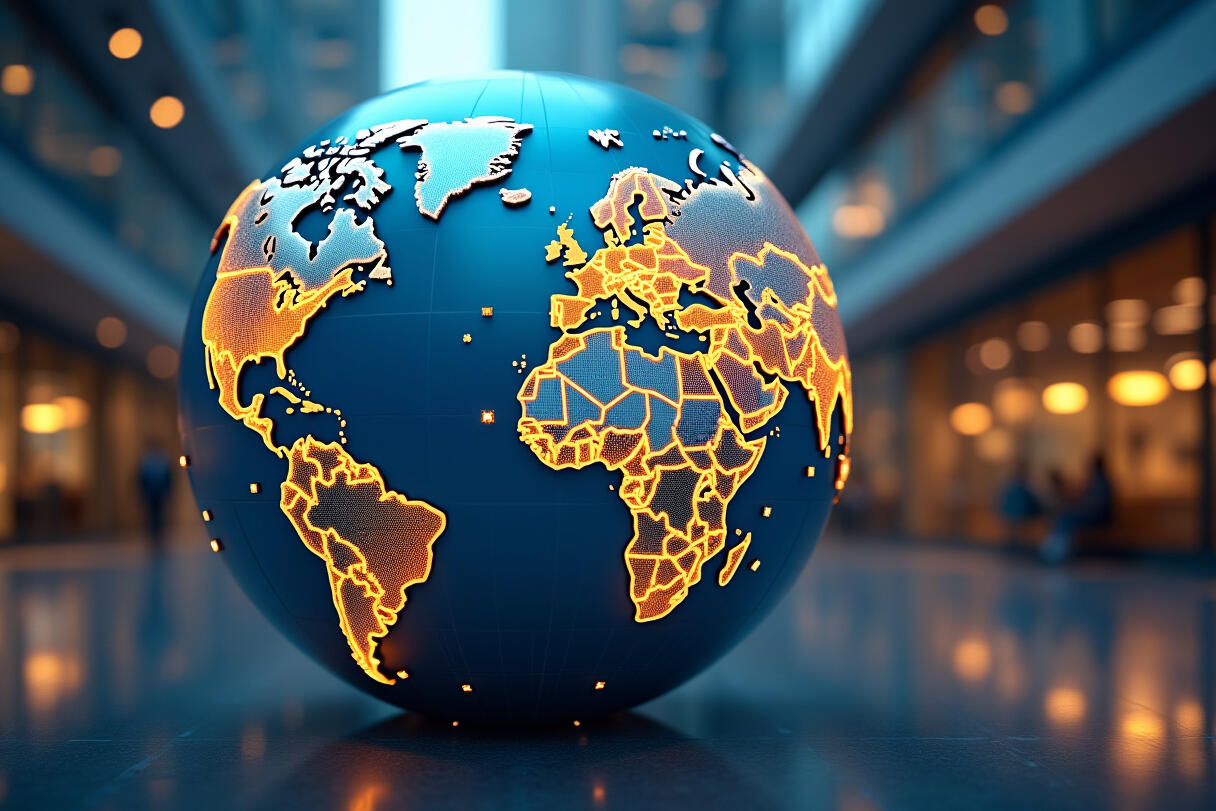
Have you ever wondered how plastic can be cut so precisely and efficiently in industrial production? Or why laser cutting is so popular in modern manufacturing? In this article, you'll learn everything you need to know about laser cutting plastics – from the basics and advantages to the best materials and technologies. Let's discover together why this technology is indispensable and how it can take your projects to the next level.
What Is Laser Cutting, and Why Is It So Efficient?
Laser cutting is a cutting-edge technology that uses a concentrated laser beam to cut, engrave, or mark materials. This beam heats the plastic so intensely that it melts, vaporises, or burns. The result? Perfectly smooth and clean cut edges – often without post-processing. This saves not only time but also material.
The advantages of laser cutting are obvious: It enables highly precise cuts, even with complex shapes, while causing minimal material waste. Moreover, the process is extremely flexible and can be used for a variety of plastics and applications, from prototypes to series production.
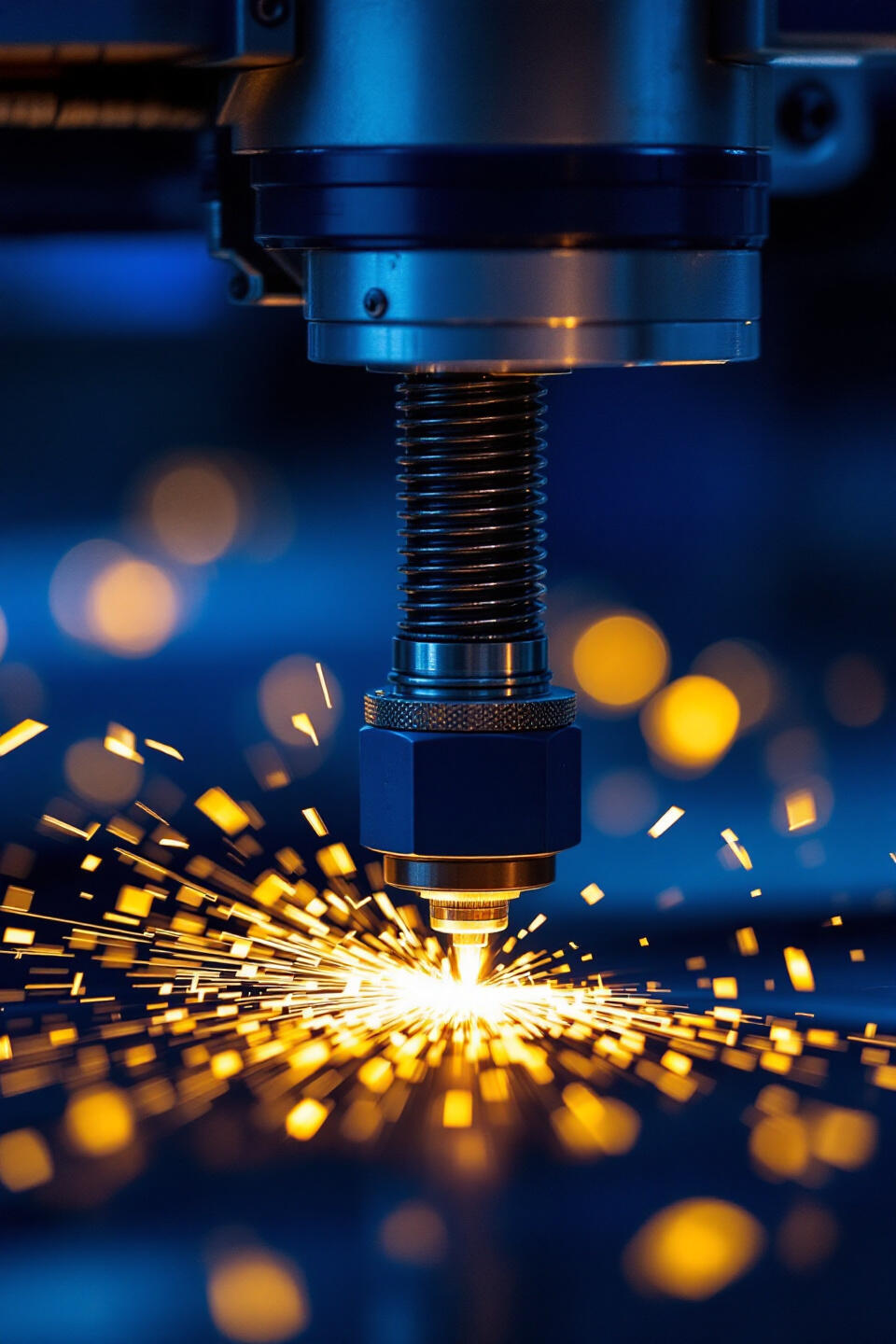
Which Plastics Are Particularly Suitable?
Not every plastic reacts equally well to laser cutting. Some materials can be cut easily and cleanly, while others require special precautions. Here are the most important plastics and their properties:
PMMA, also known as acrylic glass, is one of the most suitable materials. It offers optical clarity and enables extremely precise cuts. Polycarbonate and PVC, however, require special safety measures as they can release harmful fumes.
How Does Laser Cutting Work in Detail?
The laser cutting process is impressively simple yet technically sophisticated. The laser beam is focused on the surface of the plastic, where it generates extreme heat. This heat melts, burns, or vaporises the material, creating a precise cut. The generated fumes and particles are typically removed by extraction systems to ensure a clean and safe working environment.
Depending on the desired application, there are three main methods:
- Cutting: The material is completely cut through. Ideal for precise and complex shapes.
- Engraving: Material is superficially removed to create patterns or logos.
- Marking: Changes in material structure or colour, without material loss. Perfect for serial numbers or barcodes.
What Matters in the Technology?
To achieve perfect results in laser cutting, several technical factors are crucial. Laser power is a central point. Thin materials like 1-3 mm thick PMMA often require power between 25 and 50 watts. Thicker materials from 6 mm need 100 watts or more. Cutting speed is also important: Too slow a pace can cause overheating, while cutting too fast affects precision.
Modern control systems, such as those developed by ProCom Automation, offer additional support. They enable the management of material parameters, visualisation of cutting progress, and optimisation of cut quality in real-time.
How Safe Is Laser Cutting?
Safety is the top priority when working with lasers. Especially with plastics like PVC or polycarbonate, powerful extraction is essential as harmful gases can be released during processing. Safety glasses matched to the laser wavelength protect your eyes from intense radiation. You should also always pay attention to fireproof covers and fire protection measures to minimise potential risks.
What Does the Future Hold for Laser Cutting?
Laser cutting technology continues to evolve. Hybrid systems that combine laser technology with other processes open up new possibilities for even more flexible applications. At the same time, the integration of Industry 4.0 solutions ensures that machines become smarter and more connected. This allows you to monitor and optimise your production even better. Sustainability also plays an increasingly important role: Modern laser systems are more energy-efficient and help reduce the ecological footprint of production.
Conclusion: Why Laser Cutting Can Revolutionise Your Production
Laser cutting of plastics is a versatile and forward-looking technology that combines precision, efficiency, and sustainability. With the right choice of materials, optimised technical parameters, and modern control systems, you can not only reduce your production costs but also raise the quality of your products to a new level. Whether you're creating prototypes or engaged in mass production – this technology will sustainably improve your manufacturing processes.
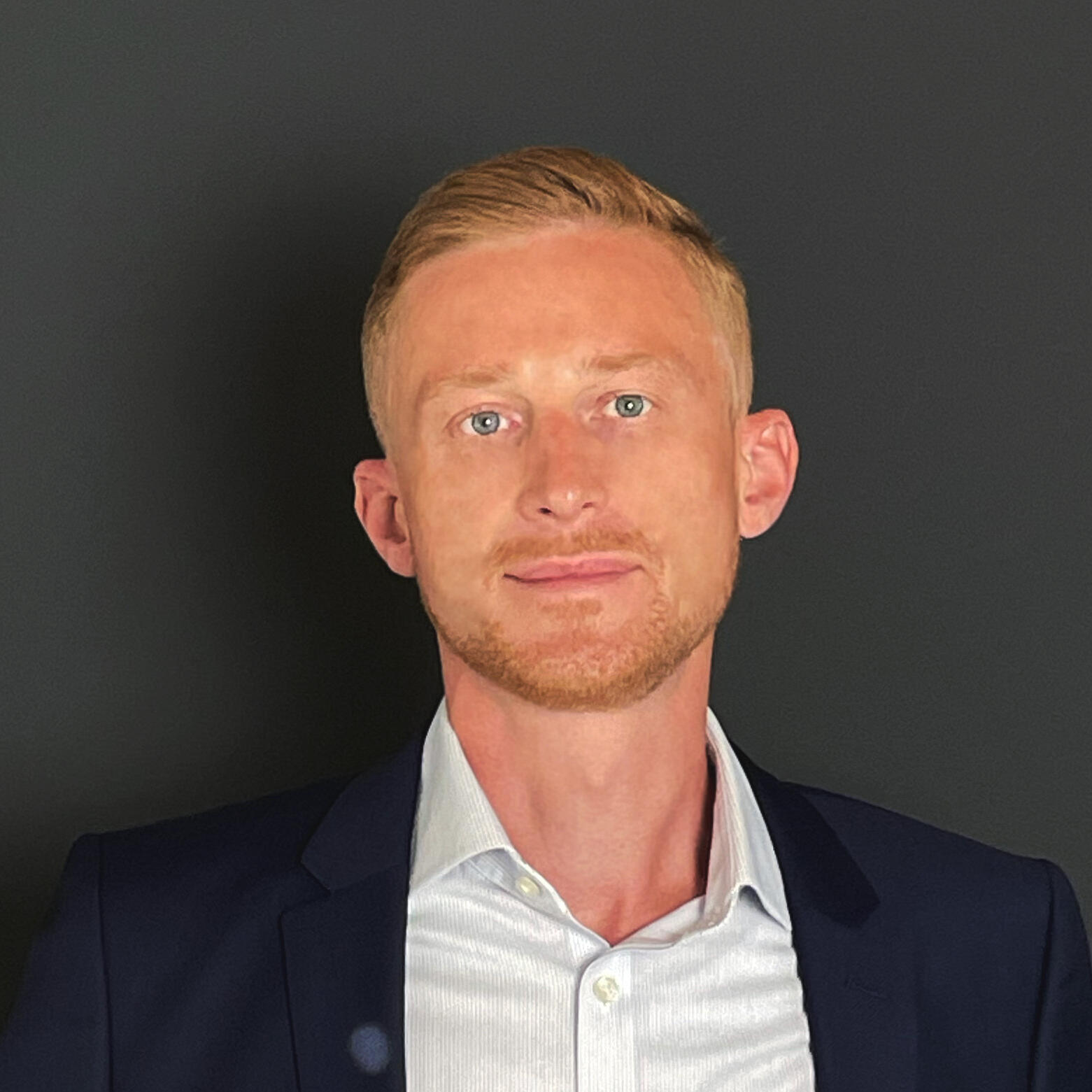
Dimitri Koneger
Sales Manager
Have questions about the topic or want to learn more about our solutions?
Contact us and discover how our products can future-proof your machines. Let’s work together to find out how we can help take your production to the next level!
- +49 241 93681-500
- contact@procom-automation.de
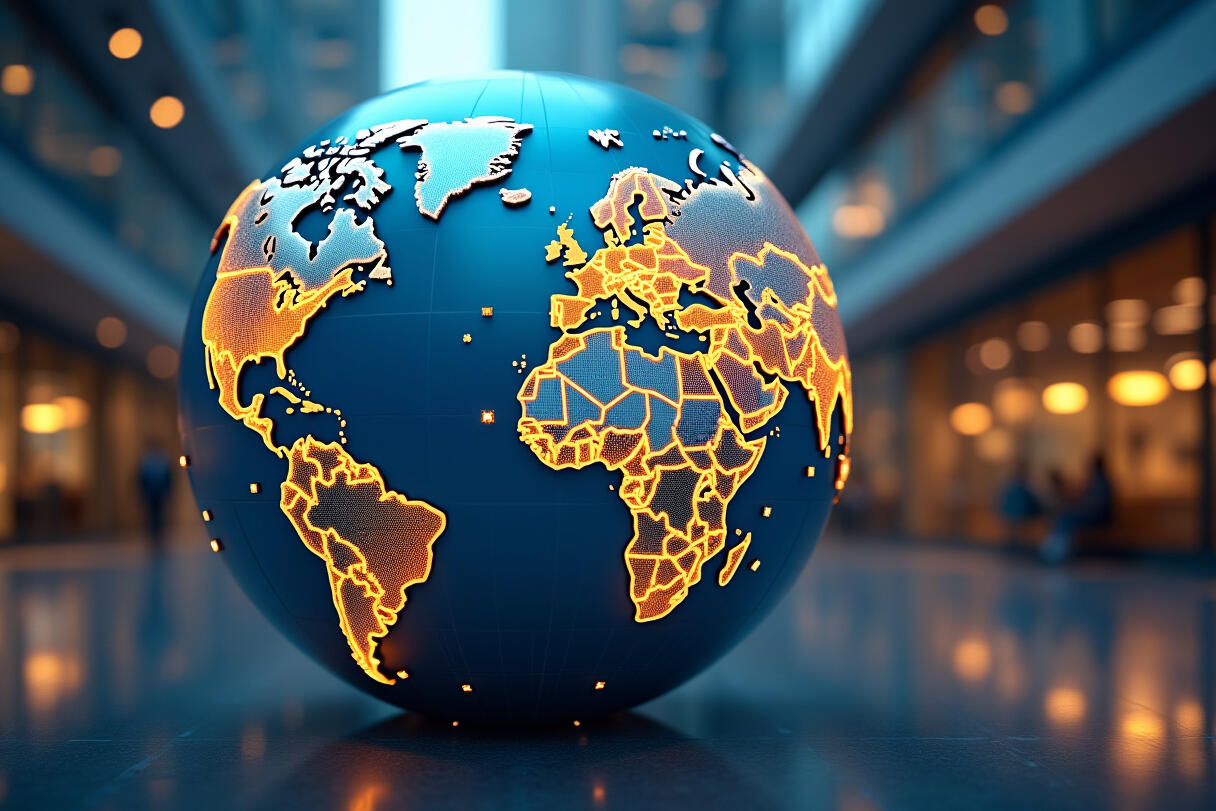
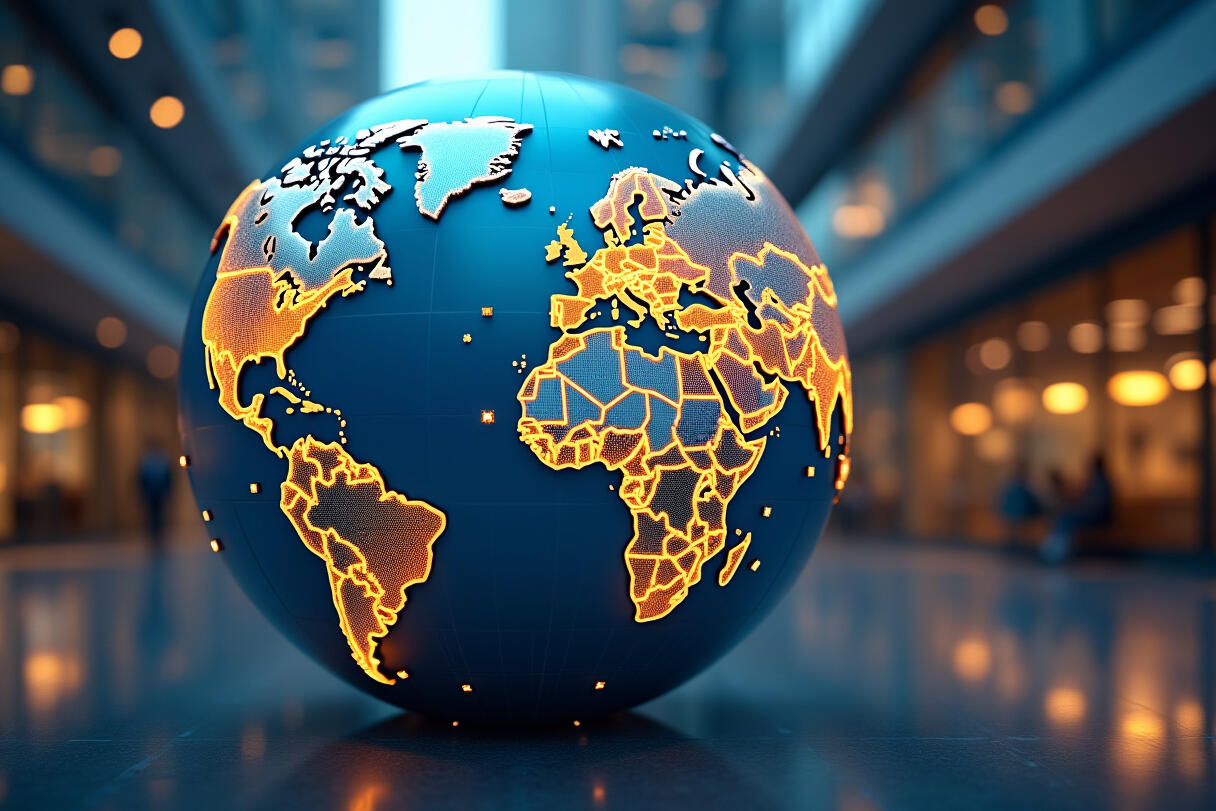