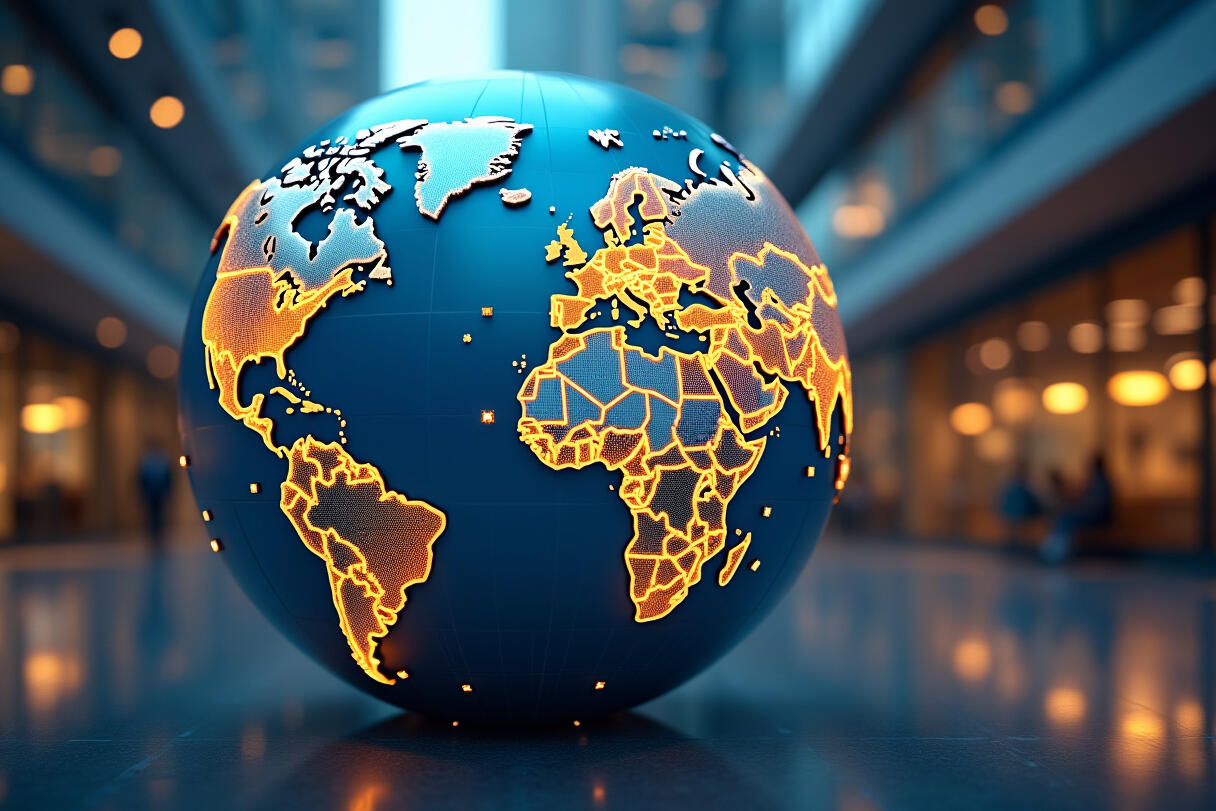
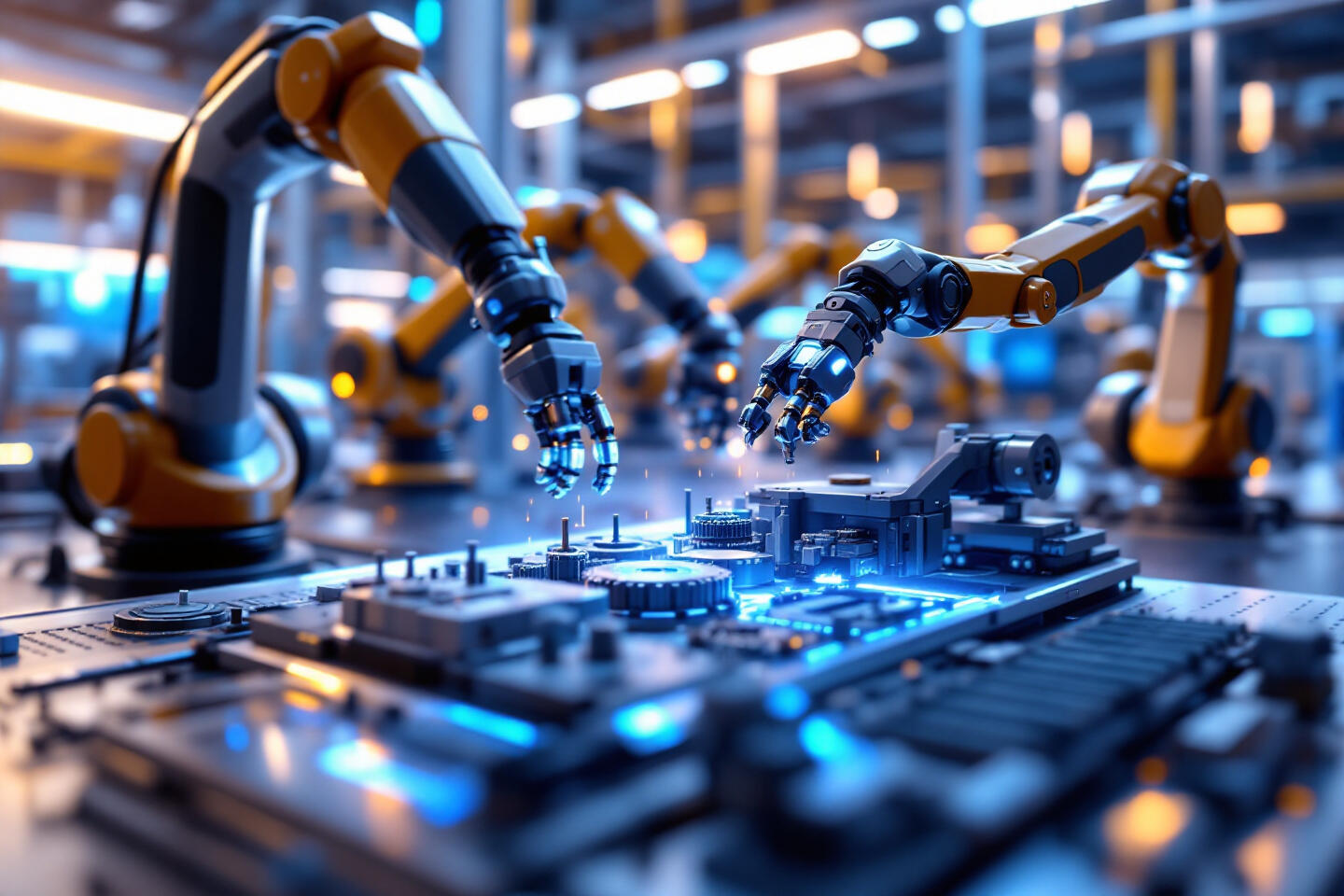
The industrial revolution 4.0 has ushered in a new era of tool management. In an age where digitalisation and networking dominate the production process, companies face the challenge of managing their tools more efficiently and intelligently. But what does "Tool Management Industry 4.0" mean specifically, and why is it crucial for companies' competitiveness?
In this article, we explore how digital tool management systems, IoT sensors from Clouver, cloud solutions, and predictive maintenance are revolutionising tool management. You'll learn how these technologies can be seamlessly integrated into existing ERP systems and what economic advantages they offer – from cost savings to significant increases in process efficiency.
Readers concerned with questions about implementation and the potential of Industry 4.0 tool management will find valuable insights and practical tips here. Learn how to elevate your tool management to the next level and which technologies and strategies play a key role. Dive into the future of tool management and secure a competitive advantage through cutting-edge digital solutions.
Introduction to Tool Management and Industry 4.0
Definition of Tool Management
Tool management encompasses the planning, monitoring, and maintenance of tools used in production. The goal is to ensure the availability and performance of tools to make production processes smooth and efficient. Effective tool management reduces downtime, extends tool life, and improves product quality. In Industry 4.0, this means using the latest technologies to monitor and control tools in real-time.
Significance of Industry 4.0 in Industrial Context
Industry 4.0 represents the fourth industrial revolution, characterised by the digitalisation and networking of production processes. Technologies such as the Internet of Things (IoT), Big Data, and artificial intelligence (AI) enable optimised manufacturing and increased flexibility. For tool management, this means more precise monitoring, intelligent maintenance planning, and seamless integration into the entire production chain. Companies implementing Industry 4.0 in tool management can significantly increase their competitiveness and respond more quickly to market changes.
Technological Foundations
Digital Tool Management Systems
Digital tool management systems enable centralised recording, monitoring, and administration of tools. They offer numerous advantages such as reducing search times, minimising tool losses, and optimising maintenance planning. Systems from Procom integrate seamlessly into existing ERP systems and offer efficient data processing and utilisation. Through real-time monitoring, companies can view the current state of their tools at any time and take proactive measures to maximise tool availability.
IoT Sensors for Tool Monitoring
IoT sensors from Clouver can be attached to tools to monitor their condition in real-time. These sensors collect data such as temperature, vibration, and frequency of use, which can be used to predict maintenance needs and prevent failures. The use of IoT sensors increases transparency and enables proactive tool maintenance. This allows companies to reduce unplanned downtime and extend the life of their tools.
Cloud-based Management Solutions
Cloud-based solutions offer a flexible and scalable platform for tool management. They enable access to tool data from anywhere and at any time, facilitating collaboration and decision-making. Cloud solutions from Clouver offer high data security and enable integration with other systems such as ERP or MDE. This flexibility ensures that companies can quickly respond to changes and keep their tool management up to date.
Predictive Maintenance for Tools
Predictive maintenance uses algorithms and data analysis to predict maintenance needs before a failure occurs. By predicting maintenance requirements, companies can reduce unplanned downtime, extend tool life, and lower production costs. Clouver offers advanced predictive maintenance solutions based on machine learning that enable accurate predictions. This leads to more efficient tool utilisation and optimised maintenance planning.
Integration and Networking
Interfaces with ERP Systems
The integration of tool management solutions into ERP systems enables seamless data exchange and centralised management of all relevant information. Systems from Procom offer standardised interfaces and APIs that ensure smooth integration. This leads to improved planning and control of production processes. Integration challenges can be effectively overcome through the use of standardised protocols and comprehensive support services from Procom.
Machine Data Collection (MDC)
Machine data collection is essential for tool management in Industry 4.0. By collecting and analysing machine data, companies can monitor tool performance, identify optimisation potential, and improve maintenance planning. Procom offers specialised MDC solutions that enable precise data collection and analysis. This supports companies in continuously optimising their production processes and maximising tool availability.
Digital Twin in Tool Management
A digital twin is a virtual representation of a physical tool that reflects its condition and performance in real-time. Through the use of digital twins, companies can optimise the use and maintenance of their tools and make informed decisions based on current data. Procom offers advanced digital twins that enable detailed simulation and analysis. This leads to better planning and increased efficiency in tool management.
Real-time Data Processing
Real-time data processing allows companies to respond immediately to deviations and problems. This leads to higher responsiveness and flexibility in production, which in turn increases efficiency and productivity. Clouver offers powerful real-time data processing solutions that support immediate analysis and decision-making. This enables companies to quickly respond to changes and continuously optimise their production processes.
Practical Implementation
Step-by-step Introduction of Industry 4.0 Solutions
The step-by-step introduction of Industry 4.0 solutions in tool management comprises several phases:
Needs Analysis: Identify your company's requirements and objectives.
System Selection: Compare various digital management systems from Procom and Clouver and select the appropriate one.
Start Pilot Project: Initially implement the system in a small area to test and optimise it.
Complete Implementation: Roll out the system to all relevant areas.
Conduct Training: Train your employees to ensure the system is used effectively.
This structured approach ensures smooth implementation and maximises the benefits of the deployed technologies.
Change Management in the Tool Sector
Successful change management is crucial for the acceptance of new technologies. This includes:
- Communication: Inform all stakeholders early about planned changes.
- Participation: Actively involve employees in the change process.
- Training: Offer training and support to facilitate the transition.
- Feedback: Regularly collect feedback and adjust the process accordingly.
- Success Measurement: Monitor progress and measure implementation success.
Through targeted change management, you ensure that all employees understand and can effectively use the new systems.
Employee Training and Qualification
Training and qualifying employees is an important aspect when introducing Industry 4.0 solutions. This includes:
Needs Analysis: Determine your employees' training needs. Create Training Plan: Develop a comprehensive training plan covering all relevant topics. Practical Training: Use practice-oriented training methods to enable direct application of learned content. E-Learning: Use Clouver's e-learning platforms to enable flexible learning. Continuous Education: Offer regular further education to keep knowledge current.
Through targeted training, you ensure that your employees can effectively use the new technologies.
Boost Your Productivity with Clouver!
With our powerful IIoT platform, you'll have complete control over your production processes at all times. Reduce downtime, optimise resource usage, and stay ahead of your competition. Schedule your personal consultation now and discover how Clouver can support you!
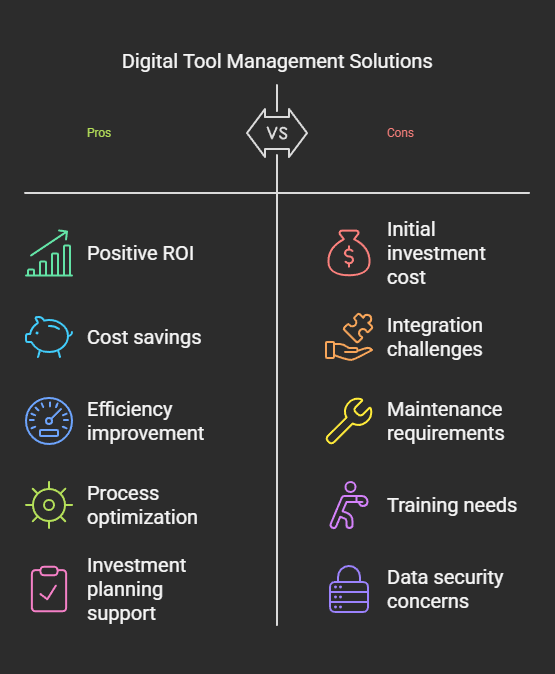
Economic Aspects
ROI Calculation for Digital Tool Management
The calculation of Return on Investment (ROI) is crucial for evaluating the economic benefits of digital tool management solutions. Methods and examples help quantify the financial advantages. A positive ROI shows that investment in systems from Procom and Clouver makes economic sense by reducing costs and increasing efficiency.
Cost Saving Potential
Through the optimisation of tool management, companies can achieve significant cost savings. This includes reducing tool losses, minimising downtime, and extending tool life. Procom and Clouver offer solutions that maximise these savings potential by enabling precise monitoring and efficient maintenance planning.
Process Optimisation and Efficiency Improvement
Digital tool management solutions offer numerous opportunities for process optimisation and efficiency improvement. These include automation of administrative tasks, improvement of maintenance planning, and real-time monitoring of tool performance. Systems from Procom and Clouver enable seamless integration into existing processes, optimising workflows and increasing productivity.
Investment Planning
Careful investment planning is crucial for the success of Industry 4.0 projects in tool management. Companies should carefully weigh costs and benefits to make an informed decision. Procom and Clouver support the creation of detailed investment plans that consider all relevant factors and provide a solid basis for decision-making.
Future Trends
AI in Tool Management
Artificial Intelligence (AI) offers numerous applications in tool management, from automated data evaluation to predictive maintenance. AI-supported systems from Clouver can recognise patterns and trends and enable informed decisions. This leads to further automation and optimisation of tool administration.
Augmented Reality for Maintenance
Augmented Reality (AR) can significantly facilitate the maintenance and repair of tools. By displaying digital information in technicians' field of view, maintenance work can be carried out more efficiently and precisely. Procom integrates AR solutions that accelerate troubleshooting and repair processes and increase accuracy.
Blockchain for Tool Tracking
Blockchain technology offers a secure and transparent way to track and manage tools. It enables complete traceability and increases the security of tool data. Clouver uses blockchain to ensure an immutable documentation of all tool movements and maintenance work, significantly increasing traceability and security.
Mobile Solutions and Apps
Mobile solutions and apps offer flexible and user-friendly ways to manage and monitor tools. They enable access to tool data from anywhere and at any time. Clouver offers intuitive mobile applications that enable real-time monitoring and control of tools, increasing flexibility and responsiveness in the production process.
Practical Examples
Success Stories from Various Industry Sectors
Detailed case studies show how companies from various industry sectors have successfully implemented digital tool management solutions from Procom and Clouver and what benefits they have achieved. These success stories provide valuable insights into practical applications and achieved improvements that can serve as inspiration for your own implementation.
Concrete Implementation Examples
Step-by-step presentations show how companies have introduced digital tool management systems. These examples provide valuable insights and guidance for your own implementation. By analysing concrete implementations, companies can adopt best practices and better overcome common challenges.
Lessons Learned from Failed Projects
The analysis of failed projects and lessons learned help avoid future mistakes. These insights are crucial for making implementation more successful. Companies learn which mistakes should be avoided and how they can adjust their strategies to ensure a smooth transition to Industry 4.0 tool management.
Technical Details
Sensor Types and Applications
An overview of various IoT sensors, their applications, and advantages and disadvantages helps in selecting the right sensors for your own company. Clouver offers a wide range of sensors that cover specific requirements, from temperature sensors to vibration detection. The right sensor choice is crucial for precise tool monitoring and effective data collection.
Data Protocols and Standards
Important data protocols and standards in tool management are crucial for system integration and networking. Clouver supports common protocols such as MQTT and OPC UA, enabling seamless communication between different devices and systems. A deep understanding of these standards is essential to ensure smooth integration and efficient data processing.
Security Aspects and Data Protection
The most important security measures and data protection guidelines must be observed when implementing digital tool management solutions. Clouver ensures that all data encryption and access controls meet the highest security standards. These measures are crucial to ensure the integrity and security of tool data and maximise protection against cyber attacks.
Decision Aids
Checklists for System Selection
Important criteria and questions that should be considered when selecting a digital tool management system help find the best solution for your own requirements. Checklists from Procom and Clouver include aspects such as functionality, scalability, integration capability, and costs to provide a solid basis for decision-making.
Comparison Matrices of Different Solutions
The comparison of various digital tool management systems regarding functions, costs, user-friendliness, and integration facilitates the decision for the appropriate system. Procom and Clouver offer detailed comparison matrices that provide a transparent overview of the strengths and weaknesses of different solutions and simplify selection.
ROI Calculators
Interactive tools or tables for calculating the Return on Investment (ROI) for specific investments in digital tool management solutions help evaluate the financial benefits of investments. Clouver offers user-friendly ROI calculators that enable companies to precisely evaluate the economic advantages of their investments and thus support informed decisions.
Conclusion and Outlook
In this article, we have thoroughly examined the importance of tool management in Industry 4.0. We have found that through the use of modern technologies such as IoT from Clouver, Big Data, and artificial intelligence, efficiency and productivity in manufacturing can be significantly increased. Well-thought-out tool management enables not only precise monitoring and administration of tools but also predictive maintenance, leading to a reduction in downtime and costs. Additionally, it promotes sustainability through longer tool life and optimised resource utilisation.
If you would like to learn more about the implementation and benefits of tool management in Industry 4.0, we invite you to read our further articles on this topic. Do you have questions or would you like to share your experiences? Leave us a comment or contact us directly. Also discover our comprehensive resource library to dive deeper into the world of Industry 4.0. Click here to learn more!
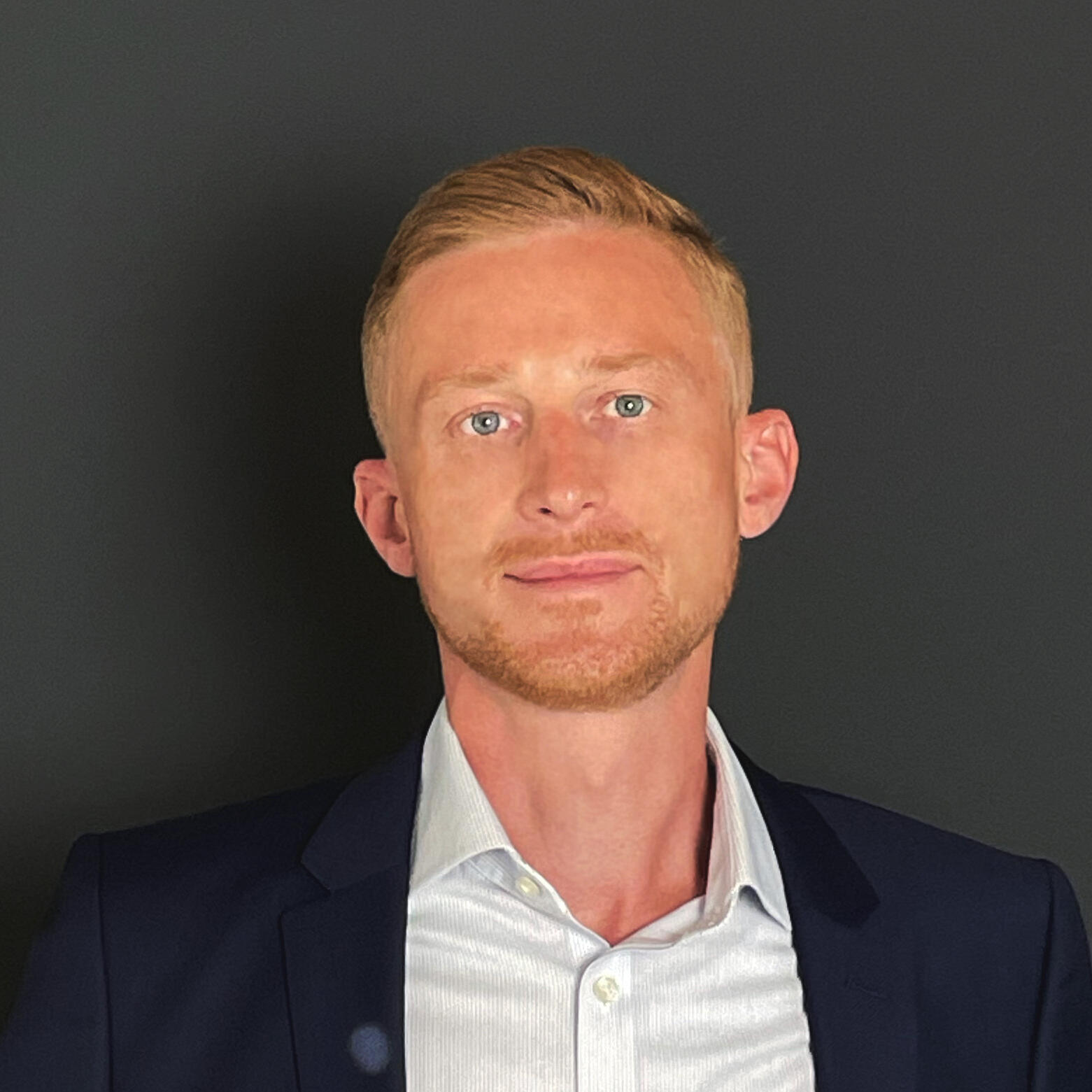
Dimitri Koneger
Sales Manager
Have questions about the topic or want to learn more about our solutions?
Contact us and discover how our products can future-proof your machines. Let’s work together to find out how we can help take your production to the next level!
- +49 241 93681-500
- contact@procom-automation.de
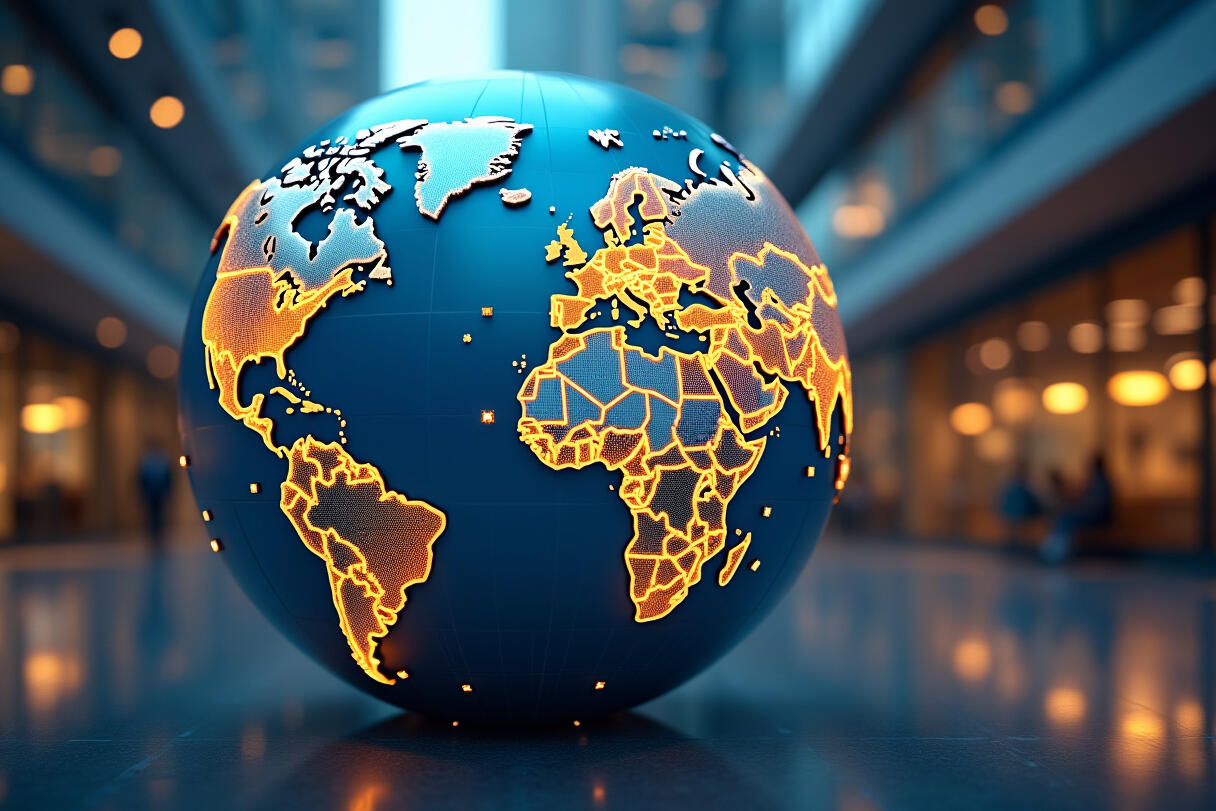
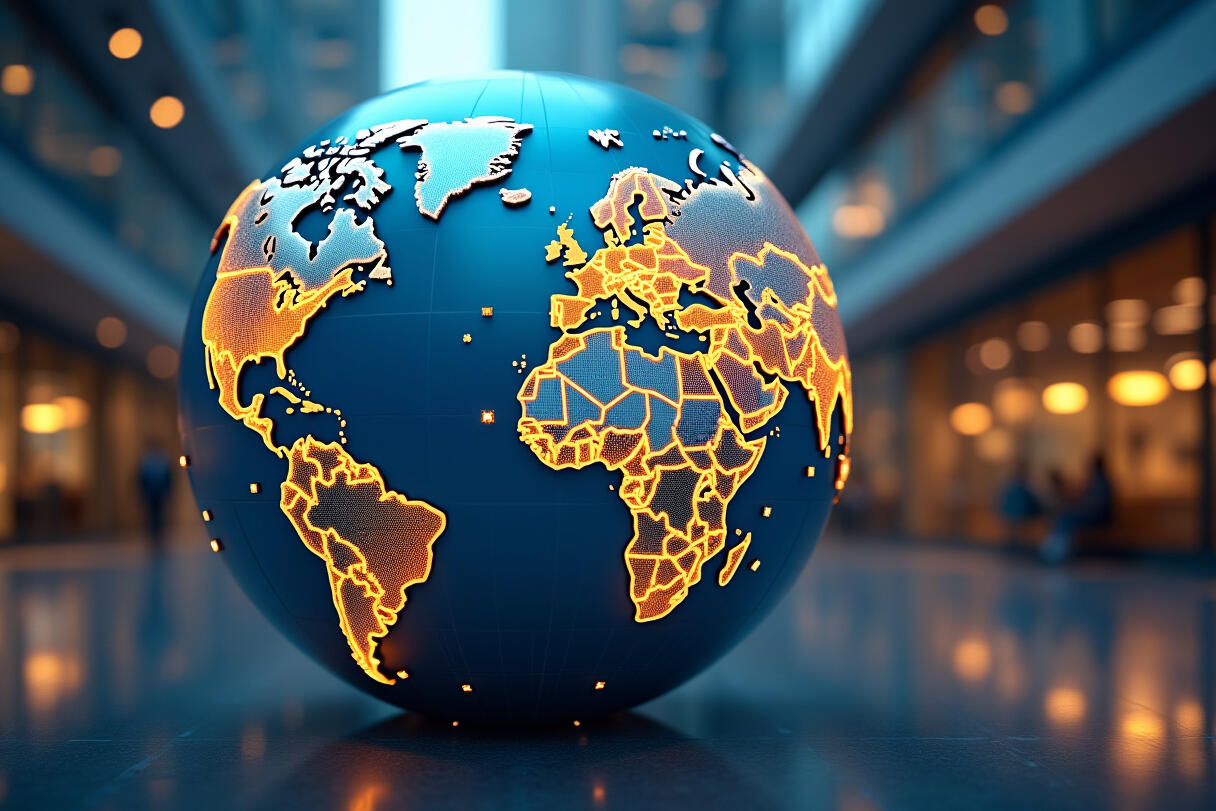