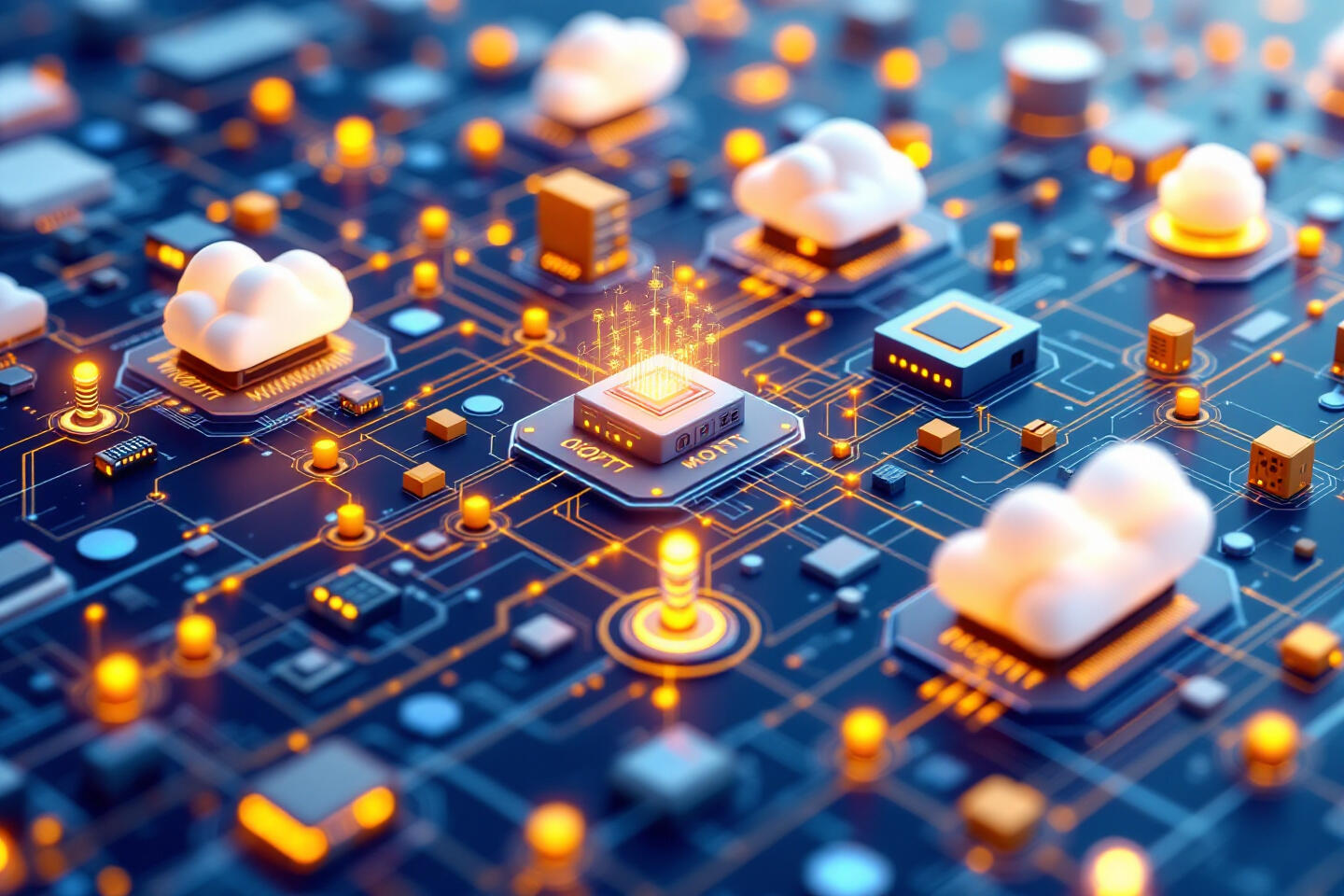
What is the Industrial Internet of Things (IIoT)?
Definition: The Industrial Internet of Things (IIoT) describes the networking of machines, sensors and IT systems in industry with the aim of improving processes based on data and increasing productivity.
The IIoT defines itself as a comprehensive system of interconnected smart objects, cyber-physical assets and associated information technologies. As Boyes et al. aptly describe it, IIoT enables “real-time access, intelligent capture, analysis and exchange of process information within industrial environments, with the aim of making the entire production value more efficient.”
IIoT goes far beyond a simple transfer of the IoT concept into an industrial context. It includes not only self-regulating production logic but also the generation of additional information for all key stakeholders. IIoT platforms such as Clouver serve as central middleware, linking existing industrial assets, enterprise software, cloud solutions, and external services.
Your benefits include:
Connected middleware function: Platforms like Clouver enable seamless data exchange between various machines and systems.
Integration of legacy machines: Even older machines can be retrofitted with sensors and integrated into modern IIoT networks.
Real-time monitoring: Dashboards allow you to maintain full visibility of your production processes at all times.
Data-driven process optimisation: Systematic machine data collection helps identify bottlenecks and reduce downtime.
Keep track of all processes in your production – from machine status to production data.
Advantages of IIoT in Industrial Manufacturing
The Industrial Internet of Things (IIoT) offers manufacturing companies a multitude of critical advantages that go far beyond mere efficiency improvements. This technology has become a fundamental component of Industry 4.0 and is revolutionising the way companies design and adapt their production processes.
Significant efficiency gains and productivity increase
IIoT enables more precise monitoring and control of production processes through continuous data collection and analysis. By networking machines and systems, manufacturing companies can increase their Overall Equipment Effectiveness (OEE) by 10–15%. Real-time monitoring of metrics such as availability, performance, and quality allows bottlenecks to be identified early and workflows to be continuously improved.
Cost reduction through predictive maintenance
One of the most valuable IIoT applications is predictive maintenance. Unplanned downtime costs the industrial sector an estimated $50 billion annually. IIoT systems can predict potential failures through continuous monitoring of machine data and reduce maintenance costs by up to 50%. Predictive maintenance typically reduces machine downtime by 30–50% and extends equipment life by 20–40%.
Increased flexibility and adaptability
IIoT solutions enable companies to adapt their production to changing market demands. Smart connectivity allows production lines to be reconfigured quickly and new product variants introduced without major conversion times. This flexibility is particularly important as customers increasingly expect customised products and fast delivery times.
Improved safety and occupational protection
IIoT contributes significantly to improved workplace safety. Sensors continuously monitor operating parameters and environmental conditions to ensure production processes stay within safe limits. Proactive monitoring detects and prevents accidents and safety risks early. IIoT systems can also monitor human-machine interaction and issue immediate warnings in dangerous situations.
Sustainable resource optimisation
IIoT platforms create transparency in energy consumption and enable targeted optimisation of resource use. Continuous monitoring of energy data allows companies to identify consumption peaks and realise savings. This not only reduces costs but also supports sustainability goals and CO₂ reporting obligations.
Increased competitiveness through data-driven decisions
IIoT enables companies to make well-founded, data-driven decisions in real time. Systematic data collection and analysis create new business models and open up opportunities for innovative services. By integrating IIoT technologies, companies can sustainably strengthen their competitive position and prepare for the future.
Quality improvement and error reduction
By continuously monitoring production processes, quality issues can be detected and corrected early. IIoT sensors capture critical process parameters and make it possible to immediately identify deviations before defective products are produced. This significantly reduces scrap rates and increases product quality.
Implementing IIoT technologies thus represents a strategic competitive advantage that helps companies future-proof and streamline their process chains.
Real-Time Monitoring & Data Analysis for Production Processes
Wondering how to monitor your production status in real time? Thanks to modern IIoT solutions, this is no longer just a vision—it’s reality. Real-time monitoring enables you to capture critical operating parameters directly and respond immediately to deviations.
Modern platforms like Clouver connect operational technology (OT) with information technology (IT). These systems continuously collect data from all machines and present it via intuitive dashboards. This gives you constant oversight of metrics such as Overall Equipment Effectiveness (OEE). Useful features include:
Immediate responsiveness: Push notifications alert relevant staff to critical events.
Intelligent OEE analysis: Digital dashboards visualise availability, performance and quality of your assets in real time.
Advanced analytics: Time series data forms the basis for advanced analyses that reveal trends and anomalies.
- Heterogeneous machine integration: Even older machines can be integrated into your IIoT network using special SmartKit solutions.
Integrating Legacy Machines into IIoT: Successful Retrofit
Many companies face the challenge that not all machines have modernised interfaces. Yet integrating these legacy machines into modern IIoT networks offers enormous potential. You can continue using existing equipment while benefiting from digital transformation.
Typical challenges when integrating older machines include:
Lack of connectivity: Older machines often lack digital interfaces.
Heterogeneous control systems: Different manufacturers and control protocols complicate data exchange.
Data extraction: Capturing machine data is often technically demanding.
This is where retrofit solutions come in. With the Clouver SmartKit, old machines can be retrofitted with sensors and connectivity modules. This step-by-step integration protects your existing equipment investment while laying the foundation for continuous efficiency improvement in your production processes.
Connect your machines and gain valuable insights into your production processes. Reduce unused capacity, improve resource utilisation, and increase your revenue.
Paperless Production Management with IIoT Technology
Paper-based processes are a thing of the past. Traditional manual documentation processes lead to delays, errors, and unnecessary costs. With a digital, paperless solution, you have all essential order data at your fingertips, significantly improving your production flow.
With IIoT solutions like Clouver Paperless, you not only optimise your information flow but also achieve measurable efficiency gains:
Real-time capture of downtimes: Disruptions are automatically recorded and categorised.
Digital documentation: Precise analyses help reduce downtimes.
Automated work instructions: Digital approval processes shorten setup times and minimise errors.
Access to real-time data: All relevant information is immediately available to authorised employees.
The advantages of this paperless method are clear: up to 25% reduction in setup times, 30–50% shorter response times in case of disruptions, and significant savings on printing and archiving costs. In addition, IIoT devices help make all processes more efficient and individually adaptable.
Process Optimisation through Intelligent IIoT Data
Modern production environments generate vast amounts of data every day. Data-driven optimisation of industrial processes is at the heart of digital manufacturing in the IIoT era. This process is based on several key aspects:
Real-time data acquisition: All relevant process parameters are continuously captured.
Data processing: Raw data is transformed into meaningful performance indicators.
Visualisation: Intuitive dashboards give you a complete overview at all times.
Action implementation: Concrete improvements are identified based on data analysis.
In practice, this data-based approach leads to significant improvements: equipment availability increases, OEE improves by 10–15%, and continuous analyses help realise resource savings. Increasingly, artificial intelligence methods are being used to detect patterns and streamline workflows.
To implement this improvement sustainably, it is advisable to proceed step by step: start by identifying critical process KPIs and gradually expand your data infrastructure—based on a flexible, modular IIoT platform such as Clouver, which supports various protocols.
Conclusion & Recommendations
The integration of IIoT platforms into industrial applications opens up completely new possibilities for data-driven process optimisation. With IIoT, you gain not only real-time access to production data but also the ability to easily integrate legacy machines into a unified monitoring system and implement paperless processes.
Data-driven optimisation, combined with a modular platform like Clouver, enables you to continuously discover new potential and gradually increase your level of digitalisation. Take advantage of this technology to make your production processes future-proof and more competitive.