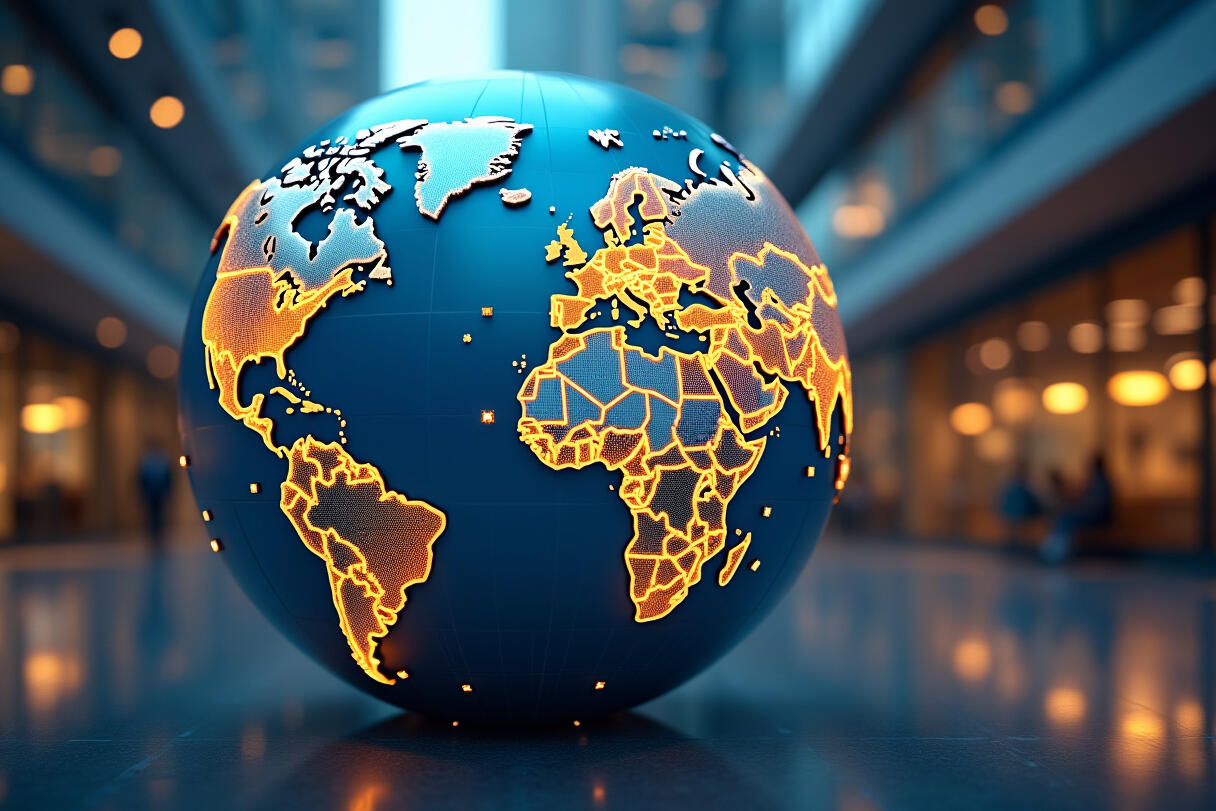
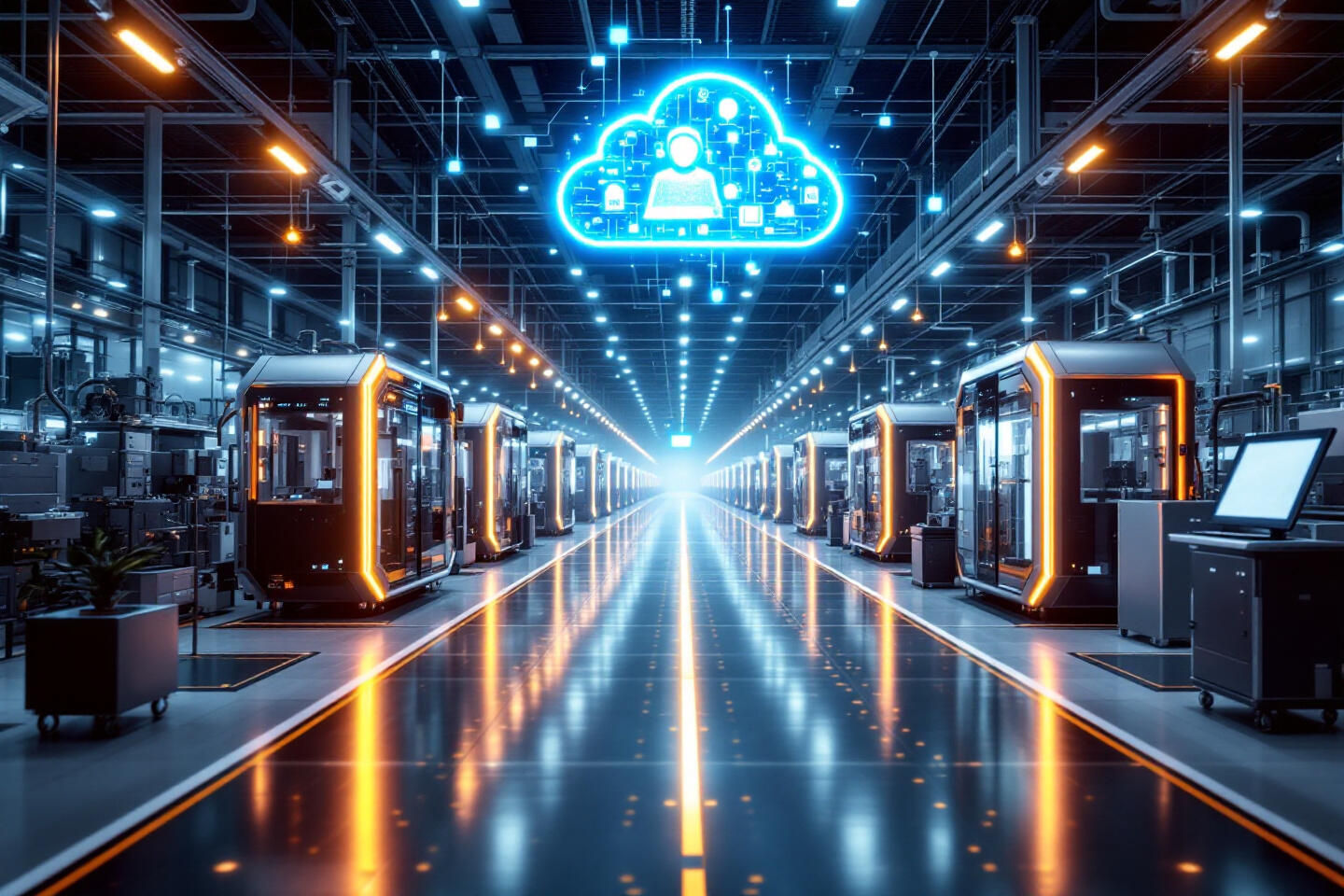
Imagine being able to predict and prevent breakdowns and expensive maintenance of your machines and equipment before they even occur. Predictive maintenance makes this possible and revolutionises the way companies optimise their operations and conserve their resources. In a world where production downtimes cause immense costs and efficiency is a decisive competitive advantage, predictive maintenance offers invaluable added value.
In this blog post, you will learn everything you need to know about predictive maintenance: from the technological foundations and innovations to implementation and best practices, through to real-world application examples from various industries. We explore how IoT sensor technology, machine learning and big data analytics work together to make precise predictions about the condition of your machines. We also address questions about data security and compliance and highlight future trends and developments.
Are you wondering how you can successfully implement predictive maintenance in your company? What economic benefits and cost-saving potentials are associated with it? Or what challenges and solutions exist? This blog post provides you with all the answers and offers valuable insights to help you take your maintenance strategies to the next level. Keep reading and discover how predictive maintenance can transform your operations!
1. Introduction to Predictive Maintenance
Predictive Maintenance (PdM) is a strategy based on monitoring the condition of machines and equipment to perform maintenance work only when it is actually required. This forward-looking method uses advanced technologies such as IoT sensors, machine learning and big data analytics to predict the optimal timing for maintenance work. Data such as vibrations, temperatures and pressure values are continuously collected and analysed to identify patterns and anomalies that indicate impending failures.
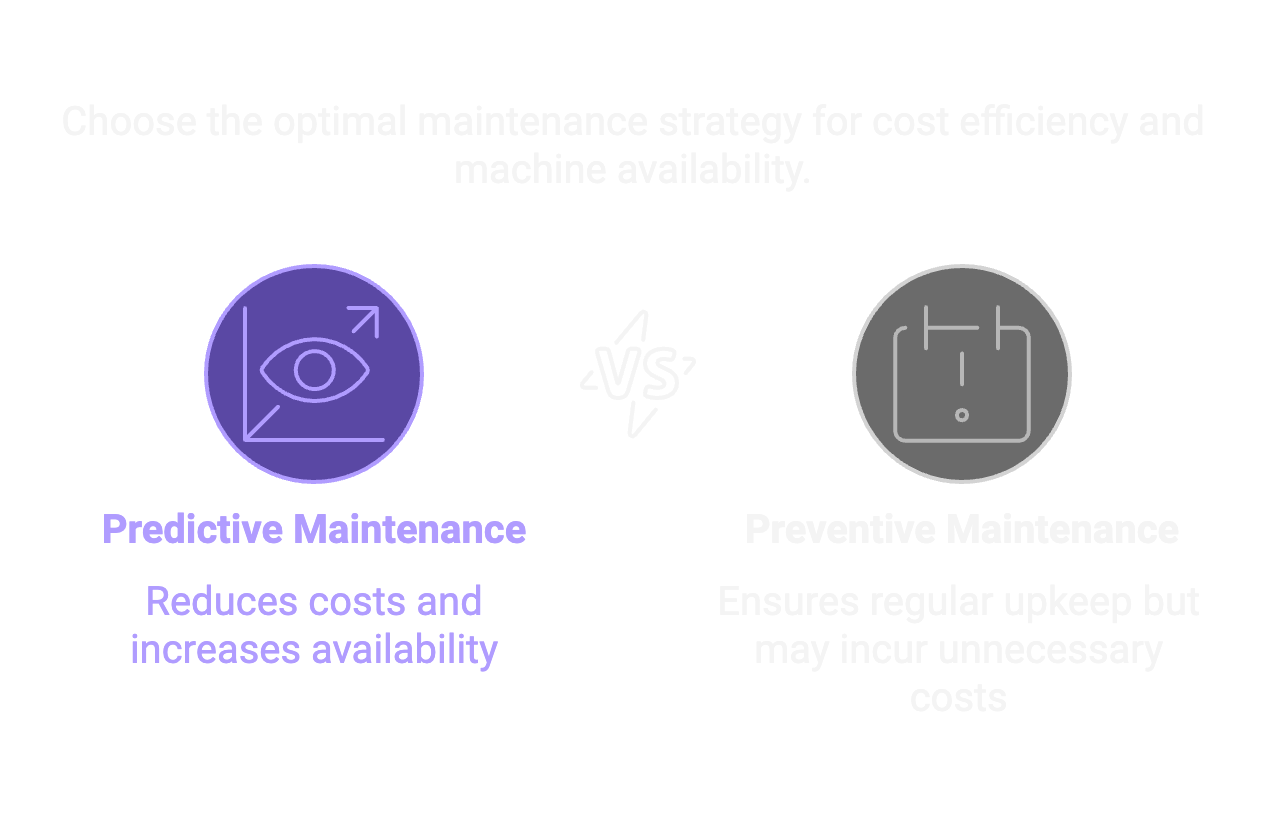
Set New Standards in Production with ProCom!
Our high-tech control solutions are designed to maximise efficiency and precision in your production. Stay competitive and future-proof with our support. Contact us today to learn more about our technologies and achieve your goals!
Difference Between Predictive and Preventive Maintenance
Whilst predictive maintenance is based on predicting failures, preventive maintenance relies on regular, time-controlled maintenance. Preventive maintenance occurs at fixed intervals or usage cycles, regardless of the actual condition of the machine, which can lead to unnecessary maintenance measures and associated costs. In contrast, predictive maintenance intervenes in a targeted and efficient manner as soon as there is an actual need, thereby reducing maintenance costs and increasing machine availability.
2. Technological Foundations and Innovations
IoT Sensor Technology and Developments
IoT sensors continuously collect data about the condition of machines and equipment. These sensors can measure various physical parameters such as vibration, temperature and pressure. The real-time data enables precise monitoring and early detection of potential problems. The development of increasingly smaller and more powerful sensors and their integration into existing systems has significantly improved the spread and efficiency of predictive maintenance.
Machine Learning Algorithms for Predictive Maintenance
Machine learning algorithms analyse the collected data and recognise patterns that indicate impending failures. These algorithms continuously learn from historical data and current measurements to enable increasingly precise predictions. By applying techniques such as anomaly detection and predictive modelling, maintenance teams can take early action before serious problems occur.
Edge Computing in Maintenance Prediction
Edge computing enables data processing directly at the source, i.e. close to the machines. This reduces latency and enables faster reactions to potential problems. Through decentralised data processing, large amounts of data can be handled efficiently without having to be constantly transferred to central data centres. This is particularly useful in environments with limited connectivity or high latency requirements.
Digital Twin Technology
A digital twin is a virtual model of a physical machine or system. By combining real data with virtual models, companies can monitor the condition of their machines in real-time and make predictions. Digital twins enable detailed simulations and analyses that help optimise maintenance strategies and extend machine life. They provide a platform for continuous learning and improvement through the replication and analysis of operating conditions.
Impact of 5G on Predictive Maintenance
The introduction of 5G technology enables faster and more reliable data transmission. With higher bandwidths and lower latency times, 5G significantly improves communication between IoT sensors and central data platforms. This leads to more efficient data processing and enables real-time analyses that further increase the efficiency of predictive maintenance systems. 5G also supports the integration and use of augmented reality and other advanced technologies in maintenance processes.
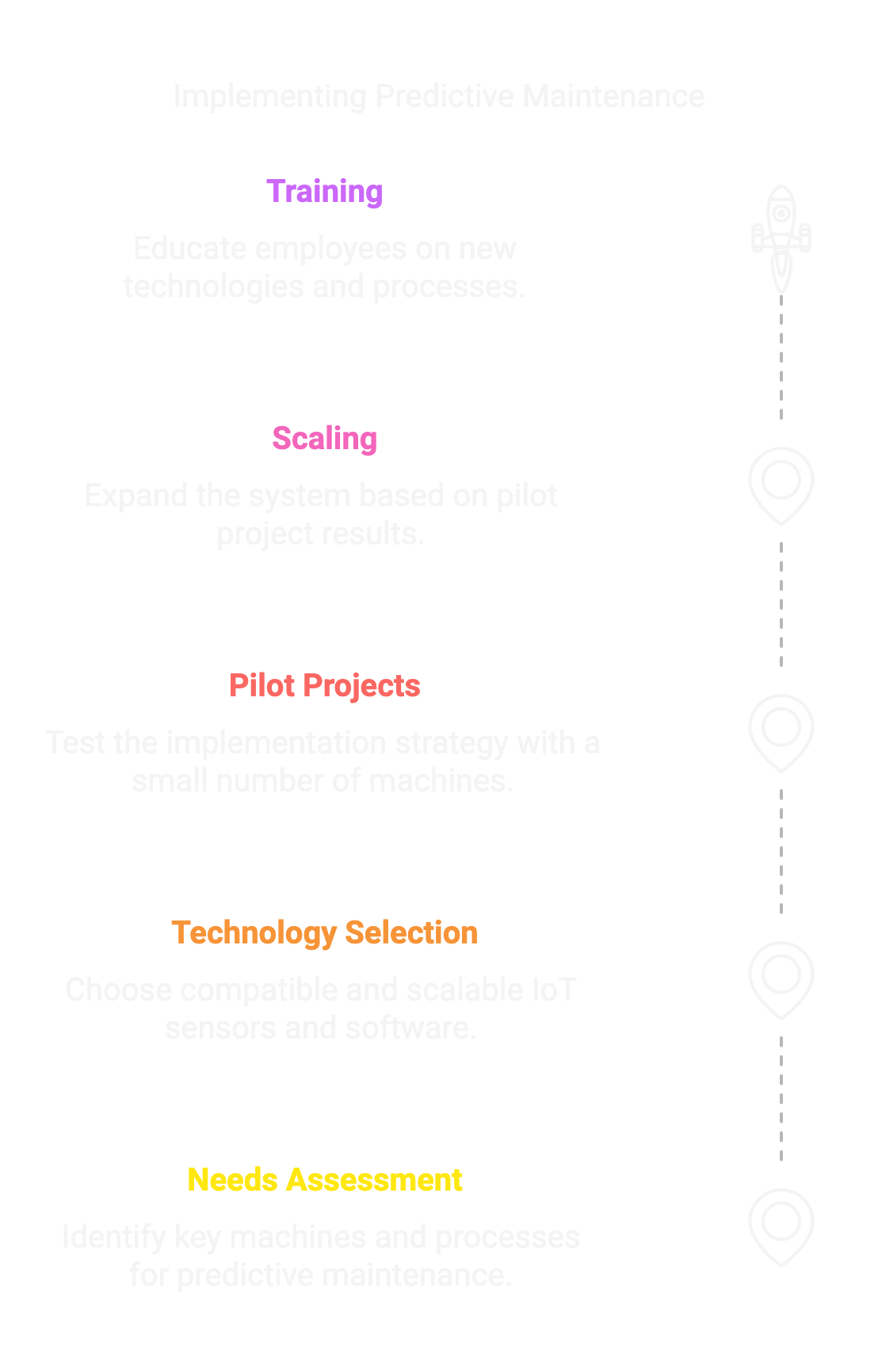
3. Implementation and Best Practices
Step-by-Step Implementation Guide
Needs Assessment: Identify the most important machines and processes that could benefit from predictive maintenance. Analyse current failure rates and maintenance costs to determine potential savings.
Technology Selection: Choose the appropriate IoT sensors, data platforms and analysis software. Ensure that the selected technologies are compatible and scalable.
Pilot Projects: Conduct pilot projects to test practicability and benefits. Start with a small number of machines to gain experience and refine the implementation strategy.
Scaling: Scale the implementation to additional machines and processes based on the results of the pilot projects. Use the insights gained to maximise the efficiency and effectiveness of the systems.
Training: Train your employees in handling new technologies and processes. Ensure that maintenance personnel understand and can effectively use the new systems.
Success Factors and Common Pitfalls
The success of predictive maintenance depends on the quality of data and the willingness of employees to adapt to new technologies. Careful planning and gradual introduction are crucial. Common pitfalls include insufficient data quality, lack of integration with existing systems and insufficient training. Comprehensive change management and the involvement of all stakeholders are also important to overcome resistance and promote acceptance.
ROI Calculation and Business Case Development
Develop a simple tool for calculating the Return on Investment (ROI) for your predictive maintenance projects. Consider all relevant costs and savings, including the reduction of downtime, extension of machine life and reduction of maintenance costs. Create a detailed business case that describes the potential financial and operational benefits to demonstrate the necessity and value of the investment.
Change Management During Implementation
The introduction of new technologies requires effective change management. Ensure that all parties involved are informed and trained to minimise resistance and promote acceptance. Continuously communicate the benefits and progress of predictive maintenance initiatives and offer support and training to facilitate the transition.
Employee Training and Competency Building
Train your employees continuously in handling new technologies and processes. This ensures that the full potential of predictive maintenance is realised. Offer regular further education opportunities and certifications to keep your teams' knowledge and skills up to date.
4. The Role of Big Data and Analytics
Data Collection and Analysis
Continuously collect data from your machines and equipment and use advanced analytical tools to interpret this data and gain valuable insights. Accurate data collection and analysis are crucial for making precise predictions and informed decisions. Use both historical and real-time data to gain comprehensive insights into the condition and performance of your machines.
Integration of Data Sources
Ensure that all relevant data sources are merged into a central platform. This enables comprehensive analysis and better predictions. Integrate data from various systems such as ERP, CMMS and IoT platforms to obtain a complete picture and support data-driven decisions.
Use of Predictive Analytics for Maintenance Forecasting
Use predictive analytics to precisely forecast future maintenance needs and thus maximise the efficiency and availability of your facilities. Predictive analytics combines statistical models, machine learning and data analysis techniques to identify patterns and trends that indicate upcoming maintenance requirements. This enables proactive measures and improves the planning and execution of maintenance work.
5. Industry-Specific Applications
Manufacturing 4.0
Predictive maintenance is a central component of Industry 4.0 and helps manufacturing companies minimise downtime and increase productivity. Through the integration of IoT sensors and data analysis, manufacturers can continuously monitor the condition of their machines and plan maintenance measures as needed. This leads to higher efficiency and better use of resources.
Energy Sector and Utilities
Energy providers can increase the reliability of their networks and reduce maintenance costs through predictive maintenance. Continuous monitoring of transformers, generators and other critical components enables early intervention and prevents costly failures. This contributes to the stability and efficiency of energy supply.
Healthcare Equipment
Hospitals and other healthcare facilities use predictive maintenance to ensure the availability and safety of medical equipment. By monitoring diagnostic devices, ventilators and other vital equipment, potential problems can be identified and resolved early, increasing patient safety and reducing operating costs.
Smart Buildings
In intelligent buildings, predictive maintenance ensures the smooth operation of heating, ventilation and air conditioning systems. Sensors continuously monitor the condition of HVAC systems and report anomalies before they lead to larger problems. This improves building comfort and energy efficiency whilst reducing maintenance costs.
Process Industry
In the process industry, predictive maintenance helps maximise the availability and efficiency of complex facilities. By monitoring pumps, valves and other critical components, companies can ensure their production facilities operate optimally and minimise unplanned downtime.
6. Data Security and Compliance
Cybersecurity in Predictive Maintenance Systems
Implement robust cybersecurity measures to protect your data and systems from unauthorised access and attacks. This includes data encryption, the use of firewalls and intrusion detection systems, as well as regular security checks and updates. Ensure that all systems and networks meet the highest security standards.
Data Protection Aspects
Ensure that your predictive maintenance solutions comply with all relevant data protection regulations. This includes compliance with regulations such as the EU General Data Protection Regulation (GDPR) and other regional data protection laws. Implement data protection policies and procedures to ensure the confidentiality and integrity of collected data.
Industry Standards and Certifications
Adhere to industry standards and certifications to ensure the quality and safety of your predictive maintenance systems. These include standards such as ISO 27001 for information security management and ISO 55001 for asset management. Compliance with these standards demonstrates your company's commitment to best practices and continuous improvement.
Cloud vs On-Premise Solutions
Weigh the advantages and disadvantages of cloud-based and on-premise solutions to choose the best option for your company. Cloud-based solutions offer scalability, flexibility and lower initial costs, whilst on-premise solutions enable greater control over data and systems. Consider your specific requirements and resources to find the optimal solution.
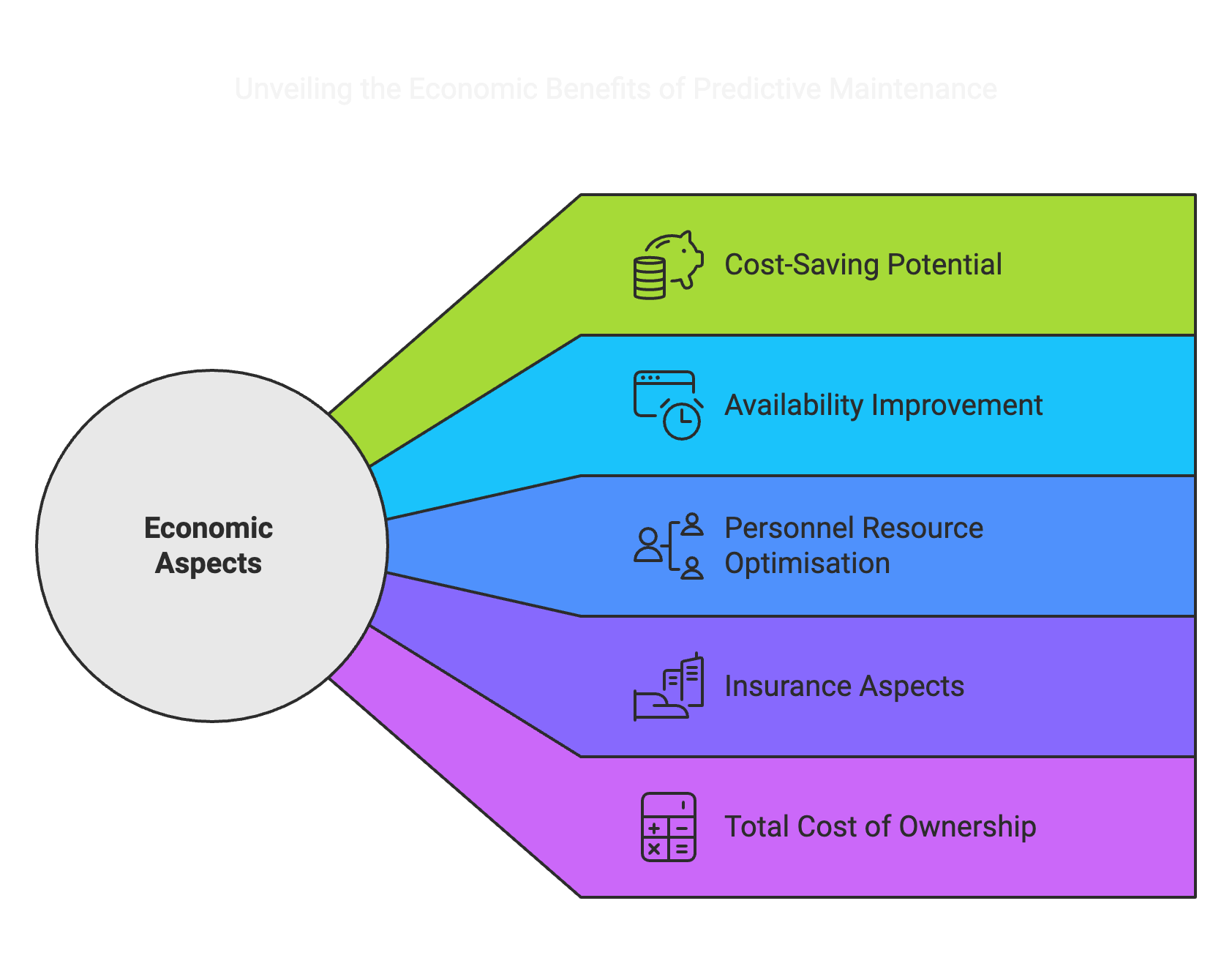
7. Economic Aspects
Cost-Saving Potential
Predictive maintenance helps reduce maintenance costs and avoid expensive downtime. Through early detection and resolution of problems, companies can minimise unplanned shutdowns and improve the efficiency of their maintenance processes. This leads to significant cost savings and higher profitability.
Availability Improvement
Early detection of problems maximises the availability of your machines and equipment. Predictive maintenance helps increase uptime and maximise production capacity by ensuring machines and equipment remain in optimal condition.
Personnel Resource Optimisation
Optimise the deployment of your maintenance teams and improve the planning of maintenance work. Predictive maintenance enables more efficient use of personnel resources by planning maintenance tasks based on actual need rather than rigid schedules. This leads to better workload distribution and higher employee satisfaction.
Insurance Aspects
Predictive maintenance can lead to lower insurance premiums as the risk of failures and damage is reduced. Insurance companies recognise the benefits of predictive maintenance and often offer more favourable rates for companies that employ these technologies.
Total Cost of Ownership
Reduce the total cost of operating your machines and equipment through more efficient maintenance and longer service life. Predictive maintenance helps lower the Total Cost of Ownership (TCO) by minimising unplanned downtime, extending machine life and increasing the efficiency of maintenance processes.
8. Integration and Interfaces
ERP System Integration
Ensure that your predictive maintenance solutions are seamlessly integrated with your ERP system. This enables a unified data base and improves the planning and control of maintenance processes. Seamless integration also supports analysis and reporting by bringing together all relevant information in a central platform.
CMMS Connection
Integrate your predictive maintenance systems with your Computerised Maintenance Management System (CMMS) for better maintenance work management. This integration facilitates the planning, execution and tracking of maintenance tasks and ensures that all maintenance activities can be documented and analysed.
IoT Platforms
Use IoT platforms for collecting and analysing sensor data. These platforms provide the infrastructure and tools required to manage large amounts of data and gain valuable insights. By integrating IoT platforms into your predictive maintenance strategy, you can improve the efficiency and accuracy of your maintenance predictions.
Cloud Services
Benefit from the advantages of cloud-based solutions for storing and analysing large amounts of data. Cloud services offer scalability, flexibility and cost efficiency by reducing the need for expensive on-site infrastructure. They also enable easy access to data and analytics from anywhere at any time.
Mobile Solutions
Use mobile solutions to transmit maintenance information to your technicians in real-time. Mobile applications enable maintenance teams to access information, track tasks and create reports whilst working on site. This improves communication, efficiency and responsiveness of maintenance teams.
9. Future Trends and Developments
AI-Supported Predictive Maintenance
Artificial Intelligence (AI) will further improve the accuracy and efficiency of predictive maintenance. Through the use of advanced algorithms and machine learning, AI systems can recognise complex patterns and relationships in large amounts of data that are difficult for human analysts to grasp. This enables more precise predictions and more proactive maintenance strategies.
Augmented Reality in Maintenance
Augmented Reality (AR) can support maintenance technicians in carrying out repairs and increase efficiency. AR glasses or mobile devices can display real-time information, instructions and visual overlays that help technicians complete complex tasks more quickly and accurately. This leads to a reduction in downtime and an improvement in maintenance quality.
Blockchain Integration
Blockchain technology can improve the security and transparency of predictive maintenance data. By using blockchain, companies can ensure their data is immutable and traceable. This increases confidence in data integrity and facilitates compliance requirements.
Autonomous Maintenance
Autonomous maintenance systems could perform maintenance work without human intervention in the future. Through the use of robotics and AI, such systems can independently perform inspections, diagnoses and repairs, further increasing the efficiency and accuracy of maintenance processes.
Sustainable Maintenance
Sustainable maintenance practices aim to minimise the ecological footprint of maintenance work. Through the use of predictive maintenance, companies can reduce energy consumption and waste production by only performing maintenance work when it is actually required. This contributes to environmental protection and the achievement of sustainability goals.
Conclusion
Predictive maintenance is far more than just a trend – it represents a decisive turning point in maintenance technology. Through the targeted use of IoT sensors, machine learning and big data analytics, it not only enables precise prediction of maintenance needs but also significant reduction in downtime and maintenance costs. Companies that rely on predictive maintenance succeed in making their operations more efficient, extending the life of their machines whilst conserving resources.
Another highlight is the versatility of this technology: from manufacturing to the energy sector to smart buildings and healthcare – the benefits are impressive across industries. Predictive maintenance not only helps reduce operating costs but also actively contributes to sustainability by avoiding unnecessary repairs and energy waste.
The future of maintenance lies in the combination of artificial intelligence, digital twins, 5G and blockchain. These technologies will further automate maintenance processes and make them more sustainable, whilst augmented reality increases efficiency and precision on site. Companies that invest in these technologies today secure decisive competitive advantages and position themselves successfully for future challenges.
Would you like to find out how predictive maintenance can transform your company too? Then read our blog now and dive deeper into the world of predictive maintenance! Or contact our expert team directly for a no-obligation consultation and get individual insights into how you can successfully implement predictive maintenance.
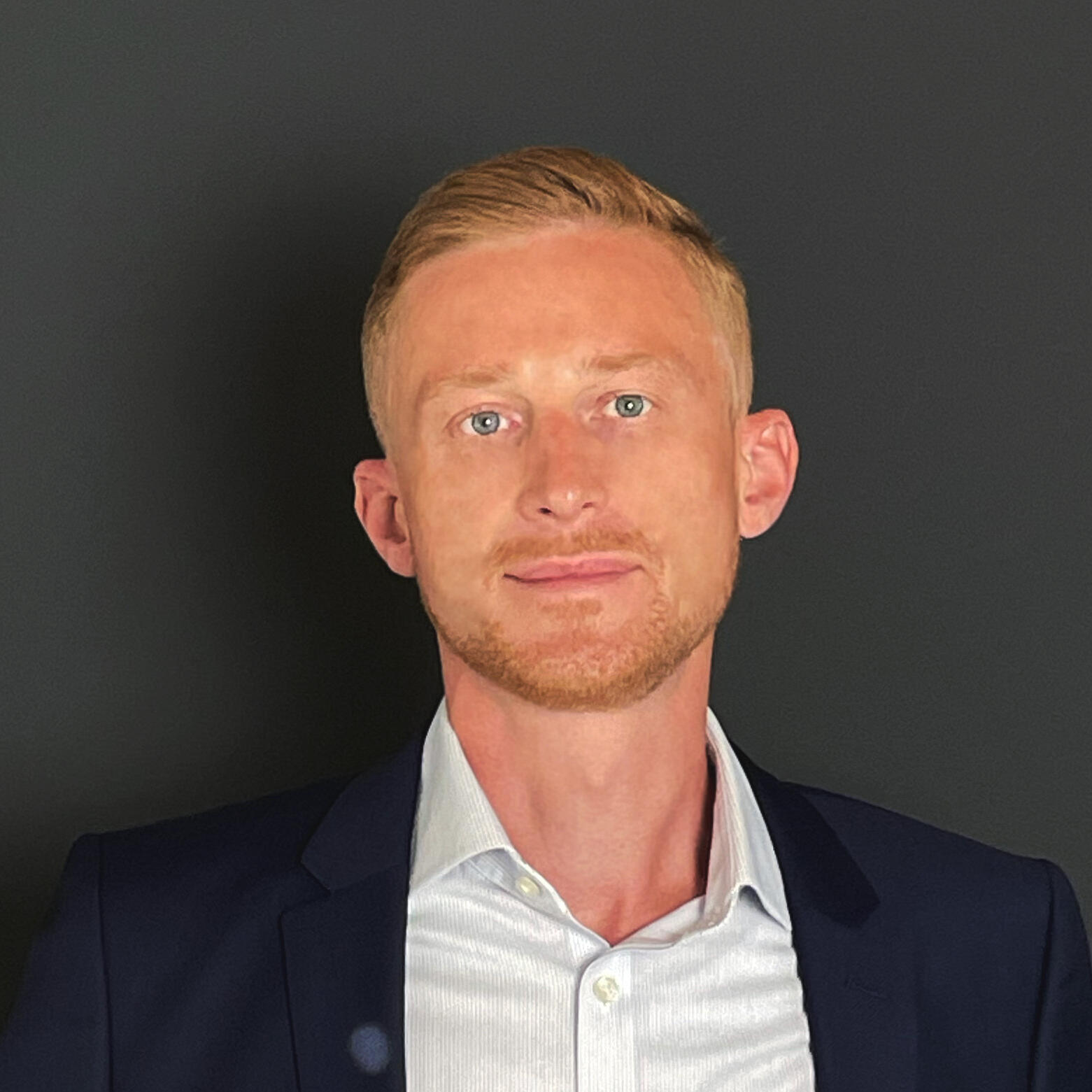
Dimitri Koneger
Sales Manager
Have questions about the topic or want to learn more about our solutions?
Contact us and discover how our products can future-proof your machines. Let’s work together to find out how we can help take your production to the next level!
- +49 241 93681-500
- contact@procom-automation.de
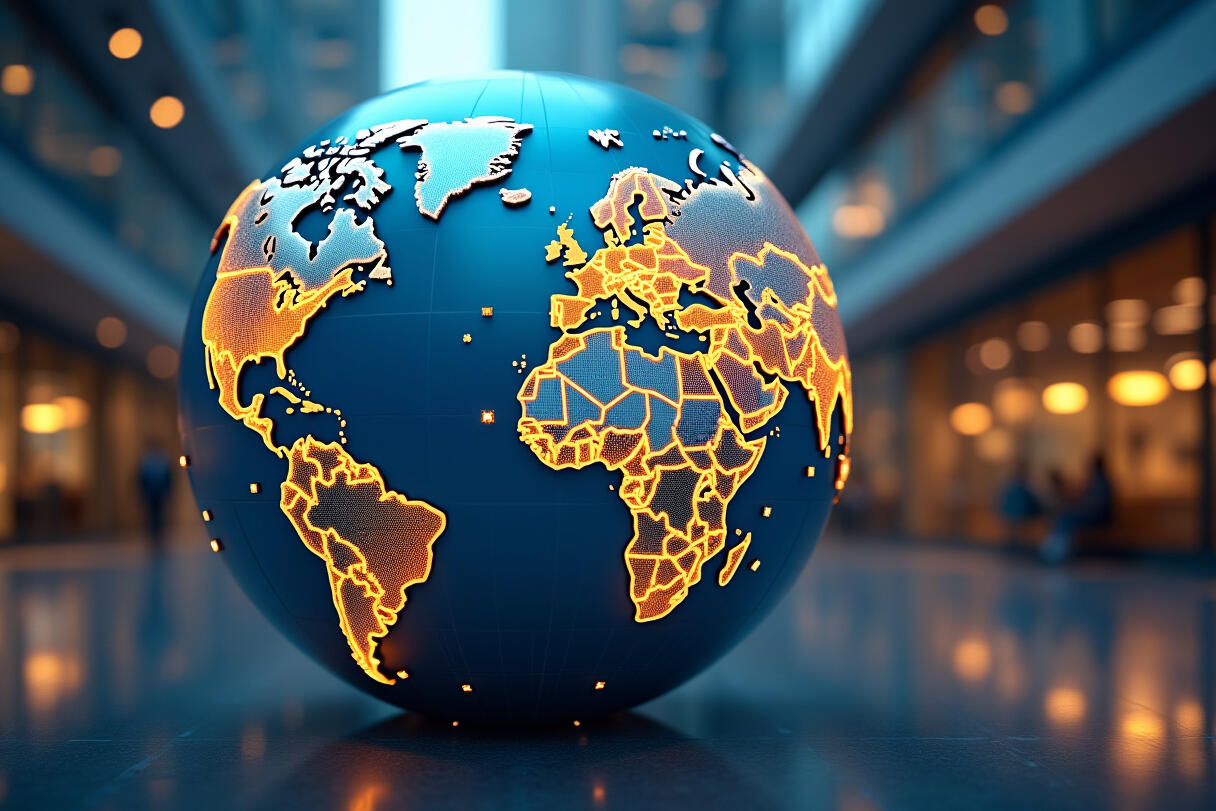
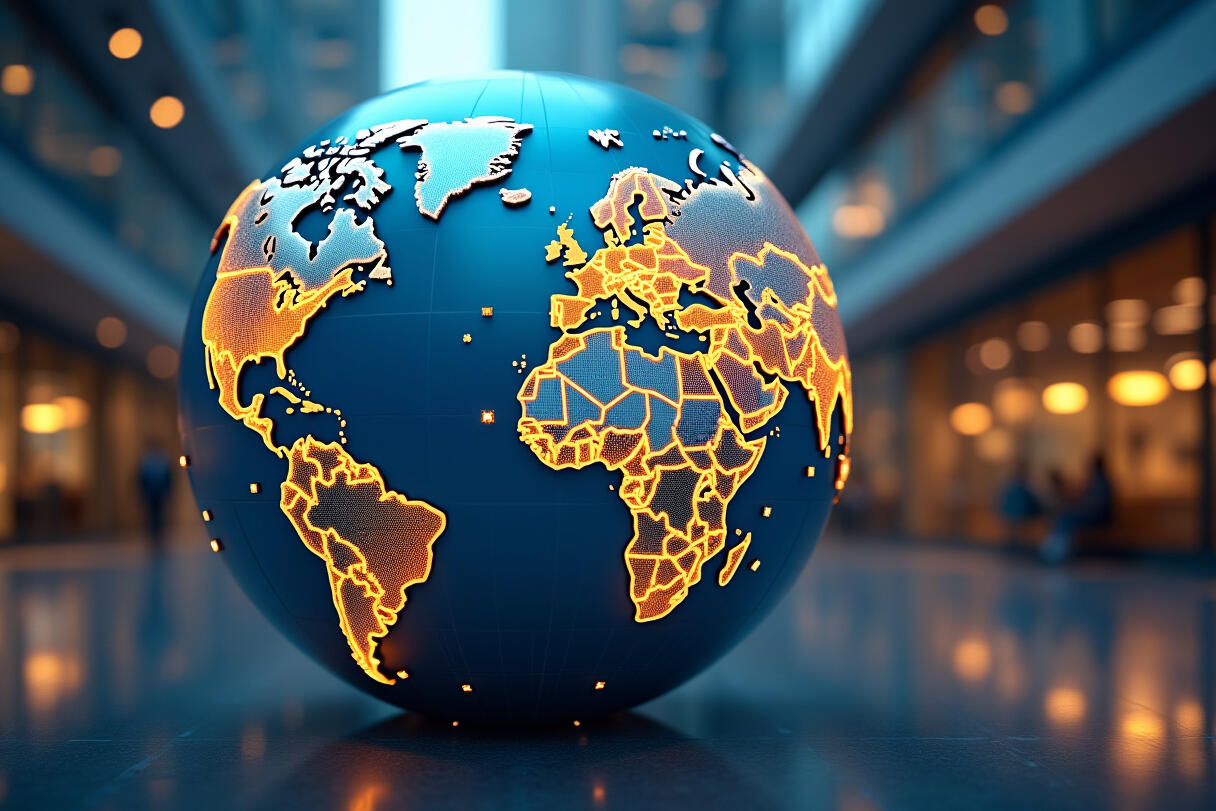