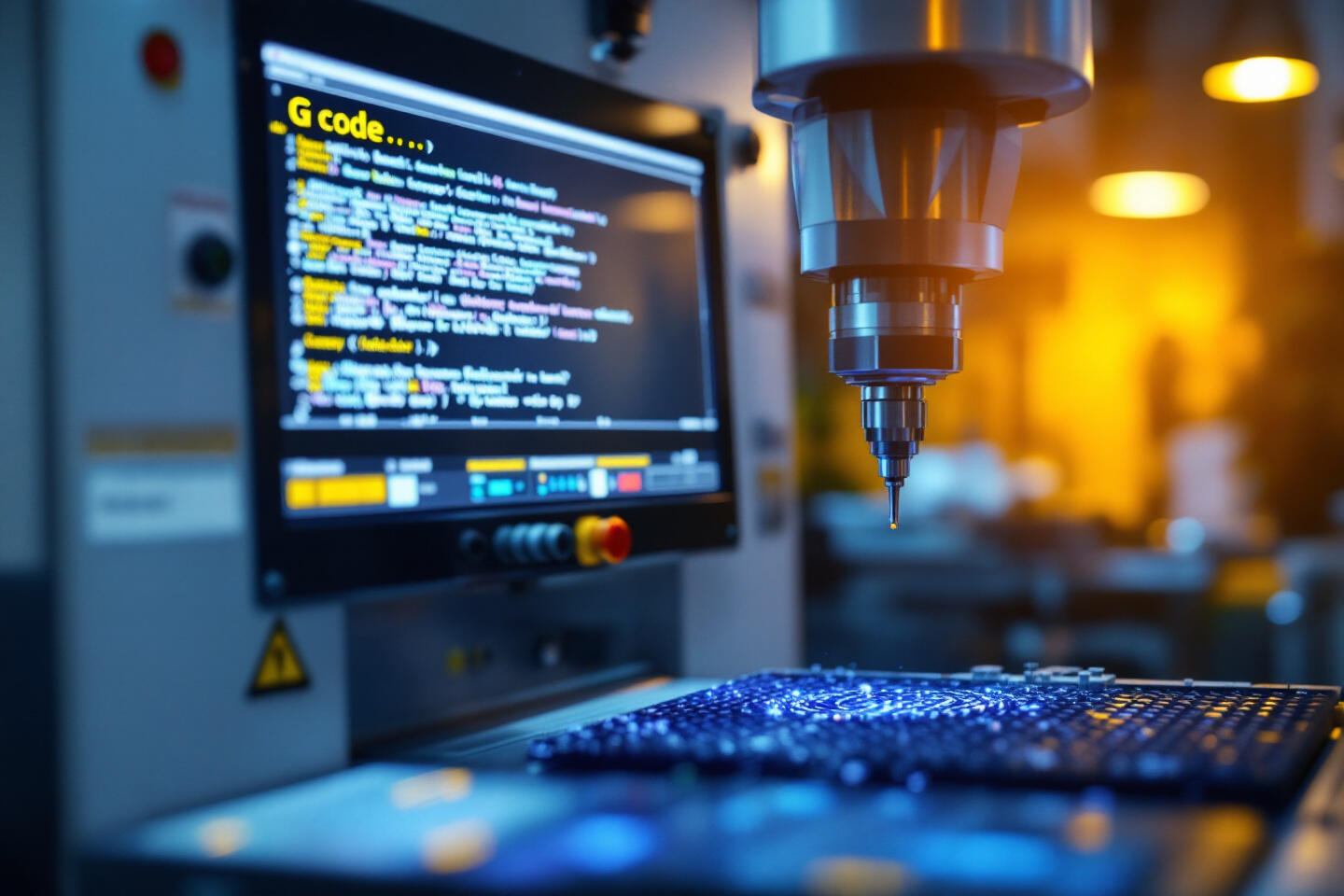
Imagine being able to not only measure the reliability of your equipment, but actively improve it – and all with a single metric: MTBF. Mean Time Between Failures (MTBF) is more than just a mathematical value; it's the key to more stable processes, reduced downtime, and higher efficiency. Unplanned failures cost not only time, they also affect your delivery capability and cause high consequential costs. In this article, you'll learn what MTBF specifically means, how to calculate and optimise it – and how modern Industrial Internet of Things (IIoT) solutions like Clouver can help you do this.
Definition and Significance of Mean Time Between Failures (MTBF)
Mean Time Between Failures (MTBF) is a central metric for measuring the reliability of your production equipment. It describes the average time span between two consecutive disruptions of a system. A high MTBF signals stable equipment with rare failures. Complementing this, Mean Time To Repair (MTTR) measures the average repair time. Together, both metrics give you a comprehensive overview of your equipment's operational capability and are essential for Overall Equipment Effectiveness (OEE) management.
The calculation of MTBF is simple: MTBF = Total operating time / Number of failures
An example: A production line with 20,000 operating minutes and 25 disruptions in a month has an MTBF of 800 minutes or 13.3 hours. This information helps you identify weaknesses, evaluate maintenance measures, and make informed decisions regarding replacement investments.
However, precise recording of MTBF is often a challenge: Manual records are frequently inaccurate, and the definition of "disruptions" varies between departments. This is where modern IIoT solutions come in, automatically collecting machine data in real time.
Get the Best Out of Your Production with Clouver!
Connect your machines and gain valuable insights into your production processes. Reduce unused capacity, optimise resource utilisation, and increase your revenue. Contact us today for a no-obligation consultation!
MTBF and Its Role in Optimising Industrial Processes
MTBF is much more than a metric – it's a strategic instrument for improving equipment efficiency. In production environments, where every unplanned failure causes significant costs, MTBF provides you with valuable indications of problem areas. Through continuous monitoring, you can recognise whether certain shifts, production batches, or operator practices systematically lead to disruptions.
Targeted MTBF management allows you to identify bottlenecks early and initiate proactive measures. In combination with other metrics, you gain a comprehensive insight into the condition of your equipment, optimise maintenance strategies, and extend the lifespan of your facilities.
How Real-Time Data Analysis Improves MTBF
Are you wondering how to optimise MTBF more effectively? The answer lies in real-time data analysis. Modern IIoT platforms like Clouver automatically capture all relevant operational data of your equipment and give you insights into hidden patterns that are often missed with manual recording.
The advantages of real-time data analysis for MTBF optimisation:
- Identification of hidden disruption patterns: Through continuous data collection, you recognise whether certain times of day or shift changes lead to increased failures.
- Immediate response to deviations: Automatic exception reports warn you when critical threshold values are exceeded.
- Data-based optimisation of maintenance cycles: Precise analyses help you determine optimal maintenance intervals instead of following rigid schedules.
- Long-term trend analyses: The archiving of historical data enables informed decisions for future maintenance strategies.
With Clouver, you receive not only a real-time dashboard but also detailed analyses that enable you to transition from reactive to proactive maintenance – without cumbersome manual data collection.
Predictive Maintenance: The Key to MTBF Optimisation
Targeted optimisation of MTBF requires a shift from reactive to proactive maintenance. Predictive maintenance aims to prevent failures before they occur by intelligently using the data gathered. Unlike preventive maintenance with fixed replacement intervals, predictive maintenance is oriented to the actual condition of your equipment.
Central elements of predictive maintenance for increasing MTBF:
- Continuous condition monitoring: Modern sensors record important parameters in real time, such as temperature, vibration, and running times.
- Data pattern analysis: Structured evaluation of operational data enables early detection of anomalies.
- Trend-based maintenance planning: Components are replaced not according to rigid schedules, but when signs of an imminent failure appear.
- Integration of expertise: The combination of automated data analyses and the experience of your maintenance staff leads to continuous improvement.
With this proactive approach, you reduce unplanned downtimes, increase the lifespan of your machines, and lower costs in the long term.
Boost Your Productivity with Clouver!
With our powerful IIoT platform, you'll have complete control over your production processes at all times. Reduce downtime, optimise resource usage, and stay ahead of your competition. Schedule your personal consultation now and discover how Clouver can support you!
Integration of Clouver to Increase System Reliability
The integration of modern IIoT solutions like Clouver plays a decisive role in optimising system reliability. Clouver is an Industrial Internet of Things (IIoT) production monitoring platform from ProCom that enables access to real-time data and simplifies the monitoring of heterogeneous machine parks.
With Clouver, you benefit from:
- Real-time data access: The user-friendly dashboard visualises all operational and disruption data in real time.
- Modular structure: The flexible architecture allows exact adaptation to your needs and gradual integration of important equipment.
- Integration of existing machines: The Clouver SmartKit enables the incorporation of older machines from various manufacturers into your IIoT network.
- Paperless order management: Clouver optimises access to order and disruption data for quick reactions.
Continuous monitoring with Clouver leads to a measurable increase in MTBF. Companies report a reduction in unplanned downtime of 15-25%, improved equipment availability, and targeted maintenance planning. The cloud-based infrastructure also ensures high flexibility, performance, and security.
Your Partner for Innovative Automation Solutions!
ProCom offers the perfect combination of intelligent software, premium hardware, and comprehensive support. Whether knife, laser, or waterjet cutting – we'll develop the ideal solution for your production needs. Arrange your consultation today and get started!
Summary
Mean Time Between Failures (MTBF) is a crucial metric for evaluating the stability and efficiency of your production processes. It measures the average time between two disruptions of a system and provides valuable information for optimising your operational procedures. With systematic recording and analysis of MTBF, you identify weaknesses in your machinery and maximise equipment availability.
By using modern IIoT solutions like Clouver, you benefit from real-time data access, modular integration possibilities, and paperless order management. This technology enables you to continuously improve MTBF, implement a proactive maintenance strategy, and reduce hidden production costs. Thus, your production process becomes sustainably more stable and efficient – a clear competitive advantage in an increasingly digitalised market.