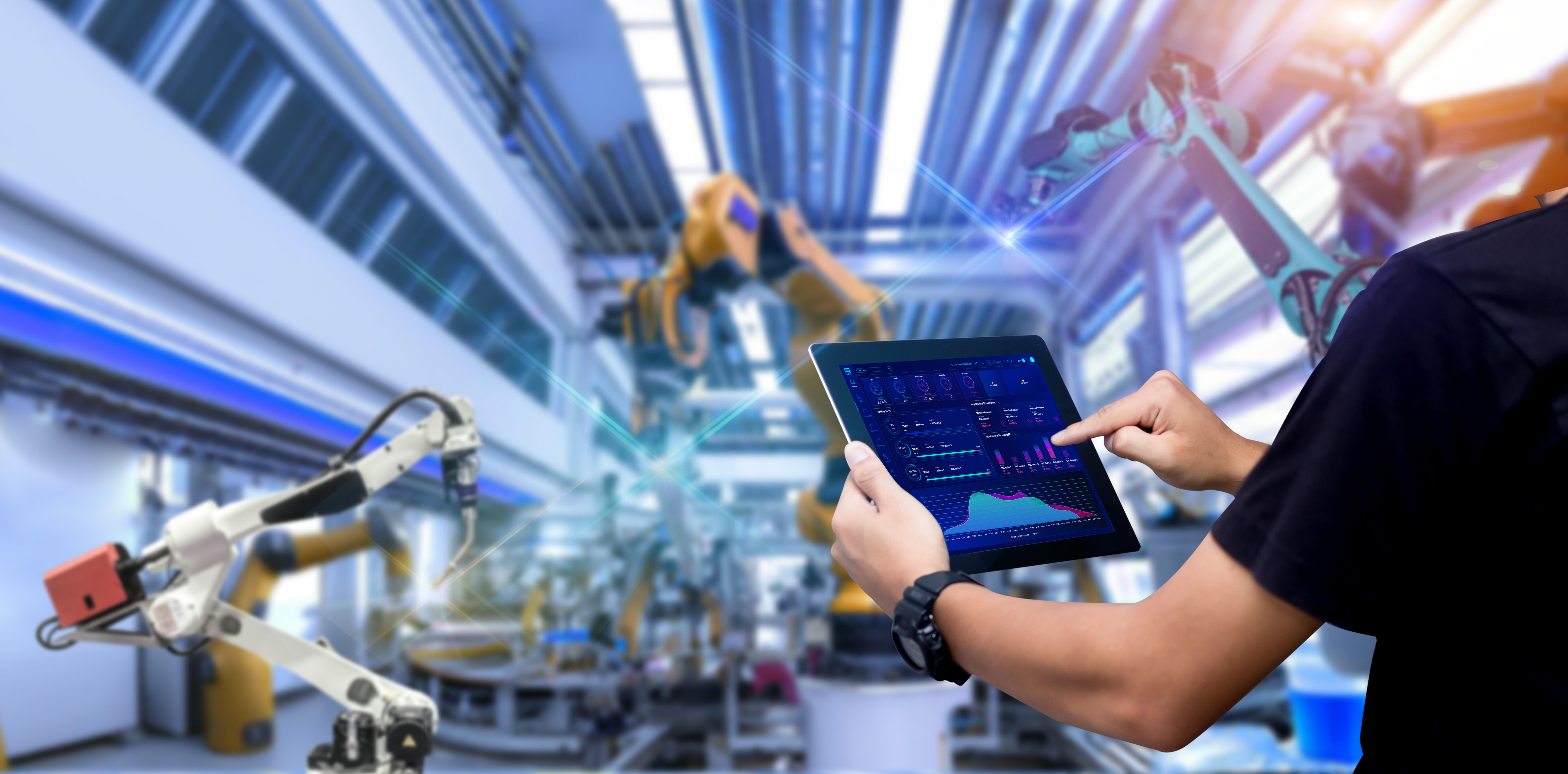
Imagine being able to not only plan your production processes, but optimise them in real time, reduce costs, minimise downtime, and increase productivity at the same time. Production Planning and Control systems (PPS) are the key to achieving exactly that – especially in the age of Industry 4.0. But how do you select the right system, integrate it seamlessly into existing structures, and utilise the most modern technologies to make your manufacturing future-proof? In this article, you'll learn how PPS as a central control instrument makes your production more flexible, sustainable, and efficient – and how the IIoT production monitoring platform Clouver from ProCom helps you to fully realise your potential.
Introduction to PPS: Fundamentals and Functions
Production Planning and Control systems (PPS) form the backbone of efficient manufacturing. They help you to organise and optimise the complex process from order acceptance to product completion in a structured manner. Essentially, a PPS functions as the central nervous system of your production: it captures, plans, and coordinates all production-relevant processes and resources.
A modern PPS typically includes the following core functions:
- Production planning: This is where manufacturing orders are created, material requirements determined, and capacities planned.
- Production control: This component monitors ongoing production, compares target and actual states, and promptly initiates measures when deviations occur.
- Operational data collection: Data such as machine running times, downtimes, or scrap rates are continuously collected – the basis for calculating Overall Equipment Effectiveness (OEE).
With advancing digitalisation, PPS is increasingly being linked with Industrial Internet of Things (IIoT) technologies. This integration enables the collection and analysis of real-time data, so you can immediately respond to production deviations.
Optimise Your Production with Clouver!
With Clouver, you get precise insights into performance, downtimes, and production volumes – in real time. Make your processes more efficient and save time and costs. Get started now and discover how Clouver can revolutionise your production!
PPS and Industry 4.0: The Role of Digitalisation
Digitalisation is revolutionising the way production processes are planned and controlled. Classical, often isolated PPS systems are giving way to dynamic, data-driven decision systems. Are you wondering how you can utilise this novel flexibility for your company?
Modern PPS solutions in the Industry 4.0 context are based on the continuous collection and transparent visualisation of real-time data. An important aspect here is the integration of heterogeneous machines – both the latest equipment and older devices can be incorporated into a unified monitoring system through IIoT platforms like Clouver. This enables cross-machine collection of production data, which helps you make informed and data-based decisions.
In addition to real-time data availability, digitalisation also promotes paperless order management, which makes all production data centrally and digitally available. This way, you can identify bottlenecks, respond early to disruptions, and optimally control the material flow.
Efficiency Increase Through PPS: Real-Time Data and Analyses
Modern PPS systems enable you to transform your production into a dynamic, self-optimising system. Through continuous collection and immediate evaluation of real-time data, production deviations are detected instantly – for example, when a system is operating below 80% of its capacity.
The advantages of real-time data analysis are diverse:
- Immediate detection of deviations: Based on defined thresholds, you receive automatic push notifications that allow you to intervene directly.
- Proactive action: Through predictive analyses, you can optimise early and avoid unplanned failures.
- Pattern recognition: Advanced data analysis reveals connections that would otherwise remain hidden.
With the IIoT platform Clouver, you can implement these advantages concretely: intuitive dashboards provide an overview of machine status, downtimes, and important metrics such as OEE at any time. The paperless order management ensures that all information is digitally and real-time available.
Integration of PPS into Existing Systems: Mastering Challenges
Implementing a PPS system into the existing infrastructure brings challenges – especially in mechanical engineering. One of the biggest hurdles is the heterogeneous machine landscape: old and new equipment, often poorly networked, make uniform data collection demanding.
Modern IIoT monitoring platforms like Clouver were specifically developed to overcome these hurdles. Through a modular structure and flexible hardware components, such as the Clouver SmartKit, even older machines can be gradually integrated into the digital network.
A careful inventory of all technical and organisational prerequisites, as well as a phased integration, are crucial. Change management and targeted training help to bring employees on board early and facilitate the handling of the new PPS system.
Get the Best Out of Your Production with Clouver!
Connect your machines and gain valuable insights into your production processes. Reduce unused capacity, optimise resource utilisation, and increase your revenue. Contact us today for a no-obligation consultation!
PPS as the Key to Production Optimisation: Practice-Oriented Solutions
Modern PPS systems form the backbone of successful manufacturing companies in the age of Industry 4.0 and 5.0. Once you implement a PPS system, numerous possibilities for efficiency improvement open up:
- Real-time transparency: With Clouver, you continuously receive current data on Overall Equipment Effectiveness (OEE), revealing previously unused potentials.
- Data-driven decision-making: Central metrics in an intuitive dashboard enable well-founded process optimisations.
- Reduction of downtimes: Through continuous monitoring, setup and throughput times are minimised.
The integration of RFID technologies facilitates the automatic identification of production processes and the precise counting of produced parts. Studies document measurable improvements: machine efficiency increases by an average of 10-15%, throughput times are shortened, and setup times significantly reduced.
In volatile markets with rapidly changing customer demands, a flexible PPS system offers decisive advantages – instead of investing in rigid complete solutions, you can select exactly the modules that correspond to your specific requirements.
Your Partner for Innovative Automation Solutions!
ProCom offers the perfect combination of intelligent software, premium hardware, and comprehensive support. Whether knife, laser, or waterjet cutting – we'll develop the ideal solution for your production needs. Arrange your consultation today and get started!
Conclusion
The integration of smart data sources into your manufacturing is a central step to realising efficient and precise production. It becomes apparent that PPS systems deliver far more than mere planning functions – they create transparency, promote data-driven decisions, and enable continuous optimisation of your production processes.
If you want to take the path to future-proof, digitalised manufacturing, it is essential to integrate a PPS system into your company and combine it with modern IIoT solutions like Clouver. This way, you reduce downtimes, improve equipment productivity, and create a basis for sustainable efficiency improvements.