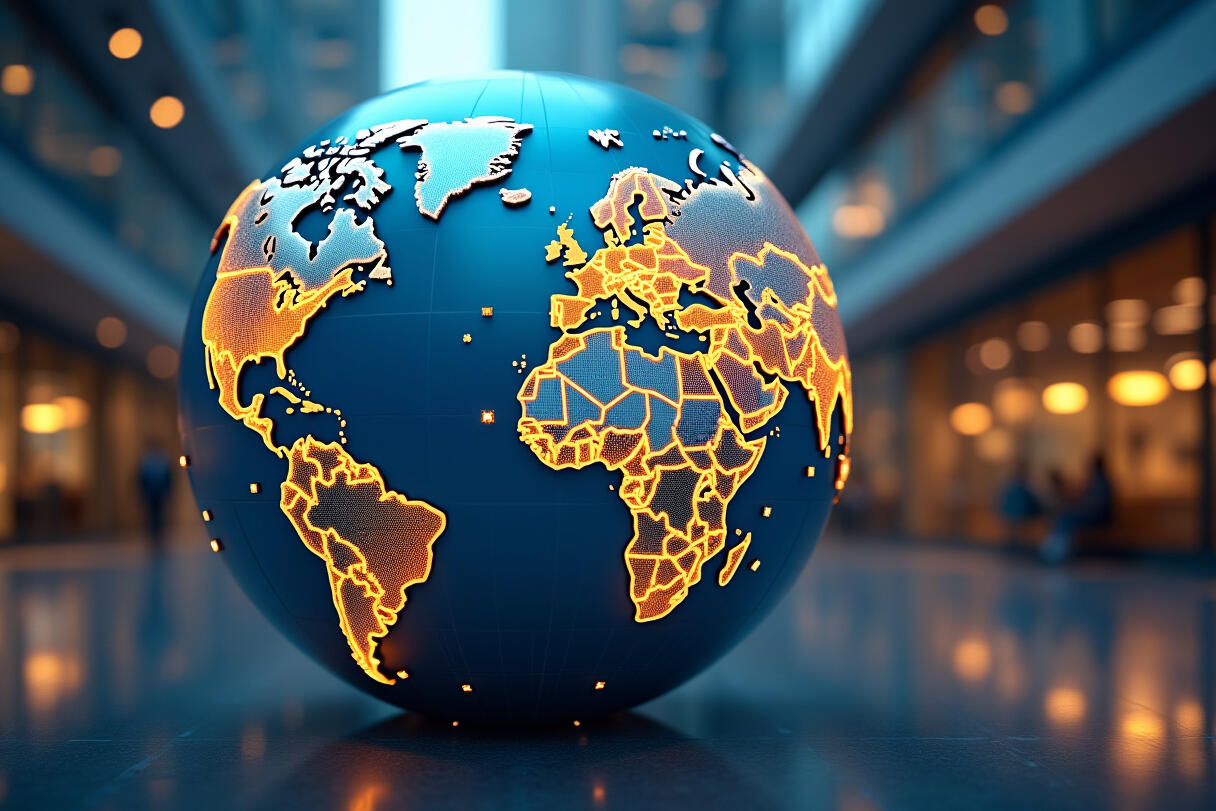
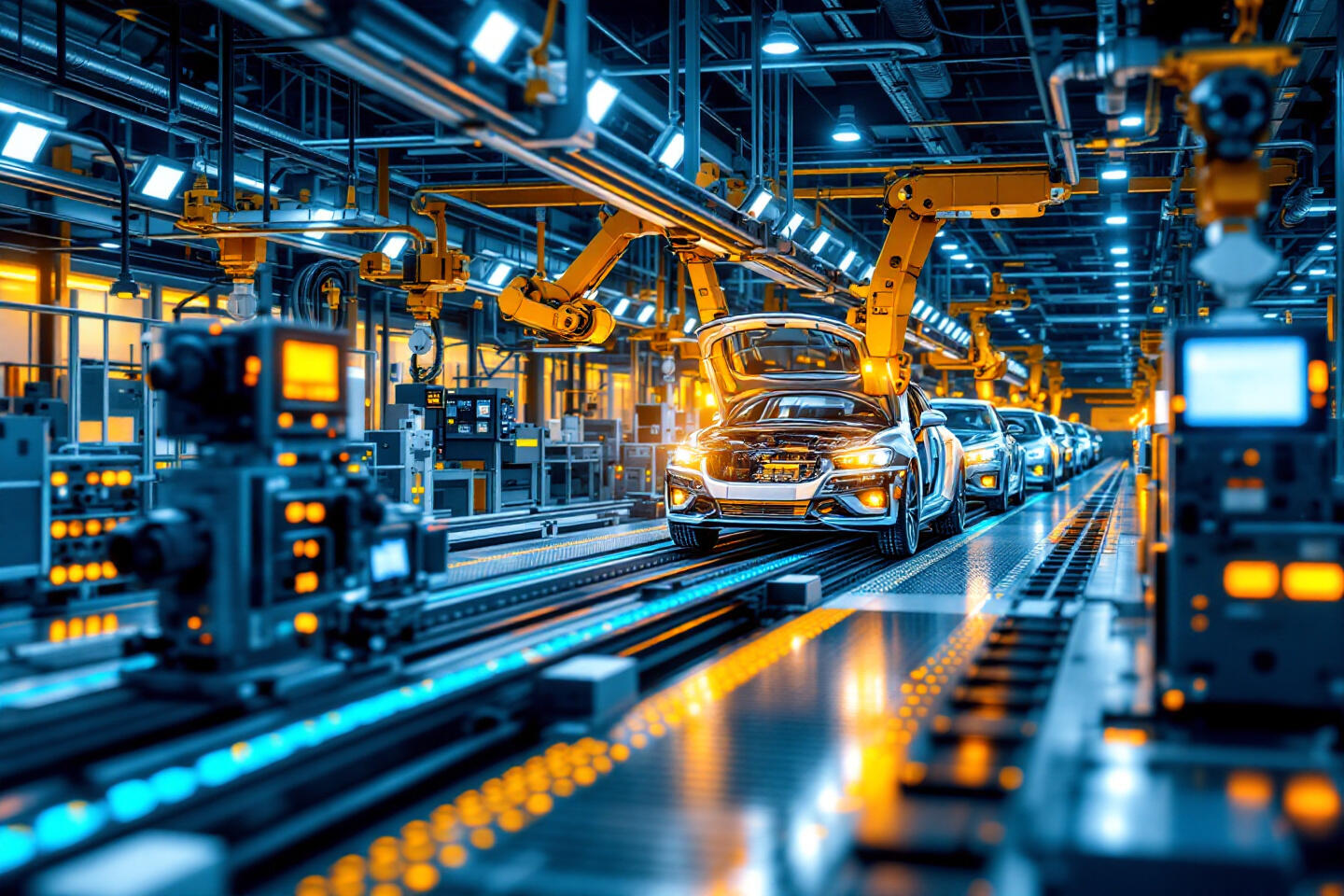
Industry 4.0, often referred to as the fourth industrial revolution, represents the intelligent networking of machines and processes using state-of-the-art information and communication technologies. But why is this topic so relevant, and what does it specifically mean for companies, employees, and society?
In this post, you will learn how Industry 4.0 makes production more flexible and efficient, which new business models and technologies play a role, and how the working world is changing. We illuminate the practical challenges in implementation, the opportunities for various sectors, and the global impacts of this revolutionary development.
By reading this post, you will not only gain a deep understanding of the fundamentals and possibilities of Industry 4.0 but also receive valuable insights into concrete application examples, security aspects, and future perspectives. Whether you are an entrepreneur, employee, or simply interested in technology – this post helps you better understand and actively shape the transformation towards networked and digital industry. Dive into the world of Industry 4.0 and discover how this revolution can change your everyday life!
Introduction to Industry 4.0
Definition and Significance
Industry 4.0 refers to the intelligent networking of machines and processes through modern information and communication technologies. The goal is flexible and efficient production that can quickly adapt to changing conditions. This means that machines are not only automated but also networked and capable of communication to adapt in real-time to dynamic production requirements.
Historical Context
The fourth industrial revolution follows the mechanical revolution (Industry 1.0), which was characterised by the introduction of steam engines, the electrical revolution (Industry 2.0), defined by electrification and mass production, and the digital revolution (Industry 3.0), characterised by the use of electronics and IT for production process automation. Industry 4.0 extends this automation through comprehensive digitalisation and networking of production, leading to a new quality of production flexibility and efficiency.
Goals and Key Concepts
Industry 4.0 aims to increase efficiency, flexibility, and individualisation of production. Key concepts include Cyber-Physical Systems (CPS), which connect the physical world with the digital world, the Internet of Things (IoT), which enables communication between machines and devices, Artificial Intelligence (AI), which is used to optimise processes, and Big Data, which is used to analyse large amounts of data to make informed decisions and control production in real-time.
Technological Foundations of Industry 4.0
Cyber-Physical Systems (CPS)
These systems connect physical and digital processes. An example is the networking of machines via sensors with a central control system that collects and analyses data in real-time to make immediate adjustments in production. This enables self-organising production that responds to current conditions and requirements.
Internet of Things (IoT)
IoT enables communication between machines and devices. This includes sensors that collect data and transmit it to central systems, which analyse and use this data to optimise production processes. For example, IoT sensors in a production line can monitor the condition of machines and report maintenance needs early to minimise downtime.
Cloud Computing and Edge Computing
Cloud Computing offers the possibility to store and process large amounts of data, which is particularly useful for analysing production data. Edge Computing, on the other hand, enables data processing directly at the point of data collection, which is necessary for applications that require low latency, such as real-time monitoring and control of production processes.
Artificial Intelligence and Machine Learning
These technologies are used to optimise production processes by collecting, analysing, and using historical production data to create prediction models. A machine learning algorithm can, for example, detect anomalies in production processes and provide recommendations for action to increase efficiency and avoid errors.
Digital Twin Technology
A Digital Twin is a virtual model of a physical object or system that monitors its state and performance in real-time. This enables precise simulation and analysis, improving machine maintenance and optimisation. Through continuous data streams from sensors, the digital twin can monitor the condition of the physical machine and recommend predictive maintenance measures.
Key Features and Possibilities of Industry 4.0
Flexible Production
Through networking and coordination between different actors in the production chain, the use of machines and resources can be optimised. This enables flexible adaptation of production to changing demand and individual customer requirements.
Adaptable Factory
Modular production lines enable production processes to be quickly and cost-efficiently adapted to new products or customer requirements. This leads to higher productivity and better utilisation of production capacities.
Customer-Oriented Solutions
The direct connection between consumers and producers enables the personalisation of products and the use of smart products that send data about their usage back to manufacturers. This promotes the development of tailored solutions and improves customer satisfaction.
Practical Implementation of Industry 4.0
Introduction
A step-by-step implementation of Industry 4.0 technologies helps minimise risks and maximise success. This includes creating an implementation plan, defining pilot projects, and scaling successful projects to larger production areas.
Successful Case Studies
Analysis of successful case studies from one's own industry can provide valuable insights into proven methods and strategies for implementing Industry 4.0. Both technological and organisational aspects should be considered.
Benefit from over 40 years of expertise in control solutions for textile cutting!
Get in touch with our experts today and discover the perfect solution for your production needs.
Optimised Logistics and Material Flow
Algorithm-Based Route Calculation
Through the networking of logistics systems and the use of algorithms for route optimisation, supply chains can be designed more efficiently. Machines can automatically report material requirements, enabling seamless and efficient logistics.
Data Management and Usage
Analysis of Production and Product Data
Data analyses play a central role in Industry 4.0. By combining and analysing production and product data, companies can design their production processes more efficiently and develop new business models such as Predictive Maintenance, which are based on predicting maintenance requirements.
Resource-Efficient Circular Economy
Product Lifecycle Management
By using data throughout the entire lifecycle of a product, companies can optimise material usage and promote recycling. This leads to a resource-efficient circular economy that is both ecologically and economically advantageous.
Impact on the Working World
New Job Profiles and Qualification Requirements
The introduction of Industry 4.0 technologies requires new qualifications and job profiles. Employees must be trained in new technologies and digital tools to meet the new requirements of digitalised production.
Human-Machine Collaboration
Collaboration between humans and machines is intensified through Industry 4.0. Ergonomic workplace design and safety protocols are crucial to ensure effective and safe human-machine collaboration.
International Perspectives and Cooperation
Comparison of National Strategies
The global networking of production requires international cooperation and standards. A comparison of national strategies can help maintain competitiveness and learn from best practices of other countries.
Security Aspects and Data Protection
Cybersecurity
Comprehensive security measures are necessary to protect the networked systems in Industry 4.0. These include both technical solutions and organisational measures to prevent cyber attacks and protect data.
Data Protection and GDPR
The protection of personal data is a central aspect of Industry 4.0. Companies must ensure that all data processing procedures are GDPR-compliant and that user privacy is maintained.
Future Perspectives and Emerging Technologies
New Technologies
Continuous observation and evaluation of new technologies such as 5G and Quantum Computing is crucial to recognise and utilise their potential for Industry 4.0. These technologies can enable further improvements in production and communication efficiency.
Sustainability
Sustainable production methods are becoming increasingly important to conserve resources and reduce costs. Companies should implement sustainable technologies and processes to operate successfully and environmentally consciously in the long term.
Concrete Application Examples
Smart Factory Concepts
Developing a Smart Factory roadmap is an important step towards digitalising production. This includes implementing IoT solutions, using AI for process optimisation, and developing digital twins for monitoring and controlling production facilities.
Predictive Maintenance
Predictive Maintenance uses data analyses to predict machine maintenance requirements and thus minimise downtime. This improves the availability and lifespan of production facilities and reduces maintenance costs.
Economic Aspects and Investments
Investment Costs and Funding Opportunities
The implementation of Industry 4.0 technologies requires significant investment. Government funding programmes can help reduce the financial burden and accelerate implementation.
New Business Models
The digitalisation of production opens up new business models and revenue streams. Companies can develop new services and products tailored to their customers' needs through the analysis of production and usage data.
Legal Framework
Legal Requirements
The use of autonomous and networked systems in production raises new legal questions. Companies must carefully examine legal requirements and liability issues and ensure that their systems comply with legal requirements.
Measurement and Success Control
KPIs for Industry 4.0 Projects
To measure the success of Industry 4.0 projects, companies should define and regularly monitor specific KPIs. These KPIs can relate to efficiency improvements, reduction of downtime, or customer satisfaction and help ensure continuous improvements.
Conclusion
Industry 4.0 is revolutionising the way companies produce and optimise their processes. Through the integration of cutting-edge technologies such as the Internet of Things (IoT), artificial intelligence (AI), and Big Data, Industry 4.0 enables not only higher efficiency but also greater flexibility and adaptability in production. This transformation leads to intelligent factories where machines and systems autonomously communicate and collaborate to optimise the production process.
If you would like to learn more about the exciting world of Industry 4.0, we invite you to explore our further articles and resources on this topic. If you have questions feel free to contact us! Click here to dive deeper into the technologies and applications of Industry 4.0 and learn how your company can benefit from this revolution.
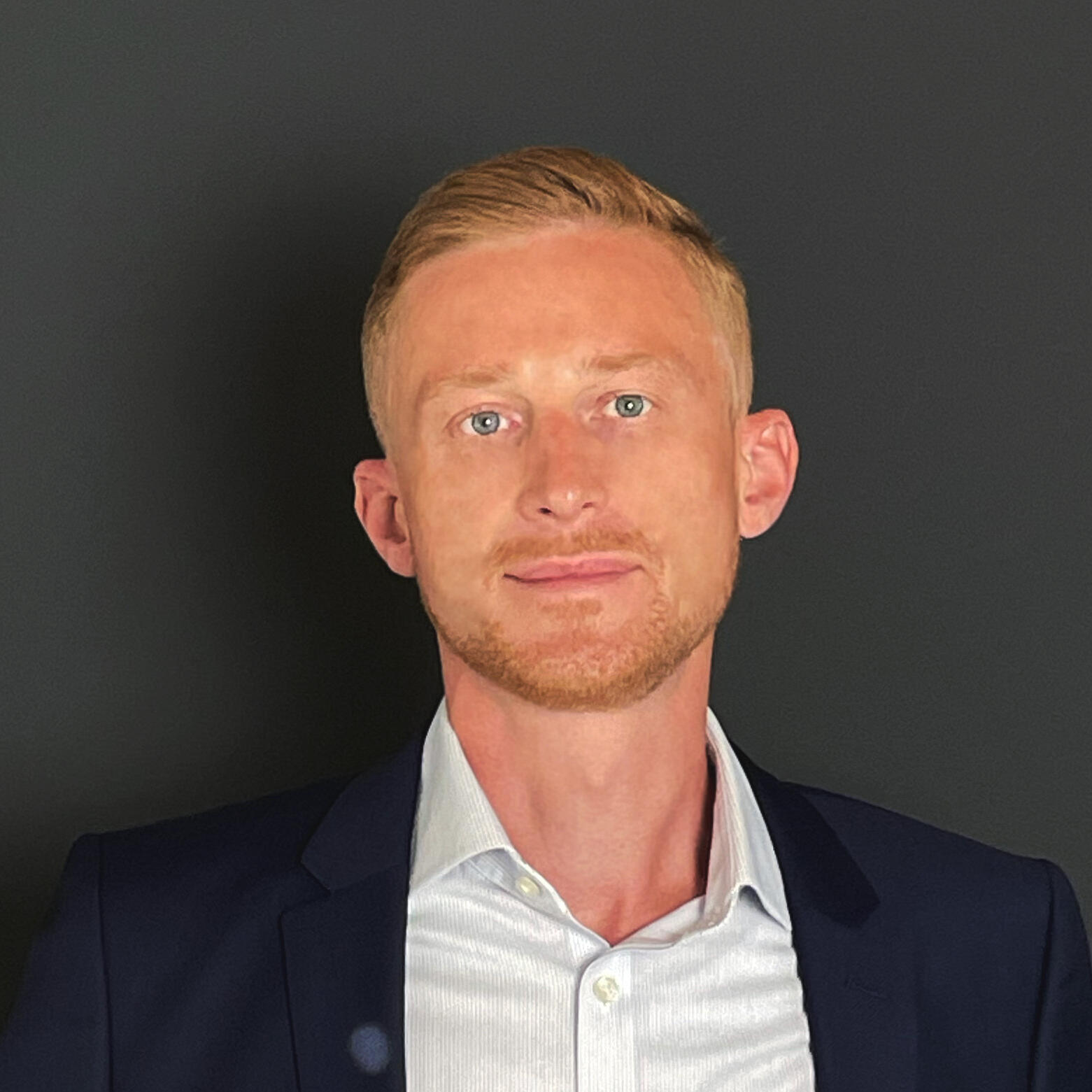
Dimitri Koneger
Sales Manager
Have questions about the topic or want to learn more about our solutions?
Contact us and discover how our products can future-proof your machines. Let’s work together to find out how we can help take your production to the next level!
- +49 241 93681-500
- contact@procom-automation.de
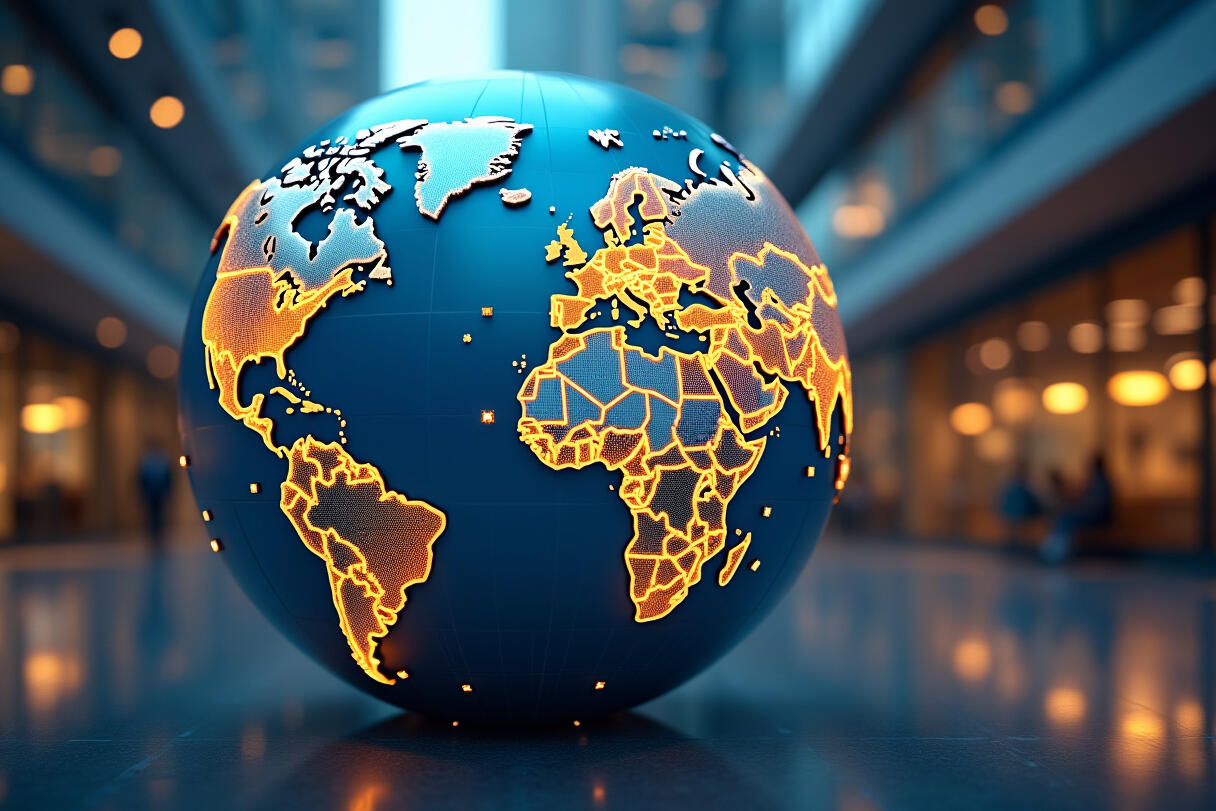
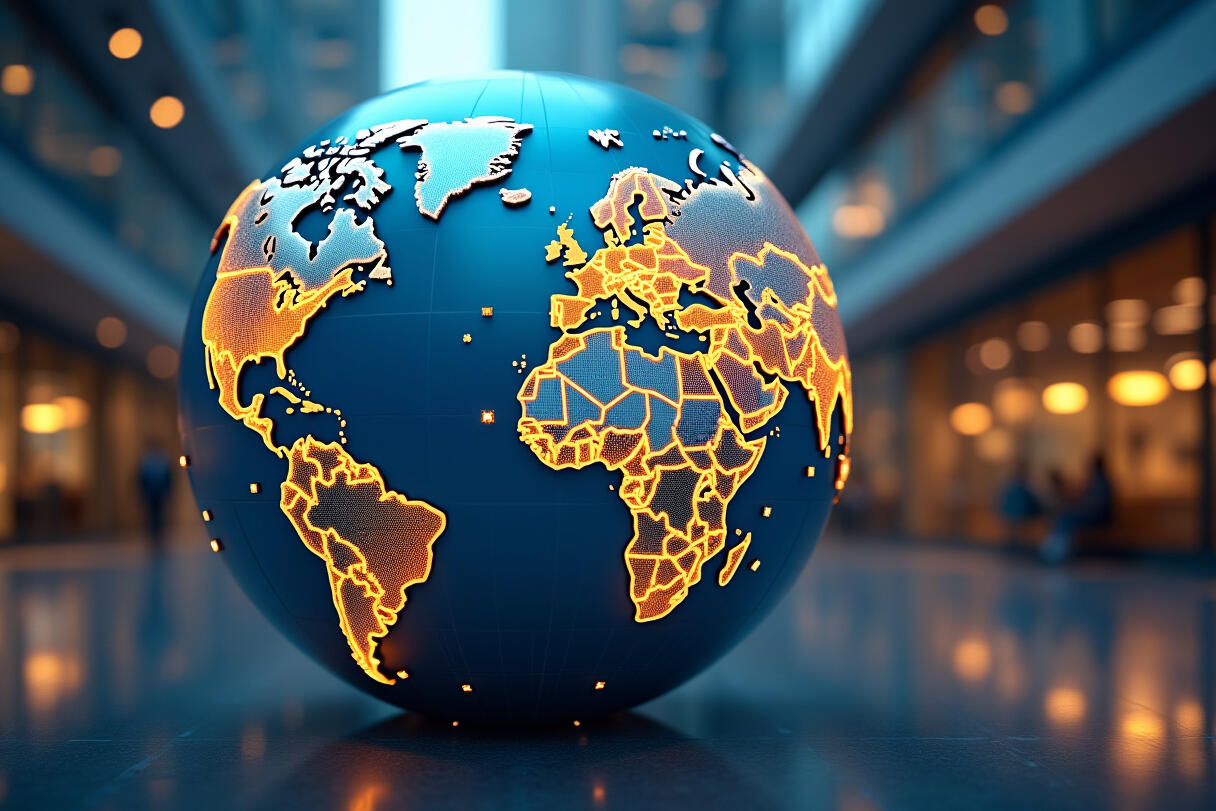