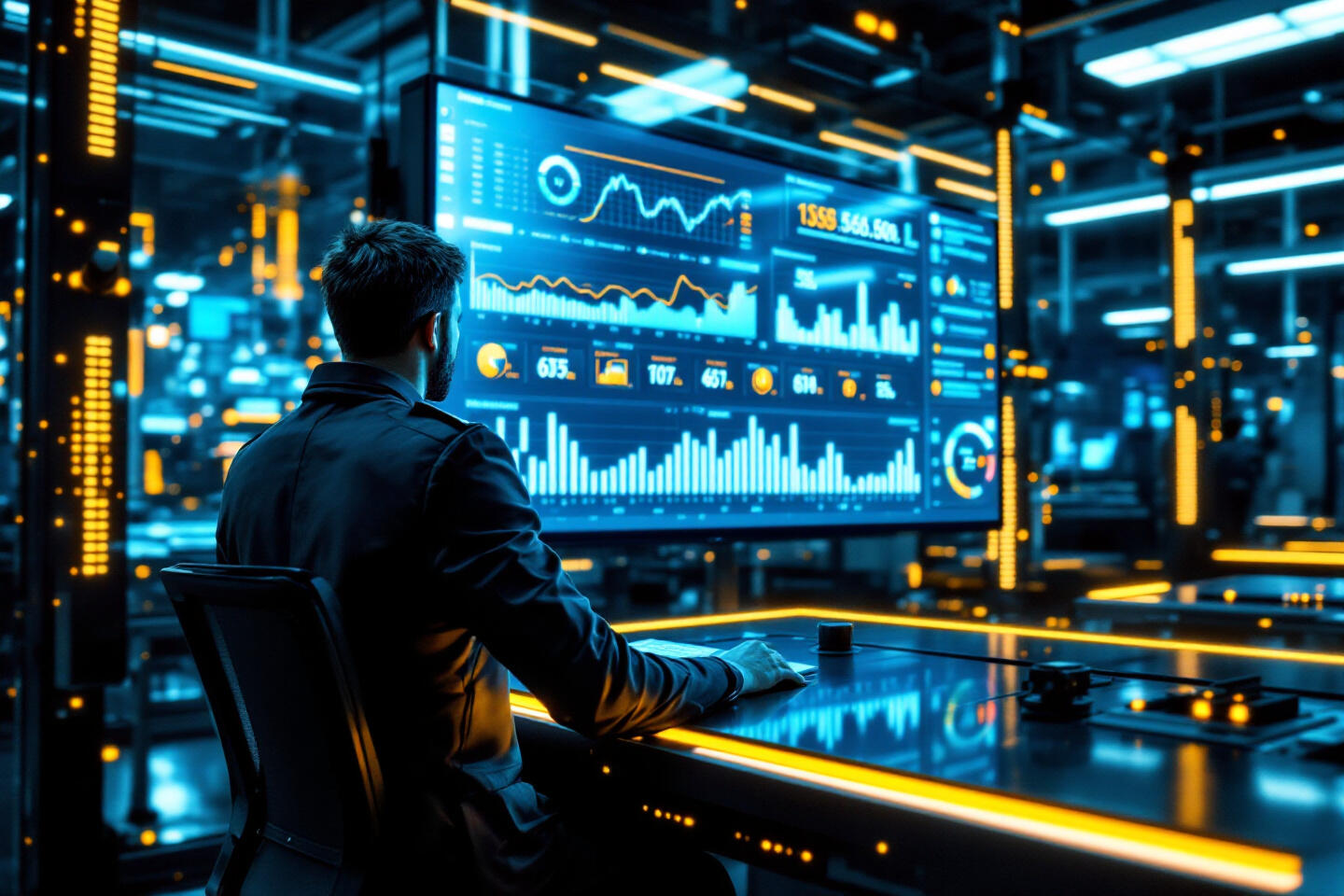
Imagine being able to see at a glance where valuable time, performance or quality is being lost in your production – and taking action precisely there to sustainably increase your efficiency. Overall Equipment Effectiveness (OEE) is the key metric that creates exactly this transparency. It shows you with brutal honesty how closely your equipment is operating to its maximum, ideal productivity and provides the data foundation to initiate targeted improvement measures. In this article, you will learn what OEE is exactly, how to calculate it pragmatically, and how you can take the next step towards production excellence using modern Industrial Internet of Things (IIoT) solutions, such as the Clouver platform from ProCom Automation.
OEE: Definition and Significance for Modern Manufacturing
OEE measures the "true" equipment productivity by systematically capturing all areas of loss that impair the output of your machines. Unlike isolated metrics such as pure runtime or quantity, OEE offers a holistic, unvarnished view of the efficiency of a machine or even entire production lines. It combines three essential factors:
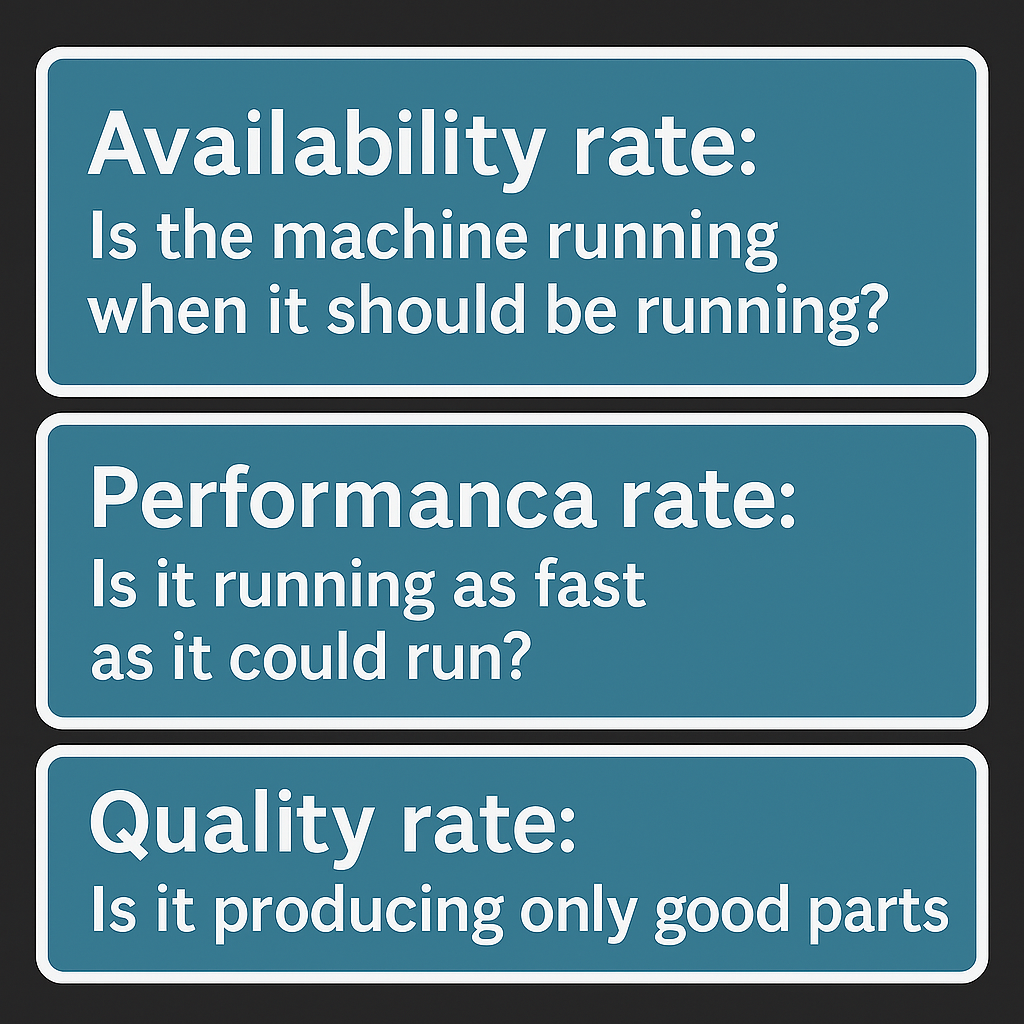
Multiplying these three factors gives the OEE value – a percentage that shows the unused potential.
The central idea behind OEE is to make the "Six Big Losses" (the six major sources of loss in production) visible:
The Three Key Elements of OEE Calculation in Detail
To determine the "true" equipment productivity, OEE breaks down the complexity into three tangible factors:
1. Availability – The Foundation of Equipment Productivity
The availability rate measures how much of the planned production time your equipment is actually running productively. Any downtime that occurs during planned operating time reduces availability. This includes unplanned machine failures (disruptions), planned downtime such as setup times or maintenance, as well as organisational delays (e.g. material shortages).
The calculation is done using the formula:
- Availability rate = (Actual production time / Planned production time) × 100%
- Actual production time = Planned production time - Sum of all downtime
Modern IIoT solutions like Clouver revolutionise data collection here: Instead of manual estimates or tally sheets, they provide precise, automatically recorded timestamps for the start and end of each downtime. Through connected sensors or machine signals, Clouver can often even automatically categorise downtime reasons. This allows you to immediately identify, without manual effort, which availability losses offer the greatest leverage for improvements.
Get the Best Out of Your Production with Clouver!
Connect your machines and gain valuable insights into your production processes. Reduce unused capacity, optimise resource utilisation, and increase your revenue. Contact us today for a no-obligation consultation!
2. Performance – Measuring Production Speed
The performance rate indicates how efficiently your equipment operates during its actual runtime. It compares the actual production quantity (number of pieces) with the theoretically possible output at ideal (or maximum specified) cycle time or speed.
Calculate the performance rate like this:
- Performance rate = (Actually produced quantity / Theoretically possible quantity in production time) × 100%
- Theoretically possible quantity = Actual production time / Ideal cycle time per piece
Common causes of performance losses are short, often unnoticed interruptions (micro-stops), idle times or deliberately or unconsciously reduced machine speed (e.g. due to wear, poor material quality or suboptimal settings). Continuous monitoring via systems like Clouver helps to make these often hidden losses visible, which would be overlooked with manual recording.
3. Quality – Ensuring Error-Free Production
The quality rate measures the proportion of flawless products (good parts) in the total production within the considered time period. Scrap, rework (parts that need to be repaired) and defective parts during the startup phase after setup are typical reasons for quality losses.
Calculate it with:
- Quality rate = (Number of good parts / Total number of produced parts) × 100%
- Total number of produced parts = Good parts + Scrap/Rework
The digital recording of quality data directly at the machine or line, as enabled by Clouver, allows quality deviations to be detected immediately – not just at the end of the shift or during final inspection. Through automated documentation of even minor quality issues, you can respond more quickly and systematically address the causes.
The Overall OEE: The Multiplication Result
The final OEE value is derived from multiplying the three factors:
OEE = Availability rate × Performance rate × Quality rate
An OEE value of 85% is often considered world-class, although this strongly depends on the industry and equipment type. Much more important than an absolute benchmark, however, is the continuous improvement of your own OEE value.
Boost Your Productivity with Clouver!
With our powerful IIoT platform, you'll have complete control over your production processes at all times. Reduce downtime, optimise resource usage, and stay ahead of your competition. Schedule your personal consultation now and discover how Clouver can support you!
Real-Time OEE Monitoring with IIoT Solutions: The Game Changer
Are you wondering how to efficiently, precisely and, above all, collect and evaluate all these production data in real time? The answer lies in digital transformation and the Industrial Internet of Things (IIoT). Modern IIoT platforms like Clouver from ProCom Automation revolutionise OEE management by switching from error-prone, time-delayed manual data entry to automated real-time measurements.
From Manual Records to Automated Analyses
Traditional methods of OEE recording often relied on manual notes from machine operators and later entries into Excel spreadsheets. This approach is not only time-consuming but also has a high potential for inaccuracies, estimates and delays in detecting production losses.
With an IIoT platform like Clouver, all OEE-relevant data – runtimes, downtimes, piece counts, cycle times, quality reports – are automatically captured directly from the machine or via simple sensors.
The advantages of real-time recording with Clouver are crucial:
- Immediate visualisation: You see machine utilisation, current OEE values and occurring downtimes live on clear dashboards – accessible anytime and anywhere.
- Automatic calculation: All OEE components are determined without manual inputs or calculations.
- Objective data basis: No more guesswork – you make decisions based on facts.
Direct notifications: Set up alarms that immediately inform you or your team of significant deviations or longer downtimes, enabling quick responses.
Your Partner for Innovative Automation Solutions!
ProCom offers the perfect combination of intelligent software, premium hardware, and comprehensive support. Whether knife, laser, or waterjet cutting – we'll develop the ideal solution for your production needs. Arrange your consultation today and get started!
Technological Foundations of Real-Time Monitoring
The digital recording of production data via a platform like Clouver typically takes place across multiple levels:
- Machine connectivity: Direct connection to the machine control (PLC) via standard interfaces (e.g. OPC UA) or retrofitting simple sensors (e.g. light barriers, current sensors, vibration sensors) to record operating states and quantities.
- Edge computing (optional): Compact hardware modules like the Clouver SmartKit can pre-process, buffer and securely send data directly at the machine to the central platform. This minimises network load and enables autonomy during network interruptions.
- Cloud platform or on-premises: The central Clouver software collects, stores and analyses the data. This is where OEE calculations are performed, dashboards generated and reports created.
A major advantage of Clouver is its modularity and flexibility: With the Clouver SmartKit, older machines or equipment from different manufacturers that were previously not network-capable (brownfield approach) can be easily and cost-effectively integrated into digital monitoring. This gives you a unified overview of your entire machine park.
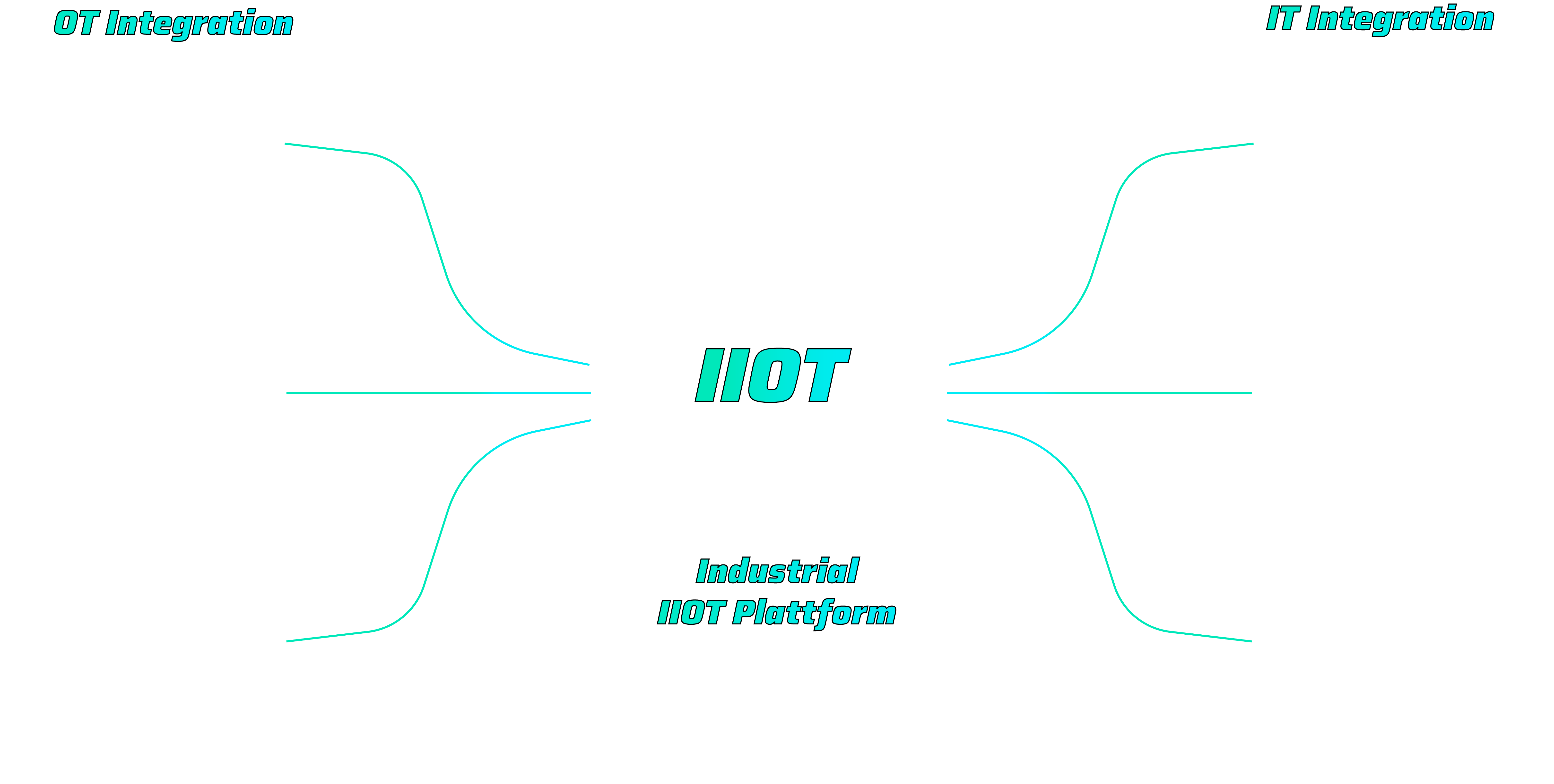
OEE Optimisation Through Automated Production Monitoring
Would you like to not only measure your equipment productivity but also continuously and systematically increase it? The answer lies in automated production monitoring that puts OEE at the centre of your optimisation strategy.
From Reactive Troubleshooting to Proactive Control
Traditional OEE analyses often take place only at the end of a shift or even the next day. Valuable reaction time is lost. Clouver enables immediate evaluation of production data. You see in real time when equipment is running below expected performance, an unexpected stoppage occurs or the scrap rate increases – and can intervene immediately, not hours later.
Automated monitoring offers you the following strategic advantages:
- Precise real-time measurements: Recognising problems as they happen.
- Early warning systems: Defined thresholds trigger alarms before small problems become major failures.
- Granular loss analyses: Detailed evaluations of downtime reasons, performance deviations and quality defects over time periods reveal patterns and the true causes (Pareto analysis of losses).
- Data-based prioritisation: Focus your improvement efforts on the largest sources of loss with the highest optimisation potential.
Such data-driven insights help you identify recurring patterns and derive targeted, sustainable measures to improve OEE – whether through technical adjustments, process changes or targeted employee training.
Practical Implementation – How to Start with OEE Optimisation
The implementation of an automated OEE monitoring system with a solution like Clouver ideally takes place in structured steps, with ProCom Automation supporting you with its expertise:
With this approach, OEE becomes a living, effective instrument that helps you achieve operational excellence and secure your competitiveness in the long term.
Ready to take the first step towards OEE optimisation?
Our experts from ProCom Automation are happy to advise you without obligation on how to successfully implement Clouver in your production. Schedule your free consultation now!
Summary: OEE and IIoT – The Dream Team for Production Excellence
Overall Equipment Effectiveness (OEE) is more than just a metric – it is a compass that shows you the way to more efficient and productive manufacturing. It makes the hidden losses in your production transparent by holistically considering availability, performance and quality.
While manual collection of OEE data can be laborious and inaccurate, modern IIoT solutions like Clouver from ProCom Automation unleash the full potential of this concept. Through automated real-time data collection, precise analyses and immediate visualisation, you gain the necessary insights to specifically identify waste, act proactively and sustainably increase your equipment productivity.
ProCom Automation supports you in fully exploiting these potentials. With our many years of experience in industrial automation and our flexible, modular IIoT platform Clouver, we offer you a holistic solution from a single source – from connecting your machines to data-driven optimisation of your processes.
Make your production more transparent, efficient and future-proof!