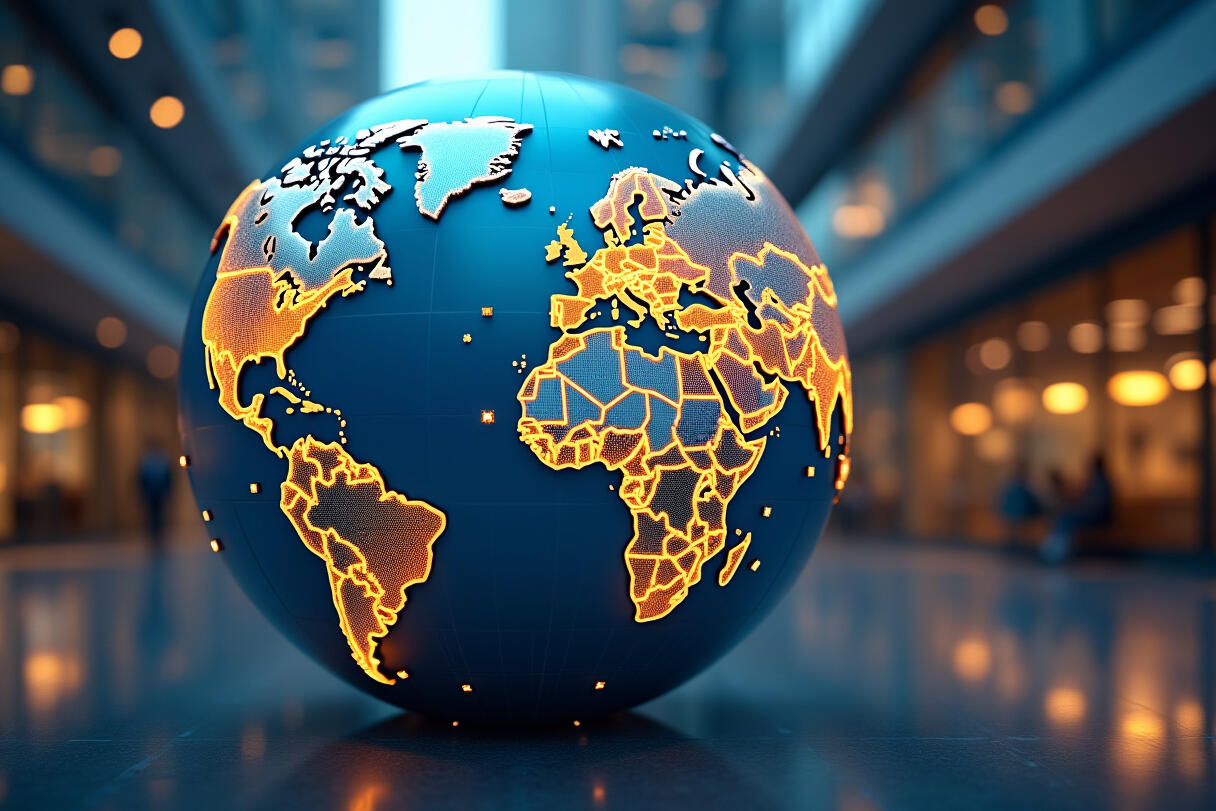
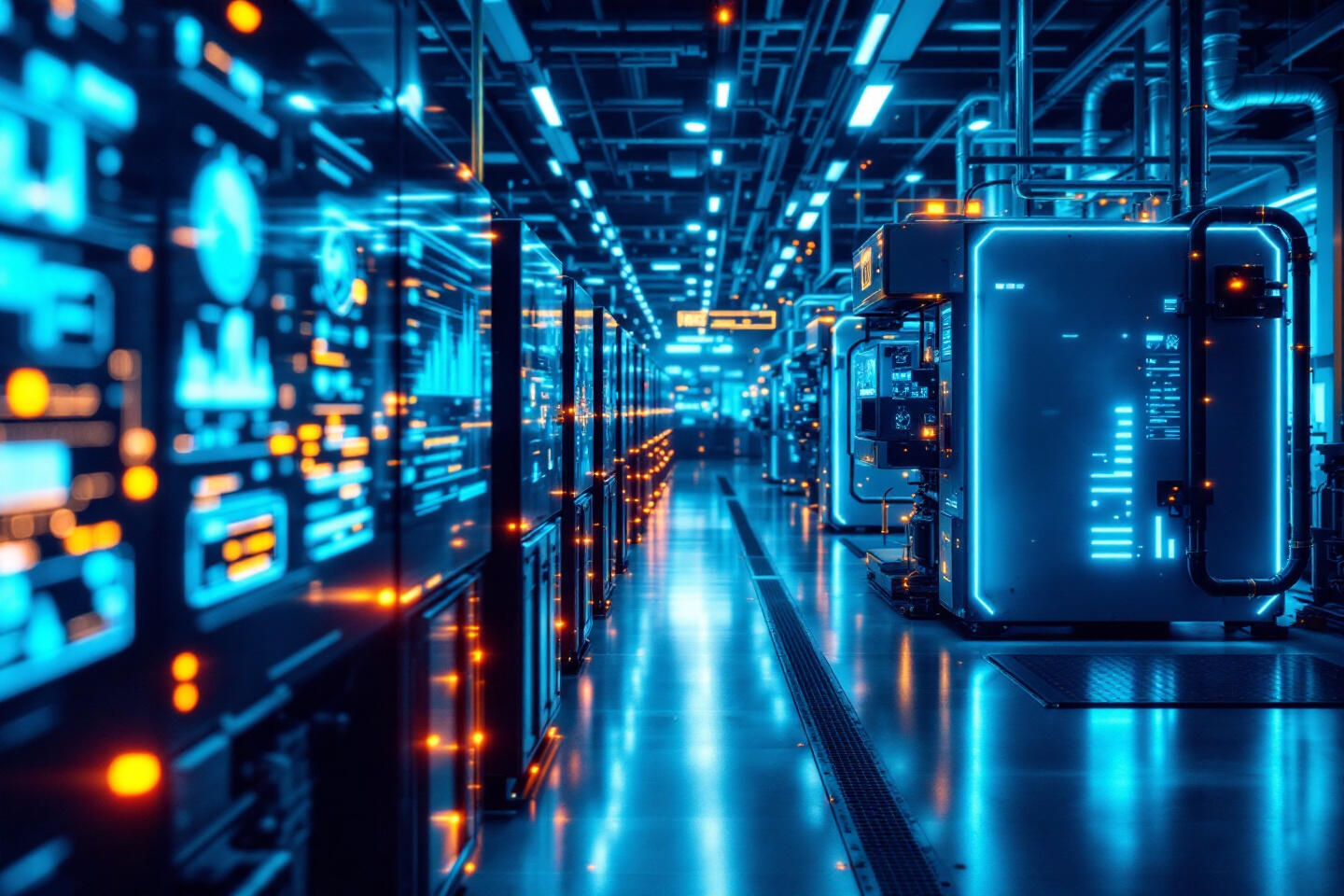
Are you familiar with this? You want to digitalise your production, but the challenges of a smart factory seem overwhelming? You're not alone: many production managers face the same situation. The good news: with the right strategy, you'll successfully master the transformation to a smart factory.
A smart factory intelligently connects people, machines and processes. The result? Higher efficiency, lower costs and better product quality. However, the path there isn't always simple. In this practical guide, you'll learn which smart factory challenges await you and - more importantly - how to overcome them.
These Technical Challenges You Need to Know
The integration of existing systems into your new smart factory environment is likely your biggest challenge. Often, companies use various machines and software solutions that cannot readily communicate with each other. Therefore, begin with a thorough inventory of your current systems. Use middleware solutions and APIs to build communication bridges between different systems. Pay particular attention to ensuring new technologies are compatible with your existing systems. Careful planning and gradual integration can help you minimise technical difficulties.
With increasing connectivity comes an increased risk of cyber attacks. In your smart factory, sensitive production data and trade secrets are exposed to potential threats. Therefore, implement a multi-layered security architecture that combines various security mechanisms. Firewalls, Intrusion Detection Systems (IDS) and encryption technologies form your foundation. Regular training of your employees in security protocols is just as important as continuous security checks and penetration tests.
How to Win Over Your Employees for the Transformation
Implementing a smart factory isn't just a technical challenge, but above all a human one. Employees may resist when they don't understand the benefits of new technologies or fear their jobs are at risk. Therefore, involve your employees early in the change process. Transparent communication and involving employees in decision-making processes can significantly increase acceptance.
Continuous training of your employees is key to success. Develop a training programme tailored to your employees' individual needs. Use various formats such as e-learning platforms and practical workshops. Partnerships with educational institutions and technology providers can help you offer customised training.
Set New Standards in Production with ProCom!
Our high-tech control solutions are designed to maximise efficiency and precision in your production. Stay competitive and future-proof with our support. Contact us today to learn more about our technologies and achieve your goals!
These Economic Aspects You Should Consider
Implementing a smart factory requires high initial investments. You must carefully weigh whether the expected benefits justify the costs. Create a detailed business case that shows the costs and expected benefits of your smart factory. Use financial models and scenario analyses to evaluate the economic viability of your project. Consider not just the direct savings, but also the long-term benefits such as increased flexibility, improved quality and faster response times.
Various government funding programmes can help you reduce the financial burden and accelerate implementation. Research funding programmes and grants specifically targeting Industry 4.0 and digitalisation. Creating funding applications may seem demanding but can pay off through substantial financial support.
These Future Trends Will Revolutionise Your Production
Artificial Intelligence and 5G technologies play a crucial role in the smart factory of the future. AI can help you optimise processes, recognise patterns and enable predictive maintenance. 5G provides the necessary bandwidth and reliability for real-time applications. Start with small, clearly defined AI projects to gain initial experience and increase acceptance. Implement AI solutions for specific use cases such as quality control or predictive maintenance. Use data analysis tools to gain valuable insights from your production data.
How to Successfully Start Your Smart Factory Future
A gradual implementation can minimise risks and increase acceptance. Through pilot projects, you can test new technologies in a controlled environment before expanding them to the entire production. Develop an implementation plan that defines clear milestones and success criteria. Start with small, manageable projects and expand these gradually. The insights from pilot projects help you continuously optimise your implementation strategy.
FAQ Section
What is a Smart Factory?
A smart factory is a highly automated, connected production environment that increases production efficiency and flexibility through the use of IoT, AI and cyber-physical systems.
What are the benefits of a Smart Factory?
The benefits include increased productivity, reduced downtime, improved quality, greater flexibility and the ability to quickly respond to market changes.
What are the typical challenges in implementing a Smart Factory?
The challenges include integrating new technologies, ensuring data security, change management and high initial investments.
How long does it take to implement a Smart Factory?
The duration varies depending on the size and complexity of the project but can take several years, particularly if a gradual implementation is preferred.
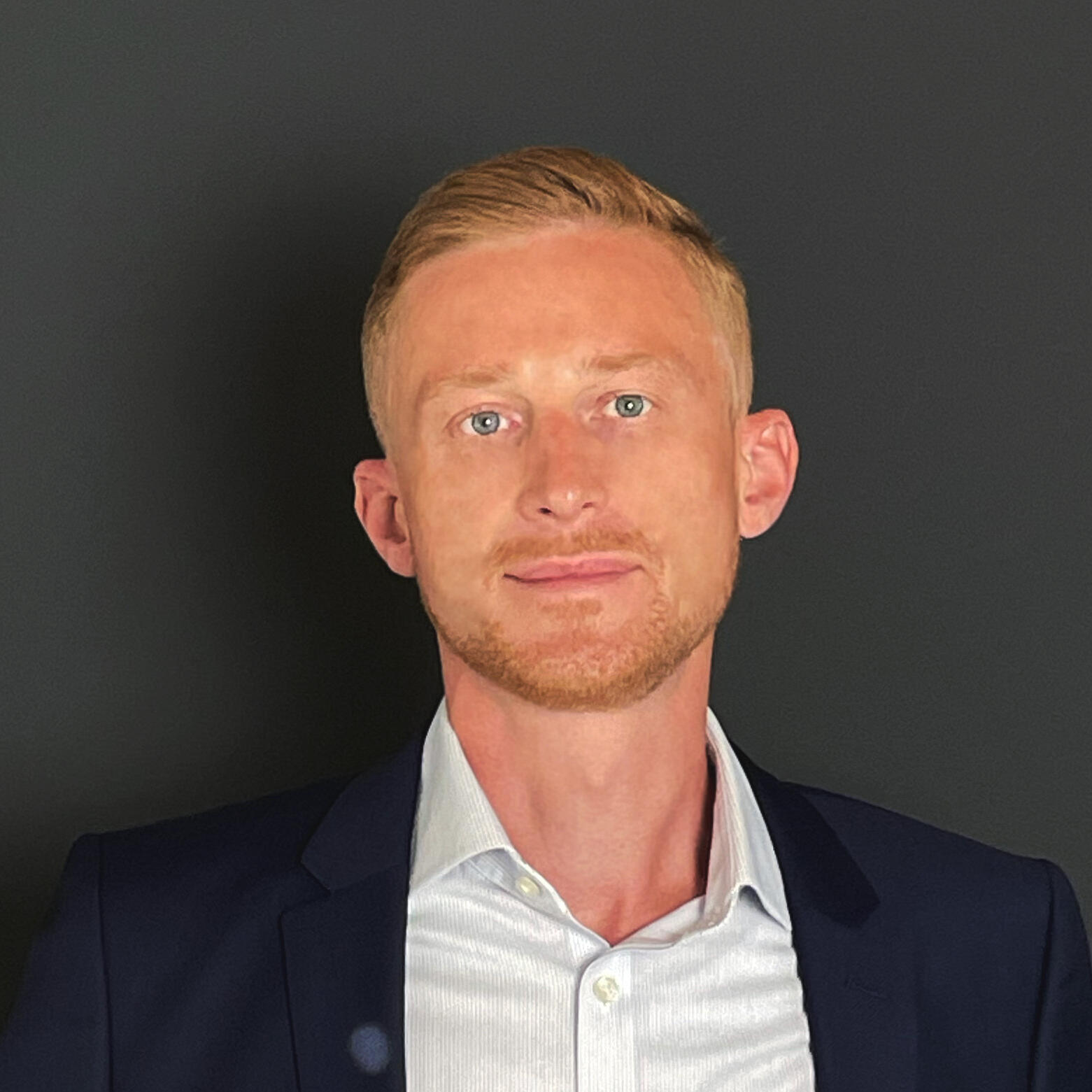
Dimitri Koneger
Sales Manager
Have questions about the topic or want to learn more about our solutions?
Contact us and discover how our products can future-proof your machines. Let’s work together to find out how we can help take your production to the next level!
- +49 241 93681-500
- contact@procom-automation.de
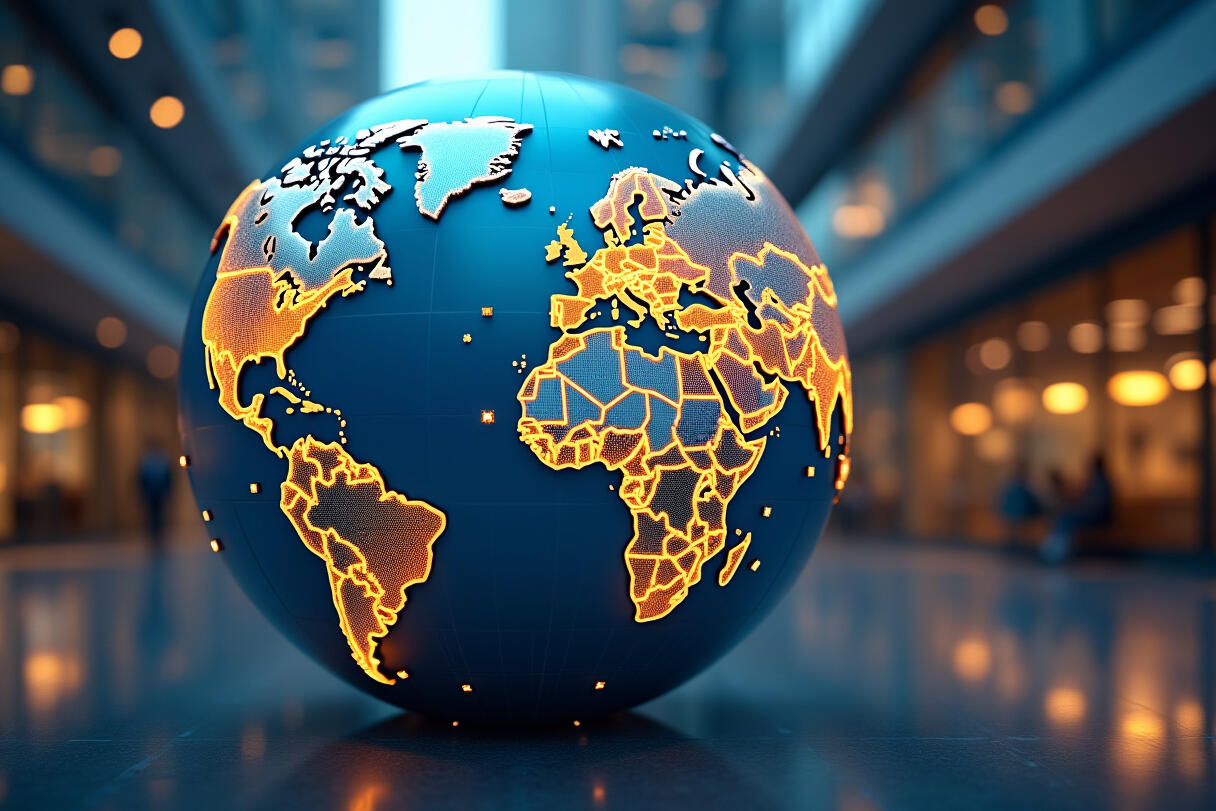
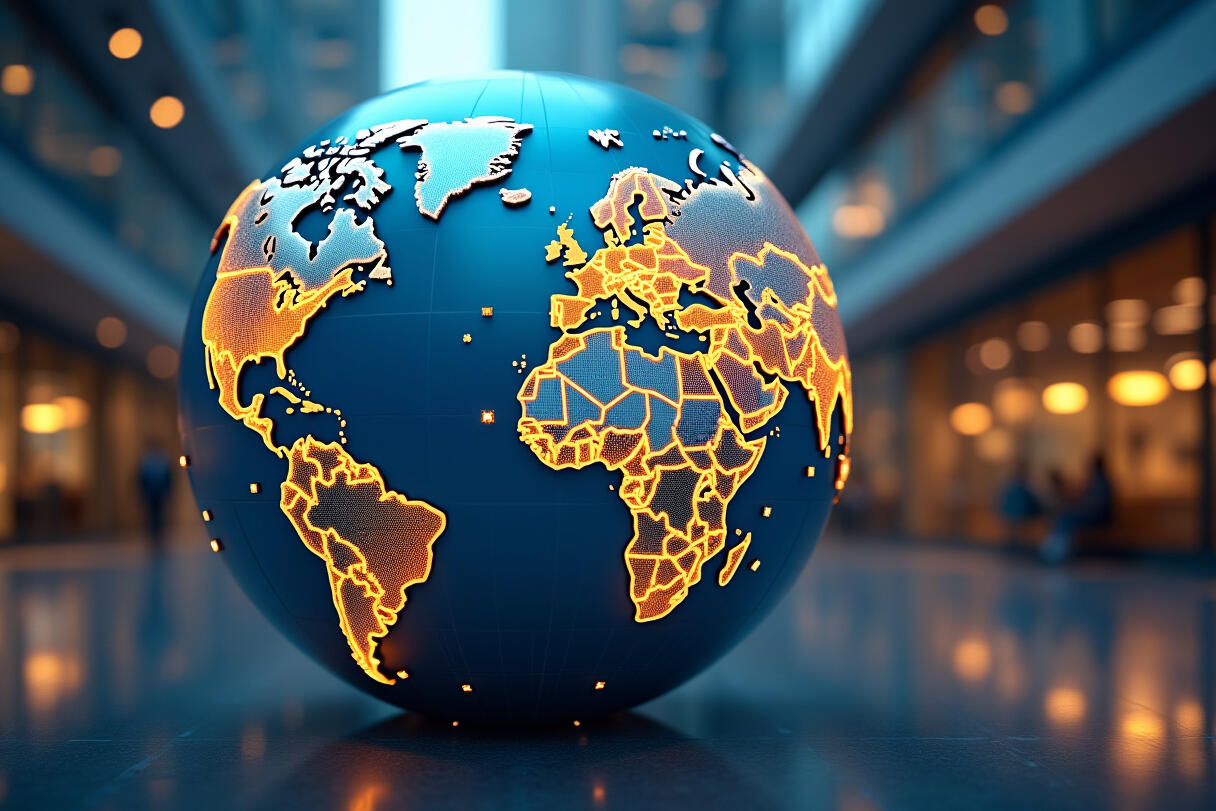