictive Maintenance: Through predictive maintenance, potential problems can be identified and resolved before they lead to failures, increasing facility availability.
- Real-time OEE monitoring: Real-time monitoring enables immediate response to problems and adjustments to optimise performance.
- Mobile OEE tracking solutions: Mobile applications enable OEE data to be monitored and analysed anytime, anywhere, improving decision-making and reducing response time.
Industry-Specific Applications
OEE is applied in various industries, including:
- Automotive industry: Optimisation of manufacturing processes to reduce downtime and improve production quality.
- Process industry: Improving the efficiency of continuous production processes by minimising failures and optimising process parameters.
- Mechanical engineering: Increasing machine availability and performance through targeted maintenance strategies and process improvements.
- Food industry: Ensuring high quality standards through continuous monitoring and improvement of production processes.
Advanced Metrics and Alternatives
Besides OEE, there are other metrics for evaluating production performance:
- TEEP (Total Effective Equipment Performance): Evaluates the total utilisation of the production facility, including planned and unplanned downtimes.
- OOE (Overall Operations Effectiveness): Considers the overall productivity of the operation, including logistical and organisational aspects.
- OPE (Overall Process Effectiveness): Evaluates the effectiveness of specific production processes and identifies opportunities for process improvement.
Future Perspectives of OEE
With Industry 4.0 and new technologies, OEE continues to evolve. Sustainability aspects and new calculation models offer additional optimisation possibilities. For example, using IoT devices and machine learning can capture more precise and timely data, enabling even more accurate analysis and optimisation.
FAQ Section
What is OEE and why is it important?
OEE is a metric for evaluating the efficiency of production facilities that considers availability, performance and quality. It is important because it helps companies understand and improve the effectiveness of their production processes.
How is OEE calculated?
OEE is calculated by multiplying the availability, performance and quality of a facility.
Which industries use OEE most frequently?
OEE is used in many industries, including the automotive industry, process industry, mechanical engineering and food industry.
What are the main benefits of OEE implementation?
The main benefits include reducing downtime, optimising production speed, improving product quality and increasing overall efficiency.
What are the most common mistakes in OEE calculation?
Common mistakes include inaccurate data collection, misunderstandings about the definition of OEE factors and neglect of continuous monitoring and adjustment.
Conclusion
In conclusion, Overall Equipment Effectiveness (OEE) represents a crucial metric for evaluating the efficiency and productivity of production facilities. Through the analysis of the three main components – availability, performance and quality – companies can gain valuable insights and take targeted measures to optimise their processes. A deep understanding of the OEE definition and its application enables minimising production losses and increasing competitiveness. For questions about OEE, please use our contact form!
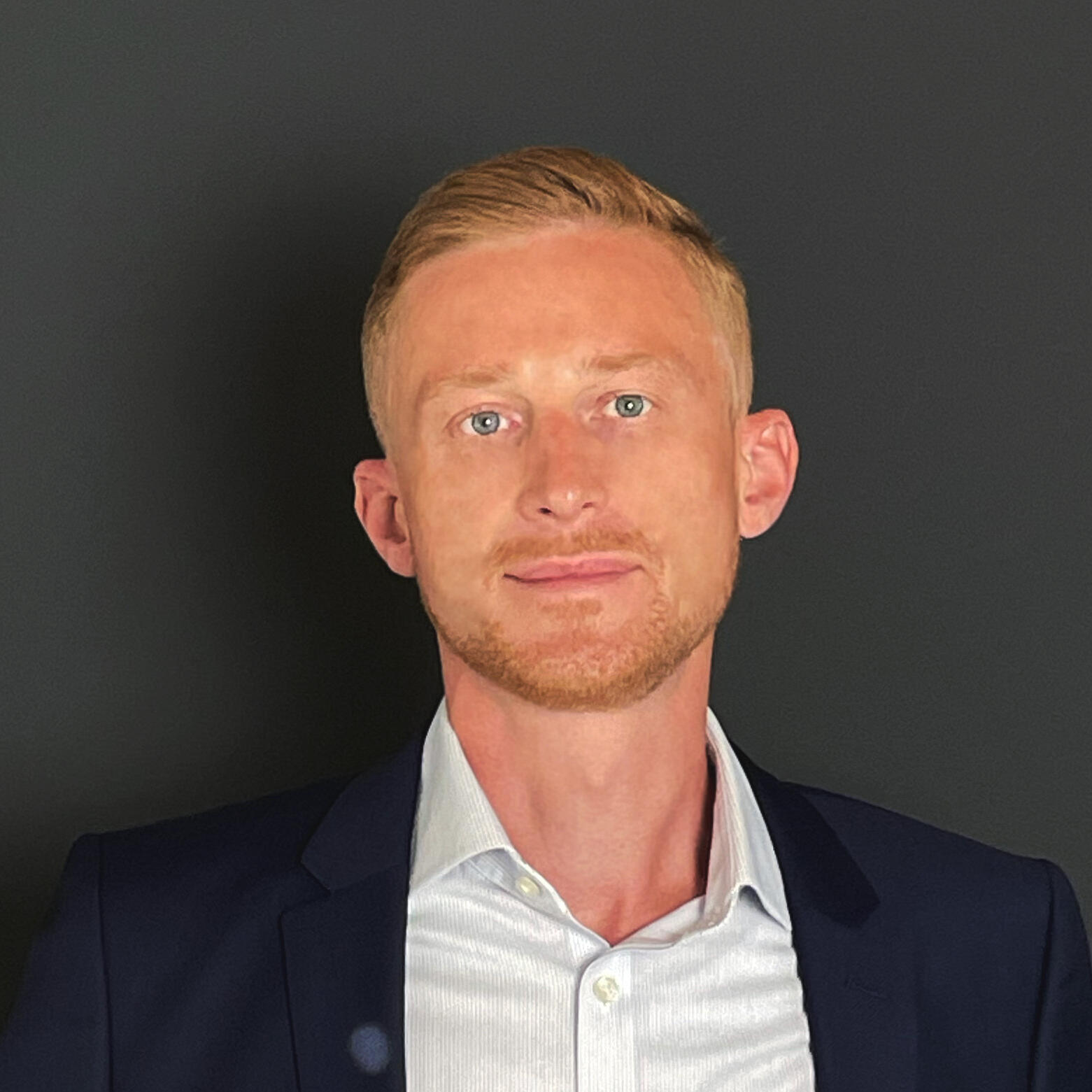
Dimitri Koneger
Sales Manager
Have questions about the topic or want to learn more about our solutions?
Contact us and discover how our products can future-proof your machines. Let’s work together to find out how we can help take your production to the next level!
- +49 241 93681-500
- contact@procom-automation.de
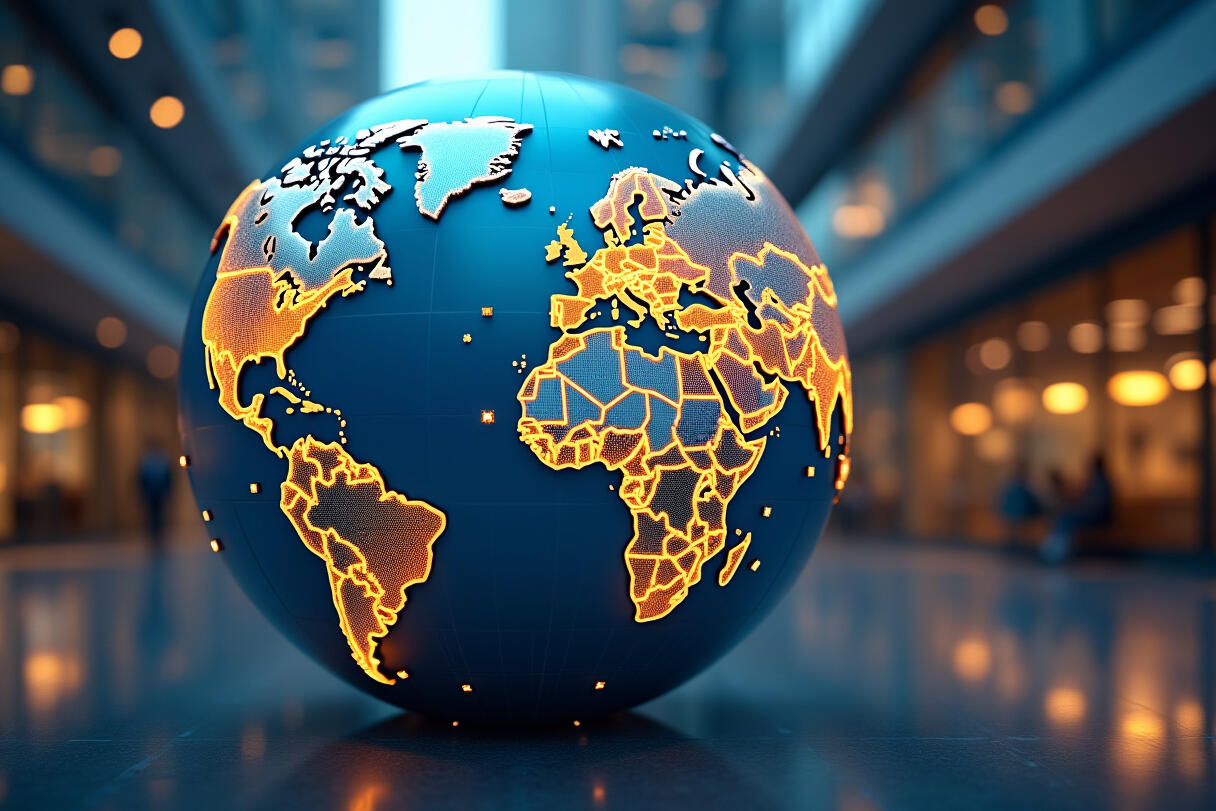
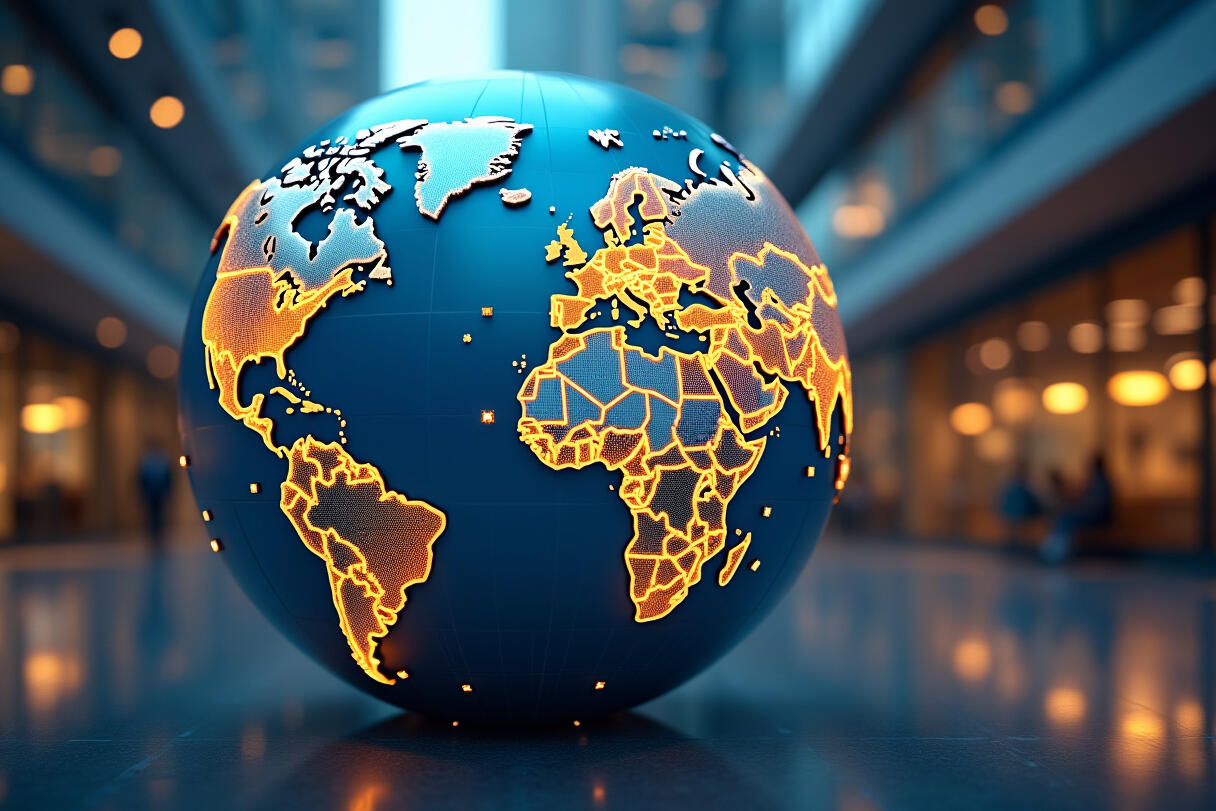